Технология производства сахарной ваты
Сладкая вата сегодня является одним из самых востребованных лакомств для взрослых и детей, и ее изготовление может стать весьма рентабельным бизнесом для тех, кто в этом заинтересован.
Если у Вас возник вопрос, как сделать сахарную вату, то, прежде всего, нужно понять, что же это за продукт и ознакомиться с основными технологическими моментами его изготовления. Итак, сладкая вата представляет собой тончайшие сахарные нити, которые получают из предварительно нагретого до температуры 180-200 градусов сахарного песка. Нити образуются из расплавленного сырья под воздействием центробежной силы. Для придания витаминной ценности, улучшения вкуса и внешнего вида продукта на охлажденные волокна методом распыления наносят витаминизированные натуральные добавки и красители. В настоящее время существует большое количество таких добавок, позволяющих наладить производство сахарной ваты с самым разнообразным вкусом.
Наиболее распространено изготовление ваты рулонного типа, при которой волокна наматываются на пластиковую или деревянную палочку или же в виде рулонов слоями укладываются в специальные емкости. Именно такой продукт привычен для потребителя и широко встречается в продаже.
Базовым оборудованием для осуществления всех указанных технологических процессов являются специальные аппараты для сладкой ваты. Основой их конструкции служит металлический бокс, на котором устанавливается чаша из нержавеющей стали для сбора сахарных нитей. Для защиты от потери продукта большинство производителей оснащают чаши специальной защитной сеткой или пластиковым колпаком. Работают такие аппараты от электрической сети, с номинальным напряжением 220В. На их разогрев для начала работы уходит порядка 1 минуты, а на изготовление одной порции ваты порядка 15-30 секунд. Расход сахара при этом составляет в среднем около 20 грамм на порцию. Действия оператора не требуют особой подготовки и сводятся к тому, чтобы засыпать нужное количество сырья в емкость и по истечении времени собрать готовый десерт.
Сегодня на рынке представлено весьма разнообразное оборудование для производства сладкой ваты, как от отечественных, так и от импортных производителей. Наибольшую популярность в последнее время завоевывают аппараты AIRHOT, представленные в нескольких модификациях разной производительности. Они ценятся за относительно невысокую стоимость, а также компактность, легкость и мобильность конструкции. Аналогичными достоинствами обладает и оборудование STARFOOD. Линейка данных аппаратов считается весьма экономичной и быстро окупается в процессе работы. По желанию и в зависимости от предполагаемых объемов производства можно приобрести агрегаты, выполненные в настольном или напольном варианте, а также оснащенные тележкой. Тележки, защитные сетки и пластиковые куполы различного диаметра имеются и в отдельной продаже.
Хлопковая вата – происхождение, преимущества, особенности
Хлопковая вата – материал знакомый всем с детства. Делают ее из разного сырья, но лучшей в большинстве случаев считается вата из хлопка, представляющая собой волокна хлопковых семян, слабо связанные друг с другом и разделенные на слои.
Преимущества хлопковой ваты
Хлопчатник – растение, чьё волокно используется для производства тканей и ваты, знаком человечеству уже тысячи лет. Специалисты до сих пор спорят, появился ли он в Индии или в Древнем Египте. Очевидно одно – материал, получаемый из этого растения, очень нужен и полезен людям, иначе оно не удержалось бы столько лет рядом с человеком.
Список преимуществ хлопковой ваты не длинный, но выразительный:
- Хлопчатобумажная вата – материал натуральный, проверенный веками, а, следовательно – абсолютно безопасный с экологической точки зрения.
- На хлопковую вату не бывает аллергии. Если неправильно ухаживать за ватными изделиями, в них, как и везде, может скопиться пыль. Реакцию на нее часто путают с аллергией, но хлопковая вата не аллергенна.
- Вата лучше всего остального сохраняет тепло. Несмотря на многочисленные изобретения химиков, ничего лучше ваты для сохранения тепла до сих пор не придумали. Исключение – очищенный птичий пух, без примеси пера, но изделия из него очень дороги.
- Хлопковая вата – материал упругий, хорошо впитывающий влагу.
- Изделия, в которых использован ватный наполнитель, не требуют сложного ухода – их можно стирать, сушить, стерилизовать паром. Главное – после просушки расправить волокна, чтобы вернуть вещи упругость и пышность.
- Стоимость ваты из хлопка – одна из самых низких по сравнению с другими натуральными наполнителями. Отработанный веками процесс производства позволил понизить себестоимость этого материала и повысить его качество, причем новые разработки в этой области и сегодня время от времени появляются на рынке.
Производство хлопковой ваты
Чтобы разобраться, на чем основаны преимущества ваты, и понять, в каких областях ее лучше всего использовать, необходимо разобраться, из чего именно и как ее производят. Собранные семенные коробочки хлопчатника поступают на заводы, где их в первую очередь очищают от всевозможных примесей: песка, мелких камушков, стеблей, недозревших семян и прочего. Затем необходимо отделить волокна хлопка от семян. Выполняется это при помощи специальных машин, которые называют джинами.
Джины-волокноотделители в первую очередь разделяют хлопок на волокна, линт и делинт. Волокна используются для изготовления пряжи и ткани, а вот из линта – волокон короче 2 см и делинта (волокна короче 0,5 см) изготавливают вату. Для того чтобы собрать весь линт полностью, семена с оставшимся на них пухом еще несколько раз пропускают через специальные очистители – линтеры.
Кроме волокон в производстве ваты используются еще и хлопковые угары. Так называют остатки пуха, которые оседают на стенках машин после очистки сырья и при производстве хлопчатобумажных тканей.
Угары делят на три вида:
- волокнистые угары,
- регенерированное волокно
- хлопковый пух.
Волокнистые угары используют для производства высококачественной ваты, остальные же виды чаще добавляют в набивку мебели и матрасов.
Получившуюся смесь расщепляют с помощью механизмов и формуют в листы и кипы. На этом обработка большинства видов ваты заканчивается, исключением являются кипы, предназначенные для изготовления медицинской ваты. Их еще раз очищают, разрыхляют и отваривают в растворах щёлочи при достаточно высокой температуре, чтобы отбелить. Затем удаляют пектиновые и азотистые соединения и стерилизуют под высоким давлением, после чего вата готова к отправке.
Виды хлопковой ваты
Хлопковая вата делится на группы в зависимости от длины волокон и степени очистки. Названия виды получили по области применения разновидностей этого продукта. Современные стандарты выделяют 4 вида:
- одежную, которая легко делится на слои;
- мебельную, нерасчесанную;
- медицинскую, белую, иногда желтоватую, для компрессов, повязок и операций;
- техническую, которая используется для упаковки или в качестве сырья.
Одежная вата
Одежную вату производят из хлопка четвертого, пятого и шестого сортов, не пригодного для производства пряжи. К хлопковым волокнам добавляют пух, хлопкопрядильные угары, иногда вторичное сырье.
По количеству и виду примесей вату делят на несколько сортов, требования к которым регламентирует ГОСТ 5679 — 91 «Вата хлопчатобумажная одежная и мебельная. Технические условия»:
- Вата «Люкс»
- Вата «Прима»
- Вата «Швейная».
Этот стандарт четко регламентирует свойства ваты, и именно его соблюдение гарантирует, что вы получите именно то, что вам требуется.
В вате сортов Люкс и Прима хлопковые угары почти не встречаются, основной их состав – коротковолокнистый хлопок. Вата Люкс – самая чистая: количество необработанных волокон в ней, по ГОСТ 5679 минимально – всего 2,6%, это вата самая упругая – упругость 67%. Ее плотность всего 22 кг/м3, а значит, изделия из ваты Люкс будут легкими, теплыми, пышными и долго не потеряют форму.
Вата Прима сортом чуть ниже, в ней сорных примесей уже 5%, она менее упругая (65%), то есть изделия из нее чуть хуже сохраняют форму. Весит она тоже больше – ее плотность 23 кг/м3, правда в этом случае разница с ватой Люкс не очень заметна.
Швейная вата делается из хлопчатого пуха и угаров, доля длинных хлопковых волокон в ней 35%. Вата Швейная более плотная и тяжелая, чем Люкс и Прима, ее плотность 25 кг/м3. Сорные примеси и необработанные волокна составляют в ней 7%. При этом Швейная остаётся достаточно упругой (60%) и продукция из нее хорошо держит форму. Применяют такую Швейную как утеплитель одежды, включая спецодежду, для производства одеял и высококачественных беспружинных матрасов.
Мебельная вата
Мебельная вата (она же тюфячная) по составу близка к Швейной – она так же делается из низкосортового хлопка, угаров и отходов текстильных фабрик. Ее приходится долго чистить, затем пропускать через рыхлительно-трепательные механизмы, чтобы волокнистая масса приобрела объём и упругость.
Для мебельной ваты характерна загорошенность – так называется наличие в вате узелков и пороков волокна, которые не удалось растрепать. Их легко почувствовать, прикоснувшись к такой вате. Уровень загорошенности тоже строго регулируется ГОСТами. Этой ватой набивают мягкую мебель и тюфяки.
Медицинская вата
Медицинская вата – наиболее чистый продукт. Она делится на несколько групп – глазную, бытовую гигиеническую, хирургическую (стерильную или нет) и прочее. Главный признак, на котором основано использование медицинской ваты — обезжирена она или нет. Обезжиренная вата, вываренная в щелочном растворе, используется при перевязках и операциях, а необезжиренная – более упругая и пышная, чаще используется для подклада под фиксаторы при лечении переломов и для компрессов.
Техническая вата
Этот сорт ваты делают из регенерированного хлопкового волокна, которое получают переработкой отходов от производства ваты более высоких сортов, и вторичного сырья. Техническую вату тоже иногда используют для набивки мебели и матрасов, но основная область ее применения – упаковка бьющихся товаров, а также теплоизоляция и звукоизоляция помещений. Хлопковая техническая вата встречается нечасто, обычно в такой продукции есть синтетические волокна, количество которых может достигать 40%.
Востребованность хлопковой ваты
Натуральная хлопковая вата еще долго будет востребована в швейной и мебельной промышленности, в строительстве и медицине. Даже самые новые материалы никогда не смогут превзойти лучшего мастера – природу по экологичности, безопасности и комфорту, которые дает хлопковый ватный наполнитель.
Производство ваты и ватина
Компания «Матрасофф» выпускает два вида ватных матрасов:
- из хлопка. В качестве наполнителя используется швейная белая вата, состав — 100 % хлопок;
- из регенерируемого волокна. Наполнитель — вата РВ серого цвета, изготовленная из остатков х/б ткани со швейных фабрик. В состав входит хлопок с добавлением синтетического волокна (10 %). Это придает изделию упругость и прочность.
На весь ассортимент продукции имеются сертификаты качества и соответствия ТУ и ГОСТу.
Как происходит изготовление ваты и ватина?
Сырье для продукции поступает в кипах весом от 200–300 кг и хранится на сухом складе с естественной влажностью и температурой. Затем его перевозят в цех первичной обработки хлопка или ткани, где на специальном оборудовании сырье разделяют на небольшие пласты и загружают в смеситель непрерывного действия.
Кусочки ваты по транспортёрной ленте попадают или на щипальную машину (в случае переработки хлопка), или на рубочную машину (в случае переработки ткани).
На щипальной машине сырье разделяют на волокна, производят очистку от пыли и удаляют примеси и инородные частицы. Затем массу загружают в резервный питатель для тщательного перемешивания. Уже отсюда масса попадает в бункер чесальной машины, где вату расчесывают на отдельные волокна. Из волокон образуют тонкий холст шириной около 100 см и проводят еще одну очистку от пыли и примесей.
На следующем этапе в зависимости от сырья производственный процесс различается. Вату для более дешёвых матрасов «Классик» загружают в надувочную камеру и равномерно заполняют сырьем чехол. Вату для более дорогих изделий категории «Премиум» складывают друг на друга, получая холст шириной около 2 м. После этого холст сматывают в рулоны определённого веса и диаметра.
Далее все матрасы попадают в пиковочную машину, где на изделия устанавливают кнопки для предотвращения смещения слоёв ваты внутри. Если изготавливается матрас индивидуального размера, процесс производят вручную.
На последнем этапе к матрасам крепят ярлыки с указанием состава наполнителя, размера и веса изделия, наименованием ГОСТа или ТУ. Готовая продукция попадает на склад.
Таким образом, в нашей компании соблюдаются все требования к технологическим процессам по изготовлению ватных матрасов из хлопка. Контроль качества ведется на всех этапах производства, включая и упаковку готовой продукции.
Приобретая матрасы от компании «Матрасофф» вы можете быть уверены в их качестве! Мы даем гарантию на весь ассортимент: ватные матрасы, включая модели для детей, одеяла, подушки, тюфяки и постельное белье.
А также: Желаете купить в СПб поролоновый матрас напрямую у производителя? Обращайтесь!
Вата медицинская | Статья от специалистов компании «Фарм-Глобал»
03.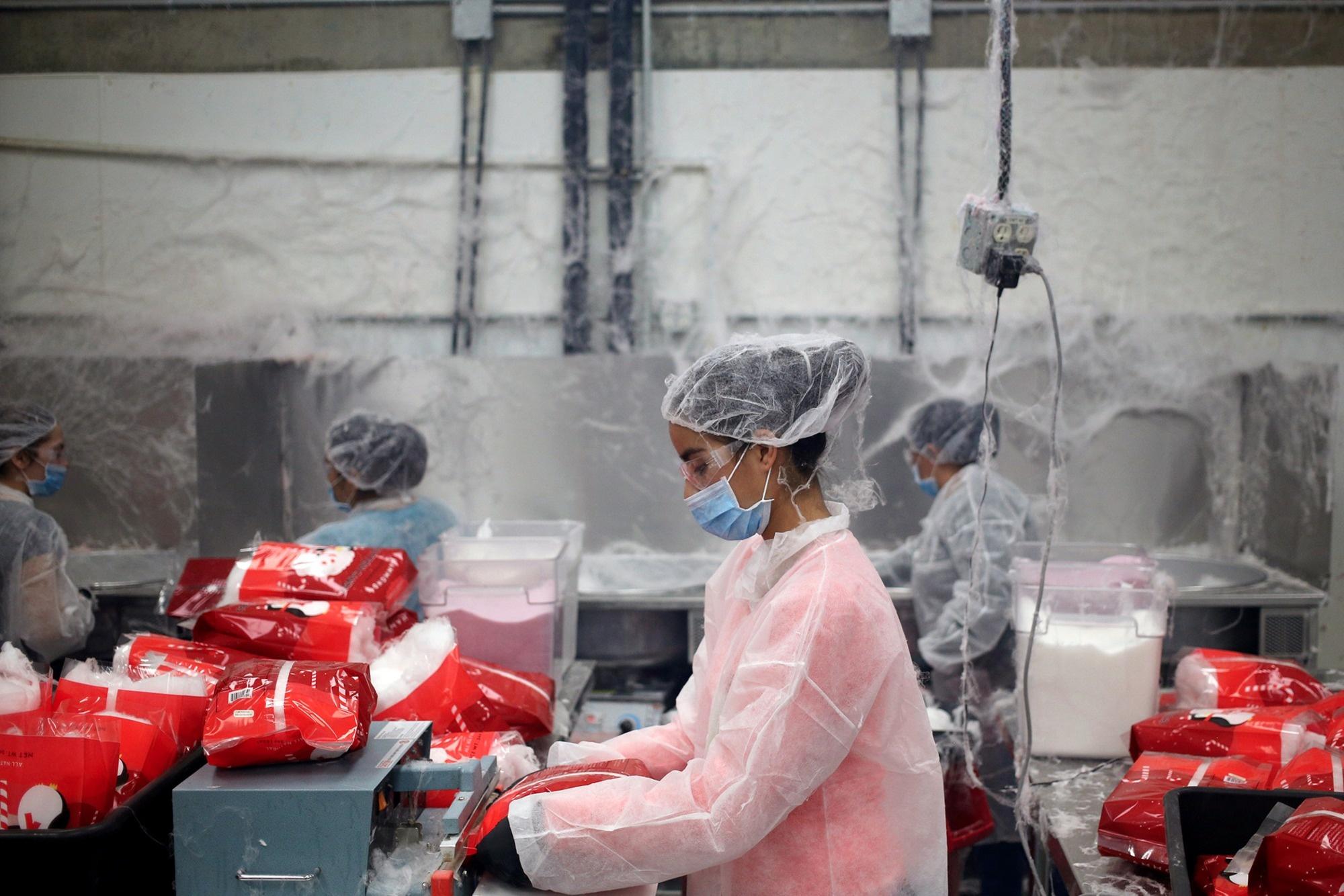
Вата медицинская представляет собой пушистую хлопковую массу, имеющую слабопереплетенную волокнистую структуру. Применяется в клинических и домашних условиях при выполнении различных лечебных и косметических процедур, в том числе перевязок, компрессов, инъекций. Благодаря сочетанию хорошей впитывающей способности и гигиеничности этот материал стал незаменимым в работе перевязочных, процедурных, хирургических отделений, а также стоматологических, физиотерапевтических и офтальмологических кабинетов.
Вата медицинская бывает следующих видов:
- Гигроскопическая. Используется при перевязках ран.
Компрессная. Предназначена для согревающих компрессов.- Глазная. Обладает наивысшей капиллярностью и поглотительной способностью.
- Хирургическая. Предназначена для перевязок ран.
- Гигиеническая. Используется для ежедневного гигиенического ухода и различных медицинских манипуляций.
Вату выпускают как стерильной, так и нестерильной. Срок годности первой составляет не менее 5 лет.
К вате предъявляют определенные требования:
- Она должна иметь слоистую структуру и обладать высокой степенью сорбции для аккуратного и эффективного впитывания жидких выделений при обработке и перевязке ран (вата накладывается поверх слоев марли или перевязочных бинтов).
- Стерильность, необходимая для обеспечения возможности работать с поврежденной поверхностью кожи или открытой раной.
- Однородность материала.
- Отсутствие посторонних добавок и примесей. Это обеспечит безопасную обработку раневой поверхности без риска возникновения вторичных инфекций и раздражения.
- Высокая степень белизны и капиллярности.
- Гипоаллергенность.
Производство ваты осуществляется из сырья, получаемого после переработки плода хлопчатника мохнатой. Внутри коробочки этого растения, которая раскрывается после созревания плода, находится мягкое волокно белого цвета вместе с семенами. Это волокно собирается на специальных пунктах, упаковывается и далее отправляется на хлопкоочистительный завод, где происходит отделение волокон от семян и разделение их по длине. При этом длинные волокна (2 – 2,5 см) идут на изготовление тканей, короткие же, называемые линт, — на производство ваты. Далее происходит расщепление, разрыхление и очищение от примесей волокон, и полученная в результате масса с помощью разрыхлительно-трепального агрегата формируется в так называемые холсты. Холсты отправляются на чесальные машины, с помощью которых превращаются в съем ваты – это сырье подвергается щелочной варке под давлением и обработке гипосульфитом натрия. В результате волокно приобретает характерные ему свойства (быстрого смачивания и поглощения жидкостей), белизну и эстетический вид.
В настоящее время используются новейшие методы производства, позволяющие при отбелке не использовать хлорсодержащие химические реагенты. Благодаря экологичным бесхлорным технологиям исключается возможность появления аллергии у пациентов, снижается загрязнение окружающей среды.
Произведенная вата пакуется в кипы по 20, 30, 40 и 50 кг. Вата фасуется в индивидуальную упаковку по 25, 50, 100, 200 и 250 грамм.
Медицинская гигроскопическая вата должна быть изготовлена в соответствии со стандартами ГОСТ 5556-81 1.3. Согласно этому ГОСТу, медицинская гигроскопическая глазная вата должна быть выработана только из 100% хлопкового волокна, хирургическая – из хлопкового волокна или смеси хлопкового волокна с вискозным штапельным волокном. Вата должна быть хорошо прочесанной, легко расслаиваемой на слои произвольной толщины и при этом сохраняющей связь между волокнами.
В последнее десятилетие российское ватное производство, да и в целом текстильная промышленность, испытывает трудности в поставках сырья для производства ваты. Значительная часть ваты в нашу страну импортируется из Китая, Индии, США, Пакистана, Бразилии, Узбекистана. Возникший дефицит сырья компенсируется использованием отечественного лубяного волокна низкого сорта, а также его отходов и целлюлозных химических волокон (в частности вискозного волокна).
Вата на основе целлюлозного волокна, для производства которой используется льняное волокно, по некоторым показателям имеет низкие эксплуатационные свойства. Гигроскопическая вата, состоящая из волокнистой смеси на основе хлопкового и вискозного волокон, имеет на ощупь неприятный скрип. Именно поэтому находящиеся в поисках альтернативных материалов производители все чаще склоны отдавать предпочтение льну, выращиваемому во многих регионах России. Лен характеризуется большей гигроскопичностью и стоит дешевле. Единственная сложность при работе с ним возникает на этапе производства: лен имеет грязноватый оттенок и требует отбеливания, а хлор как наиболее известный промышленный отбеливатель нивелирует природные дезинфицирующие свойства льна, за которые и ценится.
В настоящее время появилось много косметической продукции, в состав которой входит медицинская вата. Это ватные диски, шарики, валики, палочки и тампоны. Также в продаже имеется вата «Зиг-Заг», поставляемая в удобном виде фасовки, позволяющем отрывать нужное количество от ватной ленты, не затрагивая находящийся в пакете остаток.
Рынок ваты в России 2016 — Обзор и анализ рынка
Фото: © THPStock / Bigstockphoto
Согласно исследованию рынка ваты, объемы ее выпуска в России неуклонно снижаются пятый год подряд. По последним оперативным данным Росстата, в апреле 2016 г. произведено на 30 т. ваты меньше, чем в предыдущем месяце.
Российские предприятия показывают неустойчивую понижательную динамику производства ваты на протяжении последних 12 месяцев. В 2015 году индекс производства к предыдущему месяцу был отрицательным 6 месяцев из 12. Объем производства ваты в январе-апреле 2016 года в натуральном выражении сократился на 1% г/г.
Годовое падение производства в 2015 году составило 10%. По оценкам специалистов Indexbox, процесс импортозамещения в легкой промышленности не имеет предпосылок, так как производство одежды в РФ лишено сырьевой базы. Ранее хлопок поставлялся из стран Средней Азии, но в настоящий момент эта производительная цепочка разорвалась. За 1990-е гг. узбекские производители хлопка переориентировались на рынки Китая и Турции. Не смотря на это, вата относится к товарам первой необходимости и спрос на неё будет всегда устойчив. Из-за стратегической важности данного производства в России оно по-прежнему сохраняется на достаточно высоком уровне — по оценкам IndexBox, доля продукции российского производства на рынке ваты составляет примерно 1/3.
Динамика производства ваты в России
Динамика производства ваты в стоимостном выражении отличается от динамики производства в натуральном выражении, характеризуясь при этом ростом. Так, за январь-апрель 2016 года объем производства в стоимостном выражении оказался на 19% выше г/г. Согласно данным исследования, проведенного специалистами компании IndexBox, себестоимость производства ваты значительно выросла из-за подорожания сырья (хлопка), ввозимого из-за рубежа.
Объем производства ваты в России
В числе важнейших поставщиков ваты можно выделить: ООО «НЬЮФАРМ» из Ивановской области, ООО «РУСВАТА» и ООО «ЕМЕЛЬЯНЪ САВОСТИНЪ» из Рязанской области, ЗАО «ГИГРОВАТА-САНКТ-ПЕТЕРБУРГ» (Амелия) из Ленинградской области, ЗАО «ФАБРИКА НИКА» из Санкт-Петербурга и некоторые другие.
Рынок ваты в России: география производства
Наибольший объем производства среди всех федеральных округов приходится на Центральный федеральный округ: в 1 кв. 2016 года там было произведено 853 т. ваты, что составляет 75% от совокупного объема. На втором месте с долей 22% находится Северо-Западный федеральный округ. В совокупности на данные федеральные округа приходится 97% от российского объема производства в 1 кв. 2016 года, как и в 4 кв. 2015 года. Стабильное распределение долей в совокупном объеме производства показывает равномерное внутригодовое использование мощностей во всех федеральных округах.
По мнению экспертов МЭР и Минпромторга, российское производство изделий из натуральных волокон (хлопка, шерсти, льна) практически не имеет прочной базы для восстановления, то есть потеря потенциала отрасли произошла безвозвратно. В настоящее время на уровне Правительства в качестве приоритетного рассматривается вариант переориентации отечественного легпрома на синтетическое сырье с синтетическими тканями и изделиями из них в качестве перспективной специализации.
Традиционная легкая промышленность в среднесрочной перспективе сохранится в России настолько, насколько окажется конкурентоспособной в условиях открытости границ и высокой стоимости сырья. Однако, если рассматривать именно производство и рынок ваты, то в этом секторе не стоит ожидать значительных перестановок за исключением тех, которые связаны с мерами государственной политики.
Источник: Маркетинговое исследование. Рынок медицинской ваты
Вата рв производство
Производство ваты рв — наполнитель для матрасов ватных
Регенерированное волокно
Регенерированное волокно, что это такое вата рв — проще всего ответить на этот вопрос посмотрев наше видео. Основные цели и задачи это отсутствие неразработанного материала и выпуск максимально чистого не побоимся этого слова лучшего по этим параметрам продукта. Вата матрасная — не совсем корректное название, до 60 процентов товара идет на другие более технологичные производства. Также мы производим вату техническую швейную.
ПЕРЕД ТЕМ КАК КУПИТЬ ВАТУ РВ в Москве В ИЮНЕ ОЗНАКОМЬТЕСЬ КАК ОНА ПРОИЗВОДИТСЯ
На начальном этапе происходит тотальный контроль входящего сырья, а также выборочно производится спектральный анализ. Здесь Вы увидите технологический процесс превращения швейных отходов в высококачественную волокнистую массу вату из швейных отходов рв, прошедшую обеспыливание на девяти агрегатированных в единую линию аппаратах. Данное оборудование благодаря изменяющимися параметрам позволяет производить различную по качеству продукцию: 1. наполнитель вата рв матрасная, набивка для подушек, одеял. 2. сырье для утеплителей и нетканых материалов 3. волокно для чесального оборудования и аэромеханических систем. 4. волокно для технологий использующими печи с добавлением легкоплавких компонентов.
Вы посмотрите как делается наполнитель вата рв, на данный момент на всех переходах установлены дополнительные сепараторы что еще на 18% увеличило фильтрацию выходящего продукта и улучшило культуру производства. По предварительному заказу возможна двойная обработка. Если у Вас остались не ясности в чем различие ваты рв и ваты хб и что такое регенерированное волокно для матрасов всегда рады помочь. Мы уверены купив в Москве нашу продукцию вату рв Вы не только поймете что это лучший наполнитель для матрасов но и станете нашим постоянным клиентом.
Минеральная вата-основа для производства теплоизоляционных изделий
Минеральная вата представляет собой волокнистый теплоизоляционный материал, получаемый путем плавления силикатных горных пород, металлургических шлаков и их смесей.
По внешний виду сырья минеральную вату подразделяют на каменную и шлаковую. В первом случае для производства применяются горные породы — базальт, диабаз, известняк, доломит, во втором — шлаки, являющиеся отходами производства металлов.
Процесс производства минеральной ваты включает в себя несколько этапов:
1-подготовку сырья;
2-получение расплава;
3-вырабатывание волокон;
4-осаждение волокон;
5-получение минераловатного ковра.
Немаловажным шагом в производстве минеральной ваты является расчет состава смеси сырьевых материалов – шихты. От него во многом зависят дальнейшие свойства полученного материала.
Процесс приобретения расплава обычно происходит в вагранках – шахтных плавильных печах.
Организацию минерального волокна производят дутьевым или центробежным методом. Первый заключается в воздействии на струю расплава струи водяного пара или сжатого газа, другой основан на использовании центробежной силы, превращающей горячий жидкий шлак или камень в тончайшие волокна. Данные нити попадают в камеру осаждения, а оттуда определяются на конвейер под уплотняющие их валки.
На следующем этапе делается введение связующего для образования плит или матов, а следом, после дополнительного формования и уплотнения, минераловатный ковёр подвергается продольной и поперечной резке для придания заданного размера.
Применение минераловатных изделий
Применяя для склеивания волокон синтетическое связующее, из минеральной ваты производят ряд утеплителей для строительных объектов.Теплоизоляционные изделия из минеральной ваты представляют собой плиты, умноженной жесткости, рулонные материалы – маты, а также войлок, скорлупы, сегменты и иные изделия.Минераловатные теплоизоляционные изделия применяются в многослойных теплоизоляционных системах. Среди них системы наружного утепления «мокрого» типа, системы с утеплителем внутренней стороны ограждающей конструкции, теплоизоляционный слой в навесных вентилируемых фасадах.На объектах, где изоляция подвергается нагрузке во время монтажа или в процессе эксплуатации, применяются жесткие минераловатные утеплители. Это, в основном, участки теплоизоляции цокольных конструкций. А в системах пола под цементную стяжку утеплители из минеральной ваты не только сохраняют тепло, но и значительно повышают звукоизоляцию межэтажных перекрытий.Плиты повышенной жесткости рассчитаны на использование для изоляции покрытий из профилированного металлического настила или железобетона, без устройства стяжки. Минеральная вата также предназначается наполнителем кассетных сэндвич-панелей.
На сегодняшний день минераловатные плиты, маты и однотипные изделия прочно занимают лидирующие позиции среди теплоизоляционных материалов, обладающих большим коэффициентом сохранения тепла и минимальной экологической опасностью.
Производство хлопчатобумажной пряжи
На хлопок приходится почти 50% мирового потребления текстильного волокна. Китай, США, Российская Федерация, Индия и Япония являются основными потребителями хлопка. Потребление измеряется количеством закупленного хлопкового волокна-сырца, которое используется для производства текстильных материалов. Ежегодное производство хлопка в мире составляет от 80 до 90 миллионов тюков (от 17,4 до 19,6 миллиарда кг). Китай, США, Индия, Пакистан и Узбекистан являются основными производителями хлопка, на долю которых приходится более 70% мирового производства хлопка.Остальные производятся примерно в 75 других странах. Хлопок-сырец экспортируется примерно из 57 стран, а текстильные изделия из хлопка — примерно из 65 стран. Многие страны делают упор на внутреннем производстве, чтобы уменьшить свою зависимость от импорта.
Производство пряжи — это последовательность процессов, которые превращают хлопковые волокна-сырцы в пряжу, пригодную для использования в различных конечных продуктах. Для получения чистой, прочной и однородной пряжи, необходимой на современных текстильных рынках, требуется ряд процессов. Начиная с плотной упаковки спутанных волокон (тюк хлопка), содержащей различное количество материалов без ворса и непригодных для использования волокон (инородные тела, растительный мусор, пылинки и т. Д.), Непрерывные операции по открытию, смешиванию, смешиванию, очистке, чесанию, вытяжке , ровинг и прядение используются для преобразования хлопковых волокон в пряжу.
Несмотря на то, что текущие производственные процессы высоко развиты, давление конкуренции продолжает побуждать отраслевые группы и отдельных лиц искать новые, более эффективные методы и машины для обработки хлопка, которые однажды могут вытеснить сегодняшние системы. Однако в обозримом будущем будут по-прежнему использоваться существующие традиционные системы смешивания, чесания, вытяжки, ровницы и прядения. Похоже, что в ближайшем будущем только процесс сбора хлопка обречен на упадок.
Производство пряжи производит пряжу для различных тканых или трикотажных конечных продуктов (например, швейных или промышленных тканей), а также для швейных ниток и веревок. Пряжа выпускается с разным диаметром и разным весом на единицу длины. В то время как основной процесс производства пряжи оставался неизменным в течение ряда лет, скорость обработки, технология управления и размеры упаковки увеличились. Свойства пряжи и эффективность обработки связаны со свойствами обработанных хлопковых волокон.Конечные свойства пряжи также зависят от условий обработки.
Процессы производства пряжи
Открытие, смешивание, смешивание и очистка
Обычно фабрики выбирают смеси для тюков со свойствами, необходимыми для производства пряжи для конкретного конечного использования. Количество тюков, используемых разными заводами в каждой смеси, колеблется от 6 или 12 до более чем 50. Обработка начинается, когда тюки, подлежащие смешиванию, доставляются в камеру разгрузки, где мешки и стяжки удаляются.Слои хлопка удаляются из тюков вручную и помещаются в питатели, оборудованные конвейерами с шипами, или целые тюки помещаются на платформы, которые перемещают их назад и вперед под или над ощипывающим механизмом. Цель состоит в том, чтобы начать последовательный производственный процесс, превратив уплотненные слои тюкованного хлопка в небольшие легкие пушистые пучки, которые будут способствовать удалению посторонних предметов. Этот начальный процесс называется «открытием». Поскольку тюки поступают на мельницу с разной степенью плотности, связки тюков обычно разрезаются примерно за 24 часа до обработки тюков, чтобы они «распустились».Это улучшает открытие и помогает регулировать скорость кормления. Очистные машины на мельницах выполняют функции открывания и очистки первого уровня.
Кардочесание и гребнечесание
Карточка — самая важная машина в процессе производства пряжи. Он выполняет функции очистки второго и конечного уровней на подавляющем большинстве текстильных фабрик. Карта состоит из системы из трех покрытых проволокой цилиндров и ряда плоских покрытых проволокой стержней, которые последовательно обрабатывают небольшие скопления и пучки волокон до высокой степени разделения или раскрытия, удаляют очень высокий процент мусора и т. Д. Посторонние предметы соберите волокна в виде веревки, называемой «лентой», и доставьте ее в контейнер для использования в последующем процессе (см. рисунок 1).
Рисунок 1. Кардочесание
Wilawan Juengprasert, Министерство здравоохранения, Таиланд
Исторически хлопок подавался на карту в виде «холста сборщика», который образовывался на «сборщике», комбинации подающих роликов и взбивателей с механизмом, состоящим из цилиндрических сит, на которых открываются пучки хлопка. собираются и скручиваются в войлок (см. рисунок 2). Войлок снимается с экранов ровным плоским листом, а затем скатывается в холст.Однако потребность в рабочей силе и наличие автоматизированных систем обработки с потенциалом повышения качества способствуют устареванию сборщика.
Рисунок 2. Современный сборщик
Wilawan Juengprasert, Министерство здравоохранения, Таиланд
Устранение процесса комплектования карт стало возможным благодаря установке на картах более эффективного оборудования для открывания и очистки, а также систем подачи лотков. Последние распределяют открытые и очищенные пучки волокон по картам пневматически через каналы.Это действие способствует единообразию обработки и повышению качества, а также сокращает количество необходимых рабочих.
Небольшое количество фабрик производит гребенную пряжу, самую чистую и однородную хлопчатобумажную пряжу. Расчесывание обеспечивает более тщательную очистку, чем предусмотрено картой. Целью расчесывания является удаление коротких волокон, ворса и мусора, чтобы полученная полоса была очень чистой и блестящей. Гребнечесальная машина представляет собой сложную машину, состоящую из рифленых подающих роликов и цилиндра, который частично покрыт иглами для вычесывания коротких волокон (см. Рисунок 3).
Рисунок 3. Вычесывание
Wilawan Juengprasert, Министерство здравоохранения, Таиланд
Волочение и ровинг
Вытяжка — это первый процесс в производстве пряжи, в котором используется роликовая вытяжка. На чертеже практически вся тяга возникает в результате действия роликов. Контейнеры с лентой, полученной в процессе чесания, забиваются в шпулярник вытяжной рамы. Вытяжка происходит, когда лента подается в систему парных роликов, движущихся с разной скоростью.При вытяжке волокна в ленте выпрямляются за счет вытяжки, чтобы сделать больше волокон параллельными оси ленты. Распараллеливание необходимо для получения желаемых свойств при последующем скручивании волокон в пряжу. При вытяжке также получается лента, более однородная по весу на единицу длины и помогающая достичь больших возможностей смешивания. Волокна, полученные в процессе окончательной вытяжки, называемого чистовой вытяжкой, почти прямые и параллельны оси ленты.Вес на единицу длины финишной вытяжной ленты слишком велик для вытяжки пряжи на обычных кольцепрядильных системах.
Процесс ровинга снижает вес ленты до размера, подходящего для прядения в пряжу и добавления скрутки, что сохраняет целостность вытяжных прядей. Банки с лентой после вытягивания или гребнечесания финишера помещаются в шпулярник, и отдельные ленты проходят через два набора роликов, второй из которых вращается быстрее, таким образом уменьшая размер ленты примерно с 2.5 см в диаметре до диаметра стандартного карандаша. Скручивание волокон придается путем пропускания пучка волокон через ровничный «летун». Этот продукт теперь называется «ровинг» и упаковывается на бобину длиной около 37,5 см и диаметром около 14 см.
Прядение
Прядение — единственный наиболее затратный этап преобразования хлопковых волокон в пряжу. В настоящее время более 85% пряжи в мире производится на кольцепрядильных машинах, которые предназначены для вытягивания ровницы до желаемого размера или количества пряжи и для придания желаемой крутки.Величина скрутки пропорциональна прочности пряжи. Отношение длины к поданной длине может варьироваться от 10 до 50. Катушки с ровницей помещаются на держатели, которые позволяют ровнице свободно подавать в вытяжной валок кольцепрядильной машины. Следуя за вытяжной зоной, пряжа проходит через «дорожку» на прядильную катушку. Веретено, удерживающее эту бобину, вращается с высокой скоростью, заставляя пряжу раздуваться при скручивании. Длина пряжи на бобинах слишком мала для использования в последующих процессах, и их снимают в «прядильные коробки» и доставляют на следующий процесс, который может быть намоткой или намоткой.
В современном производстве более тяжелой или грубой пряжи открытое прядение заменяет кольцевое прядение. Полоска волокон подается в высокоскоростной ротор. Здесь центробежная сила превращает волокна в пряжу. В шпульке нет необходимости, и пряжа набирается на упаковку, необходимую на следующем этапе процесса.
Значительные усилия в области исследований и разработок посвящены радикально новым методам производства пряжи. Ряд новых прядильных систем, которые в настоящее время разрабатываются, могут произвести революцию в производстве пряжи и вызвать изменения в относительной важности свойств волокна, как они сейчас воспринимаются.В целом, четыре различных подхода, используемых в новых системах, кажутся практичными для использования на хлопке. Системы внутреннего прядения в настоящее время используются для производства различных видов специальной пряжи и швейных ниток. Пряжа без кручения коммерчески производится в ограниченном количестве с помощью системы, которая связывает волокна вместе с поливиниловым спиртом или каким-либо другим связующим. Система пряжи без кручения обеспечивает потенциально высокую производительность и очень однородную пряжу. Превосходный внешний вид имеют трикотаж и другие швейные ткани из бескрученой пряжи.При воздушно-вихревом прядении, которое в настоящее время изучается несколькими производителями оборудования, вытяжная лента подается на разрыхляющий валок, аналогично роторному прядению. Воздушно-вихревое прядение способно развивать очень высокие производственные скорости, но модели-прототипы особенно чувствительны к изменениям длины волокна и содержанию посторонних веществ, таких как частицы мусора.
Намотка и намотка
После прядения производители должны подготовить правильную упаковку. Тип упаковки зависит от того, будет ли пряжа использоваться для ткачества или вязания.Намотка, намотка, скручивание и квиллинг считаются подготовительными этапами для ткачества и вязания пряжи. Как правило, продукт намотки будет использоваться как пряжи основы (пряжа, которая проходит вдоль тканого полотна), а продукт намотки будет использоваться как пряжи наполнения или пряжи утка (пряжа, которая проходит через фабрика). Продукты от прядения с открытым концом обходят эти этапы и упаковываются либо для начинки, либо для основы. При скручивании получается слоистая пряжа, при которой две или более пряжи скручиваются вместе перед дальнейшей обработкой.В процессе квиллинга пряжа наматывается на маленькие бобины, достаточно маленькие, чтобы поместиться внутри челнока ткацкого станка. Иногда процесс квиллинга происходит на ткацком станке. (См. Также статью «Ткачество и вязание» в этой главе.)
Обращение с отходами
На современных текстильных фабриках, где важна борьба с пылью, обращению с отходами уделяется больше внимания. В классических текстильных операциях отходы собирались вручную и доставлялись в «мусоросборник», если их нельзя было переработать в систему.Здесь он накапливался, пока не было достаточно одного вида, чтобы сделать тюк. На современном уровне техники центральные вакуумные системы автоматически возвращают отходы от открывания, захвата, кардочесания, вытягивания и ровницы. Центральная вакуумная система используется для очистки оборудования, автоматического сбора отходов из-под оборудования, таких как мухи и пылинки от чесания, а также для возврата непригодных для использования подметальных машин и отходов из конденсаторов фильтров. Классический пресс-подборщик — это пресс с вертикальным ходом вверх, который по-прежнему формирует типичный тюк массой 227 кг.В современной технологии мусоросборников отходы накапливаются из центральной вакуумной системы в приемном баке, который питает горизонтальный пресс для тюков. Различные отходы производства пряжи могут быть переработаны или повторно использованы в других отраслях. Например, прядение можно использовать в индустрии прядения отходов для производства пряжи для швабры, гранат можно использовать в производстве хлопчатобумажных ватин для изготовления ватина для матрасов или мягкой мебели.
Проблемы безопасности и здоровья
Машины и оборудование
Аварии могут происходить на всех типах машин для текстильного хлопка, хотя частота их невысока.Эффективная защита множества движущихся частей создает множество проблем и требует постоянного внимания. Также важно обучение операторов безопасным методам работы, в частности, чтобы избежать попыток ремонта, когда оборудование находится в движении, что является причиной многих несчастных случаев.
Каждая часть оборудования может иметь источники энергии (электрические, механические, пневматические, гидравлические, инерционные и т. Д.), Которые необходимо контролировать до того, как будут предприниматься какие-либо работы по ремонту или техническому обслуживанию. На предприятии следует определить источники энергии, предоставить необходимое оборудование и обучить персонал отключению всех опасных источников энергии во время работы с оборудованием.Следует регулярно проводить проверки, чтобы гарантировать, что все процедуры блокировки / маркировки соблюдаются и правильно применяются.
Вдыхание хлопковой пыли (биссиноз)
Вдыхание пыли, образующейся при превращении хлопкового волокна в пряжу и ткань, вызывает профессиональное заболевание легких, биссиноз, у небольшого числа текстильных рабочих. Обычно требуется от 15 до 20 лет воздействия более высоких уровней пыли (выше 0.От 5 до 1,0 мг / м 3 ), чтобы рабочие стали реакторами. Стандарты OSHA и Американской конференции государственных промышленных гигиенистов (ACGIH) устанавливают 0,2 мг / м 3 вдыхаемой хлопковой пыли, измеряемой вертикальным отбойником, как предел профессионального воздействия хлопковой пыли при производстве текстильной пряжи. Пыль, переносимые по воздуху твердые частицы, выбрасываемые в атмосферу при транспортировке или переработке хлопка, представляет собой неоднородную сложную смесь растительного мусора, почвы и микробиологического материала (т.э., бактерии и грибки), который различается по составу и биологической активности. Этиологический агент и патогенез биссиноза неизвестны. Мусор хлопковых растений, связанный с волокном и эндотоксином грамотрицательных бактерий на волокне, и растительный мусор, как полагают, являются причиной или содержат возбудителя. Само хлопковое волокно, которое в основном состоит из целлюлозы, не является причиной, поскольку целлюлоза представляет собой инертную пыль, не вызывающую респираторных заболеваний. Соответствующий технический контроль на участках обработки хлопчатобумажного текстиля (см. Рисунок 4) наряду с рабочими методами, медицинским наблюдением и средствами индивидуальной защиты может по большей части устранить биссиноз.Мягкая стирка хлопка в системах периодической стирки и непрерывных системах войлока снижает остаточный уровень эндотоксина как в ворсе, так и в переносимой по воздуху пыли до уровней ниже тех, которые связаны с резким снижением легочной функции, измеряемым объемом форсированного выдоха за 1 секунду.
Рис. 4. Система пылеудаления чесальной машины
Шум
Шум может быть проблемой в некоторых процессах производства пряжи, но на некоторых современных текстильных фабриках его уровни ниже 90 дБА, что является стандартом США, но превышает стандарты воздействия шума во многих странах.Благодаря усилиям производителей оборудования и инженеров по промышленному шуму уровень шума продолжает снижаться по мере увеличения скорости оборудования. Решением проблемы высокого уровня шума является внедрение более современного и бесшумного оборудования. В Соединенных Штатах программа сохранения слуха требуется, когда уровень шума превышает 85 дБА; это будет включать мониторинг уровня шума, аудиометрическое тестирование и предоставление средств защиты слуха всем сотрудникам, когда уровень шума не может быть ниже 90 дБА.
Тепловое напряжение
Поскольку для прядения иногда требуются высокие температуры и искусственное увлажнение воздуха, всегда необходимо внимательно следить за тем, чтобы не превышались допустимые пределы. Хорошо спроектированные и обслуживаемые установки кондиционирования воздуха все чаще используются вместо более примитивных методов регулирования температуры и влажности.
Системы менеджмента профессиональной безопасности и здоровья
Многие современные фабрики по производству текстильной пряжи считают полезным иметь какой-либо тип системы управления безопасностью и гигиеной труда для контроля опасностей на рабочем месте, с которыми могут столкнуться рабочие.Это может быть добровольная программа, такая как «Поиски лучшего в области здравоохранения и безопасности», разработанная Американским институтом производителей текстиля, или программа, предусмотренная такими нормативными актами, как Программа профилактики профессиональных травм и заболеваний штата Калифорния США (раздел 8, Свод правил штата Калифорния, раздел 3203). Когда используется система управления безопасностью и здоровьем, она должна быть достаточно гибкой и адаптируемой, чтобы завод мог адаптировать ее к своим потребностям.
Назад
С поля на производство пряжи
Усилия по модернизации принесли серьезные изменения в U.С. текстильная промышленность. Оборудование было оптимизировано, и многие операции были полностью автоматизированы с помощью компьютеров. Скорость машины сильно увеличилась.
На большинстве фабрик открытие тюков хлопка полностью автоматизировано.
Пух из нескольких тюков смешивается и смешивается вместе, чтобы обеспечить однородное сочетание свойств волокон. Чтобы гарантировать максимальную эффективность работы нового высокоскоростного автоматизированного загрузочного оборудования и постоянство свойств волокна, компьютеры группируют тюки для производства / подачи в соответствии со свойствами волокна.
Смешанный ворс выдувается воздухом из питателя через желоба к чистящим и чесальным машинам, которые разделяют и выравнивают волокна в тонкое полотно. Кардочесальные машины могут обрабатывать хлопок более 100 фунтов в час. Затем полотно волокон на лицевой стороне карты протягивается через устройство в форме воронки, называемое трубой, в результате чего получается мягкая веревочная прядь, называемая лентой (произносится SLY-ver).
В процессе вытяжки смешивают до восьми нитей ленты.Скорость рисования значительно увеличилась за последние несколько лет и теперь может превышать 1500 футов в минуту.
Ровничные рамы вытягивают или вытягивают ленту еще более тонко и добавляют легкую перекрутку в качестве первого шага кольцевого прядения пряжи.
Кольцепрядильные машины дополнительно вытягивают ровницу и добавляют скручивание, делая ее все плотнее и тоньше, пока она не достигнет толщины пряжи или «количества», необходимого для ткачества или вязания ткани. Пряжу можно перекручивать много раз на дюйм.
Кольцепрядильные машины продолжают играть важную роль в этой стране, но все большее распространение получает прядение с открытым концом, ротор которого может вращаться в пять-шесть раз быстрее, чем кольцепрядильная машина.При открытом прядении пряжа производится непосредственно из ленты. Исключается процесс ровницы.
Другие прядильные системы также устранили необходимость в ровнице, а также устранили ключевое ограничение как кольцевого прядения, так и прядения с открытым концом, а именно механическое скручивание. Эти системы, воздушная струя и Vortex, используют потоки сжатого воздуха для стабилизации пряжи. За счет отказа от методов механического скручивания Air Jet и Vortex работают быстрее и производительнее, чем любые другие системы прядения с коротким штапелем.
После прядения пряжа плотно наматывается на бобины или трубки и готова к формованию ткани. Слойная пряжа — это две или более одинарных пряжи, скрученных вместе. Шнур — это сложенная пряжа, скрученная вместе.
USDA ERS — Хлопок и шерсть
На этой странице представлена информация о:
Хлопок — одно из важнейших текстильных волокон в мире, на долю которого приходится в среднем около 25 процентов всего мирового потребления волокна. Соединенные Штаты являются третьим по величине производителем хлопка в мире и ведущим экспортером хлопка, на долю которых приходится треть мировой торговли хлопком-сырцом.На хлопковую промышленность США ежегодно приходится более 21 миллиарда долларов на продукцию и услуги, создавая более 125000 рабочих мест в отраслях промышленности от фермы до текстильной фабрики.
ERS предоставляет ряд отчетов и информационных продуктов по рынкам хлопка, включая внутренние и международные предложения, спрос, торговлю и цены.
Периодические, запланированные выходы
- Обзор хлопка и шерсти Отчет за 9 месяцев в году, в котором представлены прогнозы предложения и использования для U.S. и мировые рынки хлопка, основанные на самых последних оценках мирового спроса и предложения в сельском хозяйстве .
- Краткий обзор WASDE Ежемесячная интерактивная визуализация, которая предоставляет ключевые данные и основные моменты из оценок мирового предложения и спроса в сельском хозяйстве Министерства сельского хозяйства США на полевые культуры, а также животноводство и молочные продукты.
- Таблицы Ежегодника хлопка и шерсти Годовой информационный продукт, содержащий статистику производства, предложения, использования, торговли и цен на хлопок и шерсть в США.Таблицы также включают ряды и индексы внутренних и мировых цен; Государственные данные о посевных площадях, урожайности и производстве хлопка; и конверсия импорта и экспорта текстиля в США.
- Эквиваленты необработанного волокна данных о торговле текстилем в США Годовой информационный продукт, который обеспечивает объем торговли текстилем в США в эквиваленте сырого волокна. Эти данные используются для отслеживания и оценки потребительского спроса в США на текстильные изделия, отслеживания тенденций изменения доли волокна и обеспечения понимания уровня использования хлопка на фабриках в мире.Этот набор данных содержит исторические годовые данные, а ежемесячные данные публикуются в Cotton and Wool Outlook .
- Товарные издержки и доход s Продукт данных, который предоставляет годовые оценки производственных затрат и прибылей по основным полевым культурам, включая хлопок.
- Базовые прогнозы Министерства сельского хозяйства США Годовой отчет, опубликованный в феврале, который предлагает 10-летние прогнозы для сельскохозяйственного сектора на основе годового долгосрочного анализа Министерства сельского хозяйства США.Связанная с Базовая база данных охватывает прогнозы для четырех основных кормовых культур (кукуруза, сорго, ячмень и овес) в дополнение к другим основным кормовым культурам и животноводству.
Другие публикации ERS, касающиеся хлопка и шерсти
Помимо периодических отчетов Outlook и информационных продуктов, ERS публикует отчеты, охватывающие вопросы, важные для рынка хлопка в Соединенных Штатах и во всем мире. Последние отчеты ERS, касающиеся хлопка, включают:
Обработка хлопка-сырца | Как обрабатывается хлопок
Мы потратили столетие на совершенствование нашего процесса
Как происходит процесс изготовления изделий из хлопка? Наша готовая продукция проходит обширный процесс очистки на нашем заводе по переработке хлопка, прежде чем попадет в руки потребителей.
Хлопок-сырец сначала поступает в плотно упакованных тюках, и эти тюки со временем подвергаются ряду этапов, в конечном итоге претерпевающих кардинальные изменения. Хотя хлопок-сырец содержит клетчатку, из-за того, как собирают хлопок, он также несет с собой мелкие части растений и полевой мусор (без ворса или посторонних предметов), которые необходимо тщательно удалить.
Многие люди также не знают, что хлопковое волокно имеет покрытие из натурального воска, которое защищает его от дождя, что, в конечном итоге, делает его гидрофобным (что является причудливым словом для обозначения водоотталкивающих свойств).Это означает, что хлопок-сырец непригоден для использования во многих потребительских товарах, требующих впитывающей способности, а это свойство имеет решающее значение для многих видов хлопка.
Решение проблемы водоотталкивающих свойств и водопоглощения — лишь одна из причин того, что хлопок подвергается переработке, и, как вы прочитаете дальше, отделке, чтобы он мог трансформироваться, чтобы соответствовать ожиданиям конечного потребителя в отношении характеристик продукта, не теряя при этом его естественных качеств.
Шаг первый: механическая очистка (EVŌC) и образование корки
Первый шаг в нашем процессе — пропустить его через обрабатывающую машину, которая открывает плотные пучки волокна из тюков хлопчатобумажного волокна.Волокно подается в бункер, который механически разделяет пучки волокон, а затем открытое волокно подается в серию передовых технологий очистки, которые мы назвали EVŌC (сокращение от Enhanced Visual, Opening, Cleaning system), которые удаляют большая часть растительных веществ, таких как стебли, стебли и листья, а также посторонние вещества и мусор.
Хотя цель состоит в том, чтобы удалить весь безворсовый материал, на самом деле он никогда не удаляется на 100% с помощью только механического метода очистки.Остальная часть процесса проводится в больших сосудах, называемых киерами. Эти киеры можно нагревать и создавать повышенное давление для ускорения процесса влажной очистки.
Хлопок намочен и упакован в большие лепешки с дырочкой посередине (для идеального вида представьте себе пирог Bundt). Затем хлопковые лепешки опускают в кир и закрывают.
Шаг второй: чистка
Далее, во время обработки хлопка, раствор, содержащий гидроксид натрия, закачивается в установку для очистки хлопка.По мере нагрева и повышения давления раствор щелочи непрерывно прокачивается через кек. За это время воск на волокне омыляется (превращается в водорастворимое мыло), оставшееся растительное вещество размягчается, а пектины и другие нецеллюлозные материалы находятся во взвешенном состоянии, чтобы их можно было смыть.
По прошествии заданного времени при повышенной температуре и давлении, чтобы обеспечить полную очистку, омыленный воск и взвешенные материалы смываются пресной водой.После очистки хлопковое волокно становится абсорбирующим, а оставшиеся небольшие количества растительного вещества размягчаются.
Шаг третий: очищение
После слива промывочного раствора в кир закачивается очищающий раствор. Barnhardt использует только перекись водорода в качестве окислителя (очищающего), что делает наш процесс полностью бесхлорным (TCF).
Перекись водорода отбеливает волокна, окисляя красящее вещество. Поскольку в процессе очистки оставшееся растительное вещество размягчается, очищающее средство может более эффективно проникать в растительный материал и также делать его белым.
Очищающий раствор прокачивается через кек в течение заданного времени при повышенной температуре, чтобы удалить все цветные тела. Затем очищающий раствор смывается пресной водой, а резервуар опорожняется.
На этом этапе обработки хлопка все примеси и красящие вещества волокна удалены, и волокна хлопка представляют собой чистую целлюлозу.
Шаг четвертый: обработка волокна
Хотя покрытие из натурального волокна (воск) было удалено, волокно может быть трудно обрабатывать из-за высокого уровня трения волокна о волокно.Следовательно, чтобы обеспечить эффективную обработку на высокопроизводительном оборудовании для формования полотна, необходимо добавить волокнистую отделку (смазку).
В зависимости от области применения могут применяться многие типы волоконной отделки. Эти отделочные растворы прокачиваются через лепешки, что позволяет нанести на хлопковые волокна желаемый уровень отделки. По достижении желаемого уровня финишный раствор сливают.
Шаг пятый: открытие и сушка
На этом последнем этапе влажные лепешки снова открываются в пучки волокна, и волокно сушится до определенного уровня влажности, который был предварительно определен спецификациями заказчика.
После тюкования содержание влаги измеряется, а затем печатается на этикетках, которые прикрепляются к каждому тюку, — окончательная подпись, которая позволяет нашим клиентам узнать, что их хлопок прошел тщательную обработку Barnhardt для обеспечения идеального качества хлопка.
Процесс производства хлопка
Это сообщение может содержать партнерские ссылки. Ознакомьтесь с полной политикой раскрытия информации здесь.
От поля до ткани в процессе производства хлопка сырые волокна превращаются в нити, пряжу и ткань в три этапа: подготовка, прядение и ткачество.
В Америке до XIX века этот процесс был утомительным и трудоемким занятием, выполнявшимся вручную. Для большинства колонистов они либо сами делали домотканое изделие из хлопка, льна или шерсти, либо покупали ткань, импортированную из Англии. С развитием современных технологий процесс производства хлопка занимает меньше времени.
Препарат
Для изготовления ниток или ткани хлопок-сырец должен быть очищен от мусора.Семена, заусенцы, грязь, стебли и листья удаляются с хлопка во время очистки.
Изобретенный Эли Уитни в 1794 году хлопкоочиститель был одним из многих изобретений, созданных во время американской промышленной революции.
разбивают модули на части, и подает хлопок в джин.
Некоторые устройства подачи модулей имеют гигантские конвейеры, перемещающие модули в стационарные головки.
Другие устройства подачи модулей являются самоходными и движутся по рельсовому пути вместе с модулями.
Хлопковые модули в джинПопадая в хлопкоочистительную машину, хлопок-сырец проходит через сушилки и через несколько очистительных машин, которые удаляют с хлопка отходы джина, такие как заусенцы, грязь, стебли и листья. После тщательной очистки и высыхания хлопок попадает в стойку для джина, где дисковые пилы с маленькими острыми зубьями выщипывают волокно из семян. Этот процесс делает ленту более гладкой, что позволяет производить более однородную пряжу. Затем хлопок плотно упаковывается в тюки, готовые к переработке в текстиль.
Несмотря на то, что хлопок очищается во время процесса джина, он далеко не такой чистый, как должен быть. Хлопковые волокна выбриваются из тюков и отправляются через серию чистящих и сушильных машин. Смешанный и взбитый хлопок поступает в чесальную машину, которая завершает очистку и выпрямление волокон, превращая их в мягкую раскрученную веревку, называемую ленточкой (произносится как хитрый).
Лента вытягивается на более тонкую прядь и слегка скручивается для повышения прочности, затем наматывается на шпульки (катушки, намотанные с нитевидным продуктом для хранения).
Теперь он называется ровницей, и шпульки с ровницей готовы к процессу прядения.
Прядильная
На современных прядильных машинах пряжа идет прямо с ленты. Прядильные устройства берут волокна из ленты и вращают ее до 2500 оборотов за секунду, что превращает волокна в пряжу для ткачества или вязания в ткани.
Прядение — последний процесс в производстве пряжи. Сегодняшние фабрики вытягивают и скручивают ровницу в пряжу и помещают ее на катушки.Они делают это достаточно эффективно. Большая современная фабрика может произвести достаточно пряжи или ниток за 30 дней, чтобы обернуться вокруг Земли 2300 раз или вернуться на Луну и вернуться с нее 235 раз. С помощью автоматической намотки бобины пряжи переносятся на бобины большего размера, называемые сырными конусами. Эти сырные рожки можно хранить до тех пор, пока они не понадобятся в процессе плетения.
Ткачество
Ткацкие станки ткают хлопчатобумажную пряжу в ткани так же, как первые ткацкие станки вручную. Современные ткацкие станки работают на больших скоростях, переплетая продольные нити (основа) и поперечные нити (уток).
Основа — это пряжа, идущая в продольном направлении в тканых изделиях. При подготовке нитей основы к ткачеству сотни нитей пряжи наматываются из сырных конусов на большой пучок основы. Затем пряжа на этой балке покрывается крахмальной смесью (замасливателем) для повышения прочности ткачества.
Хлопковое переплетение — пряжа основы и уткаУток — это пряжа, которая проходит поперечно в тканых изделиях и может называться пряжей для наполнения. Калибровка не производится по утку, потому что в процессе ткачества требуется гибкость.
На самых современных фабриках уток подается в ткацкий станок из сырных конусов с помощью воздушных форсунок с такой высокой скоростью, что его движение невозможно увидеть.
Ткань, называемая серыми товарами, отправляется на отделочную фабрику, где она отбеливается, предварительно усаживается, окрашивается, набирается и получает специальную отделку перед тем, как из нее будет изготавливаться одежда или товары для дома. Другие машины производят трикотаж для рубашек, свитеров или одеял.
хлопок | Описание, история, производство, использование, ботаническое название и факты
Хлопок , семенное волокно нескольких видов растений рода Gossypium, , принадлежащих к семейству гибискусов или мальвы (Malvaceae).
хлопчатобумажный комбинатКрупный план хлопкового завода.
© Comstock Images / JupiterimagesПодробнее по этой теме
Истоки сельского хозяйства: Механизированное оборудование для хлопка
Механизация также существенно сократила трудозатраты, необходимые для выращивания хлопка. В состав оборудования входят трактор, ножницы двухрядные, дисковые (до …
)Хлопок, одна из ведущих сельскохозяйственных культур в мире, производится в изобилии и экономично, что делает хлопковые продукты относительно недорогими.Из волокон можно изготавливать самые разные ткани — от легких вуалей и шнурков до тяжелых парусиновых полотен и бархатных тканей с толстым ворсом, подходящих для самых разных видов одежды, предметов домашнего обихода и промышленного использования. Хлопковые ткани могут быть чрезвычайно прочными и устойчивыми к истиранию. Хлопок принимает много красок, обычно его можно стирать и гладить при относительно высоких температурах. Его удобно носить, потому что он быстро впитывает и отводит влагу. Когда требуется тепло, его можно ворсировать, при этом ткань становится пушистой.Были разработаны различные процессы отделки, чтобы сделать хлопок устойчивым к пятнам, воде и плесени; для повышения устойчивости к складкам, уменьшая или устраняя необходимость в глажке; и уменьшить сокращение отмывки не более чем до 1 процента. Нетканый хлопок, полученный путем сплавления или склеивания волокон вместе, полезен для изготовления одноразовых изделий, которые будут использоваться в качестве полотенец, салфеток для полировки, чайных пакетиков, скатертей, бинтов, а также одноразовой униформы и простыней для больниц и других медицинских целей.
Обработка хлопкового волокна
Хлопковые волокна можно условно разделить на три большие группы в зависимости от длины штапеля (средней длины волокон, составляющих образец или тюк хлопка) и внешнего вида. Первая группа включает тонкие блестящие волокна с длиной штапеля от примерно 2,5 до 6,5 см (примерно от 1 до 2,5 дюймов) и включает виды высочайшего качества, такие как хлопок Си-Айленд, египетский хлопок и хлопок пима. Наименее многочисленный и сложный в выращивании длинноволокнистый хлопок дорогостоящий и используется в основном для производства тонких тканей, пряжи и чулочно-носочных изделий.Вторая группа включает стандартный средневолокнистый хлопок, такой как American Upland, с длиной штапеля примерно от 1,3 до 3,3 см (от 0,5 до 1,3 дюйма). Третья группа включает коротковолокнистый грубый хлопок длиной от 1 до 2,5 см (от 0,5 до 1 дюйма), используемый для изготовления ковров и одеял, грубых и недорогих тканей и смесей с другими волокнами.
Большая часть семян (семена хлопка) отделяется от волокон с помощью механического процесса, называемого джиннингом. Хлопчатобумажный хлопок в тюках отправляется на текстильную фабрику для производства пряжи.Традиционным и все еще распространенным методом обработки является кольцевое прядение, при котором хлопковая масса может быть подвергнута вскрытию и очистке, сбору, прочесыванию, расчесыванию, вытяжке, ровнице и прядению. Кипу хлопка открывают, и его волокна механически сгребают, чтобы удалить посторонние предметы (например, почву и семена). Сборщик (захватывающая машина) затем заворачивает волокна в холст. Кардочесальная машина расчесывает свободные волокна в ряды, которые соединяются в мягкий лист или полотно, и формирует из них свободную нескрученную веревку, известную как лента для карточек.Для получения более качественной пряжи кардочесальная лента пропускается через гребнечесальную машину, которая дополнительно выпрямляет скобу и удаляет нежелательные короткие отрезки или зазубрины. На стадии вытяжки (вытяжки) серия валков с регулируемой скоростью ослабляет и измельчает ленту до плотных однородных прядей подходящего размера. Более тонкие пряди получаются в процессе ровинга (смачивания), при котором лента превращается в ровницу путем вытягивания и легкого скручивания. Наконец, ровница переносится на прядильную машину, где она протягивается дальше, скручивается на кольцевом прядильном устройстве и наматывается на бобину в качестве пряжи.
Кардочесальная машинаКардочесальная машина на текстильной фабрике.
© Yongnian Gui / Dreamstime.com Получите подписку Britannica Premium и получите доступ к эксклюзивному контенту. Подпишитесь сейчасБолее быстрые методы производства включают роторное прядение (тип прядения с открытым концом), при котором волокна отделяются от кардочесальной ленты и скручиваются внутри ротора по мере того, как они присоединяются к концу пряжи. Для производства смесей хлопка может использоваться воздушное прядение; В этом высокоскоростном методе воздушные потоки оборачивают свободные волокна вокруг прямой ленточной сердцевины.Смеси (композиты) производятся во время обработки пряжи путем соединения вытянутого хлопка с другими штапельными волокнами, такими как полиэстер или казеин.
хлопкопрядениеРоторные прядильные машины на фабрике грубой хлопчатобумажной ткани.
© Voy-ager / FotoliaПроцедура вплетения хлопковой пряжи в ткань аналогична процедуре для других волокон. Хлопковые ткацкие станки переплетают натянутую продольную пряжу, называемую основой, с поперечной пряжей, называемой утком, или наполнителем. Нити основы часто обрабатывают химическими веществами, чтобы предотвратить разрыв во время ткачества.
Различные виды хлопка, выращиваемого в качестве сельскохозяйственных культур, являются аборигенными для большинства субтропических частей мира и многократно независимо одомашнивались. Хлопок можно найти как многолетнее древовидное растение в тропическом климате, но обычно его выращивают как кустарниковый однолетник в умеренном климате. В то время как в тропиках он вырастает до 6 метров (20 футов) в высоту, при культивировании он обычно составляет от 1 до 2 метров (от 3 до 6,5 футов). Через 80–100 дней после посадки у растения появляются белые цветки, которые меняют цвет на красноватый.Оплодотворенные цветы опадают через несколько дней и заменяются небольшими зелеными треугольными стручками, называемыми коробочками, которые созревают через 55–80 дней. В этот период семена и прикрепленные к ним волоски развиваются внутри коробочки, которая значительно увеличивается в размерах. Волосы семян, или хлопковое волокно, достигающие максимальной длины около 6 см (2,5 дюйма) у длинноволокнистых разновидностей, известны как пух. Пух — волокна, которые значительно короче семенных волосков и более тесно связаны с семенами, образуются в результате второго роста, который начинается примерно через 10 дней после того, как начинают развиваться первые семенные волоски.При созревании коробочка превращается в белый пушистый шар, содержащий от трех до пяти клеток, каждая из которых содержит от 7 до 10 семян, встроенных в массу семенных волокон. Две трети веса семян хлопчатника (т.е. семян с приставшими семенными волосками) составляют семена. Волокна состоят из 87-90% целлюлозы (углеводного растительного вещества), 5-8% воды и 4-6% природных примесей.
Хотя хлопок можно выращивать между 30 ° северной широты и 30 ° южной широты, урожайность и качество волокна в значительной степени зависят от климатических условий, и лучшие качества достигаются при высоком уровне влажности в результате дождя или орошения во время вегетационного периода и засушливых, теплое время года в период сбора урожая.
Чтобы избежать повреждения хлопка ветром или дождем, его собирают, как только коробочки открываются, но поскольку коробочки не все созревают одновременно, выбирается оптимальное время для уборки с помощью механических средств. Сбор вручную, проводимый в течение нескольких дней, позволяет отобрать созревшие и раскрытые коробочки, так что возможен более высокий урожай. Ручной сбор также дает значительно более чистый хлопок; механические комбайны собирают коробочки всасыванием, накапливая рыхлый материал, пыль и грязь, и не могут отличить хороший хлопок от обесцвеченного.Химический дефолиант обычно применяется перед механической сборкой, чтобы растения сбрасывали листья, тем самым способствуя более равномерному созреванию коробочек.
Вредители и болезни
Хлопок подвергается нападению нескольких сотен видов насекомых, в том числе таких вредных видов, как долгоносик, розовая совка, хлопковая листовая червь, хлопковая блохина, хлопковая тля, клоп-моллюск, конхуэла, южный зеленый вонючий, паутинный клещ. (красные пауки), кузнечики, трипсы и потускневшие насекомые.Ограниченный контроль над ущербом, наносимым насекомыми-вредителями, может быть достигнут путем правильного выбора времени посадки и других методов культивирования или путем селективного выведения сортов, обладающих некоторой устойчивостью к повреждению насекомыми. Химические инсектициды, которые были впервые представлены в начале 1900-х годов, требуют осторожного и избирательного использования по экологическим соображениям, но, по-видимому, являются наиболее эффективным и действенным средством борьбы. Обычное производство хлопка требует больше инсектицидов, чем любая другая основная культура, а производство органического хлопка, в котором используются несинтетические инсектициды, растет во многих местах по всему миру.Кроме того, был разработан генетически модифицированный «Bt-хлопок» для производства бактериальных белков, токсичных для травоядных насекомых, что якобы снижает количество необходимых пестицидов (). Устойчивый к глифосату хлопок, который может переносить гербицид глифосат, также был разработан с помощью генной инженерии.
долгоносик пузырчатыйдолгоносик пузырчатый ( Anthonomus grandis )
Гарри Роджерсдолгоносик коробчатый ( Anthonomus grandis ), самый серьезный вредитель хлопка в Соединенных Штатах в начале 1900-х годов, наконец, был уничтожен соответствующими методами выращивания и применением таких инсектицидов, как хлорированные углеводороды и органофосфаты.В конце 1950-х был зарегистрирован вид долгоносика, устойчивый к хлорированным углеводородам; с этим видом эффективно борются смесью токсафена и ДДТ (дихлордифенилтрихлорэтан), которая, однако, запрещена в США и некоторых других странах. Розовая совка ( Pectinophora gossypiella ), впервые обнаруженная в Индии в 1842 году, распространилась по странам-производителям хлопка, вызывая среднегодовые потери урожая до 25 процентов, например, в Индии, Египте, Китае и Бразилии.Контроль и карантин на пораженных территориях помог ограничить распространение насекомого, а искоренение стало возможным на нескольких относительно небольших территориях при достаточно строгом контроле. Коробчатый червь ( Heliothis zea, также известный как кукурузный червь) питается хлопком и многими другими дикими и культурными растениями. Своевременное применение инсектицидов обеспечивает довольно эффективный контроль.
Растения хлопчатника подвержены болезням, вызываемым различными патогенными грибами, бактериями и вирусами, а также нематодам (паразитическим червям) и физиологическим нарушениям, также классифицируемым как болезни.По оценкам, потери в некоторых африканских странах и Бразилии достигают 50 процентов. Поскольку молодые сеянцы особенно чувствительны к атаке комплекса болезнетворных организмов, обработка семян перед посадкой является обычным делом. Были выведены некоторые сорта, устойчивые к бактериальному заболеванию, называемому угловатой пятнистостью листьев. Фумигация почвы умеренно способствовала борьбе с такими грибковыми заболеваниями, как фузариозное увядание, вертициллезное увядание и техасская корневая гниль, которые ограничены определенными условиями почвы, количеством осадков и общим климатом.Однако селекция устойчивых сортов оказалась более эффективной.
Ганс-Дитрих Х. ВейгманнПодробнее читайте в связанных статьях Britannica:
Истоки сельского хозяйства: Механизированное оборудование для хлопка
Механизация также существенно сократила трудозатраты, необходимые для выращивания хлопка.Оборудование включает трактор, двухрядный нож для стеблей, диск (для измельчения стеблей), грядку (для формирования гребней или грядок), сеялку, культиватор, опрыскиватель и комбайн. Хлопок Волокно убирают очесывающим комбайном, разработанным…
США: экономика
… для бума в производстве хлопка на Юге.Если к середине столетия южане европейского происхождения стали рассматривать рабство, на которое опиралась хлопковая экономика, как «позитивное добро», а не «необходимое зло», как они ранее считали систему, то это было в значительной степени из-за все более возрастающей центральная роль…
Индия: культуры
… техническая техническая культура — хлопок.Махараштра, Гуджарат и Пенджаб — основные штаты, выращивающие хлопок. Джут, в основном из Западной Бенгалии, Ассама и Бихара, является вторым по величине натуральным волокном. Большая часть его экспортируется в переработанном виде, в основном в виде мешковины. Еще более грубое волокно получается из кокосового волокна, внешнее…
Хлопчатобумажная пряжа — обзор
12.2.12 Трение
Трение хлопчатобумажной пряжи в основном важно при машинном вязании, особенно при вязании относительно тонкой пряжи на высокоскоростных вязальных машинах.В общем, измеряются два типа трения пряжи или их комбинация, а именно трение пряжи о металл (или иногда трение пряжи о керамику) и пряжа с пряжей (ASTM D3412), поскольку они представляют типы трения чаще всего встречается на практике. Трение пряжи определяет силы трения и натяжение, создаваемые пряжей, поскольку, например, она скользит по направляющим для пряжи, натяжным устройствам, вязальным иглам и грузилам, самой пряже или другим видам пряжи. Если трение пряжи чрезмерно, натяжение пряжи может превысить ее прочность на разрыв, что приведет к обрывам пряжи, например, во время намотки или вязания.Наиболее эффективным и широко используемым средством уменьшения трения является нанесение смазки, например, с использованием диска из твердого парафина из парафина, на пряжу, когда она наматывается на упаковку, во время намотки или во время роторного прядения. Иногда смазочный материал (или смягчитель) наносится на красильную ванну после окрашивания упаковки, в то время как в некоторых случаях эмульсионная смазка наносится во время наматывания, например, с помощью облицовочного валика.
Доступны различные коммерческие тестеры трения и методы испытаний (например, ASTM D3108), большинство из которых измеряют натяжение, возникающее в нити, когда она проходит по цилиндрической или плоской металлической поверхности, или саму по себе коэффициент трения между нитью и металлом. (μ) можно оценить, измерив натяжение нити (T 1 ) перед поверхностью и натяжение (T 2 ) после поверхности (рис.12.6), используя следующее классическое уравнение для кабестана:
12.6. Диаграммы, показывающие методы приложения натяжения к пряжи: (а) плоская пластина; (б) шпиль; (c) и (d) система двойных плоских пластин.
(источник: PJ Kruger, Text . Месяц , февраль 1970 г.)12,8T2 / T1 = eμΘandT2 = T1eμΘ
, где Θ = общий угол контакта (в радианах) между пряжей и цилиндром, а e = основание (2.