Технология производства минеральной ваты, производители в России
Каменная вата — это разновидность утеплителя, изготовленного на основе габбро-базальтовых горных пород, который позволяет выполнять тепло- и звукоизоляцию различных сооружений или же осуществлять противопожарную защиту.
Благодаря своим физико-химическим свойствам данный тип утеплителя служит в качестве основной энергосберегающей технологии при отделке фасадов, кровли, полов и инженерных сетей как промышленных, так и полупромышленных и бытовых объектов.
Технология производства каменной минеральной ваты
Производство минеральной (базальтовой) ваты заключается в плавке горных пород при температуре 1500 С. После чего, жидкая лавоподобная масса с помощью центрифуги, специальных фильтров на основе платины или других тяжело плавких металлов и сильных воздушных потоков вытягивается в каменные волокна.
Далее в полученные волокна добавляются различные водоотталкивающие добавки и пластификаторы, после чего, при температуре порядка 200 С происходит процесс полимеризации в результате чего оборудование для производства минеральной ваты выпускает готовые базальтовые плиты, которые разрезаются в соответствии с необходимыми размерами.
Химический состав каменной ваты
Поскольку производство теплоизоляционных материалов данного класса осуществляется исключительно из горных пород, полученные базальтовые волокна имеют следующий химический состав:
- Диоксид кремния SiO2 в количестве от 45 до 55%.
- Диоксид титана TiO2 с массовой долей от 1.36 до 2%.
- Оксид кальция CaO в количестве от 7 до 11%.
- Окислы железа FeO и Fe2O3 с массовой долей от 5,38 до 13,5%.
- Оксид мангана MnO в диапазоне от 0,25 до 0,5%.
- Оксид алюминия Al2O3 с процентной долей от 14 до 20%.
- Оксид марганца MgO в количестве от 3 до 8%.
- Оксида натрия и калия (Na2O, K2O) в количестве от 2,7 до 7,5%.
- Прочие вещества составляют не более 5%.
Все вышеуказанные оксиды связываются между собой при помощи битумных, синтетических или композиционных связующих, или же при помощи бентонитовой глины.
Основной показатель качества полученного базальтового волокна — это модуль кислотности, который зависит от соотношения между кислотными и основными (лужными) окислами. Его значение регламентируется согласно требованиям ГОСТ 4640-93 «ВАТА МИНЕРАЛЬНАЯ. Технические условия».
Согласно вышеуказанному документу, каменная вата подразделяется на 3 категории:
- Категория «А» с показателем модуля кислотности от 1,6 и выше.
- Категория «Б» с показателем модуля кислотности в диапазоне от 1,4 до 1,6.
- Категория «С» с показателем модуля кислотности ниже 1,4.
Как видно из вышеуказанной категорийности, чем выше показатель модуля кислотности, тем высшего качества получается базальтовая вата, поскольку она является более долговечной и влагостойкой.
Очень часто для регулирования вышеуказанного показателя производители применяют различные добавки на основе карбонатных соединений.
Виды и сфера применения базальтовых волокон
Оборудование для производства минеральной ваты позволяет изготавливать следующие виды каменного (базальтового) волокна:
- Микротонкие волокна для изготовления фильтров тонкой очистки воздушной или жидкостной среды с диаметров волокон менее чем 0.6 мкм.
- Ультратонкие каменные волокна применяются в фильтрах тонкой очистки воздушной, газовой или жидкостной среды, или же при изготовлении сверхлёгких звуко- и теплоизоляционных материалов с диаметров волокна в диапазоне от 0,6 до 1 мкм.
- Супертонкие (микрокристаллические) базальтовые волокна служат для изготовления теплозвукоизоляционных гидрофобизированных изделий (матов или рулонов), различных жгутов и фильтров. Данный тип волокон считается наиболее популярным, поскольку благодаря специальной термической обработке, полученные микрокристаллы способны выдерживать температуру на 200 С выше чем предыдущие типы волокон. Также супертонкое микроволокно (диаметр от 1 до 3 мкм) не усаживается в процессе эксплуатации, что значительно увеличивает спектр применения данного материала.
- Тонкие волокна на минеральной основе представляют собой хаотические структуры с диаметром волокна в диапазоне от 9 до 15 мкм. Длинна отдельных волокон колеблется в диапазоне от 3 до 2000 мм. Данный материал широко применяется в фильтрах грубой очистки, а также при производстве минерального утеплителя для промышленных нужд.
- Утолщенные каменные волокна в большинстве случаев применяются в качестве основных систем фильтрации дренажных систем. Толщина данного типа волокон колеблется в диапазоне от 15 до 25 мкм, а длинна от 5 до 1500 мм.
- Толстые волокнистые структуры представляют собой хаотически расположенные волокна с диаметром от 25 до 150 мкм и длинной одного волокна от 0,05 до 3 м. Благодаря этому полученный материал может выдерживать колоссальные нагрузки на разрыв до 650 МПа.
- Грубые волокна — дисперсионно волокнистая масса из волокнистых структур толщиной от 150 до 500 мкм. Данная разновидность утеплителя может применяются в качестве армированного слоя при помощи специальных вяжущих элементов.
Сфера применения базальтовой (каменной) ваты
В связи с тем, что каменная вата является натуральным негорючим и долговечным материалом (поскольку на 95% состоит из натурального камня) она широко стала применятся в строительстве еще с начала 20-го века.
Благодаря своим отменным свойствам, которые заключаются в снижении потерь тепловой энергии в холодный период времени, и в сокращении попадания тепловой энергии вовнутрь здания летом, каменная вата широко применяются в следующих сферах:
- При утеплении фасадов зданий с последующей штукатуркой или монтаже сайдинга или профильного листа.
- При утеплении помещения изнутри (балконы, лоджии, наружные стены и т.д.).
- При возведении перегородок из листов ГКЛ в квартирах, промышленных или офисных зданий для звукоизоляции.
- При утеплении основания пола с последующей заливкой стяжки.
- Для звукоизоляции «плавающего пола».
- При устройстве кровли или утеплении мансардных этажей.
- Для огнезащиты инженерных конструкций и сетей (данный материал способен выдерживать температуру до 700 С).
Достоинства каменной ваты (базальтового утеплителя)
Высокая химическая стойкость. Благодаря этому свойству материал не реагирует с щелочами и кислотами и имеет повышенную стойкость к продуктам нефтепереработки и растворителям.
Пористая структура. Благодаря данному свойству волокна составляют всего 70% от общего объема материала. Остальная часть — это прослойки воздуха, которые обеспечивают низкую теплопроводность полученного материала.
Огнеупорность. Данное свойство позволяет производить утепление как паропроводов, так и промышленного оборудования с высокими температурами. Поскольку материал изготавливается из натурального камня, он способен выдерживать температуру до 7000С.
Высокая паропроницаемость. Благодаря этому свойству материал не впитывает, а пропускает через себя влагу без образования конденсата.
Основные производители каменной ваты
На современном рынке, существует 3 основных производителя минеральной ваты на базальтовой основе:
- Технониколь.
- Knauf.
- Rockwool.
Минеральная вата Технониколь
Данный материал служит для тепло- и звукоизоляции фасадов, кровли, перегородок и технологических трубопроводов. Плотность данного материала находится в диапазоне от 30 (РОКЛАЙТ и ТКХНОЛАЙТ Экстра) до 145 кг/м3 (ТЕХНОФАС).
На современном рынке России, данный продукт представлен следующими разновидностями:
Наименование | Номинальная плотность, кг/м3 | Тепловая характеристика, Вт/м*0С | Область применения |
РОКЛАЙТ | 30 | 37-41*10-3 | Теплоизоляция стен и перегородок внутри помещения, утепление скатной кровли и полов на лагах |
ТЕХНОЛАЙТ ЭКСТРА | 35 | 36-41*10-3 | Устройство звуко- и теплоизоляции перегородок офисных и бытовых помещений |
ТЕХНОФАС | 145 | 36-42*10-3 | Утепление фасадов перед последующей штукатуркой или отделкой с помощью сайдинга |
ТЕХНОФЛОР | 90-170 | 34-47*10-3 | Утепление плавающих, теплых или наливных полов с последующим устройством цементно-песчаной стяжки |
ТЕХНОРУФ | 140-190 | 36-42*10-3 | Основной теплоизоляционный слой при новом строительстве или проведении реконструкции кровельного покрытия без необходимости в последующей стяжке |
ТЕХНОБЛОК СТАНДАРТ | 45 | 34-39*10-3 | Утепление и звукоизоляция всех типов зданий и сооружений, в которых слой утеплителя не подвержен высоким статическим нагрузкам |
ТЕХНОВЕНТ СТАНДАРТ | 80-90 | 33-40*10-3 | Устройство вентилируемых фасадов |
Базальтовая вата Knauf
Каменная вата Кнауф — это эффективная тепло- и звукоизоляция на основе горных пород, которая обладает высокой паропроницаемостью, химической стойкостью к кислотам, лугам и продуктам нефтепереработки.
На рынке России данный материал выпускается под маркой Knauf Insulation и представлен следующим ассортиментом:
Наименование | Номинальная плотность, кг/м3 | Тепловая характеристика, Вт/м*0С | Область применения |
Insulation DDP | 150-200 | 40*10-3 | Утепление и звукоизоляция плоской кровли, угол наклона которой не превышает 150 |
Insulation DDP-K | 105-110 | 37-41*10-3 | Утепление и звукоизоляция плоской кровли, угол наклона которой не превышает 150, а также для утепления плавающих полов |
Insulation FKD | 140-150 | 39*10-3 | Утепление наружных фасадов здания или устройство вентилируемых фасадов |
Insulation FKD-S | 100-140 | 36*10-3 | Утепление стен снаружи и устройство скрепленных фасадов |
Insulation FKL | 85 | 40*10-3 | Наружное утепление стен перед монтажом сайдинга |
Insulation HTB | 35-150 | 37-39*10-3 | Утепление инженерных сетей, трубопроводов и воздухопроводов с температурой от -180 до 7000С |
Insulation LMF AluR | 35-90 | 40*10-3 | Утепление инженерных сетей, трубопроводов и воздухопроводов с температурой от -180 до 7000С |
Insulation PVT | 175 | 40*10-3 | Утепление перекрытий и плавающих полов |
Insulation WM 640 GG/WM 660 GG | 80-100 | 35*10-3 | Утепление технологического оборудования и трубопроводов |
Insulation цилиндры | 75 | 40*10-3 | Техническая изоляция инженерных сетей и трубопроводов |
Базальтовая вата Rockwool
Продукция концерна Роквул — это высокоэффективные гидрофобизированные минеральные плиты, изготавливаемые из базальтовой породы с добавлением специальных добавок для улучшения технических характеристик.
Компания предлагает на территории России следующий ассортимент:
Наименование | Номинальная плотность, кг/м3 | Тепловая характеристика, Вт/м*0С | Область применения |
EPIROCK | 20 | 45*10-3 | Утепление вентилируемых перекрытий, а также деревянных полов на лагах |
ROCKROLL | 22 | 44*10-3 | Утепление вентилируемых перекрытий, а также деревянных полов на лагах |
ROCKSLAB ACUSTIC | 50 | 36*10-3 | Звукоизоляция перекрытий и перегородок помещений различного назначения |
ROCKSLAB | 26 | 42*10-3 | Утепление стен, потолков и полов без нагрузки на слой каменной ваты |
STEPROCK HD | 140 | 39*10-3 | Утепление строительных конструкций и перекрытий с высокими динамическими нагрузками |
ROCKMIN | 26 | 39*10-3 | Устройство не нагружаемого теплоизоляционного слоя |
STEPROCK HD4F | 140 | 39*10-3 | Устройство динамического модуля упругости для производственных и жилых зданий |
FRONTROCK S | 110 | 39*10-3 | Утепление фасадов зданий и сооружений с последующим нанесением армированного слоя и штукатурки |
MONROCK MAX E | 115-220 | 37*10-3 | Утепление всех типов перекрытий без необходимости в последующем устройстве цементно-песчаной стяжки |
FIREROCK | 80 | 42*10-3 | Теплоизоляция поверхности каминов и технологического оборудования |
Выводы
Оборудование для производства минеральной ваты позволяет изготавливать высокоэффективные утеплители для любых типов помещений, а также обеспечивать надёжную тепло- и звукоизоляцию как кровли, так и полов, и стен.
На современном рынке можно найти большое разнообразие минеральных утеплителей на основе базальтовых пород, которые обладают не только высокими техническими характеристиками, но и обеспечивают огнеупорность технологическим трубопроводам в соответствии с мировыми стандартами.
Каменная (базальтовая) вата: производство, особенности, преимущества, применение
Волокнистые неорганические материалы с функцией тепловой и звукоизоляции образуют группу популярных утеплителей – минеральная вата. Представляющие группу разновидности материала своим характерным свойствам обязаны исходному сырью для их производства. В технологии получения каменной ваты такими определяющими компонентами являются горные породы естественного вулканического происхождения.
Именно такой состав увеличивает долговечность конечного продукта, значительно повышает его теплоизоляционные и влагоотталкивающие свойства. Очевидно, что подобный утеплитель с улучшенными физико-химическими характеристиками стал основой большинства энергосберегающих технологий для многих отраслей и видов деятельности.

Содержание статьи
Производство каменной ваты, технология заводского процесса
Английское словосочетание для обозначения базальтового утеплителя при дословном переводе на русский язык звучит как «горная шерсть». Представляя внешний вид утеплителя, и зная, что сырьем для производства служат горные габбро-базальтовые породы, с этим определением можно согласиться.
Впервые изверженные и застывшие волокна вулканической лавы, как будто взбитые и похожие на пучки шерсти, были найдены 15 веков назад. Их можно считать прототипом современной каменной (базальтовой) ваты, которую запустили в производство в далеком 1897 г. на американском континенте. Для рядового потребителя утеплитель стал доступен позже. В нашей стране его популярность и стабильный рост продаж приходится на последние три десятилетия. Пора узнать, в чем заключается технологический процесс получения «горной шерсти».

Многоступенчатая технология заключается в искусственном повторении на заводе по производству утеплителя сложных природных условий извергающейся лавы. 1500°С – температура печи, в которую попадает измельченный вулканический камень базальтовой группы и доводится до жидкого лавообразного состояния.

Расплавленная масса из отверстий питателя стекает в сопла специальных раздувочных приспособлений. Сжатым воздухом (9 атм.) струя разбивается на мелкие капли, которым придается огромное ускорение. Разлетаясь на выходе из сопла, частицы расплава удлиняются и после мгновенного охлаждения превращаются в небольшие тонкие волокна. Эта стадия производства утеплителя хорошо продемонстрирована в начальном отрезке представленного видеоматериала:
При осаждении полученных штучных волокон, в объем камеры вводят распылением необходимый связующий состав для объединения всех волокон в цельный «ковер».
Далее основа будущего утеплителя проходит обработку жидкими составами, помогающими повысить его паропроницаемость, водоотталкивающие характеристики и плотность. На следующем этапе «ковер» поступает в камеру тепловой обработки, где при 200°С происходит поликонденсация. Теперь полотно можно разрезать и отправлять на упаковку.

Химический состав каменной ваты
Сырьем для производства каменной ваты преимущественно выступает базальтовая порода и ограниченная доля метаморфических пород со схожим химическим составом.
Примерный процентный состав основных компонентов сырья для производства утеплителя:
- 45-65% – SiO2.
- 10-20% – Al2O3.
- 5-15% – FeO и Fe2O3.
- 7-11% – CaO.
- 5-10% – MnO.
Оставшаяся доля приходится на оксиды других металлов и прочие вещества.
Важным показателем качества ваты является соотношение между окислами – кислыми и основными. Параметр характеризуется модулем кислотности, с увеличением которого улучшается термическая и химическая стойкость волокна, вата приобретает дополнительную водоотталкивающую способность и становится более долговечной.
ГОСТ 4640-93 определяет типы минерального утеплителя с диаметром волокон 6-12 мкм по величине модуля кислотности:
- Тип А – свыше 1,6.
- Тип Б – 1,4-1,6.
- Тип В – 1,2-1,4.
Продукцию из волокон меньшего диаметра автоматически определяют, как минеральную вату типа А.
Для получения заданной плотности и формы в состав утеплителя при производстве вводится связующий компонент (чаще синтетический). В готовом изделии его массовая доля не превышает 2%. Причем, вещество присутствует в связанном состоянии, поэтому оно инертно к внешней среде и безопасно для здоровья.
Обратите внимание! При создании единого утепляющего слоя не применяют каменную вату с различной плотностью.
Базальтовые волокна: классификация и применение производимых видов
Базальтовые волокна делятся на непрерывные, длина которых может превышать 50 км, и штапельные – отрезки небольшой длины. Толщина (диаметр) волокон измеряется миллионными долями метра – микрометрами (мкм). Этот параметр лежит в основе их классификации:
- Микротонкие – диаметром до 0,6 мкм. Эти волокна востребованы при производстве аппаратов тонкой очистки различных сред.
- Ультратонкие – диапазон толщины 0,6-1,0 мкм. Используются в фильтрах, а также для получения сверхлегких материалов с универсальными изоляционными свойствами.
- Супертонкие – 1-3 мкм. Область применения – фильтры, утеплительные маты, жгуты. Материал не усаживается, его теплостойкость на 200°С превышает показатели предыдущих типов.
- Тонкие – 9-15 мкм. Популярные волокна для изоляторов промышленного назначения и грубых фильтрующих изделий.
- Утолщенные – 15-25 мкм. Основной материал для фильтрации в различных дренажных системах.
- Толстые – 25-150 мкм. Полотно из хаотично сплетенных волокон, с длиной каждого до 3 м, отличается выдержкой к усилиям на разрыв. Величина выдерживаемой нагрузки может достигать 650 МПа (примерно, это сила в 65 кг, приложенная к каждому квадратному миллиметру площади поперечного сечения).
- Грубые – 150-500 мкм. В комбинации со специальными вяжущими компонентами, такие волокна часто выступают как армирующая прослойка.

Сфера применения базальтовой (каменной) ваты
Области применения базальтового утеплителя обусловлены уникальными физико-механическими и эксплуатационными свойствами материала. Основные сферы, в которых каменная вата нашла применение:
- Устройство вентилируемых фасадов и утепление поверхностей под окончательную штукатурку.
- Внутренняя теплоизоляция лоджий и балконов, несущих стен (при отсутствии возможности выполнить наружные работы).
- Шумо- и теплоизоляция пустотелых перегородок жилых помещений и офисов.
- Тепловая защита полов, перекрытий, мансард, кровли.
- Огневая защита коммуникаций, инженерных конструкций, несущих балок и колонн из металла.
- Обустройство бань и парных.
- Тепловая изоляция плит, печей, жарочных шкафов.
- Наполнение сэндвич-панелей и каркасных конструкций.
- Изоляция конструкций бытовых и промышленных холодильников.
- Скорлупы для изоляции трубопроводов и вентиляционных возвуховодов.

Важно! Менее плотные образцы утеплителя отличаются хорошей эластичностью. Это качество помогает при защите фигурных, сложных, ассиметричных поверхностей и элементов строительных конструкций.
Достоинства каменной ваты (базальтового утеплителя)
Перечисленные преимущества относятся непосредственно к утеплителям из базальтовых волокон:
- Служба изоляционного материала превышает 50 лет.
- Утеплитель не боится следующих факторов влияния: ультрафиолетовых лучей, температурных перепадов, влажности, агрессивных химических составов и веществ, технических масел, грибка, бактерий, грызунов, насекомых.
- Низкая теплопроводность утеплителя объясняется хаотичной структурой каменных волокон, объем которых ограничен размерами плиты. Все пространство между волокнами заполняется статичным воздухом, а он практически не участвует в теплопередаче. Благодаря таким особенностям базальтовая вата отлично удерживает тепло внутренних помещений в холода, и препятствует быстрому их прогреву в жару.
- Паропроницаемость – очень важное положительное свойство каменного утеплителя. Через толщу волоконного материала легко отводится и испаряется лишняя влага и конденсат, способные разрушать материал изолированных поверхностей.
- Материал базальтового теплоизолятора не горит, сдерживает распространение огня, выдерживает колоссальный нагрев (свыше 1000°С) без разрушения структуры и выделения удушающих или отравляющих веществ.
- Значительный диапазон возможной плотности материала облегчает задачу подбора плит определенной жесткости и прочности для решения конкретных задач.
- Экологическая чистота природного сырья и произведенного из него материала.
- Универсальность. Об этом качестве базальтового утеплителя говорит предыдущий раздел со списком основных сфер применения материала.
- Дополнительное создание акустического комфорта в помещениях, которые утеплялись базальтовой ватой.
- Разнообразие и доступность для потребителей ваты различной плотности, формы выпуска, назначения, линейных размеров и толщины.
- Удобство хранения, транспортировки и погрузки легкого материала. Простота резки и монтажных работ для исполнителей без достаточного опыта.

Полезная информация! Электроизоляционные и диэлектрические свойства характерны для волокон из базальтовых камней. Поэтому изделия из них «прозрачные» для магнитных полей и излучений любой природы.
Главные качества, за которые профессионалы-строители и частные застройщики выбирают именно каменный утеплитель, продемонстрированы в видеоматериале:
Известные фирмы-производители
Из поставщиков минеральной ваты рассматриваемого типа выделяются несколько крупных компаний. Их конкуренция, стремление постоянно улучшать качество и не завышать стоимость товара, только на руку потенциальному потребителю.
Минеральная вата Технониколь
Образец качества отечественного товара, который вышел на международный рынок. Сеть представительств торговой марки включает более трех десятков стран. Варианты выпускаемой продукции относятся к нескольким линейкам: частное и профессиональное строительство, варианты огнезащиты, техническая изоляция.

Базальтовая вата Knauf
Производство каменной изоляции является лишь одной их линеек выпускаемых фирмой материалов, отделки и комплексных систем. Но качество выпускаемых утеплителей от этого не страдает, а предлагаемый ассортимент помогает решить любую задачу.
Продукция Rockwool
Датская торговая марка славится качеством выпускаемых марок товара. Из 28 заводов компании, на российского потребителя работают 4 производственных комплекса на территории РФ. В ассортименте Rockwool несколько серий выпускаемой продукции различного назначения: утеплители для кровли, фасадов, квартир и зданий, огнезащиты, шумоподавления, изоляции инженерных систем, сооружений нефтегазового комплекса.
Не отстают в борьбе за покупателя и другие производители изоляционных материалов из базальтовых волокон – Эковер и ISOROC. Первое молодое предприятие находится у источника сырья (на Урале) и быстро прогрессирует. А тамбовский завод компании ISOROC, после масштабной модернизации, гарантирует соответствие продукции отраслевым и мировым стандартам.
Проверенная технология и промышленное оборудование последнего поколения позволяют производить высокоэффективные минеральные теплоизоляторы, которые надежно утепляют любые поверхности и проложенные коммуникации. Получить более высокий уровень защиты помогает каменная вата из базальтовых пород. Если требуется обеспечить класс теплоизоляционной защиты, соответствующий самым строгим стандартам, нужно обратить внимание именно на этот материал.
Вконтакте
Одноклассники
Как производят каменную вату — Как это сделано, как это работает, как это устроено — LiveJournal
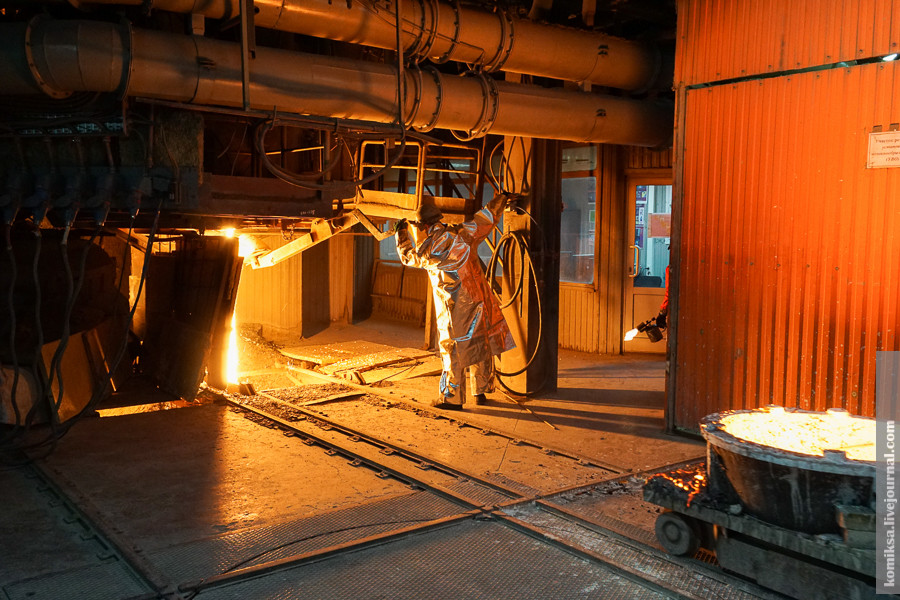
В сентябре этого года мы с Наталей Меелис 13vredina, Анастасией Сергеевой yaginya и Евгением Вовнеем vovney побывали в г. Юрга Кемеровской области, на заводах по производству рулонных кровельных материалов, экструзионных пенополистирольных плит и каменной ваты.
Сегодня мой рассказ и показ о третьем заводе — заводе по производству каменной (базальтовой) ваты.
«Быстрее! Быстрее пойдемте смотреть на процесс!» — позвали нас, увлекшихся вырезанием лего из экструзионного пенополистирола (мне из ЭПП сердечко вырезали!).
Заинтригованные, мы думали, что сейчас из этих серых полистирольных кубиков еще что-нибудь забабахают, но нас посадили в машину и помчали к другому заводу.
Завод по производству каменной ваты стал третьим заводом корпорации ТехноНИКОЛЬ в Сибири и на юргинской площадке в частности. В 2013 году с конвеера только этого завода сети вышло почти 900 тысяч кубов продукции.
Каменная вата является высокоэффективным теплоизоляционным материалом. По термической эффективности она готова соперничать с эталонным теплоизолятором – воздухом в неподвижном состоянии. Высокое сопротивление теплопередачи достигается за счёт удержания большого количества воздуха в неподвижном состоянии внутри утеплителя при помощи тесно переплетённых тончайших волокон минеральной ваты.
Наталя 13vredina с плодами трудов из XPS.
На заводе мы нарядились в респираторы и пошли в цех. Каски и жилеты уже были на нас.
Такого, конечно, я не видела никогда. Для кого-то это трудовые будни, а для меня это было завораживающее зрелище: мужчины в серебряных костюмах и шлемах колдовали у вагранки (это такая шахтенная печь). Почему-то в голове вертелась песня Чичериной: пожаааарные в серебряных касках добрые и ласссковые…
Производство каменной ваты — это сложный, многоступенчатый технологический процесс.
Горные породы габбро-базальтовой группы (сырье) доставляются на склад сырья.
В начале производственного цикла сырье просеивается и крупная фракция подается на дозаторы, которые тщательно взвешивают сырьевые компоненты.
Только после этого шихта (смесь исходных компонентов) подается в вагранку — вертикальную шахтную печь. Установленные на заводе коксогазовые вагранки на горячем дутье позволяют получить расплав требуемой температуры (около 1500 °С) и нужной вязкости.
Это жерло той самой вагранки. Там внутри порядка 1500 градусов по Цельсию!
Схематично вагранка выглядит примерно так:
Почти что дверь в Нарнирю.
а потом из печи полился расплавленный металл!
После тележку с чашей быстро оттаскивает второй прекрасный мужчина в серебряных одеяниях.
Это выплавленный из базальта металл — отходы производства. Потом на этом же заводе из него сделают брикеты, которые потом также будут пущены в расход.
Итак, полученный расплав направляется на многовалковую центрифугу, где под действием центробежной силы капли расплава вытягиваются в волокно. Исходное сырье и стабильность состава расплава позволяют получить качественную минеральную вату с высокой химической стойкостью и долговечностью. В момент волокнообразования через форсунки, установленные на центрифуге, подается связующее с добавками гидрофобизатора и обеспыливателя по новейшей технологии, разработанной в собственном научном центре компании.
Нам не удалось увидеть этот процесс собственными глазами, но нам рассказали, что это похоже на то, как получается сахарная вата.
Многовалковая центрифуга
Только из базальта.
Процесс выплавки закончился, а мы все стояли завороженные и продолжали щелкать камерами фотоаппаратов и телефонов. Нас вывели из транса и пока в недрах машин вытягивались каменные волокна, мы последовали в цех, где происходит остальное действо.
Безопасности на заводе уделяется очень много внимания. Повсюду — в цехах, на погрузочных площадках и на территории заводского комплекса развешаны мотивирующие плакаты.
Не знаю как брутальных мужчин, а меня пробрало и я даже старалась не сходить с пешеходных дорожек. Вот эти белые зебры — это траектория движения пеших посетителей.
Так вот, из многовалковой центрифуги базальтовое волокно, обработанное связующим, охлаждаясь потоком воздуха, попадает на транспортер. Так образуется первичный «ковер» из минеральной ваты, который поступает на маятниковый раскладчик, обеспечивающий равномерную плотность производимой продукции.
Маятниковый раскладчик.
После маятникового раскладчика «ковер» поступает на гофрировщик-подпрессовщик, который придает будущему изделию гофрированную структуру за счёт частичной вертикальной ориентации волокон, что позволяет добиться высоких механических свойств готовой продукции.
Гофрировщик-подпрессовщик.
Сформированный таким образом «ковер» поступает в камеру термообработки, где при температуре 200-250°С происходит отверждение связующего и задаются основные физико-механические характеристики.
От качества проведения этого процесса зависит качество продукции в целом. Все технологические процессы на линии контролируются автоматикой. В условиях повышения норм, регламентирующих отклонения от заданных геометрических размеров строительных материалов, большое внимание уделяется точности резки готовых изделий.
Наталя 13vredina радуется жизни
Кстати, резать можно не только по прямой. Вот пример затейливой фигурной резки. Жаль, нам не дали повырезать как в лаборатории пенополистирола, а то мы бы ух!
Готовая к применению продукция упаковывается в специальную термоусадочную пленку, которая позволяет хранить поддоны с продукцией под открытым небом, без потери товарного вида и ухудшения эксплуатационных качеств продукции.
Кстати, заводы поразили меня обилием естественного света в производственных помещениях. Я ожидала чего-то другого, видимо исходя из моих представлений о полузаброшенных цехах на заводах где десятилетиями не мылись пыльные окна.
Из цеха нас повели в испытательную лабораторию, где минвату рвали, топили, жгли, а также показывали фокусы.
Лаборатория проверки качества продукции
Сначала рвали. Вот такими машинами.
[результат испытания в кПа и прочих цифрах]результат испытания в кПа и прочих цифрах
[результат испытания в кПа и прочих цифрах]
Потом топили
Как видно, вода скаталась на поверхности в кругляши, внутрь не впиталась.
Потом нас привели в большую комнату и отожгли стали жечь вату газовой горелкой, отчего на ней образовалось коричневое пятно, но загореться она так и не загорелась. Технология.
Тепловизор нам говорит, что под струей горелки горячо.
Чтобы все было без обмана, с обратной стороны поджигаемой плиты ее можно было трогать руками.
Кстати тут видно, что сквозное пятно от огня не образовалось.
На тепловизоре все учтено и зафиксировано. Плита с обратной стороны нагрелась только от соприкосновения с рукой.
Потом было самое любопытное для меня испытание. Самое — потому что я адепт тишины. Будь моя воля, я бы звукоизолировала все, потому что меньше всего я хочу знать о чем говорят иностранные штукатуры-маляры за стеной и о чем плачет соседский ребенок. Ну еще не люблю, когда топают над головой. Поэтому тест на звукоизоляцию был для меня интересен более других. Я даже не пожалела телефона для такого мероприятия.
В гипсокартонный бокс с минватой добровольцы сложили свои любимые звонилки.
Ларчик закрывается
В этот момент остальные, кто зажал мобилку с камерой позвонить, набирают нам. В комнате звенящая тишина, в которую врываются только гудки дозвона.
Ящик открывается и вуаля! Кому-то не повезло и 5й айон превратился в будильник и трубку гороского телефона. Шутка. Для чистоты эксперимента мы складывали туда всё шумящее, что было в лаборатории.
Я не удержалась и задала в лаборатории вопрос: «а правда ли, что расположенная вертикально, каменная вата со временем оседает?» (Это я прочитала, когда выбирали входную дверь)
«Нет, не правда,» — сказали мне. Продукция бывает для горизонтальной укладки и для вертикального размещения. Правильно подобранный по назначению материал гарантированно сохраняет свои свойства несколько десятков лет. При этом в глазах не было ни тени сомнения. Я в уме стала просчитывать расход на звукоизоляцию стен с соседями.
Евгений vovney делает серьезное лицо, как будто сам придум
Вата — Википедия
Сырьё для производства хлопковой ваты — коробочка хлопчатникаВа́та (от нем. Watte[1]) — пушистая масса волокон, слабо переплетённых между собой в различных направлениях.
Этимология
Существуют следующие версии происхождения слова «вата»:
- Слово пришло в русский язык из японского в XVII веке в результате торговых связей между Россией и Японией, начиная с первой встречи японца Денбея с Петром I в 1697 году и последующего указа о налаживании торговых отношений России с Японией. Другими словами, которые были заимствованы в этот период и прочно ассимилировались в русском языке, являются «иваси» и «сакура»[2].
- Согласно М. Фасмеру[3], слово заимствовано из немецкого языка (Watte), в который оно попало предположительно из арабского wáḍḍa или batin «подкладка».
Виды ваты
По способу получения различают ваты: естественную — шерстяную, шёлковую, пуховую, хлопковую, льняную, пеньковую, сосновую, асбестовую, и искусственную — целлюлозную, стеклянную, металлическую, шлаковую, базальтовую.
Естественная вата по назначению разделяется на одёжную, мебельную, техническую (термоизоляционная, огнестойкая и др.), прокладочную, листовую клеёную и медицинскую.
Изготовление ваты
При изготовлении ваты растительные волокна расщипываются, разрыхляются и очищаются от примесей, полученная волокнистая масса формируется в так называемые холсты на машинах разрыхлительно-трепального агрегата; бесформенная масса волокна, составляющая холст, на чесальной машине превращается в съём ваты определённой толщины. При производстве медицинской ваты сырьё подвергается варке в щёлочи под давлением и затем обрабатывается гипосульфитом натрия. В результате волокно приобретает белизну и характерные свойства — способность быстро смачиваться и поглощать жидкости.
Виды медицинских ват
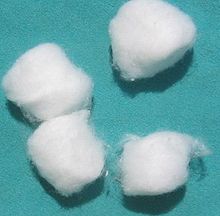
Медицинская вата (лат. Gossypium) — волокно из выростов клеток эпидермы семян (волосков) культивируемых видов хлопчатника (Gossypium L.), более чем на 95 % состоящее из клетчатки.
Различают гигроскопическую и компрессную медицинскую вату. Гигроскопическая вата белая, легко расслаивается, употребляется как материал, впитывающий жидкие выделения (гной, сукровицу) при перевязке ран поверх слоёв перевязочной марли. В зависимости от назначения, различают следующие виды гигроскопической ваты:
- Глазная. Производится из хлопко-волокна 1 сорта;
- Хирургическая. Производится из хлопко-волокна 3 сорта, с включением вискозного волокна 1 сорта не более 30%. Является одним из основных перевязочных материалов.
- Гигиеническая. Производится из хлопко-волокна 5 сорта и линта хлопкового 1 сорта (не более 25%). Используется для гигиенических женских повязок.
Компрессная вата служит для отепления завязанной или забинтованной части тела (например, при согревающих компрессах), а также мягкой подкладкой при наложении шин, иммобилизующих повязок (например, гипсовых).
Вплоть до середины XX века в медицине в основном использовалась хлопковая вата, затем вместе с ней стала распространяться вата вискозная. В 2011 году в России воссоздано производство льняной ваты, в том числе для медицинских целей[4].
Применение
В мировой медицине вата стала применяться на рубеже XIX—XX веков, в первую очередь в военной хирургии, поскольку на лечение ран влияли совершенствующееся оружие и особенности вызываемых им ранений. Впервые использовать гигроскопические повязки для лечения ран на основе хлопковой ваты предложил в 1880 году хирург Королевского госпиталя в г. Бирмингеме Дж. С. Гэмджи[5]. До этого вместо ваты повсеместно использовались льняная или конопляная пенька, кудель, джут или корпия — расщипанная на нити хлопчатобумажная ветошь.
К началу 1890-х годов, по словам врачей-современников, в российской медицине вата «совершенно вытеснила корпию»[6]. Но еще во время Первой мировой войны в российских больницах и госпиталях, наряду с хлопковой ватой, по-прежнему использовали корпию, паклю, кудель и пр.[7].
Искусственная вата широко применяется в строительстве в качестве тепло- и звукоизоляционного материала; в химической промышленности — для фильтрации жидкостей и газов.
Ватилин
Особый вид ваты — так называемый ватилин, то есть вата, проклеенная с одной или с двух сторон клеевой эмульсией. Ватилин — заменитель ваты при шитье одежды, прокладочный материал и др[8].
См. также
Примечания
Литература
- Вата // Большая советская энциклопедия : [в 30 т.] / гл. ред. А. М. Прохоров. — 3-е изд. — М. : Советская энциклопедия, 1969—1978.
- Вата // Краткая энциклопедия домашнего хозяйства. — М.: Государственное Научное издательство «Большая Советская энциклопедия», 1959.
Вата — Википедия
Сырьё для производства хлопковой ваты — коробочка хлопчатникаВа́та (от нем. Watte[1]) — пушистая масса волокон, слабо переплетённых между собой в различных направлениях.
Этимология
Существуют следующие версии происхождения слова «вата»:
- Слово пришло в русский язык из японского в XVII веке в результате торговых связей между Россией и Японией, начиная с первой встречи японца Денбея с Петром I в 1697 году и последующего указа о налаживании торговых отношений России с Японией. Другими словами, которые были заимствованы в этот период и прочно ассимилировались в русском языке, являются «иваси» и «сакура»[2].
- Согласно М. Фасмеру[3], слово заимствовано из немецкого языка (Watte), в который оно попало предположительно из арабского wáḍḍa или batin «подкладка».
Виды ваты
По способу получения различают ваты: естественную — шерстяную, шёлковую, пуховую, хлопковую, льняную, пеньковую, сосновую, асбестовую, и искусственную — целлюлозную, стеклянную, металлическую, шлаковую, базальтовую.
Естественная вата по назначению разделяется на одёжную, мебельную, техническую (термоизоляционная, огнестойкая и др.), прокладочную, листовую клеёную и медицинскую.
Изготовление ваты
При изготовлении ваты растительные волокна расщипываются, разрыхляются и очищаются от примесей, полученная волокнистая масса формируется в так называемые холсты на машинах разрыхлительно-трепального агрегата; бесформенная масса волокна, составляющая холст, на чесальной машине превращается в съём ваты определённой толщины. При производстве медицинской ваты сырьё подвергается варке в щёлочи под давлением и затем обрабатывается гипосульфитом натрия. В результате волокно приобретает белизну и характерные свойства — способность быстро смачиваться и поглощать жидкости.
Виды медицинских ват
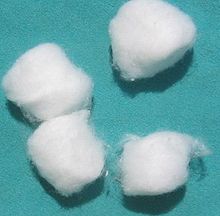
Медицинская вата (лат. Gossypium) — волокно из выростов клеток эпидермы семян (волосков) культивируемых видов хлопчатника (Gossypium L.), более чем на 95 % состоящее из клетчатки.
Различают гигроскопическую и компрессную медицинскую вату. Гигроскопическая вата белая, легко расслаивается, употребляется как материал, впитывающий жидкие выделения (гной, сукровицу) при перевязке ран поверх слоёв перевязочной марли. В зависимости от назначения, различают следующие виды гигроскопической ваты:
- Глазная. Производится из хлопко-волокна 1 сорта;
- Хирургическая. Производится из хлопко-волокна 3 сорта, с включением вискозного волокна 1 сорта не более 30%. Является одним из основных перевязочных материалов.
- Гигиеническая. Производится из хлопко-волокна 5 сорта и линта хлопкового 1 сорта (не более 25%). Используется для гигиенических женских повязок.
Компрессная вата служит для отепления завязанной или забинтованной части тела (например, при согревающих компрессах), а также мягкой подкладкой при наложении шин, иммобилизующих повязок (например, гипсовых).
Вплоть до середины XX века в медицине в основном использовалась хлопковая вата, затем вместе с ней стала распространяться вата вискозная. В 2011 году в России воссоздано производство льняной ваты, в том числе для медицинских целей[4].
Применение
В мировой медицине вата стала применяться на рубеже XIX—XX веков, в первую очередь в военной хирургии, поскольку на лечение ран влияли совершенствующееся оружие и особенности вызываемых им ранений. Впервые использовать гигроскопические повязки для лечения ран на основе хлопковой ваты предложил в 1880 году хирург Королевского госпиталя в г. Бирмингеме Дж. С. Гэмджи[5]. До этого вместо ваты повсеместно использовались льняная или конопляная пенька, кудель, джут или корпия — расщипанная на нити хлопчатобумажная ветошь.
К началу 1890-х годов, по словам врачей-современников, в российской медицине вата «совершенно вытеснила корпию»[6]. Но еще во время Первой мировой войны в российских больницах и госпиталях, наряду с хлопковой ватой, по-прежнему использовали корпию, паклю, кудель и пр.[7].
Искусственная вата широко применяется в строительстве в качестве тепло- и звукоизоляционного материала; в химической промышленности — для фильтрации жидкостей и газов.
Ватилин
Особый вид ваты — так называемый ватилин, то есть вата, проклеенная с одной или с двух сторон клеевой эмульсией. Ватилин — заменитель ваты при шитье одежды, прокладочный материал и др[8].
См. также
Примечания
Литература
- Вата // Большая советская энциклопедия : [в 30 т.] / гл. ред. А. М. Прохоров. — 3-е изд. — М. : Советская энциклопедия, 1969—1978.
- Вата // Краткая энциклопедия домашнего хозяйства. — М.: Государственное Научное издательство «Большая Советская энциклопедия», 1959.
Производство ваты и ватина
Компания «Матрасофф» выпускает два вида ватных матрасов:
- из хлопка. В качестве наполнителя используется швейная белая вата, состав — 100 % хлопок;
- из регенерируемого волокна. Наполнитель — вата РВ серого цвета, изготовленная из остатков х/б ткани со швейных фабрик. В состав входит хлопок с добавлением синтетического волокна (10 %). Это придает изделию упругость и прочность.
На весь ассортимент продукции имеются сертификаты качества и соответствия ТУ и ГОСТу.
Как происходит изготовление ваты и ватина?
Сырье для продукции поступает в кипах весом от 200–300 кг и хранится на сухом складе с естественной влажностью и температурой. Затем его перевозят в цех первичной обработки хлопка или ткани, где на специальном оборудовании сырье разделяют на небольшие пласты и загружают в смеситель непрерывного действия. Здесь наполнитель разъединяют на отдельные кусочки для дальнейшей переработки в вату.
Кусочки ваты по транспортёрной ленте попадают или на щипальную машину (в случае переработки хлопка), или на рубочную машину (в случае переработки ткани).
На щипальной машине сырье разделяют на волокна, производят очистку от пыли и удаляют примеси и инородные частицы. Затем массу загружают в резервный питатель для тщательного перемешивания. Уже отсюда масса попадает в бункер чесальной машины, где вату расчесывают на отдельные волокна. Из волокон образуют тонкий холст шириной около 100 см и проводят еще одну очистку от пыли и примесей.
На следующем этапе в зависимости от сырья производственный процесс различается. Вату для более дешёвых матрасов «Классик» загружают в надувочную камеру и равномерно заполняют сырьем чехол. Вату для более дорогих изделий категории «Премиум» складывают друг на друга, получая холст шириной около 2 м. После этого холст сматывают в рулоны определённого веса и диаметра. Набивка чехла таким наполнителем происходит вручную.
Далее все матрасы попадают в пиковочную машину, где на изделия устанавливают кнопки для предотвращения смещения слоёв ваты внутри. Если изготавливается матрас индивидуального размера, процесс производят вручную.
На последнем этапе к матрасам крепят ярлыки с указанием состава наполнителя, размера и веса изделия, наименованием ГОСТа или ТУ. Готовая продукция попадает на склад.
Таким образом, в нашей компании соблюдаются все требования к технологическим процессам по изготовлению ватных матрасов из хлопка. Контроль качества ведется на всех этапах производства, включая и упаковку готовой продукции.
Приобретая матрасы от компании «Матрасофф» вы можете быть уверены в их качестве! Мы даем гарантию на весь ассортимент: ватные матрасы, включая модели для детей, одеяла, подушки, тюфяки и постельное белье.
А также: Желаете купить в СПб поролоновый матрас напрямую у производителя? Обращайтесь!
секрет производства позаимствовали у блондинок
На одном из омских предприятий наладили выпуск необычной продукции — льняной ваты. По стоимости она не дороже обычного аналога из хлопка, но более качественна и обладает несравненными антисептическими свойствами. Отбеливать вату из льна будут не вредным хлором, а обычной перекисью водорода.
Партиями по четыреста килограммов в ёмкости загружают льняное волокно. Через 10 часов — после варки, отбеливания и сушки — будет готова инновационная льняная вата.
Она только внешне почти не отличается от своего собрата. Но по свойствам разница колоссальная. Эксперимент показал: переработанный лён тонет мгновенно. Насколько быстро такой материал впитывает влагу, для медиков — один из главных показателей качества.
«И антисептические свойства, и кровоостанавливающие свойства, что очень важно в работе медперсонала», — говорит Наталья Фомина, старшая медсестра Омского Областного клинического медико-хирургического центра.
Как сохранить все эти характеристики во время переработки, было главной проблемой для технологов ватного завода. Например, хлор, который обычно используют для отбеливания, полезные свойства льна убивает. Идею невредного для ваты обесцвечивания заимствовали у блондинок. Вместо хлора используют перекись водорода.
«Появляются новые нюансы, с которыми нам приходится сталкиваться, чтобы в результате сохранялись положительные свойства льна», — говорит технолог Алексей Хорошилов.
Отработанную на вате технологию уже планируют применить в производстве других материалов. Из льняного сырья начнут выпускать бинты — это следующий этап производства.
«Будет делаться целый ряд новых инновационных продуктов. Это и перевязочные материалы медицинского назначения, и целлюлоза для волохов и много-много чего еще можно делать», — рассказывает Геннадий Смыслов, президент льноперерабатывающего холдинга «Леном».
Сейчас на ватном заводе разрабатывают бактерицидное покрытие — им будут пропитывать материалы для перевязки. Производство льняной ваты уже налажено. И хотя ничего нанотехнологичного в ней нет, новинку будут продавать именно с приставкой нано-. Если не особые свойства, то эти четыре буквы точно помогут ей оказаться на прилавках.
USDA ERS — Данные о хлопке, шерсти и текстиле
Базовый уровень сельского хозяйства
Прогнозируемые Министерством сельского хозяйства США долгосрочные изменения в мировом сельском хозяйстве отражают устойчивый мировой экономический рост и постоянный спрос на биотопливо, которые в совокупности поддерживают рост потребления, торговли и цен.
Бедность и благосостояние в сельской местности
ИсследованияERS в этой тематической области сосредоточены на экономических, социальных, пространственных, временных и демографических факторах, которые влияют на статус бедности сельских жителей.
Программы детского питания
ERS проводит исследования программ Министерства сельского хозяйства США по детскому питанию и их роли в обеспечении продовольственной безопасности, питания и благополучия детей.Программы обучения ERS, такие как Национальная программа школьных обедов.
COTTON CLUB | Собственное производство
— ведущий производитель хлопчатобумажных изделий и средств гигиены с собственными производственными площадями в РФПроизводственно-складской комплекс
, расположенный в Балашихинском районе Московской области, состоит из нескольких цехов общей площадью более 47000 м²:- Цех по переработке хлопка и нетканых материалов
- Цех по производству нетканых вискозных и полиэфирных волокон
- Цех по производству влажных салфеток
- Цех по производству ваты
- Цех по производству ЖМК и косметической продукции
- Цех по производству ватной ленты
- Производство экструзионных материалов магазин
- Магазин детских одноразовых трусиков и подгузников
- Цех конвертации полотенец и упаковки пищевых продуктов
- Складские помещения
- Логистический комплекс
Одним из ключевых преимуществ Cotton Club является вертикально интегрированное производство, позволяющее полностью контролировать производство процесс как полуфабрикаты (лента, палочки, лосьоны, нетканые материалы), так и готовые изделия.
Cotton Club производит вату из хлопка-сырца. Для производства хлопковой ваты используется технология Water Jet, благодаря которой подушечки имеют гладкую поверхность, не отслаиваются и не линяют.
Оборудование для производства хлопковой ленты компании Marzoli (Италия) используется при производстве собственной ленты.

Для создания полного цикла производства ватных тампонов производится производство пластиковых палочек (оборудование Bellaform, Германия) и стаканов (термопластический автомат TOYO, Япония).
Полиэтиленовые пакеты для ватных дисков и палочек. на ведущем европейском оборудовании (Hetler, Lemo).

Нетканое полотно для салфеток производится на европейском оборудовании Andritz.
Уникальная технология, используемая в компании, позволяет производить 2 вида ткани: MD: CD (направление материала MD к направлению CD-поперечного 1: 1 — материал растягивается равномерно во всех направлениях).
Влажные салфетки доступны в различных форматах упаковки: карманная, большая, откидная, двойная, тройная.

Благодаря трем собственным машинам, Cotton Club имеет возможность производить три типа подгузников: анатомической формы (форма I), классической формы (форма T), одноразовые трусики.
Производство всех слоев подгузника: верхнего листа, заднего листа, ADL, среднего абсорбирующего слоя, а также нетканого материала для ушей и манжет также осуществляется на собственных мощностях.
Возможности типов впитывающего слоя подгузника: целлюлоза + SAP или инновационная разработка, целлюлозный впитывающий слой, состоящий из подушки Air prooff + SAP, не имеющий аналогов в России и Европе.
Используются уникальные запатентованные материалы: Icore, Iproof, 3D wavelron, Doublecore.
Упаковочная линия позволяет упаковать от 1-3 штук до 88 подгузников, что открывает большие возможности для компании и ее покупателей.

Cotton Club Group располагает оборудованием для приготовления косметической массы (кремы, гели, лосьоны, молочко, скрабы и др.), А также ее упаковки: ламинатные тубы для кремов, выдувные бутылки из ПЭТ-преформ, ламинатор. пакеты.
Раздаточный цех может разливать и маркировать продукцию в различных типах упаковки: тубы, банки, бутылки и стоячие пакеты.
Производственные линии для работы с косметической продукцией были разработаны и изготовлены европейской компанией Urlinski.

Cotton Club самостоятельно осуществляет конвертирование фольги, пленки, пергамента, а также упаковывает готовую продукцию в пленку или в картонную коробку.
Производство мешков для мусора осуществляется методом экструзии и окраски полиэтилена высокого и низкого давления. Компания производит пакеты с разными типами низа: звездообразным, прямым, боковым швом; и форматы: стандартные, с затяжками, большие, майка.
