Оборудование для экструдированного пенополистирола XPS
Линии производства экструзионного пенополистирола XPS на вспенивателях Со2 без применения фреона. Линия экструзии основана на самых современных технологиях, что позволяет изготавливать действительно качественный, надежный и долговечный теплоизоляционный материал.
Экструзионный пенополистирол XPS — теплоизоляционный материал с равномерно распределенными замкнутыми ячейками, который не дает усадки и набухания, не впитывает воду, не подвержен гниению. XPS применяется в общегражданском строительстве при устройстве теплоизоляции фундамента, кровли, полов, утеплении фасадов. Экструдированный пенополистирол относится к классу экологически чистых материалов, что делает его вне конкуренции в ряду других утеплителей.
Наш завод занимает доминирующее положение в области оборудования для производства экструзионного пенополистирола с большой производительностью. Наша компетенция позволяет нам вести проекты от консультационного обслуживания до создания производственных команд на предприятиях, с возможностью исполнить проект «под ключ».
Технологический процесс производства экструзионного пенополистирола
С помощью вакуумных загрузчиков компоненты подаются в систему подачи, которая в соответствии с заданной рецептурой осуществляет гравиметрическое дозирование сырья в экструдер. Все бункеры контролируются интегрированной системой управления. В первом экструдере происходит нагрев, расплав и перемешивание сырья, подача вспенивателей. В качестве вспенивателей выступают: СО2, этанол, HFC, LPG, DME. Углекислый газ и этанол являются основными агентами, это значительно снижает себестоимость готовой продукции по сравнению с линиями, работающими только на фреоне.
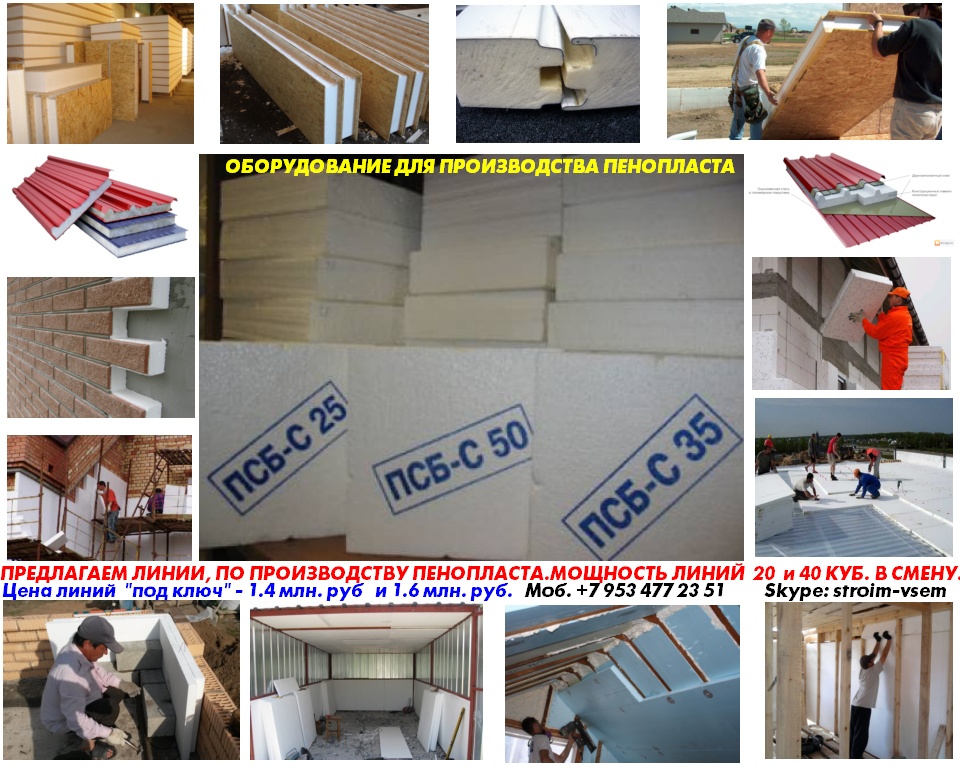
Предлагаем линии экструзии листов XPS производительностью 200-2000 кг/час. Интеллектуальная точная система контроля температуры и давления способствует производству высококачественной продукции. Возможная толщина листов 20-150 мм, ширина 600-1200 мм.
Экструзионная система.
Одношнековый экструдер
По сравнению с двухшнековым экструдером, одношнековый экструдер сохраняет свой статус во многих применениях. Возможный диаметр шнека 20-400 мм, производительность 5-5000 кг/ч.
Серия TDD с высокоэффективным одношнековым экструдером обладает инновационными функциями, которая в основном сосредоточена на энергосберегающем, более точном управлении процессом и более высокой производительности. Снижение удельного энергопотребления, на 30% меньше, чем у традиционных экструдеров. Высокая производительность может быть увеличена на 50% чем у экструдера с одинаковым диаметром. Лучше эффект смешивания. Точный и аккуратный контроль процесса. Более широкое применение: рециркуляция, компаундирование, экструзия труб и экструзия листа / пленки
Двухшнековый экструдер
Двухшнековый экструдер — большой вклад в качество конечного продукта и изменение процесса производства. Оборудование обеспечивает достаточное перемешивание и дисперсию при точном контроле температуры. Охлаждение играет большую роль в производстве пенопласта, которое имеет непосредственное влияние на качество продукта. Наш оригинальный дизайн канала охлаждения обеспечивает достаточную холодопроизводительность и стабильный контроль температуры. Уплотнение всегда является большой проблемой при использовании CO2. Инновационный метод уплотнения перманентно решает эту проблему.
Трехшнековый экструдер
Параллельный трехшнековый экструдер специально разработан для лучшего рассеивания и большей производительности. Свободный объем шнека увеличен на 40%. Супер дисперсия и распределение. Особенности узкого RTD. Идеальное самоочищение. Более высокий крутящий момент и пропускная способность
Модель | Диаметр шнека. мм | Скорость вращения, об/мин | L/D | Мощность, кВт | Производ-ть, кг/ч |
SAT-T52 | 51.4 | 600 | 32-64 | 110 | 300-400 |
SAT-T65 | 62.4 | 600 | 32-64 | 160 | 500-700 |
SAT-T75 | 71 | 600 | 32-64 | 250 | 800-1200 |
Система дозирования вспенивающих агентов
Вспенивающий агент при производстве экструзионного пенополистирола XPS: Со2, CFC, HCFC и др.
Мы предоставляем полный комплект технологической лини, включая калибратор, тянущее устройство, машину обрезку кромки, автомат для резки, укладчик, автоматическую упаковочную систему. Мы настраиваем аксессуары в соответствии с конечной целью клиента или существующим зданием. Планировщик поверхности, установка фрезерования поверхности, тиснение, установка фрезерования канавок по боковой стороне (SL,TG ). Обратитесь в наше компанию с запросом, и мы предоставим вам подробное технико-коммерческое предложение.
Оборудование для производства XPS
Компания «Green Earth®» производит следующую линейку оборудования для производства утеплителя:
Степень автоматизации | |||
Производительность линии, кг/час | Полностью автоматическая | Полуавтоматическая | |
GES-75/GED-200 | 450 — 600 | • | • |
GES-85/GED-250 | 600 — 800 | • | — |
GES-95/GED-300 | 1000 — 1200 | • | — |
GES-120/GED-400 | 1200 — 1500 | • | — |
GES-135/GED-500 | 1500 — 2000 | • | — |
Примечание: Первая цифра в названии (75, 85, 95, 120, 135) означает диаметр шнека первого экструдера в миллиметрах. Первые экструдера компании «Green Earth®» являются двухшнековыми. Вторая цифра в названии (200, 250, 300, 400, 500) означает диаметр шнека второго экструдера в миллиметрах. Второй экструдер одношнековый.
Используемый полимер: полистирол общего назначения (GPPS), первичный и/или вторичный.
Примечание: Возможность работы с использованием 100% вторичного полистирола.
Вспенивающие агенты: основные агенты: CO2 и этанол. Дополнительные агенты: HFC, LPG, DME.
Примечание: При изготовлении плиты толщиной от 30 до 100 мм используются вспенивающие агенты СО2 + этанол. Для производства плиты толщиной 20 мм и от 100 до 180 мм требуется введение третьего вспенивателя.
Используемые добавки: Огнестойкие добавки (антипирены), красители (пигменты), нуклеирующий агент (тальк, концентрат талька).
Параметры готовой продукции:
Вид продукции: Плиты из экструдированного пенополистирола
Ширина: 600 – 1200 мм
Длина: 1200 — 3000 мм
Толщина: 20 — 180 мм
Допустимая плотность: 26 — 70 кг / м3
Прочность на сжатие: 200 — 800 кПа
Комплектация и особенности полуавтоматической линии:
- Однокомпонентная система подачи сырья, рассчитана на предварительное смешивание компонентов.
- Система управления с ручной настройкой режимов работы оборудования.
- Первый двухшнековый экструдер, патент на изобретение. В первом экструдере происходит нагрев, расплав и перемешивание сырья, подача вспенивателей.
- Система подачи вспенивателей, патент на изобретение.
- Система охлаждения экструдеров с ручной регулировкой температур охлаждения и нагрева.
- Гидравлическое устройство замены сеток фильтра
- Второй одношнековый экструдер, патент на изобретение. Во втором экструдере происходит гомогенизация массы расплава и вспенивателей с последующим охлаждением.
- Статический смеситель. Предназначен для дополнительного перемешивания компонентов и вспенивателей.
- Формующая головка – фильера.
- Калибратор, патент на изобретение и тянущее устройство. Формирование ленты утеплителя по заданным параметрам.
- Система рольгангов для охлаждения.
- Устройство для формирования продольной кромки ленты утеплителя.
- Устройство для тиснения поверхности, шлифовка поверхности для лучшей адгезии, нарезка продольных канавок (например, для использования в сэндвич-панелях). Устанавливается опционально, по требованию Заказчика.
- Поперечный резчик (патент на изобретение). Устройство для нарезки ленты утеплителя на плиты заданной длины.
- Устройство для формирования L-кромки (четверти). Устанавливается опционально, по требованию Заказчика.
- Укладчик-штабелер. Устанавливается опционально, по требованию Заказчика.
- Автоматический упаковщик. Устанавливается опционально, по требованию Заказчика.
- Гранулятор. Предназначен для переработки обрезков ленты утеплителя в гранулу полистирола, и повторного использования в производстве.
Комплектация и особенности автоматической линии (основные отличия от полуавтоматической):
- Гравиметрическая система подачи сырья, 4-6 компонентов (марки IKV, Германия).
Данная система обладает высокой точностью подачи компонентов, что позволяет идеально настроить рецептуру.
- Запатентованная система автоматического контроля температуры. Состоит из 12-14 отдельных устройств, каждый из которых контролирует температурный режим на отдельных участках линии.
- Единый центр управления работой линии с возможность удаленного доступа для корректировки и контроля. Система поддерживает заданные параметры, при необходимости корректируя режимы работы оборудования, подачу вспенивателей, подачу сырья и т.д.
Линия по производству пенопласта
Если вы не нашли нужного для вас оборудования — напишите нам и наши менеджеры подберут для вас подходящий станок или линию.
Производство изделий из пенопласта представляет два типа производственных линий.
Первый тип линий работает с формовочными машинами и продукция этой линии:
Упаковка из пенопласта
Различные буквы и формы из пенопласта
Упаковка из пенопласта
Розетки для люстр из пенопласта
Панели настенные и потолочные из пенопласта
Второй вид линии производит блоки из пенопласта и далее отрезной станок вырезает из блока продукцию.
Второй тип линии вы можете посмотреть по ссылке — ССЫЛКА
Далее мы рассмотрим первый тип линии с формовочными автоматами.
Схема работы линии по производству формовочных изделий из пенопласта
Первичный материал EPS загружается в предвспениватель
Предвспениватель
Type: 90
Complete with Fluidized Bed Drier and suction filling pipe
Диаметр расширительного бака : 900 мм ,
Доступны первое и второе расширение
Первичное расширение :12 ~30 г / л
Вторичное расширение :8 ~11г / л
Производительность: 100 ~200 кг / ч
Потребляемая мощность: 9,73 кВт
Вес машины: 1500кг
Общий размер: 4700 × 2930 × 3200 мм
1.Предвспениватель оснащён процессором и сенсорный экраном, что позволяет автоматизировать следующие процессы: загрузку и электронное взвешивание сырья, температурный контроль, контроль уровня материала в камере вспенивателя.
2.Машина оснащена винтовым конвейером и системой электронного взвешивания подачи сырья, Устройства прикреплены у камере вспенивания.
3.Благодаря закрытой камере вспенивания предвспениватель потребляет примерно на 50% меньше пара, чем непрерывный предвспениватель
4.Температура в камере вспенивания контролируется датчиком температуры и позиционным клапаном, что обеспечивает точный температурный контроль
5.С вибрационным датчиком для контроля уровня материала, что обеспечивает допустимое отклонение плотности в пределах ±2%
6.Машина оснащена сушильным аппаратом кипящего слоя, в нём поддерживается температура 70°С. Сушилка выполнена из нержавеющей стали.
Сушка обеспечивает автоматическое просеивание и транспортировку материала в бункера.
Другие типы предвспенивателей
Стоимость предвспенивателей от 10 000$
Далее из предвспенивателя гранулы поступают в отстойник на 8 часов
из отстойника гранулы поступают в формовочный пресс автомат.
Стоимость от 800$
Формовочный пресс автомат
Формовочный автомат
Type:1000B
Размер формы: 1000 x 800 мм
Максимальный размер продукта:
850 x 700 x 330 мм
Время цикла: 60 ~ 90 секунд
Расход пара: ( 12 — 1 5 т) пара на 1 т материала
Расход сжатого воздуха: 1,2 м3 за цикл
Расход охлаждающей воды: 40 ~120 кг за цикл в зависимости от толщины изделий (оборотная вода)
Подключенная нагрузка: 11 кВт
Ход: 170 — 1420 мм
Вес машины: 4500кг
Габаритные размеры:: 4760×1900×4700mm
1.Пресс-автомат оснащён процессором и сенсорным экраном. Усовершенствованная технология формования позволяет производить и зделия из пенополистирола различных форм.
2.Пресс-автомат имеет герметичную камеру загрузки, что обеспечивает высокую скорость подачи материала в пресс-форму. Загрузочная камера позволяет установить от 25 до 37 загрузочных пистолетов.
3.Пресс-автомат оснащён цифровым устройством контроля движения открытия и закрытия формы, положение формы контролируется процессором с выводом на сенсорный экран. Открытие формы осуществляется гидравлической системой.
4.Вакуумная система уменьшает время формования и время охлаждения, а также снижает содержание влаги в нём.
5.Автоматический пресс-автомат подразделяется на 2 вода А и В. Разница состоит в следующем:
Тип А: имеет механическое устройство освобождения формы и выталкивания блока.
Тип В: имеет пневматическое устройство освобождения формы и выталкивания блока.
Видео работы пресс автомата
youtube.com/embed/WnqGFSN_fac»/>
Другие типы пресс автоматов
Стоимость формовочных автоматов от 20 000$
Котёл для производства пара
Производительность пара:1000 кг/ ч
Давление пара :1. 0 МПа
Эффективность : ≥ 92
Топливо : газ
Включают:
1. Главный блок парового котла, горелка (Италия), вентиль основного блока,
2. PLC и система управления на сенсорном экраном;
3. Водяной насос, водоподготовка, резервуар для воды
4. Паровая головка
Стоимость котлов от 15 000$
Резервуар для пара
Объём 6 м3 , максимальное давление 10 бар
Компрессор
Тип 15А
Производительность 2.3 м3 в минуту
Давление 7 бар, Мощность 15 кв
Стоимость линии по производству пенопласта
( цена дана в Китае без таможенного оформления и доставки из Китая)
Линия для производства пенопласта |
Кол-во, шт |
Цена в Китае |
Предвспениватель тип 90 |
1 |
112390 USD |
Формовочный автомат 1000В |
1 |
|
Система хранения для гранул |
2 |
|
Котел для производства пара |
1 |
|
Емкость для хранения пара |
1 |
|
Воздушный компрессор |
1 |
|
Баллоны для сжатого воздуха на 2 м3 |
1 |
|
Камера для прессформы + Инжекторы + Заправочные пистолеты |
1 |
|
Прессформа |
1 |
Так же можно посмотреть линии по производству блоков из пенопласта
Если вы не нашли нужного для вас оборудования — напишите нам и наши менеджеры подберут для вас подходящий станок или линию.
Оборудование для производства листового пенополистирола
(состав оборудования, технические характеристики, требования к помещению, документация)
1. Состав оборудования для комплекса производительностью 40м/куб в смену
Наименование | Количество, шт. |
---|---|
1.Дозатор сырья «ПСВ» — «ДС-300» | 1 |
2.Предвспениватель гранул «ПСВ» — «ВПМ-07» | 1 |
3.Блок-форма — «Ф-1С» | 1 |
4.Станок раскроя блоков — «СПР-12» | 1 |
5.Пневмотранспорт вспененных гранул пенополистирола — «ПГ-10» | 4 |
6.Бункеры выдержки вспененных гранул — 15м/куб. | 3 |
7.Измельчитель обрезков пенополистирола — «ДЦ — 3» | 1 |
8.Парогенератор — «ПМТ — 80-100» | 1 |
9.Паровой накопитель — 1м/куб.![]() | 1 |
10.Вакуумный насос — ВВН-1-3 | 1 |
2.Марки производимого комплексом пенполистирола по ГОСТ 15588-86
Марка пенополистирола. | Допускаемая плотность, кг. на 1м/куб. |
---|---|
М 15 | 10,0 — 14,8 |
М 25 | 15,0 — 24,0 |
М 35 | 25,0 — 34,0 |
3.Технические характеристики для комплекса, производительностью 40м/куб в смену.
Характеристика. | Показатель. |
---|---|
Производительность, м/куб. за 1 рабочую смену. | для марки М15 — 25-30. |
Потребление эл.энергии, кВт/час. | 18-25. |
Сумарная мощность, кВт. | 90. |
Потребление воды, Л за 1 рабочую смену.![]() | 300-350. |
Занимаемая площадь, м.кв. | 90-120. |
Обслуживающий персонал, кол-во человек. | 2. |
Переработка получаемых при производстве отходов пенополистирола, | повторное использование. |
4.Требования к производственному помещению
1. Требуемая площадь под установку оборудования, м.кв, | 90-120. |
2.Требуемая высота потолка, | 3,7 — 3,8 |
3.Температурный режим, град С. | +15…+30 |
4.Система водоснабжения, кол-во Л. в смену, | 300-500. |
5.Энергоснабжение, кВт.суммарной нагрузки, | 100-120. |
6.Вентиляция, | Принудительно,приточно-отточная. |
7.Другие требования, | наличие подъездных путей, складских, бытовых |
5.
Прилагаемая документация.
- Технологический регламент на производство.
- Паспорта и руководства по эксплуатации установок.
- Инструкции по монтажу и пуско-наладке комплекса.
- Сертификаты.
- Сопроводительная, бухгалтерская документация.
6. Шеф-монтаж, пуско-наладочные работы
Предприятием-изготовителем выполняется полный комплекс работ по монтажу и пуско-наладке оборудования, на месте установки, предоставленном организацией- заказчиком.
Выполняются следующие виды работ:
- Шеф-мотаж всего комплекса оборудования.
- Пуско-наладка всех единиц оборудования.
- Получение образцов конечной продукции.
- Обучение вновь прибывшего персонала.
Данные работы выполняются представителем предприятия-изготовителя, с выездом на место установки оборудования.
7. Описание, краткие технические характеристики единиц оборудования
Предназначен для автоматизированной и равномерной подачи исходного сырья «ПСВ», в установку предварительного вспенивания гранул, применение дозатора позволяет получать гранулы с требуемым насыпным весом. Использование дозатора сырья, позволяет автоматизировать процес вспенивания гранул, в процессе работы предварительно настроенный дозатор позволяет избежать длительного наблюдения за процессом и быстро изменять настройки подачи не прекращая вспенивание
Предвспениватель предназначен для предварительного вспенивания исходного сырья ПСВ. Гранулы исходного сырья поступая в рабочую камеру предвспенивателя, подвергаются тепловой обработке паром, вследствие чего происходит вспенивание гранул и увеличение в объеме в 50 раз. Рабочая камера предвспенивателя выполнена из нержавеющей стали, вследствие чего установка имеет большой ресурс, проработанность конструкции позволяет получать высокое качество производимых гранул.Оснащение: Частоно-регулируемый привод подающего шнека, система отвода конденсата, люк аварийной выгрузки сырья, собственный пульт управления, универсальный подающий шнек, дополнительно оснащается автономным парогенератором.
ПодробнееПредвспениватель средней производительности, предназначен для линий с производительностью менее 40 м. куб в смену, полностью аналогичен ВПМ-07, различие только в объеме рабочей камеры и производительности.Рабочая камера предвспенивателя выполнена из нержавеющей стали, вследствие чего установка имеет большой ресурс, проработанность конструкции позволяет получать высокое качество производимых гранул.Оснащение: Частоно-регулируемый привод подающего шнека, система отвода конденсата, люк аварийной выгрузки сырья, собственный пульт управления, универсальный подающий шнек, дополнительно оснащается автономным парогенератором.
Предназначена для формования вспененных гранул пенополистирола в блоки, форма разработана в соответствии с современной технологией изготовления пенополистирола. В блок-форму засыпают вспененные гранулы из бункера загрузки, после чего производят наполнение формы паром под небольшим давлением, гранулы разогреваясь повторно увеличиваются и под давлением спекаются между собой образуя блок пенопласта.Блок-формы выпускаются различной длинны, ширины и высоты, для производства пенопласта с размерами для сандвич панелей типа «Экопан», панелй из профильного листа и др. Для производства сандвич панелей производятся формы с размерами 1030х3030х530мм, 1230х2930х490мм, возможно изготовление блок-формы под другие размеры.Для блок-формы разработана специальная паропроницаемя проставка, позволяющая изменять длину получаемых блоков в пределах до 1000мм, что позволяет изготавливать блоки пенопласта, под несколько размеров панелей. Детали формы изготавливаются методом лазерного раскроя, включая лазерную перфорацию внутренних паропроводящих стенок.По желанию заказчика, внутренние стенки блок-формы облицовываются нержавеющей сталью с лазерной перфорацией.Оснащена; эл.приводом верхней крышки, бункером загрузки, системой замков быстрого запирания, высококачественными уплотнителями из высокомолекулярного силикона, выдерживающего температуру до 300 градусов.
Все процессы производства блока пенопласта в форме, полностью автоматизированы, что позволяет добиваться высокого качества пенопласта и производительности. Производительность составляет 12-14 м. куб пенопласта в час.Блок-форма выполнена по горизонтальной схеме, с фронтальным извлечением блока, данная компоновка позволяет изготавливать форму требуемого размера.За счет конструкции снижено потребление формы, что позволило не увеличивать мощность всей линии.
Станок оснащен частотно-регулируемым приводом портала,что позволяет резать пенополистирол любой марки, с высоким качеством, блок при резке остается неподвижным, резка осуществляется подвижным порталом за счет чего достигается высокая точность реза, одновременно с разрезанием на листы, обрезаются внешние кромки блока в размер, полный цикл раскроя выполняется за один постанов блока на раму станкаВозможно изготовление станка по размерам заказчика.
ПодробнееНовая разработка нашей компании — полностью автоматический станок для раскроя блоков пенопласта. Станок отличается высокой геометрической точностью и качества раскроя, что достигается за счет применения высокоточных алюминиевых направляющих.
Предназначен — для измельчения обрезков пенополистирола на исходные гранулы, для вторичного использования их при производстве пенополистирола, измельченные обрезки добавляются к основному сырью в соотношении до 30% от общей массы основного сырья, что делает производство пенополистирола безотходным, также измельчитель может использоваться при производстве полистиролбетона, для измельчения использованной упаковки и др. отходов пенополистирола, качество дробления позволяет добавлять измельченный пенополистирол в основное сырье, без потери качества изготавливаемых блоков полистиролбетона.Оснащение: имеет встроенный пневмотранспорт измельченных гранул, особенностью данного измельчителя является низкое энергопотребление при высокой производительности.
ПодробнееПневмотранспорт вспененных гранул пенополистирола, предназначен для транспортировки гранул по всему участку производства, работает по принципу инжектора, не сминает и не повреждает свежие гранулы при перекачке, благодаря конструкции, отсутствуют засоры, что исключает поломку дорогостоящих вентиляторов. Транспортировка при помощи пневмотранспортов, способствует промежуточной подсушке свежевспененных гранул, что экономит электроэнергию а также способствует автоматизации процесса производства, снижая трудозатраты и увеличивая производительность линии.
Используется в качестве основного источника пара при производстве пенопласта. От качества вырабатываемого пара, его насыщенности и температуры, напрямую зависит качество вспениваемых гранул и качество получаемого пенопласта. В том случае если в помещении заказчика нет возможности подключения электрического парогенератора, возможно использование, газовых, твердотопливных или жидкотопливных парогенераторов, мы оказываем помощь в подборе альтернативных источников пара. Парогенератор»ПМТ» разработан и выпускается нашим предприятием более 4-х лет, работает на трубчатых электронагревателях «ТЭН» что делает его эксплуатацию простой и надежной, производит пар отвечающими технологии производства пенопласта, имеет три ступени регулировки мощности, что позволяет снижать нагрузку на сеть, при изменении мощности нагрузка распределяется равномерно по трем фазам, исключая перекосы.
Предназначен — для выработки в автономном режиме, и пара подачи в предвспениватели, может использоваться как стационарно, так и в качестве мобильной установки. Использование отдельного парогенератора для вспенивания гранул, позволяет снизить энергозатраты, в том случае когда требуется только вспенивать гарнулы, не требуется большого количества пара и соответственно запускать основной источник пара и паровой накопитель, что в конечном итоге экономит электроэнергию и снижает нагрузку на сеть. Оснащен собственным блоком управления, работает в автоматизированном режиме.
ПодробнееПаровой накопитель, стабилизирует характеристики пара, позволяет создать запас пара с требуемыми характеристиками, что значительно улучшает качество получаемой продукции, особенно важно при производстве легких марок пенополистирола, М15 и ниже, при помощи накопителя, нашей компанией разработан метод снижения суммарной нагрузки на электрическую сеть, без потери производительности линии. Оснащен; системой накопления перегретой воды, защитным клапаном, манометрами, сливными и подающими вентилями, дополнительно оснащаются системой автоматического контроля давления и уровня перегретой воды.
Используется для охлаждения и удаления влаги из блока пенополистирола после формования.
ПодробнееВакуумная станция предназначена для охлаждения и удаления остатков влаги из блока пенопласта после формования, использование автоматизированной вакуумной станции, позволяет ускорять процесс производства пенопласта, несъемной опалубки. Станция выполнена на базе водно-кольцевого вакуумного насоса «ВВН-1-3», комплектуется накопительным ресивером объемом 1,2 м.куб, накопительной емкостью для воды, автоматической насосной станцией, автоматизированной системой управления. Использование замкнутого цикла подачи, позволяет избежать значительного перерасхода питающей воды, нашим предприятием разработан метод рекуперации израсходованной энергии при помощи вакуумной станции
ПодробнееБункер вывдержки гранул предназначен для накопления и промежуточной стабилизации вспенных гранул пенопласта, для загрузки и выгрузки гарул используют пневмотранспорты. Изготавливаются из негорючей, антистатичной ткани, разборные, на легком стальном каркасе.
Сушилка вспененных гранул используется для промежуточной просушки гранул, перед формованием блоков пенопласта. Просушенные гранулы значительно лучше транспортируются, что повышает производительность пневмотранспортов экономя электроэнергию. Эффективность использования сушилки оправдана в основном в зимний период, когда в помещении устанавливается относительно низкая температура, это заключается в том что, горячие вспененные гранулы из предвспенивателя попадая в холодный поток воздуха, от резкого охлаждения сжимаются, в результате увеличивается их вес. При поступлении в сушилку, гранулы попадают в теплый поток воздуха, высушиваются и уже после попадают в пневмотранспорт не теряя насыпного веса, в летний период использование сушилки можно исключить. Также использование сушилки целесообразно при производстве изделий из мелких фракций сырья, например при производстве несъемной опалубки, или набивке гранулами пенопласта мягкой мебели. Нашей компанией разработана универсальная сушилка циклического и непрерывного типа, позволяющая значительно снизить расход эл.энергии без потери производительности. На сушилке такого типа можно сушить как вспененные гранулы, так и исходное сырье ПСВ, с повышенным показателем по влажности. Такая сушилка успешно эксплуатируется для сушки сырья для производства экструзионнго пенопласта.
Станок предназначен для упаковки пенопласта в полимерную пленку, а также блоков несъемной опалубки, термопанелей в полиэтиленовую пленку, методом оборачивания с последующей запайкой шва и обрезкой.
ПодробнееКак выбрать оборудование для производства пенопласта. Станок для производства пенопласта: цена, фото :: BusinessMan.ru
В роли строительного материала пенопласт получил свою известность в середине прошлого века. Кроме того, его применяют в качестве тары для упаковки хрупких и бьющихся изделий. Такую популярность пенопласт получил благодаря своим свойствам: он является, прежде всего, дышащим материалом. Пенополистирол устойчив к перепадам температур и атмосферным осадкам. Поскольку спрос на этот материал не падает, имея некоторые финансовые средства, можно открыть собственный бизнес.
Краткое описание технологии производства
Прежде чем покупать оборудование для производства пенопласта, необходимо изучить технологию его изготовления и знать, что именно будет выпускаться: листы, тара, элементы фигурной резки. Лучше всего составить бизнес-план, чтобы понимать затраты и сроки окупаемости. Технология состоит из следующих этапов:
- Вспенивание исходного сырья.
- Вылеживание сырья после вспенивания.
- Придание материалу необходимой формы (формовка).
- Порезка материала согласно плану производства.
На каждом этапе требуется свое оборудование для производства пенопласта. Качество полученного продукта будет зависеть от него и от применяемого сырья. Какие гранулы для производства пенопласта будут использованы, обуславливается планом изготовления и экономическим обоснованием.
Автоматизированные линии
В зависимости от того, какие объемы продукции планируется выпускать, рассчитывается необходимое количество оборудования. Можно купить каждый станок для производства пенопласта отдельно, а можно приобрести готовую линию. Такие варианты используются при условии, что вся продукция однотипная, не требует перенастройки оборудования и выпускается в определенных объемах.
Возникает естественный вопрос: «Как выбрать хорошую автоматизированную линию?» Для этого нужно провести маркетинговые исследования и выяснить, какова потребность в пенопласте в регионе, где он будет выпускаться. И уже в соответствии с этим выбирать необходимые варианты. В автоматизированную линию входит следующее:
1) предвспениватель непрерывного вспенивания;
2) бункер вторичного вспенивания:
3) бункер для вылеживания;
4) формовочный станок;
5) дробилка:
6) парогенератор;
7) паровой или твердотопливный котел.
Стоимость такой линии выпуска пенопласта составляет порядка 30000 долларов. Она способна выпускать в смену 100 кубометров пенопласта. В качестве дополнительного оборудования потребуется стол или станок для порезки.
Самостоятельно собранная линия из оборудования
Если в перспективе намечается производство различного типа продукции, тогда имеет смысл купить оборудование для производства пенопласта по отдельности. В этом случае можно подобрать оптимальный вариант по мощности, качеству и производительности.
Например, в зависимости от того, что за изделия будут изготавливаться, можно купить стол холодной резки массива на листы, а можно приобрести станок с ЧПУ для фигурной резки. Такой станок является универсальным, резка осуществляется горячим способом, переналадка на различные варианты порезки занимает не более 30 минут.
Как выбирать оборудование для линии по производству пенопласта
Для того чтобы пенополистирол получился качественным, нужно хорошее оборудование и сырье для производства пенопласта. Основными параметрами при выборе станков или столов должны быть следующие:
1. Габаритные размеры. Исходить нужно из того, где будет размещаться оборудование для производства пенопласта, и из общей площади помещения. Поскольку есть определенные нормативы того, как оно должно быть размещено, нужно соблюдать минимальное расстояние между станками, технику безопасности и т. д.
2. Производительность оборудования. Как правило, любой станок для производства пенопласта имеет максимальную производительность. Какая производительность должна быть, определяется маркетинговыми исследованиями регионального рынка. Нет смысла брать оборудование, которое будет выпускать свыше этих потребностей.
3. Стоимость оборудования. Необходимо выбирать качественное оборудование, которое будет соответствовать финансовым возможностям. В крайнем случае можно взять кредит на недостающую сумму, но лучше обойтись без него.
4. Качество. Необязательно самый дорогой станок для производства пенопласта — самый качественный. Кроме того, что имеет смысл ознакомиться с отзывами о них, нужно еще и внимательно изучить проблемы которые чаще всего возникают в ходе эксплуатации.
Сырье
Гранулы для производства пенопласта выпускаются различными производителями. На сегодняшний день сырье, которое производится на отечественном рынке, по качеству уступает импортному. Однако различное оборудование для производства пенопласта также производит различный по качеству пенополистирол из одного и того же сырья.
А ведь пенопласт, даже листовой, не говоря уже о других изделиях, требует различной плотности, и, соответственно, различной степени раскрываемости стирольного сырья. Поэтому перед покупкой необходимо уточнить, из гранул чьего производства будет получаться наиболее качественная продукция.
Покупка с перспективой на будущее
Для организации производства листового пенопласта дополнительного оборудования не требуется. Однако если планируется выпуск и других изделий, то вместо стола холодной порезки имеет смысл приобрести станок с ЧПУ объемной резки.
На нем есть возможность холодной и горячей резки, а также создания моделей практически любой формы. С таким оборудованием можно существенно расширить ассортимент предлагаемой продукции и стать серьезным конкурентом в своем регионе.
Трудно рекомендовать определенные марки оборудования для производства изделий из пенополистирола – все сугубо индивидуально. Как правило, в значительной степени все зависит от финансовых возможностей и предполагаемых объемов выпуска. Однако есть определенные правила при выборе оборудования, они перечислены выше.
КАТАЛОГИВсе каталоги » Каталог оборудования компании |
Пенополистирол отвечает самым строгим требованиям пищевой промышленности с точки зрения безопасности материала для здоровья человека.
Ящик, закрытый крышкой, выполняет функцию термоконтейнера и стабилизирует температуру внутри упаковки, позволяя устранить влияние колебаний температуры внешней среды на ее содержимое.
Ящики из пенополистирола являются оптимальным решением любых проблем, связанных с транспортировкой и хранением свежей охлажденной рыбы или мяса, овощей, фруктов, мороженного, так как пенополистирол сочетает в себе уникальные качества:
Комплектация линии для производства термотары
Для работы оборудования необходим источник пара – промышленный пар или парогенератор, производительность не менее 250 кг/час, давление 5-6 атм. Термотара – типовые размеры * чертежи крышки (толщина 20 мм) не показаны Этап 1 – вспенивание сырьяРисунок 1
Технические характеристики (форма для ящика)
Cтепень механизации и автоматизации форм для ящика:
Cтепень механизации и автоматизации формы для крышки:
Этап 4 – охлаждение термопанелиУстановка вакуумированияCлужит для создания разряжения давления в форме, отвода конденсата, облегчения разъема формы, является необходимым элементом для получения качественного изделия.
Технические характеристики
Парогенератор необходим для выработки теплоносителя роста и сцепления гранул стирола Котел паровой электрический модели КЭП-160 Котлы электродные паровые модели 1КЭП-160/0,4 предназначены для получения насыщенного водяного пара. Пар от котла поступает в паронакопитель, откуда происходит его отбор для прохождения процесса предварительного вспенивания сырья либо для окончательного формования изделий.
Технические характеристики
Данный парогенератор в составе линии работает на 50% мощности, т.к. имеет излишнюю производительность.
Накопитель пара
Паронакопитель служит для накопления водяного насыщенного пара, генерируемого паровым котлом. Пар, попадая в ресивер под избыточным давлением, частично переходит в жидкое состояние (перегретая вода). Необходимый объем паронакопителя варьируется от выбранной модификации блок-формы
Требования к производственному помещению для размещения в нем линии по производству термотары1) Высота потолка не менее 4,0 метров.
2) Площадь производственного помещения должна быть не менее 70 м2 для установки оборудования (без учета площадей под склад готовой продукции).
3) Подводка сетей электрификации (наружных сетей и внутренней разводки)
По этим данным ведется расчет сечения кабеля для подвода электричества.
4) Потребляемый объем воды с учетом затрат на производство пара составляет 0,2…0,3 м3/час
5) Канализация
6) Обслуживающий персонал 2 человека.
все оборудование |
Что такое пенополистирол? (с иллюстрациями)
Пенополистирол — это пенополистирол, обладающий определенными желательными свойствами благодаря своей структуре. Он необычайно легкий и плавучий, а также хороший изолятор от тепла и звука. Его можно использовать в качестве строительного материала или элемента дизайна, а также можно придать ему множество форм для различных домашних нужд.
Пенополистирол — хороший теплоизолятор.В большинстве случаев пенополистирол белого цвета и состоит из небольших соединенных между собой шариков. Он сделан путем объединения химических веществ этилена и бензола, чтобы получить соединение, известное как стирол. Затем стирол обрабатывают другими химическими веществами, которые вызывают полимеризацию молекул стирола или их группировку в длинные цепи. Эта реакция может продолжаться только до определенного момента, а затем прекращается. Получившимся шарикам дают остыть, а затем их очищают.
Пенополистирол технически пригоден для вторичной переработки.После формирования и очистки бусинки должны быть расширены, что происходит в три основных этапа.Сначала шарики нагревают горячим воздухом или паром до тех пор, пока их плотность не станет трех процентов от первоначальной. Затем шарики охлаждают в течение 24 часов и формуют. Попав внутрь формы, они впрыскиваются паром низкого давления, который еще больше расширяет шарики и сплавляет их. Когда форма остынет, пенополистирол готов к использованию или отгрузке.
Пенополистирол существенно отличается от аналогичного продукта, называемого экструдированным полистиролом.Экструдированный полистирол производится с использованием хлорфторуглеродов (ХФУ), которые, по мнению многих, вредны для баланса озона в атмосфере Земли. Пенополистирол изготавливается без этих соединений, что делает его более безвредным для окружающей среды. Однако оба продукта могут быть переработаны, как и любой пластик.
Еще одно важное преимущество пенополистирола, особенно для таких продуктов, как одноразовые стаканчики, состоит в том, что он очень экономичен.Производство пенополистирола требует гораздо меньше энергии, чем производство альтернатив на бумажной основе. Кроме того, он может производить гораздо меньше отходов, чем бумага. Например, при правильном сжигании из одной тонны (907 кг) полистирольных стаканов образуется только 0,2 унции (5,66 г) золы, тогда как из того же количества бумаги образуется 200 фунтов (90,7 кг) золы.
Также следует отметить, что пенополистирол не подвергается биологическому разложению.Некоторые считают это недостатком, но тот факт, что он химически инертен, делает его стабильным наполнителем, который помогает обеспечить безопасную и гигиеничную рекультивацию полигона. Несмотря на это, преобладающей тенденцией было сокращение объема пенополистирола и его переработка везде, где это возможно.
Производство ЛИТЬЕ МЕТАЛЛА ПРОЦЕССЫ Принципы литья металлов Литье металла Операция по литью металла Влияние газов на металлическую отливку Дизайн литья металла Расходные формы для литья под давлением Литье в песчаные формы Литье гипсовых форм Керамическое литье Литье в пресс-форму Вакуумное литье или V-образный процесс Литье по выплавляемым моделям Постоянное литье формы Основное литье постоянной формы Слякоть литья Литье под давлением Литье в постоянную вакуумную форму Литье под давлением Горячее литье под давлением Холодное литье под давлением Истинное центробежное литье Полукентробежное литье Центрифужное литье Литье слитков Непрерывное литье ПРОИЗВОДСТВО ПРОЦЕССЫ Обработки металлов давлением Металлопрокат Металлическая ковка Металл Экструзия Рисунок Металла Листовой металл Порошковые процессы | В процессе литья пенополистирола песчаная форма упакован вокруг узора из полистирола, представляющего металлическую отливку, изготовлено.Узор не снимается, а расплавленный металл заливается в узор, который испаряется от тепла металла. Жидкий металл забирает место испаренного полистирола и отливка затвердевает в песчаной форме. В индустрии литья металлов этот процесс известен как процесс по выпадению пены, литье по схеме испарения или процесс полной формы. Большой с его помощью можно изготавливать различные отливки из различных материалов и размеров. техника. Детали, произведенные в обрабатывающей промышленности с использованием этого процесса, включают: коленчатые валы, головки цилиндров, основания машин, коллекторы и блоки двигателей. ПроцессПервым этапом процесса литья под давлением является производство полистирола. шаблон. Для небольших производственных партий выкройку можно вырезать из больших частей материал пенополистирол и собран вместе. Для крупного промышленного производства процессов, выкройка будет лепиться. Матрица, часто сделанная из алюминия, используется для этот процесс. Шарики полистирола помещаются в фильеру и нагреваются, они расширяются от тепло и вспененный материал принимает форму матрицы.В зависимости от сложности отливки некоторые из этих полистирольных секции, возможно, придется склеить вместе, чтобы сформировать узор. В большинстве случаев узор покрыт огнеупорным составом, это поможет создать хорошую поверхность отделка на металлическом литье. Помимо самой отливки, рисунок из пенопласта также будет Включите наливную чашку и литниковую систему.
Затем выкройку помещают в колбу и насыпают вокруг нее формовочный песок.В песок может содержать или не содержать связующие вещества, в зависимости от конкретного процедура изготовления.
Затем расплавленный металл заливают в форму, не удаляя узор. В жидкий металл испаряет рисунок из полистирола, когда он течет через полость формы. Любые остатки испаренного полистирола впитываются в формовочный песок.
Затем расплавленному металлу дают затвердеть в песчаной форме.После затвердевания отливка снимается.
Свойства и особенности производства Отливкой из пенополистирола
TOP | ПОЛИТИКА КОНФИДЕНЦИАЛЬНОСТИ |
Что такое пенополистирол? — STYRO
По сути, это то, что вы часто видите и используете в повседневной жизни — например, чашки из пенополистирола, упаковка, изоляция и многое другое.Фактически он состоит из 98% воздуха и 2% полистирола. Его пропаривают таким образом, что он становится пеной в особой форме. Что хорошего в EPS, так это то, что его можно полностью повторно использовать и перерабатывать, а значит, он экологичен.
STYRO Пенополистирол «EPS» — это жесткий пенополистирол, полученный из нефти. после воздействия пара он расширяется в 40 раз по сравнению с первоначальным размером, что делает его чрезвычайно универсальным продуктом.
Каковы общие характеристики EPS?
- Огнестойкий
- 100% перерабатываемый
- Легкий
- Стабильный
- Долговечный
- Плавучесть
- Простота в обращении
- Прочный и гибкий
- Амортизатор
- Демпфер вибрации
- Устойчив к влаге
- Стоимость- эффективный
- Высокая теплоизоляция
Каковы преимущества использования пенополистирола?
EPS — прекрасная альтернатива, если вы хотите использовать дерево, войлок, резину или стекловолокно.Вы можете заменить сырье пенополистиролом и не беспокоиться о том, что качество упадет, потому что оно станет еще лучше.
EPS можно формовать и придавать любую форму, которая вам нравится. Используя другое оборудование, вы сможете вырезать и придавать форму пенопласту и материализовать свои визуальные эффекты.
Это идеальный продукт для упаковки, поскольку он может противостоять ударам, а также воде или другим внешним элементам.
Это, несомненно, рентабельно — производители пенополистирола, такие как STYRO, могут эффективно доставлять и производить вашу продукцию из пенополистирола, тем самым экономя ваше время и деньги.
Чтобы узнать, как EPS может быть полезен для ваших проектов и бизнеса, свяжитесь с нами в STYRO, и мы доставим вам все это. Благодаря нашим накопленным знаниям и многолетнему опыту мы уже заняли позицию на рынке, которая многое говорит о нашем отличительном преимуществе по сравнению с другими производителями пенополистирола. Мы уже работали с известными брендами по всему ОАЭ и стремимся и дальше оставаться лидером в производстве пенополистирола.
Все, что вы хотели знать об удивительных свойствах полистирола
Что такое полистирол? Каковы его свойства и для чего он используется? Давайте выясним!
Полистирол получают путем полимеризации мономера стирола, который является производным нефти.Если вы посмотрите на химическую структуру полистирола, вы увидите, что он состоит только из атомов углерода и водорода. Таким образом, он классифицируется как углеводород. Теперь, если вы понаблюдаете за связями в его химической структуре, вы увидите, что атомы углерода связаны друг с другом ковалентными связями. Каждый альтернативный атом углерода в цепи полистирола имеет присоединенную к нему фенильную группу (название, данное бензольному кольцу). Это длинноцепочечный углеводород с химической формулой C 8 H 8 ) n .Ниже приводится химическая структура полистирола.
Хотите написать для нас? Что ж, мы ищем хороших писателей, которые хотят распространять информацию. Свяжитесь с нами, и мы поговорим …
Давайте работать вместе!
Стирол — ароматический мономер, производимый в промышленных масштабах из нефти. Полистирол — это виниловый полимер, производимый из мономера стирола путем свободнорадикальной виниловой полимеризации.
Свойства полистирола
Теперь, когда мы познакомились со структурой полистирола, давайте углубимся в его свойства. Здесь мы узнаем о физических, механических, оптических, тепловых, электрических и химических свойствах полистирола.
Физические свойства
- Плотность полистирола может варьироваться от 10 кг / м 3 до 50 кг / м 3 .
- Ненаполненный полистирол аморфен и имеет блестящий стеклянный вид.Он также известен как кристаллический полистирол.
- Важным свойством экструдированного полистирола является его плавучесть или способность плавать в воде. Это делает его идеальным выбором для изготовления плавающих досок. Если вы когда-нибудь были в бассейне и замечали красочные доски, вы поймете, о чем мы говорим!
- Вязкость полистирола, как и всех других неньютоновских жидкостей, зависит от скорости сдвига. Это отношение напряжения сдвига к скорости сдвига.
Вот значения физических свойств полистирола общего назначения (GPPS).
Физические свойства | ||
Имущество | Установка | Значение |
Удельный вес | г / см 3 | от 1,03 до 1,06 |
Кажущаяся плотность | г / см 3 | от 0,60 до 0,65 |
Водопоглощение | % | от 0,03 до 0,10 |
Физические свойства полистирола обусловлены наличием слабых сил Ван-дер-Ваальса между цепями полимера.При нагревании силы еще больше ослабевают, и цепи скользят одна по другой. Это причина того, что полистирол очень эластичен и размягчается при нагревании выше температуры стеклования.
Механические свойства
Механические свойства полимера включают его прочность, удлинение, модуль, ударную вязкость и ударную вязкость. Кристаллические формы полимерного полистирола обладают низкой ударной вязкостью. Полистирольные полимеры разрушаются под воздействием солнечного света из-за фотоокисления, которое влияет на его механические свойства.В следующей таблице приведены значения механических свойств полистирола общего назначения (GPPS).
Механические свойства | ||
Имущество | Установка | Значение |
Модуль упругости при растяжении или модуль Юнга | МПа | 3000-3600 |
Прочность на разрыв | МПа | 30-60 |
Относительное удлинение при растяжении | % | 1.От 0 до 5,0 |
Модуль сдвига | МПа | 1400 |
Прочность на изгиб | МПа | 76 |
Модуль упругости при изгибе | МПа | 3200 |
Оптические свойства
GPPS является прозрачным, в то время как ударопрочный полистирол (HIPS), который представляет собой сополимер, образованный добавлением каучука к полистиролу во время полимеризации, непрозрачен. Однако HIPS имеет блеск, который измеряется процентным содержанием света, отраженного поверхностью полимера.Ниже приведены значения оптических свойств GPPS.
Хотите написать для нас? Что ж, мы ищем хороших писателей, которые хотят распространять информацию. Свяжитесь с нами, и мы поговорим …
Давайте работать вместе!
Оптические свойства | ||
Имущество | Установка | Значение |
Показатель преломления | – | 1.58 к 1,59 |
Коэффициент пропускания | % | от 88 до 90 |
дымка | % | от 0,10 до 1,1 |
Тепловые свойства
Термические свойства — это свойства, проявляемые веществом при нагревании. К ним относятся температура теплового искажения, температура стеклования, теплопроводность и т. Д. Полистирол — это жесткий прозрачный термопласт, который находится в твердом или стекловидном состоянии при нормальной температуре.Но при нагревании выше температуры стеклования он превращается в жидкую форму, которая течет и может быть легко использована для формования и экструзии. Когда остывает, он снова становится твердым. Это свойство полистирола используется для отливки его в формы с мелкими деталями. Ниже приведены значения тепловых свойств для GPPS.
Тепловые свойства | ||
Имущество | Установка | Значение |
Температура стеклования | ° С | 100 |
Удельная теплоемкость | Дж / кг-К | 1250 |
Теплопроводность | Вт / м-К | 0.14 |
Тепловое расширение (от 20 ° C до 100 ° C) | мкм / м-K | 120 |
Температура размягчения по Вика | ° С | 100 |
Электрические свойства
Электрические свойства — это свойства вещества, определяющие его реакцию на электрическое поле. Ниже приведены значения этих свойств для GPPS.
Электрические свойства | ||
Имущество | Установка | Значение |
Диэлектрическая прочность | МВ / м | 20 |
Диэлектрическая проницаемость (при 1 МГц) | – | 2.5 |
Объемное сопротивление | Ом-см | > 10 16 |
Сопротивление дуги | сек | 70 |
Химические свойства
- Полистирол химически инертен и не вступает в реакцию с большинством веществ.
- Растворяется в некоторых органических растворителях. Он растворим в растворителях, содержащих ацетон, таких как большинство аэрозольных красок и цианоакрилатные клеи.
- Превращение двойных углерод-углеродных связей в менее реактивные одинарные связи в полистироле является основной причиной его химической стабильности.Большинство химических свойств полистирола являются результатом уникальных свойств углерода.
- Он легко воспламеняется и горит оранжево-желтым пламенем с выделением частиц углерода или сажи, что характерно для всех ароматических углеводородов. Полистирол при полном окислении выделяет только диоксид углерода и водяной пар.
Полистирол прочие формы
Полистирол без наполнителя также известен как кристаллический полистирол (PS) или полистирол общего назначения (GPPS).Однако, поскольку кристаллический полистирол является хрупким, к полистиролу добавляют другие полимеры для повышения его прочности, и в результате образуются сополимеры. Одним из таких сополимеров является ударопрочный полистирол (HIPS), который получают путем добавления полибутадиенового каучука к полистиролу в процессе полимеризации. HIPS прочнее и имеет большую ударную вязкость, чем полистирол без наполнителя.
Есть разные виды полистирола. Экструдированный полистирол (XPS) — это одна из форм полимера, обладающая высокой прочностью на разрыв и хорошей эластичностью.Обычно он известен как пенополистирол ™. Другой распространенной формой полистирола является пенополистирол (EPS). И EPS, и XPS сделаны из одинаковых материалов, но между ними есть разница. XPS имеет более высокую плотность по сравнению с EPS из-за отсутствия воздушных каналов между его ячейками. Более высокая плотность делает XPS более жестким и прочным. Кроме того, XPS является водонепроницаемым и эффективным теплоизолятором.
использует
Полистирол впервые был произведен в Германии в 1930 году И.Г. Фарбен. С тех пор он прошел долгий путь, и сегодня это один из наиболее широко производимых полимеров в мире, уступающий только полиэтилену. Основная причина этого заключается в том, что это термопласт. Преимущество термопластов заключается в том, что из них можно формовать множество полезных продуктов. Кроме того, будучи прозрачным и прозрачным, он позволяет добавлять различные цвета. Эти краски добавляются к пластику в жидком состоянии. Одно из основных применений полистирола — производство пенополистирола для упаковки предметов для транспортировки.Он также используется для изготовления одноразовых столовых приборов, тарелок, чашек и т. Д. Из этого полимера также производится медицинское и фармацевтическое оборудование.
На рынке вы найдете полистирол в виде гранул и листов. Экструдированный полистирол обладает изоляционными свойствами и используется в производстве обычных предметов домашнего обихода и игрушек. Полистирол не является токсичным продуктом и одобрен FDA для использования в производстве пищевых контейнеров. Однако, как и все другие пластмассы, он не поддается биологическому разложению.Однако его можно легко переработать.
На рынке вы найдете полистирол в виде гранул и листов. Экструдированный полистирол обладает изоляционными свойствами и используется в производстве обычных предметов домашнего обихода и игрушек. Полистирол не является токсичным продуктом и одобрен FDA для использования в производстве пищевых контейнеров. Однако, как и все другие пластмассы, он не поддается биологическому разложению. Однако его можно легко переработать.
Домашняя страница производства полистирола
Домашняя страница производства полистиролаВоздействие на окружающую среду
Национальное бюро стандартов Центра пожарных исследований выявило 57 побочных химических продуктов, выделяющихся при сгорании пенополистирола. Процесс производства полистирола загрязняет воздух и приводит к образованию большого количества жидких и твердых отходов.Компания McDonald’s добровольно прекратила использование ХФУ (которые разрушают озоновый слой) в качестве вспенивающих агентов (химических веществ, используемых для создания крошечных отверстий в пластике, что делает его пластичным) в версии пены с шариками в 1988 году.Они заменили ХФУ с бензолом и этиленом Горючие и токсичные, эти два убийцы представляют собой продукты нефти и природного газа, которые используются для производства стирола, основного материала для пенополистирола [1]. Агентство по охране окружающей среды определило этилен и бензол, химические предшественники полистирола, как 4-е и 6-е места в производственных процессах по количеству отходов соответственно [2]. Бензол — известный канцероген, и оба легко воспламеняются.
1. «Информационный бюллетень по полистиролу», Фонд достижений в науке и Образование, Лос-Анджелес, Калифорния.
2. Брайан Липсетт, «Области экспертизы, относящиеся к McDonalds Corp.»
Безопасность работников
Стирол (винилбензол) — сырье, используемое для производства полистирол. Нейротоксин, стирол нарушает центральную и периферическую нервную систему. Воздействие стирола на рабочем месте также связано с хромосомными аберрации, поэтому считается мутагеном. В исследовании 12 образцов грудного молока от New 75% Джерси, Пенсильвании и Луизианы были загрязнены стиролом среди других опасные химические вещества.
Недавние исследования распределения стирола в тканях человека поразительные результаты. Длительное воздействие (от 3,2 до 10 лет) небольшого количества стирола (1 до 10 частей на миллион, тогда как человек, производящий полистирол, может получать от 50 до 100 частей на миллион более 8 часов. период) вызывают широкий спектр неблагоприятных последствий для здоровья, включая нейротоксический, гематологический (низкие значения тромбоцитов и гемоглобина), цитогенетический (хромосомный и цитогенные аномалии) и канцерогенные эффекты. Нейротоксические эффекты включают: утомляемость, нервозность, проблемы со сном, плохая память и реакция на раздражители тесты и нарушения скорости нервной проводимости.Другие эффекты включают низкий уровень тромбоцитов и уровни гемоглобина, хромосомные и лимфатические аномалии на уровне ниже 50 ppm. [1]
Нейротоксическое повреждение так же серьезно, если не более серьезно, чем канцерогенное воздействие. Химикаты известно, что, как и стирол, без разбора поражают ткани и нервную систему. С участием появляется все больше свидетельств того, что такие заболевания, как болезнь Паркинсона, связаны с созданными человеком токсинами [2], общественность должна предпринять все необходимые шаги для уменьшения воздействие нейротоксинов. Болезнь Паркинсона не часто убивает людей, но это дегенеративное заболевание мозга лишит человека интеллекта и затруднит речь, ходьба, умение выполнять несложные задания.Следовательно, было бы разумно избегайте использования продуктов из полистирола при употреблении еды и напитков. [1]
Примеры из практики
Известно, что женщины, подвергающиеся воздействию паров стирола низкой концентрации на рабочем месте, имеют разнообразные нейротоксические и менструальные проблемы. Российское исследование 110 женщин, подвергшихся пары стирола на уровне около 5 мг / м3 демонстрируют нарушения менструального цикла, в частности нарушения менструального цикла и гиперменорея (необычно обильное выделение менструации во время менструального цикла) синдром.Женщины, подвергавшиеся воздействию стирола, часто страдали от метаболические нарушения, возникающие во время беременности. [3]Мужчина 45 лет, подвергшийся воздействию паров мономера стирола в течение пяти лет. появилось ощущение жжения в нижней части стопы и ощущение ходьбы по надутые воздушные шары из хлопка. При осмотре были обнаружены признаки полной демиелинизации, (разрушение, удаление или потеря миелиновой оболочки нервов). Поэтому серьезные произошло физическое разрушение нервной системы, в результате чего нервы остались незащищенными. охрана.Авторы исследования пришли к выводу, что «стирол влияет на нервную систему. в большей степени, чем считалось ранее »[4]
Другое исследование нейротоксичности толуола и стирола отмечает, что эти «ароматические углеводороды имеют неожиданные длительные невологические эффекты. Накопление эти хорошо растворимые в липидах материалы в богатых липидами тканях головного и спинного мозга, и периферические нервы, по-видимому, коррелировали с острым или хроническим функциональным нарушением нервной системы.[5]
1. Джордж Баггетт, «Миграция стирола в жировую ткань человека».
2. Эрик Адлер, «Обращение к причинам, вызывающим болезнь Паркинсона», Канзас City Star, , 17 июня 1990 г., Раздел I, страницы 5-6.
3. Н.С. Злобина, А. Изюмова, Н.Ю. Рагулье, «Эффекты слабого» Концентрации стирола на специфических функциях женского организма »(человека и белая крыса), Гигиена труда и профессиональные саболенавия, Москва, СССР, Декабрь 1975 г., № 12, стр. 21-25.
4. М. Бехари, К. Чоудхари, С. Рой, М.С. Махешвари, «Стирол Индуцированная периферическая невропатия, European Neurology, Vol. 25, No. 6, ноябрь 1986, страницы 424-427.
5. J.L. O’Donoghue, Нейротоксичность промышленного и коммерческого Химические вещества: об. 2, CRC Press, Inc., Бока-Ратон, Флорида, 1985, стр. 127– 137.
Вернуться на главную страницу полистирола
Последнее изменение: 4 марта 1996 г.
http: //www.ejnet.org / issues / plastics / polystyrene / production.html