Самостоятельный кузовной ремонт
Выполнить кузовной ремонт самостоятельно в условиях гаража непросто, поскольку данная процедура включает несколько этапов, каждый из которых требует специализированного инструмента и знания новых технологий кузовного ремонта. Однако задача эта не является невыполнимой. Данный раздел содержит множество рекомендаций по выполнению различных видов кузовных работ с фото основных этапов. Для начинающих или малоопытных автолюбителей могут оказаться полезными видео уроки кузовного ремонта авто. Узнав о приемах и современных технологиях кузовного ремонта автомобиля в гаражных условиях, вы сможете не только правильно подобрать кузовную деталь, но и установить ее на авто, устранить очаг коррозии, сделать рихтовку двери, крыла или капота своими руками, удалить небольшую вмятину на машине, правильно установить пороги и даже выполнить сварочные кузовные работы своими руками.
Виды кузовного ремонта
Самостоятельные кузовные работы в зависимости от дефектов можно разделить на несколько видов: Сложный ремонт кузова автомобиля своими руками включает такие этапы, как правка кузова, рихтовка средних и больших вмятин, замена элементов кузова, сварка кузова полуавтоматом, восстановление геометрии автомобиля.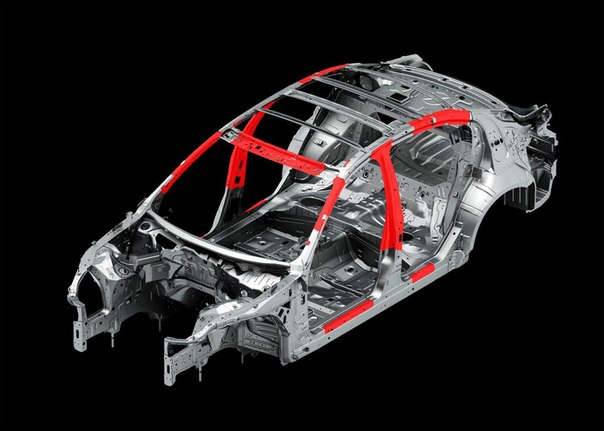
Диагностика кузова самостоятельно
Перед тем, как самому сделать кузовной ремонт, необходимо провести качественную диагностику кузова и выявить все проблемные участки. Особенно это актуально перед покупкой автомобиля, поскольку ремонт кузова любого авто, будь то Волга или ВАЗ 2109, даже своими руками может вылиться в немалую копеечку. Как же проверить геометрию кузова авто и выявить дефекты? Для этого производится скрупулезный осмотр авто.- Осмотр лакокрасочного покрытия. Необходимо внимательно просмотреть, нет ли цветовой неоднородности, переходов одного цвета в другой. Причем изучать нужно не только внешние элементы кузова, но и внутренние, такие, как пол салона или багажника, центральные стойки.
Перекрашенные стойки говорят о том, что, скорее всего автомобиль побывал в серьезной аварии и нарушена геометрия кузова. Также необходимо выявить места сколов и царапин ЛКП.
- Проверка зазоров. Симметричные зазоры между элементами кузова должны быть одинаковыми с каждой стороны. В противном случае велика вероятность того, что авто побывало в серьезном ДТП.
- Лонжероны. В передней и задней части авто лонжероны не должны иметь следов перекраски, геометрических неровностей, следов сварки, иначе можно сделать вывод о нарушении геометрии.
- Двери салона и крышка багажника. Каждая дверь должна закрываться с одинаковым усилием, герметичный уплотнитель должен ровно лежать по краям.
- Сварные швы. Они должны быть небольшими и ровными. На кузовных элементах чаще всего применяется точечная сварка. Неаккуратная сварка говорит о том, что части кузова подвергались серьезному ремонту или замене.
- Крепеж. Болты, которыми соединяются элементы кузова, не должны иметь следов от гаечных ключей, иначе можно говорить о том, что кузов подвергался ремонту со снятием или заменой элементов.
Мелкий кузовной ремонт своими руками
В процессе эксплуатации авто постоянно подвергается воздействию окружающей среды. Дождь, град, солнечное излучение, снег, ветер, камушки – все это негативно влияет на качество лакокрасочного покрытия. В результате на кузове образовываются дефекты. Если их вовремя не устранить, они могут стать очагами коррозии. Именно в этом случае понадобится мелкий ремонт кузова автомобиля. Мелкий самостоятельный ремонт кузова легкового автомобиля целесообразен, если гарантийный срок обслуживая авто исчерпан. Он не потребует дорогостоящих инструментов или оборудования, достаточно набора, который есть в каждом гараже: угловая шлифмашинка, шпатель, губки. Локальный кузовной ремонт автомобиля направлен на удаление царапин, сколов, очагов коррозии, ремонт небольших вмятин без покраски. В Сети существует множество видео, демонстрирующих эти процессы достаточно наглядно. Технологии мелкого кузовного ремонта Мерседес, Ниссан, Газель или Нива несильно отличаются.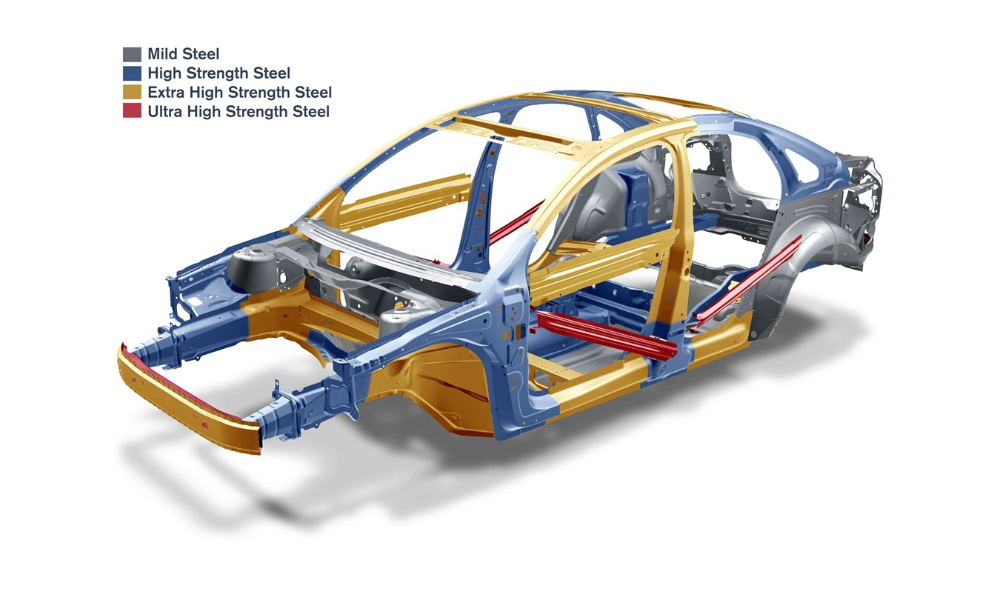
Чаще всего локальный кузовной ремонт сводится к ремонту сколов или царапин. Удаляются они шпатлеванием. Специализированных навыков для этого процесса не требуется. Сначала дефектное место автомобиля необходимо тщательно вымыть с мылом либо автошампунем. Затем царапина или скол обезжиривается Уайт-Спиритом, можно также использовать для этого бензин.
Затем можно наносить шпатлевку, для чего нужно использовать мягкий шпатель. Также можно нанести ее пальцем. Использовать необходимо специальную шпатлевку, предназначенную для кузовных работ. Посмотрите ниже видео, как правильно выполняется процесс шпатлевания.
Послы высыхания зашпаклеванное место повреждения нужно зашкурить мелкозернистой наждачной бумагой, удалить остатки пыли, загрунтовать и проводить локальную покраску.
Сложный кузовной ремонт своими руками
Причина, при которой возникает необходимость полного кузовного ремонта, чаще всего одна – это серьезное ДТП. При этом могут наблюдаться следующие дефекты:- серьезные повреждения кузова;
- изменение геометрии кузова;
- деформация подрамника.
Сейчас народные умельцы даже выкладывают видео, как сделать восстановление геометрии кузова своими руками с помощью самодельного стапеля.
Этапы самостоятельного кузовного ремонта
Сложный ремонт кузова выполняется в несколько этапов.- Арматурные работы. Перед любым сложным ремонтом необходимо демонтировать мешающие элементы кузова. Если нужно выпрямить вмятину на двери, то придется снять обшивку, элементы управления стеклоподъемником, замок и т.д. А перед тем, как восстановить геометрию кузова, необходимо будет полностью освободить салон. Данная работа хоть и кажется простой, на самом деле очень ответственна, ведь в последствии придется все возвращать на место. Поэтому нужно максимум аккуратности, чтобы снять кузов с УАЗа или Газели. По времени арматурные работы могут занять от пары часов до нескольких дней.
- Жестяные работы. На этом этапе проводится исправление вмятин беспокрасочным способом или с помощью рихтовки, устранение следов коррозии кузова, заделка дыр заплаткой, удаление прочих дефектов. Если элемент кузова неремонтопригоден, его придется поменять. Помните, перед тем как заменить кузов автомобиля, необходимо подобрать качественные аналог, желательно, произведенный на заводе изготовителе, чтобы не было проблем с подгонкой.
- Подготовка к покраске. Кузов очищается от следов старой краски, неровности поверхности заделываются шпатлевкой, далее поверхность шлифуется и наносится грунт.
- Покраска авто. Это заключительный этап любого кузовного ремонта. Своими руками делается только в хорошо освещенных помещениях, чтобы были видны все дефекты. Для работы нужен будет краскопульт. Если проводится не полная перекраска кузова, а локальная окраска крыла или капота, остальные части кузова придется плотно закрыть пленкой.
Ремонт коррозии кузова своими руками
Кузова современных автомобилей в своем большинстве делают из оцинкованного металла, что не дает развиваться коррозии, хотя при глубоких сколах слой цинка тоже может быть поврежден.
Итак, если кузов полностью поражен ржавчиной или она выступает во многих местах, первым делом автомобиль необходимо хорошо вымыть с помощью автошампуня.
После подсыхания авто все проблемные места необходимо обработать крупнозернистой шкуркой или использоваться для этого щетку с металлической щетиной. Угловую шлифмашинку использовать не рекомендуется, поскольку зачистные диски снимают грубый слой металла. Для такой процедуры подходят исключительно диски на пластиковой подошве. Также можно на дрель посадить представленный на фото абразивный круг. Также для ремонта ржавого кузова автомобиля можно использовать преобразователь ржавчины.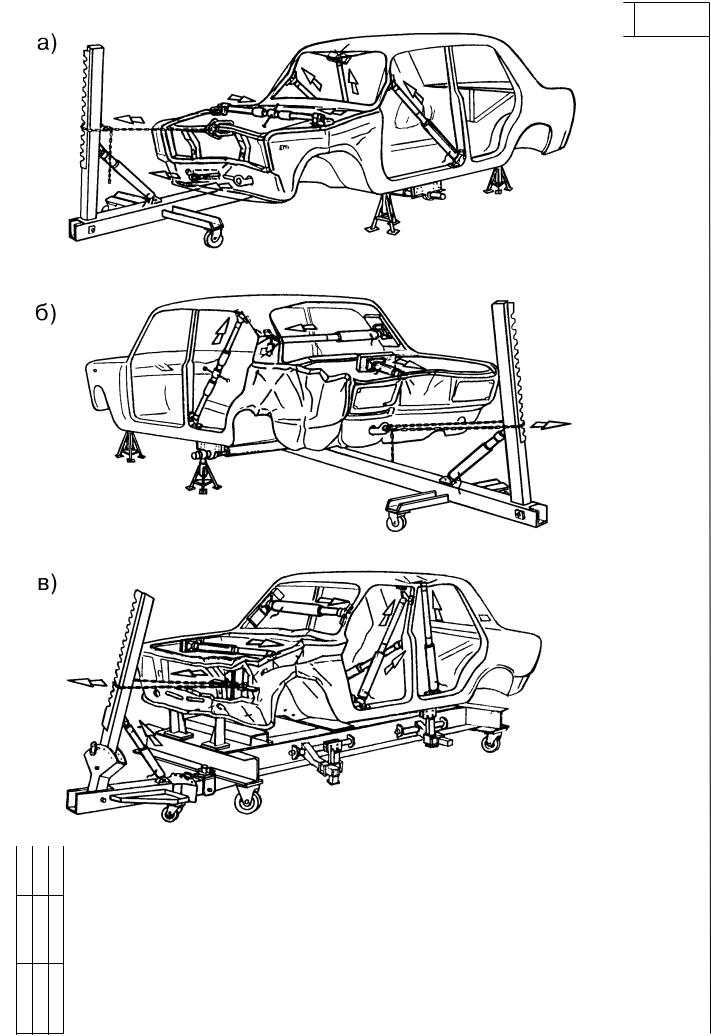
Установка заплаток на кузов своими руками
Если в элементе кузова образовала дыра, шпатлевкой не обойтись. Наиболее простой способ такого кузовного ремонта своими силами – это установка заплатки. Естественно, такой способ подходит для дыр диаметром не более 5-7 см, если дыра больше – скорее всего, понадобится полная замена элемента кузова.Как же отремонтировать дырявый кузов автомобиля? Первым делом место повреждения на кузове надо хорошенько вымыть и очистить от ржавчины. Далее необходимо вырезать заплатку немного большего диаметра, чем дыра, из тонкого металла, например из консервной банки.
Затем с помощью мощного паяльника нужно залудить оловом поверхность с наружной стороны дырки и края заплатки.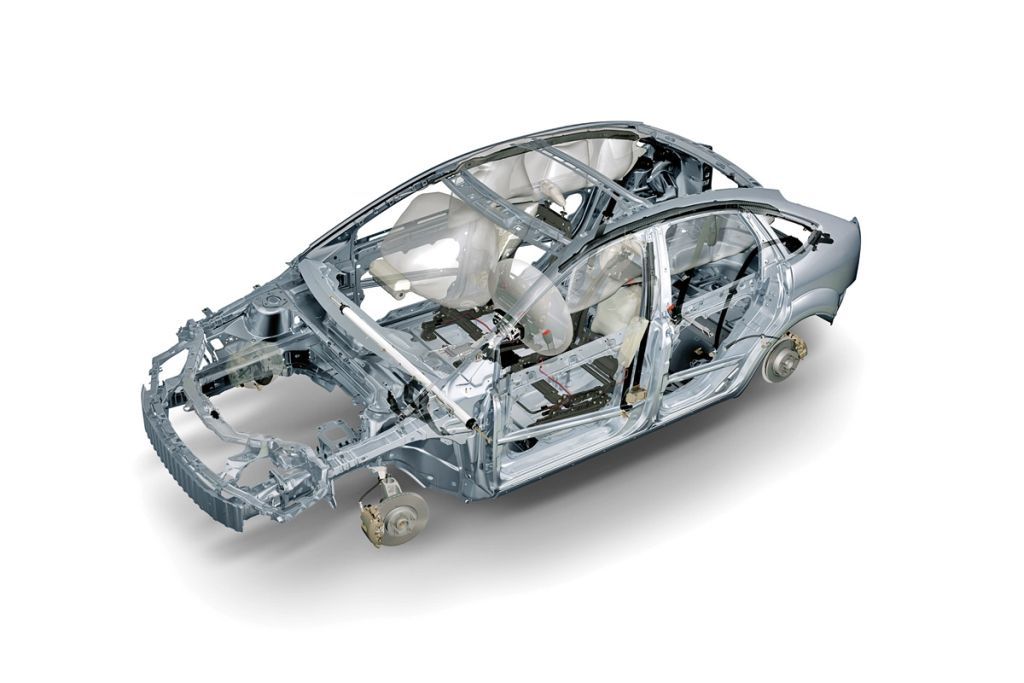
Особенности кузовного ремонта ВАЗ своими руками
Так исторические повелось, что автомобили ВАЗ являются самыми распространенными на постсоветском пространстве. Поэтому стоит поговорить о слабых местах их кузова и наиболее распространенных поломках.Кузовной ремонт «копейки» и других ранних моделей ВАЗ (2101, 21011, 2102, 2103, 2104, 2105) чаще всего вызван солидным возрастом этих автомобилей. За несколько десятилетий их эксплуатации коррозия элементов кузова неизбежна, и если их не пришлось еще менять полностью, то убирать локальную ржавчину – наверняка. Очень уязвимыми местами являются подкрылки, днище и багажное отделение, которые наверняка переваривались, и не раз.
Ремонт кузова ВАЗ 2106 и ВАЗ 2107 чаще всего заключается в устранении коррозии крыльев, днища под передними сиденьями, порогов и багажного отделения, особенно если в процессе эксплуатации авто не были установлены подкрылки и не проводилась прочистка дренажных отверстий. Начинать надо с удаления ржавчины, необходимо зачистить эти места шкуркой или обработать преобразователем ржавчины. Дыры заделываются сваркой или с помощью заплатки. При необходимости производится рихтовка. Подготовленные дефектные места шпатлюются мастикой со специальным антикоррозионным составом. Затем проблемные места затираются наждачной бумагой и обезжириваются силиконовой смывкой. Подверженные коррозии места можно дополнительно обработать смесью шпатлевки с отвердителем, чтобы выровнять поверхность элемента кузова. Можно проводить подготовку к покраске. Ремонт кузова ВАЗ 2107, направленный на устранение коррозии, окончен. Многочисленные видео кузовного ремонта ВАЗ 2107 наглядно демонстрируют этапы проводимых работ.
Ремонт кузова Оки своими руками очень часто сводится к необходимости замены порогов, прочность которых не выдерживает никакой критики. Необходимо также регулярно контролировать состояние днища и арок, которые больше всего подвержены коррозионным процессам.
Ремонт кузова 2109 своими руками может понадобиться по нескольким причинам, зависящим от условий эксплуатации и степени повреждений. Локальных ремонт может заключаться в удалении сколов и царапин. При необходимости исправления геометрии кузова придется проводить полировочные и покрасочные работы. В плане распространения коррозии слабыми местами считаются крылья и пороги, и очень часто кузовной ремонт ВАЗ 2109 направлен на устранение их дефектов.
Ремонт кузова своими руками: все методы и этапы
На чтение 5 мин. Просмотров 15. 8k. Опубликовано
Обновлено
Даже незначительные ДТП могут обернуться достаточно большими финансовыми затратами. При обращении в мастерские может быть выставлена высокая цена. Устранить деформацию кузова, убрать трещины и разрушения, восстановить лакокрасочное покрытие и сделать полировку фар автомобиля можно своими руками. Для этого нужно иметь необходимые инструменты, ресурсы и немного времени в запасе.
Виды ремонта кузова
В домашних условиях восстановление проводится с помощью нескольких методов:
- Сложный.
- Локальный (мелкий).
- Покраска и полировка.
Ремонт кузова своими руками требует тщательной предварительной подготовки. Рекомендуется изучить последовательность действий и посмотреть видео «Как самому сделать кузовной ремонт».
Сложный ремонт
Сложный кузовной ремонт авто, выполненный своими руками, предусматривает проведение рихтовки различных вмятин. При необходимости осуществляется замена поврежденных элементов, например, крыла, восстановление геометрии и сварка полуавтоматом.
Мелкий ремонт
Мелкий ремонт кузова автомобиля своими руками используется для коррекции небольших вмятин, сколов и царапин. В противном случае они могут повлечь за собой появление очагов коррозии (ржавчины). Мелкий ремонт авто своими руками проводится только после окончания гарантийного срока.
Кузовные работы включают в себя:
- Восстановление геометрии проводится после демонтажа всех съемных элементов.
- Устранение вмятин и следов коррозии, залатывание дыр и удаление всех дефектов. При наличии безнадежных элементов проводится их замена.
Полировка и покраска
Кузовной ремонт и покраска – этапы, требующие особого внимания. Не стоит зачищать поверхность, которая превышает по размеру поврежденные участки. Завершающим этапом кузовного ремонта и покраски своими руками является нанесение краски с помощью компрессора.
Для полировки своими силами, после высыхания краски, рекомендуется использовать шлифмашинку.
Этапы диагностики кузова
Ремонт автомобиля требует предварительной оценки, проводящейся в несколько этапов:
- Определить VIN-кода кузова.
- Сравнить с образцом, представленным производителем.
- Пошагово проверить параметры кузова в местах, которые являются проблемными.
Из Википедии: VIN (Vehicle identification number) — идентификационный номер транспортного средства, состоящий из 17 символов, в нем закодирована информация о производителе и характеристиках транспортного средства, и годе выпуска.
Если ремонт жестянки авто, выполняемый своими руками, требует сканирования толщины лакокрасочного покрытия, то для этого используется латунь, алюминий и ферромагнитные материалы.
Виды повреждений кузова
Для того чтобы сделать кузовной ремонт, следует определить вид повреждения:
- Деформация отдельных участков.
- Появление трещин и разрушений.
- Искажение формы проемов (оконных, дверных).
- Нарушение антикоррозионного и лакокрасочного покрытия.
Предупредить появление эксплуатационных повреждений невозможно. Для того чтобы не тратить много денег на их устранение, можно проводить ремонт кузова самим в домашних условиях.
Методы восстановления жестянки авто
- Если металл сильно поврежден, то для ремонта кузова своими силами нужно:
- Использовать наковальню и небольшую киянку.
- Приложить наковальню к внешней стороне вмятины.
- Совершать с внутренней части несильные удары киянкой.
Из Википедии: Кия́нка — столярный молоток из дерева твёрдых пород или резины
Выправление геометрии
При сильных деформациях кузовной ремонт авто требует полного снятия ЛКП. В данном случае для полного восстановления кузова не обойтись без сварочного аппарата и промышленного фена. Сварка осуществляется с помощью графитовых электродов. Сначала вмятина выправляется от ободка к центральной части. Для этого металл нагревается и только после этого прибегают к точечному воздействию. Благодаря этому жестянка становится податливой и пластичной.
Выправление вмятины без покраски
Восстановление кузова авто при несильных деформациях можно проводить без перекрашивания. В таком случае изменение формы осуществляется механически. Процесс занимает много времени и подразумевает воздействие с обратно стороны.
Напайка металла на вмятину
При самостоятельном ремонте кузова без вытягивания применяется метод напаивания специального припоя с использованием паяльника, кислоты и флюса (химически активного вещества). Такой вариант позволяет устранить дефекты и получить идеальный результат.
Метод точечной сварки
Ремонт авто при повреждении кузова предусматривает исправление дефекта снаружи целиком. С помощью сварочного электрода подхватывается металл на деформированном участке. Вытяжение осуществляется обратным молотком. Графитовый электрод обламывается и проводится шлифовка места приварки.
Приваривание заплатки на кузов
Самостоятельно можно устранить даже сквозные дыры. В данном случае нужно полностью вырезать поврежденный кусок, после чего приварить заплатку. Если участки коррозии не велики, то проводится зачистка поврежденных участков до цельного металла.
Последовательность выполнения кузовных работ
При проведении ремонта кузова, как показано на видео, нужно соблюдать последовательность действий:
- Восстановление геометрии.
- Проведение сварочных работ и рихтовки.
После завершения кузовного ремонта авто осуществляется нанесение краски и полировка:
- Очистка, демонтаж наружных деталей (бамперов, фар и светотехники).
- Обработка дефектных мест до чистого металла стамеской и наждачкой.
- Нанесение шпатлевки на неровную поверхность.
- Далее идет этап шлифовки и грунтовка.
Необходимые инструменты и материалы
Перед тем как делать ремонт авто своими руками, следует обзавестись всем необходимым:
- Молоток, ключи и измерительные устройства.
- Самодельный стапель с покупным гидравлическим блоком.
- Шлифмашинка и наждачная бумага (№60 или №100).
- Уайт-спирит, грунтовка и полироль.
Из Википедии: стапель — напольная система для правки деформированного кузова автомобиля, действующая с помощью многотонных давящих и растягивающих сил.
Без проблем восстановление кузова можно провести при наличии начальных навыков сварки и рихтовки. Выполняемые действия не зависят от марки автомобиля. Кузовной ремонт и покраска кузова, выполненные собственными силами, позволяют сэкономить время и деньги.
Кузов современного автомобиля
Любой автомобиль состоит из ряда составных узлов – силовой установки, трансмиссии, ходовой части, систем управления.Чтобы собрать все эти элементы в единую конструкцию и обеспечить их взаимосвязь между собой, используется еще один конструктивный компонент – несущая часть, к которой и осуществляется крепление всех составляющих элементов.
Назначение, конструкция и виды несущей части
По мере развития автомобилестроения было создано несколько видов несущей части. Но несмотря на имеющиеся различные типы, эта составляющая включает в себя один из основных компонентов – кузов автомобиля.
В задачу кузова входит не только крепление составных частей авто, а еще и восприятие всех нагрузок и воздействий окружающей среды, а также обеспечение пространства для размещения пассажиров и груза.
Изначально на автотранспорте применялась несущая часть, состоящая из двух элементов – кузова и рамы. В такой конструкции кузов по большей части принимал на себя только нагрузки, которые создавали пассажиры и груз. Основные же воздействия приходились на раму, которая также выступала основным связующим элементом для составных частей авто (именно к ней крепились узлы и механизмы).
Но существуют и другие виды несущей части. В целом, она подразделяется на:
- Рамную;
- С несущим кузовом;
- Комбинированную.
Рамный вид, как уже отмечено, состоит из двух элементов – рама и кузов автомобиля. Между собой эти элементы соединены посредством эластичных проставок. Изначально он применялся на всех авто. Сейчас же такую компоновку несущей части можно встретить только на грузовиках и внедорожниках (хотя на последних – не всегда). Поскольку кузов в такой конструкции не используется в качестве компонента, к которому крепятся составные элементы, второе название этого типа – с разгруженным кузовом.
Рамный кузов
Со временем на легковом транспорте рамную конструкцию вытеснил несущий кузов автомобиля. Особенность его заключается в том, что рама, как таковая, отсутствует. При этом все составные части крепятся к кузову. Но поскольку в этом типе вся нагрузка приходится на кузов, в некоторых участках присутствуют усиливающие элементы, повышающие жесткость конструкции. Сейчас этот тип несущей части используется на всех легковых авто, а также кроссоверах и некоторых внедорожниках.
Несущий кузов
Последний вид – комбинированный, он же – полунесущий кузов автомобиля, отличается тем, что в несущей части присутствуют как рама, так и сам кузов, но при этом они между собой жестко связаны. В такой компоновке воспринимаемая нагрузка распределена между ними, также оба они выступают в качестве элементов для крепления составных узлов. Этот тип несущей части применяется в автобусах.
Конструкция кузова
Как видно, во всех типах несущей части присутствует кузов автомобиля. От этого элемента во многом зависит внешний вид машины, комфортабельность, показатели безопасности. Поскольку на легковых авто наибольшее распространение получил несущий кузов, то в дальнейшем рассматривать будем именно его.
Такой кузов автомобиля представляет собой некий каркас, состоящий из ряда составных частей, к которым крепятся узлы авто, а также внешние элементы, выполняющие определенные функции, включая и декоративные – крылья, двери, капот, крышка багажника, оптические приборы, бампера и прочее.
Конструкция кузова
Конструкция кузова автомобиля включает в себя:
- основание;
- переднюю и заднюю часть;
- боковины;
- крышу.
Каждая из составных частей состоит из ряда компонентов. Все они соединены между собой при помощи сварки, что обеспечивает необходимую жесткость каркасу.
В качестве основания выступает днище, выполненное в виде щита с подогнутыми краями и проделанным в центральной части тоннелем. Этот тоннель не только повышает жесткость основы, но еще и выступает каналом для прокладки некоторых составных элементов авто – топливных и тормозных трубопроводов, труб системы отвода выхлопных газов, а в задне- и полноприводных авто – еще и для размещения ряда узлов трансмиссии. В некоторых авто в днище дополнительно проделывается ниша для размещения запасного колеса (в задней части).
Одной из основных функций передней части кузова авто является обеспечение пассивной безопасности. При фронтальном столкновении составляющие передка принимают на себя весь удар, и деформируясь гасят энергию. Поскольку для этого необходима достаточно высокая прочность, конструкция передка включает в себя продольные лонжероны. В авто с переднемоторной компоновкой они также выступают в качестве конструкции для крепления мотора. Дополнительно для выполнения этой функции передняя часть может комплектоваться подрамником.
Также в состав этой части входят передний щит, отделяющий мотор от салона, панель для крепления оптики и радиаторной решетки, боковины с колесными арками, которые могут быть выполнены заодно с крыльями. Но зачастую крылья делают съемными, поэтому являются навесной частью, так же, как и бампер с решеткой радиатора. Передняя часть сверху накрывается капотом – специальной крышкой.
Примерно такую же компоновку имеет и задняя часть, но зачастую крылья у нее входят в конструкцию и не являются съемными.
Дополнительно заднее крыло входит в конструкцию боковины кузова. Помимо нее боковина включает в себя пороги – одни из основных элементов, которые на ряду с лонжеронами обеспечивает жесткость конструкции.
К боковинам также относятся стойки – передняя, средняя и задняя, к которым крепиться крыша – цельноштампованный лист металла заданной формы. Съемными элементами этой составляющей являются двери авто.
В целом, днище с порогами и стойки с крышей и дверьми формируют отсек для размещения пассажиров.
Как уже отмечено крепления составных элементов осуществлено при помощи сварки, что делает конструкцию кузова неразъемной, поэтому многие компоненты одновременно относятся к нескольким его составляющим частям.
Стоит сказать, что состав кузова автомобиля может не иметь каких-то определенных частей. К примеру, в кузове кабриолет крыша отсутствует как таковая. Но поскольку в обычной компоновке нагрузка распределяется и на нее (за счет цельной конструкции), и крыша тоже в некоторой мере обеспечивает жесткость, то в кабриолете для компенсации снижения жесткости кузова усиливают пороги и двери.
Компоновка кузовов
На конструктивные особенности кузова автомобиля также влияет и компоновка. Все существующие типы несущей части по этому параметру подразделяются на:
- Однообъемные;
- Двухобъемные;
- Трехобъемные.
Суть разделения кузовов авто по этому критерию сводится к тому, на сколько частей поделен кузов.
Особенность однообъемной компоновки заключается в том, что разделения между моторным отсеком, салоном и багажником – нет (но это условно). Еще этот вид компоновки называют вагонным.
В авто с таким кузовом передняя часть вообще отсутствует, а двигатель помещен в специальную нишу отсека для размещения пассажиров и груза. Отсутствие разделения между отсеками считается условным потому, что двигатель все же отделен от кабины перегородкой.
Однообъемный кузов автомобиля Tata Nano
В свою очередь однообъемный кузов делится на:
- Грузовой;
- Пассажирский;
- Грузопассажирский.
Разница между ними сводится к тому, под что большая часть внутреннего объема кузова отведена. Так, в грузовом для размещения пассажиров отведен совсем незначительный объем, в который входит также и отсек для мотора (по сути, водитель сидит возле, а то и вовсе на двигателе), а все остальное пространство отведено под размещение грузов.
В пассажирском же варианте весь доступный объем предназначен для размещения пассажиров, а под груз выделяется небольшое пространство (которого и вовсе может не быть).
Грузопассажирский кузов отличается тем, что внутренний объем условно делится на два отсека (пассажирский, грузовой). В некоторых случаях все пространство авто заполнено сиденьями для пассажиров, которые можно быстро демонтировать или сложить, тем самым получить грузовой отсек.
Двухобъемный кузов автомобиля включает в себя отдельно переднюю часть, являющуюся моторным отсеком и салон, который совмещен с отсеком для перевозки грузов. Самыми распространенными представителями такой компоновки являются хэтчбек и универсал. Также она используется у внедорожников с кроссоверами.
Двухобъемный кузов кроссовера
В большинстве случаев основная часть салона отведена под размещение пассажиров, а для груза отводится не очень много места. Но если взять универсал, то очень часто конструкторы делают задние сиденья складывающимися, что значительно повышает размеры грузового отсека, делая авто, по сути, грузопассажирским. Для доступа к грузовому отсеку в этом типе предусмотрена отдельная дверь – задняя (в некоторых авто она двойная).
Трехобъемный кузов автомобиля отличается тем, что моторный отсек, салон и грузовой отсек отделены перегородками друг от друга. Основным представителем такой компоновки является седан.
Современные реалии
Напоследок отметим, что конструкторами разработано большое количество разнообразных типов кузовов (перечисленные выше являются основными из них). Из-за этого в некоторых случаях разница между компоновками нивелируется.
К примеру, лифтбек имеет трехобъемную компоновку. Но у него крышка багажника объединена с задним стеклом, поэтому является, по сути, задней дверью. Вот и получается, что вроде и отдельный багажник есть, но в то же время он входит в состав салонного отсека (поскольку открывая багажник получаем одновременно и доступ к салону). И таких примеров несколько.
Но в целом, широкое разнообразие несущих кузовов позволяет делать автомобили разных типов и назначения.
Подготовка авто к покраске: пошаговая инструкция
Шлифование
Следующий важный этап подготовки к реставрации лакокрасочного покрытия — шлифовка. По принципу действия она схожа с зачисткой, но выполняется несколько иначе, с применением более деликатных абразивов.
Шлифовка решает несколько задач:
- Удаление остатков старого покрытия.
- Максимальное выравнивание поверхности путем удаления излишков застывшей шпаклевки.
- Обеспечение адгезии основания с грунтовкой/эмалью – для этого при шлифовании все поверхности делаются шероховатыми.
Шлифовать можно вручную (при локальной окраске) или с использованием шлифовальных машинок. Сама обработка может вестись мокрым или сухим способом.
Для обеспечения максимального качества сухое шлифование будет предпочтительным. Во-первых, мокрый способ неприменим при обработке полиэфирных шпаклевок, во-вторых, так снижается риск коррозии. Но при шлифовании без увлажнения важно соблюдать технику безопасности, используя средства индивидуальной защиты, а в идеале – обеспечивая принудительное удаление пыли из рабочей области.
Еще один важный фактор, влияющий на качество подготовки – выбор шлифовального материала:
- Для черновой обработки используется абразив Р120, края участков сглаживаются абразивом Р180-220.
- При выравнивании зашпаклеванного участка применяется абразив до Р180 (желательно принудительное удаление пыли, потому что она быстро забивается в промежутки между абразивными зернами).
- При подготовке под грунт выполняется машинная обработка с применением абразивов Р220–Р320.
- Непосредственно перед окраской поверхность может шлифоваться бумагой до Р500 (при машинной обработке) или Р1000 (при ручной).
Обратите внимание! При использовании нескольких абразивов в рамках одного этапа уменьшение размера зерна не должно превышать 100 единиц за раз.
Грунтование
Грунтовка — это промежуточный слой, отвечающий за равномерное распределение эмали по поверхности и обеспечивающий повышение адгезии. Кроме того, грунт частично компенсирует огрехи предыдущих этапов подготовки, потому что полностью очистить все детали от пыли, грязи и жировой пленки практически невозможно.
По принципу действия грунтующие составы делятся на две категории:
- Первичные — повышают адгезию ЛКП и основания, защищают основу от коррозии, формируя пленку, непроницаемую для кислорода.
- Наполнители – проникают внутрь царапин, образовавшихся в результат обработки абразивом, заполняют пустоты, выравнивая поверхность. Благодаря обработке наполняющим грунтом краска ложится на кузов машины значительно ровнее.
Перед нанесением грунт необходимо тщательно перемешать, если нужно, добавив в основу отвердитель/растворитель. При использовании заколерованного грунта в состав вначале добавляется краска, а после получения нужного оттенка вводятся дополнительные компоненты.
Грунтовка обычно наносится в несколько слоев, причем каждый слой требует тщательной просушки. После высыхания поверхность можно обработать проявляющим составом – он покажет, какие участки требуют доработки (например, дополнительного выравнивания шпаклевкой).
Оптимальный вариант – трёхслойная грунтовка, при этом каждый следующий слой нужно наносить перпендикулярно предыдущему. Обработку можно выполнять только после того, как нанесенный материал полностью высохнет, иначе часть растворителя «закипит», что приведет к появлению микропузырьков.
После высыхания финишный слой грунта шлифуется тонкозернистым абразивом — и машину можно красить.
Самодельные автомобили теперь можно ставить на учет в ГИБДД — Российская газета
Теперь самоделки тоже имеют право на получение в ГИБДД регистрационных номеров, а соответственно и право самостоятельно передвигаться по дорогам.
Для регистрации конкретного автомобильного чуда необходимо обратиться в орган сертификации, представить туда «изделие», получить документ о соответствии транспортного средства предъявляемым техническим требованиям. А затем с полученной бумагой идти в ГИБДД и ставить машину на учет.
Постановление о 50 лошадях
Любовь к созданию многочисленных машин по собственным проектам появилась у нас не от хорошей жизни. В Советском Союзе не было и речи о выпуске автомобилей под запросы конкретного потребителя — хватило бы сил дать рынку массовые модели. Поэтому энтузиасты из подручных материалов и своими руками делали машины, отвечающие требованиям жизни.
Из трех старых, убитых собирали одну живую. На селе из легковых кузовов делали грузовые. Создавали амфибии, чтобы преодолевать болота и другие водные препятствия. Увеличивали грузоподъемность, удлиняли кузова — ведь грузовики не продавались в личное пользование.
Были и эстеты, которых не устраивала сама форма серийного легкового автомобиля. Они создавали автоварианты — от прилизанных спорткаров до самых фантастических и иногда нелепейших конструкций. Все это показывалось на выставках и на вполне законных основаниях ездило по дорогам.
В советские годы самоделки не то чтобы поощрялись, но во всяком случае не запрещались. Первые серьезные ограничения появились в 80-х годах. А именно — ограничения по мощности (50 лошадиных сил на тонну), по габаритам (4,7 метра по длине и 1,8 метра по ширине). Оставалась одна лазейка, которой и пользовалось большинство. Ведь регистрировали технику не только в ГАИ, но и в Ростехнадзоре. Например, трактора. Внедорожники же в те времена вполне подходили под эту категорию. А требования к самоделкам в Гостехнадзоре были значительно мягче. В результате с 1993 по 1995 год было зарегистрировано наибольшее количество автомобилей ручной сборки.
Годы полного запрета
2005 год оказался черным для самоделок — их регистрацию и в ГАИ, и в Ростехнадзоре запретили вовсе. Верховный суд РФ аргументировал запрет тем, что надо разработать четкие требования к «самодельной» продукции. Хотя настоящая причина, видимо, крылась в борьбе с новым явлением на авторынках — в продаже так называемых конструкторов. Суть рыночного бума на «конструкторы» была проста: чтобы уйти от налогов, машину (например, японскую) сначала ввозили в Россию в виде запчастей, затем собирали ее, а регистрировали как самодельную.
Однако запрет этот, к сожалению, коснулся и авторов настоящих отечественных самоделок. Их-то творческий энтузиазм не иссяк! Доказательство тому — ежегодные выставки «Автоэкзотика», где самоделки представляются в огромном количестве. Однако в большинстве случаев это машины без номеров, привезенные на эвакуаторе и права на жизнь на дорогах не имеющие. Хотя как раз на дорогах иные самоделки могли дать фору многим серийным автомобилям.
Оковы рухнули
Новые требования, которые определяют порядок сертификации, наконец, приняты и утверждены. Приказ Ростехрегулирования, утвердивший изменения N1 «Правил по проведению работ в Системе сертификации механических транспортных средств и прицепов» вступил в силу в январе этого года.
Итак, как же поставить самоделку на учет в новых реалиях? Для начала потребуется обратиться в орган сертификации. Их не так уж и много по стране. Ближайший к вам можно выбрать из списка, который опубликован на сайте Рос техрегулирования. (адрес сайта: http://www.gost.ru/wps/portal/)
Оценивать самоделку теперь будут по упрощенной схеме. Как «транспортное средство, производимое малыми сериями». Минимальное количество автомобилей в малой серии — 1 штука.
Есть тут и небольшая хитрость, с помощью которой государство спасло себя от ввоза «конструкторов». Количество автомобилей в малой партии необходимо указывать. Понятно, что тот, кто собирает для себя, больше одного автомобиля одного типа делать не будет. А тому, кто попытается лукавить с государством и под заказ привозить машинокомплекты, занимаясь практически промышленной сборкой, по новым правилам сертификации работать будет невыгодно. Ведь количество машин в партии проверяется. Повторить процедуру сертификации нельзя.
Правда, и полученное одобрение типа не имеет срока действия. Оно заканчивается тогда, когда вступают в силу новые технические требования. Например, с нового года вступили в силу требования по экологичности Евро 3. Значит, именно с этого года прекратило действовать и одобрение типа. Ведь одобряло оно нормы Евро 2.
По правилам ООН
Новые требования к самодельным машинам, естественно, не ниже, чем к выпускающимся серийно. Тут послаблений нет, а главное, самоделки должны соответствовать правилам Европейской экономической комиссии ООН. И хотя малые партии будут сертифицировать по усеченному списку требований, все равно это серьезная процедура.
Согласно документу, проверяться на соответствие требованиям будут травмобезопасность рулевого колеса, тормозные свойства, места крепления ремней безопасности и сами ремни, стекла, зеркала заднего вида и их установка, установка устройств освещения и световой сигнализации, управляемость и устойчивость, внутренний шум, содержание вредных веществ в салоне, и, конечно, содержание вредных веществ в выхлопе. Это — выборка для легковых автомобилей.
приятный момент
Есть в новых требованиях и пункт, приятный для изобретателей. Машины на испытаниях теперь увечить не будут: «В отношении единичных транспортных средств проводятся испытания, не вызывающие их повреждения. Допускается замена испытаний, вызывающих повреждения, экспертной оценкой конструкции».
После всех этих экспертиз, если машина удовлетворяет требованиям, хозяин, он же изобретатель, получает одобрение типа. С этим документом — прямой путь в подразделение ГИБДД по месту жительства, где выдадут паспорт транспортного средства и поставят автомобиль на учет. Данные об одобрении типа заносятся в ПТС.
Конечно, вряд ли эти нововведения вызовут бурный всплеск в самодеятельном конструировании новых и необычных типов автомобилей. Но во всяком случае нашим Кулибиным жить станет теперь легче.
Самые известные самоделки последнего времени: слева — ISV, получивший приз как самый экзотичный автомобиль года на выставке «Автоэкзотика», справа — автомобиль «Агата», построенный членами московского Фонда авторских автомобилей.
Вопросы от клиентов и ответы на них
На ваши вопросы отвечает Евгений Павлович Митрохин, старший специалист по кузовному ремонту. Опыт работы на этой должности: 17 лет. Самый старший и профессиональный сотрудник в нашем центре.От чего зависит цена ремонта кузова в мастерской?
Разумеется, стоимость зависит от марки вашего авто, точнее от того, насколько дорогие запчасти к нему необходимы. Также значительную роль играет степень повреждения кузова или попросту объем работы, которую необходимо будет сделать специалистам в сервисе. Также значимые аспекты при определении сервисом цены услуг это популярность СТО, в которое вы обратились.
Сколько может длиться кузовной ремонт при средней степени повреждения?
Процесс ремонта и восстановления автомобильной поверхности может занять неделю-две в мастерской. Если вы решили осуществить это самостоятельно, тогда придется уделить автомобилю где-то месяц внимания.
Должны ли сотрудники автосервиса помыть и почистить машину, если она была отдана им для починки кузова?
Так делают далеко не везде, а должны бы. Прежде чем машина вернется к своему законному владельцу, сотрудниками СТО она должна быть приведена в полагающий вид, даже если привезли ее не в самом чистом состоянии. Деньги за такую услугу, как правило, не берутся.
Может ли кузовной ремонт каким-то образом улучшить общее состояние авто или ухудшить его?
Ремонт кузова действительно содействует улучшению работы авто. Качественно сделанный ремонт кузова обеспечивает ходовые параметры, а также повышает безопасность вождения.
Насколько должен быть поврежден кузов, чтобы его невозможно было восстановить?
Конкретного определения нет. Просто в некоторых случаях количество вмятин и царапин превышает все нормы, тогда в мастерской вам сразу объявят — требуется замена кузова.
Как удалить царапины с поверхности кузова?
На сегодняшний день большой популярности приобрел знаменитый и известный почти всем маркер для удаления царапин с авто. Но на самом деле не все так прекрасно и хотя мало понимающие в автомобильном деле женщины с радостью покупают такие «подарочки» своим мужьям, те не приходят в дикий восторг от такого презента, ведь уже после первой попытки исправить какую-то даже крошечную царапину понимают бесполезность такой покупки. Лучше всего обращаться к профессионалам.
Где чаще всего появляются повреждения после столкновения бампером?
Как ни странно, но на крыше. Поэтому если вы поймали ворону и зацепили чье-то авто передней частью своей машины, прежде всего осмотрите область столкновения, а потом проанализируйте состояние крыши, там могут появится трещины краски, которые в итоге прибавят общему процессу ремонту немало проблем и затруднительных моментов.
Что значит если при столкновении на красочном покрытии автомобиля лишь образовались трещины, а больше никаких повреждений не замечено?
В таком случае практически стопроцентная гарантия, что внутри авто тоже повреждено. Треснувшая в нескольких местах краска, которая непосредственно до момента столкновения была нормальной, практически всегда обозначает повреждение внутренних деталей машины.
Как произвести диагностику состояния кузова, не имея навыков и умений?
Ответ один — никак. Если не умеете анализировать состояние автомобиля и чинить его, то на ремонте кузова уж точно учиться не стоит. А уж если знаниями о ремонтных работах обладаете весьма глубокими, то диагностировать состояние авто все равно лучше доверьте профессионалам. Это обойдется совсем недорого, зато починка будет происходить более целенаправленно.
Визуальный осмотр — эффективный ли метод диагностики?
Разумеется, что нет. Простым осмотром в таком деле явно не обойтись. В некоторых автомастерских используется высокотехнологичное оборудование, чтобы максимально точно определить отклонение каждой детали и иметь возможность отремонтировать все до мелочей.
Преимущества ремонта в автосервиса — есть ли они?
Безусловно да. Давайте посчитаем минусы и плюсы, возможно так будет понятней. Из минусов в голову приходит лишь цена, конечно же это дороже, чем делать все самому, но теперь переходим к плюсам, которых, кстати, значительно больше. Для начала стоит сказать о том, что ремонт будет выполнен профессионально, машина будет качественно отремонтирована и покрашена. По вашему желанию сотрудники мастерской могут дать рекомендации касательно, скажем, покраски вашей машины самостоятельно, так сказать на будущее. А также к плюсам относится гарантия, которую выдают большинство сервисов. Гарантия ремонта длится от полугода до года.
Возможно ли отреставрировать деформированный кузов или нужно непременно менять его?
В некоторых случаях деформация может быть несущественной, тогда можно обойтись просто рихтованием и корректировкой повреждений, а уже потом осуществляется покраска. Во всех остальных случаях следует менять поверхность на новую.
В случае замены кузова важно ли, чтобы детали были того же производителя, что и автомобиль, то есть оригинальными?
Особо острой необходимости в этом нет и если уж никак не получается найти именно таких деталей, можно взять другие от другой фирмы. Но желательно все же запчасти приобретать той же марки, то и машина. Тогда работа вашего четырехколесного друга будет более исправной.
Как полировать машину
Как полировать машину? Что это за процесс и чем он полезен? Почему на сервисах берут за данную процедуру большие деньги? В этой статье мы ответим на эти вопросы и капнем поглубже, чтобы понять как правильно можно отполировать автомобиль самому.
1. Что такое полироль?
Полироль для кузова— это стабильная эмульсия, либо пастообразное вещество, которое устойчиво к разделению и обладает большим, почти неограниченным сроком хранения.
Формула полировочного вещества весьма сложная — это смесь силиконовых смол и силиконов, а также смеси различных восков (если мы говорим о защитных составах для кузова). Абразивные составы содержат частички абразива, которые срезают верхний слой лака с глубокими царапинами и повреждениями на кузове. В составе полироли могут быть также элементы, которые усиливают цвет кузова и заполняют собой царапины и потертости, этакие пигменты и нерастворимые красители.
Полируя автомобиль защитными составами, мы фактически наносим на кузов защитный слой (прямо как зубная паста 🙂 ), который эффективно снижает воздействие солей, кислот, ультрафиолета и прочих аспектов дикой и городской среды.
Виды полиролей
Не будем заострять на этом много внимания и быстро пробежимся по основным видам полиролей, существующих в мире:
- синтетические полироли;
- полироли очистители-восстановители;
- силиконовые полироли;
- полимерные полироли;
- абразивные полироли.
2. Этапы полировки
В основном, полировку делят на два этапа:
- первая — восстановительная полировка;
- вторая — защитная полировка.
Рассмотрим каждый из них подробнее:
Восстановительная полировка, как правило, производится с использованием абразивных паст. Такой полировкой снимается тончайший, самый верхний слой лака, побитый жизнью, полный царапинок, потертостей и сколов — он уже только портит внешний вид автомобиля, поэтому и подлежит удалению. В итоге получаем свежий, красивый, блестящий кузов автомобиля.
Теперь очередь за этапом защитной полировки. Её нужно производить сразу, на только что восстановленное покрытие. Помните, что прошлым этапом полировки мы сняли слой лака? Разумеется, в таком состоянии кузов автомобиля оставлять ни в коем случае нельзя — он подвержен влиянию окружающей среды намного сильнее, чем был до этого. Поэтому, сразу после снятия верхнего слоя лака, мы нанесем слой полироли для кузова, который заполнит собой все микротрещины, так называемые поры, тем самым не дав попадать в них кислотным дождям и прочим неприятым воздействиям. К тому же, защитная полироль добавит вашему автомобилю насыщенность цвета и отличный блеск. К сожалению, такая полировка не долговечна. Специалисты рекомендуют проводить её регулярно, раз в два-три месяца.
Слегка ознакомившись с теорией, предлагаю перейти к практике.
3. Как полировать машину
Этап первый — подготовка автомобиля — очистка и обезжиривание кузова. Сперва наперво необходимо хорошенько отмыть автомобиль от пыли, грязи и песчинок. Затем лакокрасочные покрытие необходимо высушить и вытереть насухо чистой тряпкой (лучше микрофибровое полотенце или искусственная замша). Вполне вероятно, что водой могут не смыться некоторые вещества, например гудрон. Возьмите Уайт-Спирит и очистите поверхность от всего, что не отмылось водой (или средство для удаления битума). Для идеального результата можно очистить кузов абразивной глиной для очистки кузова перед полировкой.
Второй и самый главный этап — полировка кузова. В этом этапе нам понадобится чуть больше инструментов, чем тряпка, вода и Уайт-Спирит (или профессиональные товары для полировки).
Инструменты. Для хорошей полировки требуется профессиональная полировальная машинка, например производства Makita. Можно обойтись и дрелью, но вибрация, отдаваемые в руки будет сильнее, что не очень хорошо скажется на их состоянии после. Также нужны полировочные круги (полировальники). Два — для грубой и тонкой полировки. Они могут быть шерстяными и поролоновыми. Осталось купить полировочных паст (полироли) и запастись трудолюбием и терпением.
4. Сколько стоит на сервисе
Процедура довольно трудоемкая. Чтобы провести полировку автомобиля тщательно, нужно действительно любить свой автомобиль. На сервисах, где поток клиентов большой, отношение к автомобилю другое, соответственно и качество выполненной работы будет ниже. Мало того, из-за того что полировка одного автомобиля может занять полный рабочий день, это стоит немаленьких денег. Цены разнятся от места к месту, но если вам назвали цифру 150$, то не пугайтесь — так будет почти везде. Если же хочется сэкономить, или просто сделать самому, то читайте дальше, чтобы узнать как полировать машину своими руками.
5. Выбор пасты всегда за вами!
Полировочные пасты бывают разного качества и разных производителей. Для примера возьмем пасты американского производства «3M» — это великолепные полировочные вещества профессионального класса. Продаются они в тубах по 1кг, одной тубы хватает пример на полировку 3-7 кузовов. Выбор пасты всегда остается за вами, но не забывайте, что их у вас должно быть не меньше трех — с грубым абразивом, с мелким абразивом и безабразивная (финишная или антиголограммная паста).
Ну, приступим. Полировку начинаем пастой с грубым абразивом, в нашем случае — № 09374. Наносить её нужно на полировальник, можно сразу из тубы. Необходимо небольшое количество — около 10-20 грамм, что примерно эквивалентно чайной ложке без верха. Мало пасты единовременно используется для того, чтобы она не успевала высыхать. Отсюда следует, что площадь поверхности, которую вы будете полировать, также должна быть не большой — примерно 40 на 40 см.
На полировочную машину одеваем круг, предназначенный для грубой полировки. Эти круги чаще всего светло-оранжевого цвета (в 3М полировальный круг 09550). Затем, не включая машинку, размазываем пасту равномерно по всей площади обрабатываемой поверхности. После «размазывания» самое время включить машинку на самую низкую скорость, и распределить с помощью неё пасту по всей поверхности, опять же равномерно.
Чтобы избежать неравномерности полировки, движения необходимо осуществлять крестом — сначала горизонтально, потом вертикально. Повторить «крест» нужно раза два, после этого следует немного повысить скорость машинки и повторить процедуру. И так еще несколько раз.
Затем, чистой салфеткой или мягкой микрофибровой тряпочкой убираем оставшуюся полировочную пасту. На этом наш, так называемый «цикл», закончен, и можно приступать к следующему небольшому куску поверхности.
И так, обработав всю машину пастой №74 не спешите расслабляться. Берем полироль для кузова № 09375 и продолжаем придавать блеск и цвет кузову, повторяя описанные выше действия. Используем так же оранжевый полировальник.
Кстати, полировочную губку необходимо мыть в теплой воде после каждых 3-4 обработанных участков. Чтобы губка быстрее высохла, можно покатать её с ветерком, включив на машинке самую высокую скорость.
Действия с пастой №75 подошли к концу. Покурим, отдышимся и перейдем к полировальной пасте № 09376.
Но грубый кружок уже устал, самое время помучить кружок помягче, предназначенный для мягкой полировки. Чаще всего он светло-серой окраски и, разумеется, мягче, чем его предшественник. В 3М это круг для полировки кузова № 09378.
На мягкую, сухую и чистую тряпочку наносим нашу пасту и круговыми движениями распределяем её по всему полируемого элементу (прошлый раз мы делали это кругом на машинке). Не ленитесь! Ни в коем случае не допускайте сгустков пасты, разотрите все как можно тщательнее. После этого ждем пару минут, и когда паста начинает белеть, а значит подсыхать — берем машинку, включаем на среднюю скорость и полируем наш участок. Со всеми остальными кусками точно таким же образом.
6. Последний штрих
Машина отполирована, кузов блестит, цвет насыщен, вы уже не в состоянии стоять на ногах, но остался еще один небольшой штрих — защитная полироль.
Процесс нанесения «защитки» точно такой же как и с пастой №76. Не забывайте обновлять защитный слой полироли хотя бы раз в месяц и можете быть уверенным, что цвет, блеск и безопасность вашего лакокрасочного покрытия не будут вас расстраивать!
Как видите полировать машину не так уж сложно. Однако требует сноровки, труда и конечно же любви к собственному автомобилю.
Отличным обучением будет просмотр видеороликов о полировке кузова на интернет порталах.
Способ сборки кузовов автомобилей разных типов
(57) Реферат:
В основном предлагаемый способ относится к автомобильной промышленности. Решение технической задачи предполагает при минимальных затратах и сложности сборки обеспечить различную форму и габариты автомобильных кузовов. Способ заключается в предварительной изготовлении корпусов из элементов разного типа и их последующей взаимной сборке. Что нового, так это то, что выполненные опорные базы, которые являются общими для всего семейства автомобилей, одновременно составляют узел бортовой части кузова, количество которых соответствует количеству разной формы и размеров собираемого кузова, и передних подрамников, количество которых соответствует количеству модификаций различных силовых агрегатов, крепление которых унифицируется с креплением к опорному основанию, а крепление других формирующих элементов кузова будет унифицировано с их местами крепления на передней раме и корпусе. стороны кузова через основные узлы. Сборка конкретного кузова осуществляется путем позиционирования рельсов и соединительных устройств, расположенных на узлах боковых стенок бетонного кузова и переднего подрамника, затем на полученном узле закрепляются все другие формирующие элементы конкретного тела.Этот метод в первую очередь предназначен для массовой (OEM) сборки автомобилей. 2 п. ф-кристаллы, 4 ил. Изобретение относится к транспортному машиностроению, а именно к способам сборки кузовов автомобилей различных типов. Известен способ изготовления транспортного средства (заявка Франции N 2643034, кл. B 62 D 27/00, опубл. 24.01.89 г). , состоящий в раздельном изготовлении четырех составляющих элементов автомобиля: днища кузова, двух боковых подушек безопасности, багажника на крыше; установлено на каждом из четырех элементов соответствующее оборудование и аппаратура; сочетание этих четырех элементов технологии, исключающее сварку, склеивание, герметизацию, клепку или завинчивание, а также различные комбинации этих технологий; после установки на собранном узле узлов и деталей выпускники получают готовое изделие.Известен также модульный автомобиль (заявка США N 4874200, класс B 62 D 25/00, опубл. 17.10.89 г), который содержит моторный отсек в сборе, имеющий приборную панель, и панель приборов на его заднем конце, напольный агрегат, имеющий переднюю часть. и задняя панель, две боковины, каждая из сборок пола Которского залива, сборка боковины и сборка крыши являются независимыми частями кузова автомобиля, которые изготавливаются и окрашиваются независимо друг от друга. Кузов снабжен крепежными элементами для механического соединения между узлом моторного отсека, узлом пола, узлом боковой балки и узлом крыши, а также элементами заземления для электрического соединения между узлом моторного отсека, узлом пола, узлом боковины и узлом крыши. .Отсутствие модулей передних и задних подрамников препятствует модификации ведущих колес и мощности силового агрегата. В описании патента также отсутствуют сведения о технических возможностях модификации типа и форме кузова в плане кабины. Из патента Германии N 4313562, кл. B 62 D 23/00, опубл. 27.10.94 г. Известен кузов для автомобиля, боковые стенки которого образованы порогом пола из продольного образующего боковую стенку из экструдированного профиля. Опора из профилированного поперечного перекрытия примыкает к порогу.Часы из гнутых экструдированных профилей, которые устанавливаются на конвейерную линию, являются каркасом кровли. Профиль, образующий боковую стенку, разделен по длине и имеет спазиатуры для передней и задней части модуля. В этом кузове по длине автомобиля изменилось сечение несущих частей, несмотря на использование экструдированных профилей. Несущий пол также соответствует всем техническим требованиям. Благодаря стоечному каркасу крыша увеличивает характеристики по сравнению с кузовом, состоящим из неразрезанных продольных профилей.В качестве прототипа выбран способ изготовления транспортного средства с несущей базой и кузова с пластиковыми деталями, описанный в заявке стран СНГ N 0240470, кл. B 29 D 29/04, опубл. 07.10.87 г. Автомобиль содержит предварительно смонтированную несущую базу, на которой смонтированы механические прочностные и функциональные узлы и агрегаты, а также внутреннее оборудование, а также отдельно собранный кузов, состоящий из предварительно смонтированных и готовых узлов, содержащих детали, отлитые из пластика. Корпус крепится к опорному основанию методами автоматизированной сборки с помощью клея, дополненного, возможно, механическими средствами крепления, без использования сварки.Технические решения считаются равнозначными, а прототип обеспечивает простоту монтажа, обслуживания и ремонта, создает гибкий производственный цикл SBAR в производстве. Однако с помощью этих методов невозможно собрать различные по форме и размерам типы кузовов на основе Существующий фундамент.Техническое решение предусматривает возможность сборки кузовов различных форм и размеров на единой, общей для всех кузовов модификациях основе.Для решения технической проблемы известен способ сборки кузовов автомобилей разного типа, заключающийся в изготовлении из формовочных элементов под разные типы кузова и их последующая взаимная сборка, изготовление опорной базы, которая является общей для всего семейства автомобилей, одновременно производят узел боковой части кузова, количество которых соответствует количеству различных форм и размеров. кузова в сборе, и передних подрамников, количество которых соответствует количеству модификаций вариометра. нас силовые агрегаты, насадки, которые объединяются с прикреплением к опорной базе, и крепления других формирующих элементов корпуса будут унифицированы с их местами крепления на передней раме и сбоку корпуса через основные узлы, построить конкретный корпус осуществляют перцовые и горизонтальные плоскости, а также жестко-съемное крепление на несущую основу соответствующих узлов боковых стенок бетонного кузова и переднего подрамника, после чего в полученном подсборке фиксируют все остальные формирующие элементы конкретного кузова.При изготовлении несущих оснований для сборки полноприводных автомобилей дополнительно устанавливаются задние подрамники, крепление которых унифицировано с их креплением к опорному основанию. При изготовлении несущих оснований для сборки общественного кузова или лимузина дополнительно Установлена центральная перегородка, представляющая собой поперечный усиливающий элемент. Суть способа поясняется чертежами, где:— на фиг. 1 показаны боковые узлы и их возможные варианты для разных типов кузова, передний подрамник, опора база, задний подрамник;
— Рис.2 — вариант стыковочного устройства и элементов крепления переднего подрамника и опорного основания;
— на фиг. 3 показано крепление стороны узла нижнего элемента к опорному основанию;
— Рис. 4 показывает массирование для разных типов кузова. Неснера пола 4 и спинки 5, варианта для общественного кузова или лимузина дополнительно вводим центральную перегородку 6, которая образует каркас спинки подушек передних сидений. и поперечный усиливающий элемент для открытого (без верха) кузова и лимузинов, а также содержит базовую платформу 7 крепления модификаций переднего подрамника 8 для установки различных силовых агрегатов, узлов и агрегатов механики.Перегородка 6 собрана методом вставки между центральными частями переднего пола 3. Элементы переднего подрамника 8, в свою очередь, содержат основные места 9 крепления узлов переднего крыла и закрылков, переднего бампера и освещение, электрические системы, системы управления и безопасность транспортных средств. Опорная база 1 позволяет собирать как переднеприводные, так и полноприводные варианты автомобилей в задней части пола 4, имеет базовые унифицированные крепления заднего подрамника 10 в сборе с независимой подвеской и приводами задней части. колеса, другие узлы механики и системы управления полноприводным автомобилем.Для обеспечения возможности модификации различных типов кузовов, конструкция передней части и центрального порога из частей представляет собой устройство 11 спереди и четыре направляющих устройства порога боковых частей для стыковки и позиционирования различных размеров (длина, ширина, высота) верхних. Корпус модуля 12. Участок боковых стенок 12 корпуса представляет собой пространственный каркас, содержащий правую и левую стороны соответствующих модификаций, соединенных между собой поперечными элементами 13, при этом в нижней части кросс-14 сообщения могут быть выполнены сохранить геометрию сопрягаемых деталей.Кроме того, на участке боковин может быть рамка ветрового стекла и заднего крыла. Пространственный каркас верха должен быть из экструдированных профилей в различных сечениях из легкого (алюминиевого) сплава: надомная доска стоек, соединяющая нижнюю балку 15 и поперечные элементы 13, соединенные сваркой, клеем, заклепками. Участок боковин 12 может быть разным по размеру и форме, быть однородным по размеру и крепежу с самонесущей основой соединительных элементов 16. Передний подрамник 7 является самостоятельным участком для установки силового агрегата, передней подвески и других узлов. и системы транспортного средства, на которых (подрамник) в свою очередь являются базовой унифицированной платформой 9, крепление съемных формовочных частей кузова (фи существующая подложка 1 осуществляется по направляющим 11, а стыковочная станция 20 элементов расположена по углам по периметру передней панели приборов и, наконец, по периметру сквозных отверстий в поперечных элементах 21, элементы механического крепления 22.При сборке кузова осуществляют позиционирование и крепление узлов боковин 12, подсобранных в единый узел с крышей 23 и рамой ветрового стекла, являющейся модулем верхнего отсека кузова, которые являются опорная площадка 24 крепления: петлевой стороны двери 25, задних крыльев с закрылками 26 задних колес, задней двери (задней двери) 27 и фиксированного соединения с помощью винтов или других подобных креплений через изолирующую уплотнительную прокладку 28. Крепление размещается в пороге основания переднего пола и задних колесных арок и двери багажного отделения, а также в районе передних усиливающих элементов боковых панелей передней панели приборов 2.После позиционирования и фиксации участка боковины 12 к опорному основанию 1 необходимо прикрепить молдинг (см. Выше), при этом задний бампер 29 крепится на опорном основании, накладки 7 располагаются на заднем конце опорного основания 1 на задней панели. 5. Облицовка порогов 30 смонтирована на соответствующей базовой плошай и защитного покрытия. Сборка элементов кузовных элементов: переднего подрамника, опорного основания, бокового узла. Сборка кузова осуществляется обычным способом. базовый узел кузова — опорное основание 1 смонтированы соответствующие конкретные модификации передней рамы кузова 8 и соответствующая модификация участка боковин 12, подсобранных в единый узел с крышей 23, затем на едином основании, обозначенном 7. , 9, 24 крепятся передний подрамник и крепятся боковые пластины всех других подобных модификаций формы кузова.На принимающей стороне боковины подсобирайте крылья, потолок, обшивку боковин и другие детали. Опорное основание 1 подсобираю с передней 8 и задней рамой 10, которая в свою очередь собирается с комплектующими автомобиля. На основной базе 1 монтируются трубопроводы. , проводка, воздуховоды, тепло- и шумоизоляция, сиденья передние и задние (в зависимости от конкретной модификации), панель приборов и другие детали автомобиля. Затем на опорном основании 1 монтируется и закрепляется на верхнем модуле 12. молдинг к основанию платформы передок, основание, площадка боковин.Для удобства сборки некоторых форматов Pooley расширен ассортимент кузовов на единой основе с наименьшими затратами на производственную подготовку. 1. Способ сборки кузовов автомобилей разных типов, заключающийся в предсерийных формовочных элементах для разных типов кузовов и их последующей взаимной сборке, отличающийся тем, что выполненная опорная база, общая для всего семейства автомобилей, одновременно делает узел боковой части кузова, количество которых соответствует количеству разной формы и размеров собираемого кузова, и передних подрамников, количество которых соответствует количеству модификаций различных силовых агрегатов, навесное оборудование которых унифицируется с навесным оборудованием. к опорному основанию, а крепление других формообразующих элементов корпуса будет унифицировано с их местами крепления на передней раме и сбоку корпуса через базовые площадки, сборка конкретного корпуса осуществляется путем позиционирования направляющих и соединения устройства на основе узла в поперечной и горизонтальной плоскостях, а также жестко-съемное крепление на основании соответствующих узлов боковин. На бетонный кузов и передний подрамник, после чего полученный узел закрепляют на всех остальных основаниях Formosa для сборки полноприводного автомобиля, на них дополнительно устанавливаются задние подрамники, крепление которых унифицировано с их креплением к опорной базе.3. Способ по п. 1 или 2, отличающийся тем, что при изготовлении несущих фундаментов для постройки общественного кузова или лимузина дополнительно монтируется центральная перегородка, являющаяся поперечным усиливающим элементом.
Способ сборки автомобильных кузовов и приспособление для них
УРОВЕНЬ ТЕХНИКИ
1. Область изобретения
Настоящее изобретение относится к способу сборки кузовов автомобильного транспортного средства и к приспособлению для сборки, которое будет использоваться для этого.
2. Описание предшествующего уровня техники
При сборке кузовов автомобилей на сборочной линии кузова каждая из основных панелей пола, передних кузовов транспортных средств, задних кузовов транспортных средств, содержащих задние элементы пола, боковых панелей кузова транспортного средства (состоящих из боковых внутренних панели и боковые внешние панели), панели крыши (состоящие из внутренних элементов крыши и наружных панелей крыши) и элементы крышки, такие как боковые двери, капоты и крышки багажника, обычно собираются в соответствующих линиях сборки, и они поставляются из соответствующих частей -линии сборки на конвейер кузова автомобиля.Кроме того, на этапе сборки кузова транспортного средства для сборки нижней части кузова, панель пола, передняя часть кузова транспортного средства и задняя часть кузова транспортного средства выравниваются и прикрепляются к каретке или держателю с помощью множества выравнивающих элементов и зажимных узлов. смонтированный на нем, и нижняя часть кузова собирается временно сваркой, а затем дополнительной или постоянной сваркой.
Нижняя часть кузова, загруженная на тележку или шасси, переносится на площадку для монтажа верхних секций кузова, а также боковых панелей кузова, панели крыши и т. Д.крепятся к секции под кузовом. При установке боковой панели кузова транспортного средства, панели крыши и т. Д. На нижнюю часть кузова они выравниваются с нижней частью кузова на основе базовых поверхностей их внешних панелей с помощью расположенного эксклюзивного блока выравнивания на каждой из станций они крепятся к тележке или носителю и привариваются временно, а затем дополнительно или постоянно. Затем нижняя часть кузова монтируется к верхней части кузова.Передние крылья и задние крылья крепятся к секции кузова транспортного средства на этапе монтажа верхней части кузова.
С другой стороны, выложенная японская патентная публикация (kokai) № 64–1667 раскрывает удерживающий блок для удерживания частично смонтированной секции кузова транспортного средства. Удерживающий блок состоит из основной рамы и трех пар внутренних вертикальных рам. Основная рама поддерживается горизонтально четырьмя элементами колонны, расположенными вертикально на полу фабрики и дополнительно прикрепленными к двум вертикальным колоннам, расположенным на одной стороне, с возможностью перемещения в вертикальном направлении.Три пары внутренних рам установлены на основной раме в положениях, соответствующих положению вблизи секции обтекателя кузова транспортного средства, центральной части кузова транспортного средства и задней части кузова соответственно, так что они могут открываться с возможностью перемещения. в поперечном направлении кузова автомобиля. К каждой из внутренних рам прикреплено множество зажимных устройств, инструментов и так далее. Три пары внутренних рам вставляются сверху в проем в крыше частично смонтированного корпуса кузова (выглядит так, как левая и правая боковые внутренние панели временно устанавливаются на нижнюю часть кузова) путем поворота нижней части. торцевая часть основной рамы удерживающего устройства.После этого три пары внутренних рам расширяются, чтобы приблизиться к внутренней поверхности корпуса транспортного средства, а остальные операции сборки выполняются с помощью множества зажимов, инструментов и так далее.
Традиционные методы сборки кузовов автомобилей имеют различные недостатки, поскольку элементы панели, такие как боковые панели кузова транспортного средства и т. Д., Выравниваются на основе их внешних панелей с помощью специального приспособления для выравнивания. Внешние панели настолько изогнуты и имеют сложную внешнюю форму, что погрешность формы становится такой большой из-за влияния возврата кривизны внешних панелей к их исходной форме, а жесткость внешних панелей настолько мала, что точность измерения выравнивание внешних элементов панели, вероятно, станет низким.Кроме того, элементы внешней панели различаются по форме в соответствии с моделями, так что специальные инструменты для выравнивания должны быть подготовлены для каждой из моделей автомобильных транспортных средств. Кроме того, выравнивающие приспособления множества видов должны быть готовы к немедленному использованию на каждой станции, а выравнивающие приспособления должны быть закреплены и отсоединены от секции кузова транспортного средства несколько раз во время монтажа, чтобы эффективность работы могла снизиться. С другой стороны, поскольку основная панель пола монтируется к верхней части кузова на начальном этапе традиционной сборочной линии кузова, крупногабаритное и многофункциональное монтажное приспособление для монтажа секций кузова транспортного средства не может быть размещено. внутри секции кузова транспортного средства и операции по установке различных деталей, узлов и аксессуаров, таких как сиденья, могут стать очень трудными.Кроме того, возникают проблемы, связанные с тем, что внутренние элементы должны быть снабжены рядом сварочных отверстий для сварки соединений боковых внутренних панелей, таких как сборные боковые панели кузова транспортного средства и внутренние панели крыши, что обеспечивает эффективность при сварке внутренних элементы могут стать меньше, а также что количество станций для операций по сварке и соединению станет больше и что длина станций станет больше, потому что сварочные роботы и т. д. расположены вне секций кузова транспортного средства, которые устанавливаются и, как следствие, потому что секции кузова автомобиля подвергаются сварке только снаружи.
На сборочной линии кузова транспортного средства с использованием удерживающего устройства, как описано в выложенной японской патентной публикации (kokai) № 64–1667, удерживающее устройство применяется, по крайней мере, к нижней части кузова, которая временно устанавливается на боковая внутренняя панель. Следовательно, этап необходим для временного крепления нижних секций кузова к боковым внутренним панелям. Кроме того, кронштейны, стойки, болты и так далее требуются для временного крепления секций под кузовом транспортного средства к боковым внутренним панелям, так что конструкции панельных элементов могут стать сложными.Кроме того, три внутренние рамы удерживающего устройства вставляются в корпус транспортного средства через сравнительно небольшую секцию проема в крыше, так что его внутренняя рама не может быть увеличена по размеру и многофункциональна, что делает операции трудоемкими и менее эффективными. .
КРАТКОЕ ОПИСАНИЕ ИЗОБРЕТЕНИЯ
Целью настоящего изобретения является создание способа сборки кузовов автомобилей и приспособления для этого, которое может повысить точность выравнивания кузовов автомобилей при установке, по меньшей мере, от боковых панелей кузова транспортного средства до панелей крыши, которые могут упростить структуру элементов для структурирования кузовов транспортных средств, которые в целом лучше подходят для различных моделей кузовов транспортных средств, что может повысить эффективность операций по установке и которые могут повысить эффективность монтажа деталей, узлов и аксессуаров к основным панелям пола.
Для достижения вышеупомянутой цели настоящее изобретение состоит из способа сборки кузова автомобильного транспортного средства, содержащего:
— первый этап установки боковой панели кузова транспортного средства и панели крыши на зажимное приспособление, имеющее первый удерживающий механизм для удержания боковой панели кузова транспортного средства после того, как боковая панель кузова транспортного средства выровнена с зажимным устройством на основе внутренней панели боковой панели кузова транспортного средства, и второй удерживающий механизм для удерживания панели крыши после панели крыши совмещен с кондуктором на основании внутренней панели кровельной панели;
— второй этап соединения боковой панели кузова транспортного средства, установленной на зажимном блоке, с панелью крыши для образования сборки кузова транспортного средства; и
— третий этап вакуумирования зажимного устройства относительно вниз от кузова транспортного средства.
Метод сборки автомобильного транспортного средства может иметь следующие преимущества, поскольку левая и правая боковые панели кузова транспортного средства и панель крыши выровнены на основе боковых внутренних панелей, а также передней панели. коллектор и задний коллектор, составляющие внутренние элементы кровельной панели. Эти внутренние элементы имеют более точную форму, чем их внешние панели, так что боковые панели кузова транспортного средства и панель крыши могут быть установлены через соответствующие внутренние элементы с высокой точностью.Кроме того, поскольку при временной установке этих элементов панели не требуется устанавливать ни кронштейны, ни распорки, ни болты, конструкция элементов панели может быть сделана менее сложной, и этап временной установки секции кузова транспортного средства может быть опущен. Кроме того, этот метод превосходит обобщение и экономичность, потому что общий зажимной блок может быть применен к элементам панели различных и различных моделей автомобилей из-за относительного сходства боковых внутренних панелей и внутренних элементов крыши по форме и конструкции друг к другу, даже если модели автомобилей различаются, и из-за сравнительно большого количества открывающихся частей, которые могут удерживаться удерживающим механизмом.Кроме того, поскольку приспособление для крепления может быть выполнено с возможностью вакуумирования на третьем этапе из сборки кузова транспортного средства, полученной путем сборки боковых панелей кузова транспортного средства с панелями крыши, приспособление для крепления может быть выполнено большего размера и многофункционального, так что монтажные операции можно сделать высокоэффективными.
Другой аспект настоящего изобретения состоит в способе сборки кузова автомобильного транспортного средства на сборочной линии кузова транспортного средства для монтажа по меньшей мере левой и правой боковых панелей кузова транспортного средства на панели крыши, в котором боковая внутренняя панель каждой из левой и правой боковых панелей кузова подобрана с их боковой внешней панелью для образования подузла боковой панели, внутренний элемент крыши панели крыши подобрана с его внешняя панель крыши для образования подузла панели крыши, подузел боковой панели и подузел панели крыши поставляются отдельно на соединительную станцию, в которой подузел боковой панели соединен с подузлом панели крыши, и подузел боковой панели соединен с подузлом панели крыши на соединительной станции, которая включает:
— первый этап для соединения левой и правой внутренних боковых панелей кузова автомобиля с панелью крыши путем совмещения левая рука и правые внутренние боковые панели кузова автомобиля и панель крыши, подаваемые на соединительную станцию, фиксация левой и правой внутренних боковых панелей кузова автомобиля и выравнивание панели крыши, сварка левого и правого кузова автомобиля боковые внутренние панели к панели крыши временно, а затем дополнительно или навсегда; и
— второй этап для соединения левой и правой боковых панелей кузова транспортного средства с панелью крыши путем подачи левой и правой боковых наружных панелей и внешней панели крыши к соединительной станции, выравнивая левая и правая боковые внешние панели кузова транспортного средства с соответствующими боковыми внутренними панелями, выравнивание внешней панели крыши с внутренним элементом крыши и временное приваривание левой и правой боковых боковых панелей кузова транспортного средства к панели крыши а затем дополнительно или навсегда.
В соответствии с другим аспектом настоящего изобретения левая и правая боковые внутренние панели соединяются с внутренними элементами крыши на первом этапе путем их совмещения, фиксации и сварки временно, а затем дополнительно или навсегда. Точное выравнивание может быть реализовано на основе боковой внутренней панели или внутреннего элемента крыши, который представляет собой элемент, который имеет относительно простую форму, высокую жесткость и меньшую погрешность формы из-за возврата к своей исходной форме из его изогнутая форма.Кроме того, сварочные операции могут быть выполнены с высокой эффективностью в таком состоянии, что никакое выравнивание не выполняется на основе внешней панели, в отличие от традиционных процедур. Кроме того, поскольку не требуется делать сварных отверстий для боковых внутренних панелей и внутреннего элемента крыши, и не требуется устанавливать ни кронштейны, ни распорки, ни болты для временного монтажа на боковых внутренних панелях и внутреннем элементе крыши, конструкция боковых внутренних панелей и внутренних элементов крыши может быть упрощена.
Далее, на втором этапе, левая и правая боковые внешние панели соединяются с внешней панелью крыши путем совмещения левой и правой сторон с соответствующими боковыми внутренними панелями, с одной стороны, и внешнюю панель крыши с внутренним элементом крыши, с другой стороны, и сваривая их временно, а затем дополнительно или постоянно, так что внешние панели могут быть точно выровнены с боковыми внутренними панелями и внутренними элементами крыши, которые выровнены и могут быть связаны с высокой точностью.Следовательно, кузова автомобилей можно собирать с высокой точностью.
В предпочтительном варианте настоящего изобретения левая и правая боковые внешние панели дополнительно или постоянно привариваются к внешней панели крыши на втором этапе с помощью средств сварки, расположенных внутри и снаружи секции кузова транспортного средства в второй этап, так что сварочные операции могут выполняться с повышенной эффективностью, а количество станций для дополнительной или постоянной сварки может быть уменьшено, тем самым сокращая сборочную линию кузова транспортного средства.
В более предпочтительном варианте настоящего изобретения левая и правая боковые внешние панели временно привариваются к внешней панели крыши с помощью сварочных средств, расположенных внутри секции кузова на втором этапе, а затем дополнительно или постоянно с помощью сварочного робота, расположенного вне секции кузова транспортного средства на станции, где должна выполняться дополнительная или постоянная сварка. Такая компоновка для сварочных операций может повысить эффективность временных сварочных операций и обобщить сборку кузовов транспортных средств различных моделей и типов.Кроме того, поскольку дополнительные или постоянные сварочные операции выполняются с помощью сварочного робота, расположенного вне секции кузова транспортного средства, обобщение может быть улучшено при сборке кузовов транспортных средств различных моделей и типов.
С другой стороны, зажимное приспособление согласно настоящему изобретению для сборки кузовов автомобилей характеризуется:
первым удерживающим механизмом, расположенным внутри боковых панелей кузова транспортного средства для удерживания боковых панелей кузова транспортного средства, выровненных на основе боковые внутренние панели соответствующих боковых панелей; и
— второй удерживающий механизм, расположенный внутри панели крыши, для удерживания панели крыши, выровненной на основании внутреннего элемента крыши панели крыши;
, в котором первый удерживающий механизм выполнен с возможностью перемещения между первым положением, в котором удерживаются боковые панели, и вторым положением, в котором первый удерживающий механизм откачивается из боковых панелей; и
, в котором второй удерживающий механизм выполнен с возможностью перемещения между первым положением, в котором удерживается панель крыши, и вторым положением, в котором второй удерживающий механизм откачивается из панели крыши.
В соответствии с настоящим изобретением, относящимся к блоку зажимного приспособления, как описано выше, блок зажимного приспособления может выравнивать левую и правую боковые панели кузова транспортного средства на основе их соответствующих боковых внутренних панелей, которые имеют сравнительно простую форму, высокая жесткость и небольшая погрешность формы из-за возврата к исходной форме из изогнутой формы, и он может фиксировать их на зажимном устройстве. Аналогичным образом, кондуктор может выровнять панель крыши на основе ее внутреннего элемента крыши, который имеет сравнительно простую форму, высокую жесткость и небольшую погрешность формы из-за возврата к исходной форме из ее изогнутой формы, и он может прикрепить панель крыши к кондуктору.Такое расположение позволяет выровнять левую и правую боковые панели кузова транспортного средства и панель крыши с высокой точностью и прикрепить к панели крыши.
Кроме того, поскольку левая и правая боковые панели кузова транспортного средства, а также панель крыши поставляются в блок кондуктора и затем монтируются к нему, для временного монтажа этих элементов панели не требуются ни кронштейны, ни распорки, ни болты. так что конструкция элементов панели может быть простой и что этап временной установки для временной установки части кузова транспортного средства может быть опущен.Кроме того, зажимное приспособление согласно настоящему изобретению превосходит в обобщении, потому что оно может быть применено к элементам панели для различных моделей автомобильных транспортных средств по существу одинаковым образом из-за схожести формы и конструкции, а также расположения большого количество отверстий, удерживаемых удерживающим механизмом.
Кроме того, поскольку первый и второй удерживающие механизмы могут перемещаться между первым и вторым положениями, зажимное приспособление может быть эвакуировано из секции кузова транспортного средства путем перемещения зажимного приспособления вниз относительно секции кузова транспортного средства и от него после кузова транспортного средства. раздел собран.Следовательно, зажимное приспособление может быть выполнено настолько большим по размеру и таким многофункциональным, что операции по установке могут быть облегчены с высокой эффективностью.
Другие цели, особенности и преимущества настоящего изобретения станут очевидными в ходе последующего описания предпочтительных вариантов осуществления со ссылкой на прилагаемые чертежи.
КРАТКОЕ ОПИСАНИЕ ЧЕРТЕЖЕЙ
ФИГ. С 1 по 14 относятся к первому варианту осуществления согласно настоящему изобретению; в котором:
РИС.1 представляет собой блок-схему, показывающую схему линии сборки кузова транспортного средства, на которой применяется способ сборки согласно настоящему изобретению;
РИС. 2 — вид в перспективе, показывающий приспособление для зажима, которое будет использоваться для способа сборки согласно настоящему изобретению;
РИС. 3 — вид сверху, показывающий блок зажима, показанный на фиг. 2;
РИС. 4 — вид сбоку, показывающий блок зажима по фиг. 2;
РИС. 5 — вид спереди, показывающий центральную часть зажимного устройства по фиг.2;
РИС. 6 — схематическое изображение, показывающее удерживающий механизм, расположенный в зажимном блоке, для удерживания передней концевой части боковой внутренней панели;
РИС. 7 — увеличенное схематическое изображение, показывающее станции с первой по четвертую на линии сборки кузова транспортного средства;
РИС. 8 — увеличенное схематическое изображение, показывающее станции с пятой по восьмую на сборочной линии кузова транспортного средства;
РИС. 9 — схематическое изображение, показывающее в основном передающую станцию;
РИС.10 — вид сбоку, показывающий конвейерный блок для подачи боковых внутренних панелей на вторую станцию S2 на сборочной линии кузова транспортного средства;
РИС. 11 — вид в перспективе, показывающий робот для установки боковых дверей и соединительное устройство для соединения боковых дверей, каждая из которых расположена на восьмой станции S8;
РИС. 12 — вид спереди, показывающий подъемно-опускающее устройство, расположенное на девятой станции S9;
РИС. 13 — вид спереди, показывающий ступеньку для соединения секции кузова транспортного средства с основной панелью пола; и
ФИГ.14 — вид сбоку, показывающий ступеньку по фиг. 13.
РИС. 15 — вид сбоку, показывающий часть зажимного устройства второго варианта осуществления настоящего изобретения и показывающий выравнивающий механизм для выравнивания передней концевой части боковой внутренней панели.
РИС. 16 — схематическое изображение, показывающее существенную часть линии сборки кузова транспортного средства для сборки секции кузова транспортного средства согласно третьему варианту осуществления настоящего изобретения.
РИС. 17-21 относятся к четвертому варианту осуществления настоящего изобретения; в котором:
РИС.17 — вид в перспективе, показывающий зажимной блок;
РИС. 18 — вид сверху, показывающий блок зажима по фиг. 17;
РИС. 19 — вид сбоку, показывающий блок зажима по фиг. 17;
РИС. 20 — вид в перспективе, показывающий блок регулировки положения для боковых дверей, расположенный в блоке кондуктора; и
ФИГ. 21 — схематическое изображение, показывающее существенную часть линии сборки кузова транспортного средства.
РИС. 22 направлен на пятый вариант осуществления настоящего изобретения, который показывает блок регулировки положения для боковых дверей, расположенный в блоке кондуктора.
РИС. 23-27 относятся к шестому варианту осуществления настоящего изобретения, в котором:
Фиг. 23 — вид в перспективе, показывающий зажимное приспособление шестого варианта осуществления;
РИС. 24 — вид сверху, показывающий блок зажима по фиг. 23;
РИС. 25 — вид сбоку, показывающий блок зажима по фиг. 23;
РИС. 26 — вид сверху, показывающий центральную часть зажимного устройства по фиг. 23; и
ФИГ. 27 — вид сбоку, показывающий сварочный блок, расположенный в зажимном блоке.
РИС. 28-34 относятся к седьмому варианту осуществления настоящего изобретения; в котором:
РИС. 28 — схематическое изображение в перспективе, показывающее контур линии сборки кузовов транспортного средства для сборки кузовов транспортных средств.
РИС. 29 — увеличенное схематическое изображение в перспективе, показывающее станции S1-S3 сборочной линии кузова транспортного средства для сборки кузовов транспортного средства.
РИС. 30 — увеличенное схематическое изображение в перспективе, показывающее станции S4-S6 линии сборки кузова транспортного средства;
РИС.31 — увеличенное схематическое изображение в перспективе, показывающее станции S7 и S8 сборочной линии кузова транспортного средства;
РИС. 32 — вид спереди, показывающий подъемно-спусковой блок, не используемый в пятой станции S5;
РИС. 33 — вид в перспективе, показывающий поддон, расположенный на шестой станции S6, и внешний сварочный робот, расположенный вне секции кузова транспортного средства; и
ФИГ. 34 — вид в перспективе, показывающий сварочного робота, установленного на седьмой станции.
ОПИСАНИЕ ПРЕДПОЧТИТЕЛЬНЫХ ВАРИАНТОВ ОСУЩЕСТВЛЕНИЯ
Настоящее изобретение будет описано более подробно со ссылкой на прилагаемые чертежи.
ПЕРВЫЙ ВАРИАНТ ОСУЩЕСТВЛЕНИЯ
РИС. 1 показывает схему сборочной линии BL кузова транспортного средства для сборки секций верхней части кузова, составляющих часть кузова транспортного средства.
Подробное описание будет дано сборочной линии BL кузова транспортного средства со ссылкой на фиг. 1.
Как показано на фиг. 1, сборочная линия BL транспортного средства содержит девять станций от S1 до S9 включительно, состоящих из первой станции S1, второй станции S2, третьей станции S3, четвертой станции S4, пятой станции S5, от верхнего до нижнего уровня, шестую станцию S6, седьмую станцию S7, восьмую станцию S8 и девятую станцию S9.К станциям с S1 по S9 подаются зажимные приспособления JU с помощью транспортирующих устройств, устройств или систем (не показаны), которые обычно относятся к линейному, лифтовому или несущему типу. На каждой из станций с S1 по S9 каждый из элементов для структурирования кузова транспортного средства выровнен с соответствующим блоком Jig Jig, используя его внутреннюю панель в качестве эталона или на основе своей внутренней панели, и элементы для структурирования кузова транспортного средства. секции устанавливаются одна за другой к соответствующим зажимным узлам JU и соединяются одна за другой, образуя таким образом секцию кузова (верхнюю секцию кузова) 1.
Сначала описывается зажимной блок JU со ссылкой на фиг. 2-5.
Приспособление JU обычно включает поддон P, передний зажимной механизм кузова транспортного средства для выравнивания и зажима передней части 2 кузова, зажимной механизм заднего элемента пола для выравнивания и зажима заднего элемента 5 в сборе пола, пара механизмов зажима левой и правой боковых панелей, соответственно, для выравнивания и зажима левой и правой внутренних боковых панелей 3, зажимной механизм блока передней панели капота для выравнивания и зажима блока крышки передней панели 6, механизмы зажима переднего и заднего жаток, соответственно, для выравнивания и зажима переднего жатки 7a и заднего жатки 7b, и зажимного механизма лотка для пакетов для совмещения и зажима узла 8 заднего лотка для пакетов.
Зажимной механизм переднего кузова для выравнивания и зажима передней части 2 кузова автомобиля содержит центрирующий штифт 31 и зажимной блок C1, каждый из которых установлен на каждой из двух пар левого и правого опорных кронштейнов 30, расположенных на расстоянии друг от друга на заданном расстоянии в передней части поддона P кондуктора JU. Передние концевые части левой и правой передней рам передней части 2 кузова транспортного средства, а также обе концевые части его второй поперечины выровнены с поддоном P с помощью четырех центрирующих штифтов 31, а передняя часть 2 кузова закреплена на поддоне Р с помощью четырех зажимных узлов С1.
Зажимной механизм заднего пола в сборе для выравнивания и зажима заднего элемента 5 в сборе состоит из центрирующего штифта 33 и зажимного блока C2, каждый из которых установлен на каждой из двух пар левого и правого опорных кронштейнов 32, расположенных на расстоянии на заданном расстоянии друг от друга в задней части поддона P зажимного устройства JU. Передняя и задняя концевые части левой и правой задней рамок заднего элемента 5 в сборе пола выровнены с поддоном P с помощью четырех центрирующих штифтов 33, а задний элемент 5 в сборе пола закреплен на поддон P с помощью четырех зажимных устройств C2.
Как было кратко описано выше, механизмы зажима левой и правой боковых панелей должны выравнивать левую и правую боковые внутренние панели 3 с поддоном P, и они расположены слева и справа. правые стороны почти центральной части поддона P соответственно. Будет дано подробное описание зажимного механизма левой боковой панели, поскольку зажимные механизмы левой и правой боковых панелей расположены симметрично и имеют одинаковую конструкцию.
Зажимной механизм левой боковой панели обычно содержит центрирующие блоки P1, P2 и P3, а также зажимные блоки от C3 до C7 включительно для выравнивания и зажима левой внутренней панели 3 соответственно.
На левой стороне почти продольной центральной части поддона P расположено крепежное основание 34, на котором, в свою очередь, расположена опорная пластина 35. Опорная пластина 35 расположена с возможностью перемещения в поперечном направлении кузова автомобиля.
К опорной плите 35 прикреплена почти лежащая F-образная опорная рама 36. Зажимной блок C3 расположен на верхних концевых частях пары вертикальных колонн 36a, расположенных перед опорной рамой 36 и позади нее. Зажимной блок C3 является расположена так, чтобы зажимать внутренний рельс крыши, расположенный наверху боковой внутренней панели 3.
Опорная плита 35 снабжена выравнивающим блоком P1 и зажимным блоком C4. Выравнивающий блок P1 предназначен для выравнивания продольной центральной части центральной внутренней стойки 10 боковой внутренней панели 3, а зажимной блок C4 зажимает продольную центральную часть своей центральной внутренней стойки 10.
На задней оконечной части горизонтального элемента 36b лежащей F-образной опорной рамы 36 смонтированы выравнивающий блок P2 и зажимной блок C5. Выравнивающий блок P2 выполнен с возможностью выравнивания нижней концевой части внутренней задней стойки 11 боковой внутренней панели 3, а зажимной блок C5 выполнен с возможностью зажимать нижнюю концевую часть ее внутренней задней стойки 11.
Кроме того, опорное основание 37 расположено на поддоне Р перед крепежным основанием 34. На опорном основании 37 поддерживается подвижная пластина 38 с возможностью перемещения в продольном направлении кузова транспортного средства.Кроме того, опорная пластина 39 поддерживается на подвижной пластине 38 с возможностью перемещения в ее поперечном направлении. На опорной плите 39 установлена вертикальная колонна 40, и почти квадратная опорная рама 41 С-образной формы расположена наверху вертикальной стойки 40. Узел выравнивания P3 и узел зажима C6 установлены в верхней части стойки. в целом квадратная опорная рама 41 С-образной формы.
Выравнивающий блок P3 расположен так, чтобы выровнять нижнюю концевую часть передней внутренней стойки 12 боковой внутренней панели 3, а зажимной блок C6 выполнен с возможностью зажима внутренней передней части столб 12 оного.С другой стороны, зажимной блок C7 установлен на нижней части опорной рамы 41 для зажима нижней части передней концевой части боковой внутренней панели 3.
Как описано выше, боковые внутренние панели 3 выровнены. с помощью центровочных узлов P1 – P3 и зажимается зажимными узлами C3 – C7.
Зажимной механизм капот-передняя панель предназначен для выравнивания и зажима узла 6 капот-передняя панель. Зажимной механизм капот-передняя панель состоит из установочного штифта 42 и зажимного узла C8, которые расположены на верхних частях корпуса. левая и правая опорные рамы 41.Центрирующий штифт 42 и зажимное устройство C8 поддерживаются цилиндром 57 (фиг. 5) с возможностью перемещения в вертикальном направлении. Задний конец узла 6 капота и передней панели, состоящего из панели 13 капота и нижней приборной панели 14, выровнен с помощью центрирующего штифта 42, а затем узел 6 капот-передняя панель зажимается зажимом. блок зажима C8.
Кроме того, зажимной механизм жатки содержит выравнивающий блок P4a и зажимной блок C9a, каждый из которых установлен на каждой из секций 44a рычага, расположенных спереди опорной рамы 44, которая, в свою очередь, расположена между верхними концевыми частями передние и задние вертикальные стойки 43, расположенные между левым и правым крепежными основаниями 34 поддона Р.Выравнивающий блок P4a расположен так, чтобы выровнять концевую часть переднего коллектора 7a снизу, и передний заголовок 7a затем зажимается зажимным блоком C9a.
Опорная рама 44 имеет пару левых и правых секций 44b с двумя ответвлениями, расположенных на ее заднем конце, а выравнивающий блок P4b и зажимной блок C9b установлены на задней оконечной части каждого из левый и правый двухветвевые секции 44b. Выравнивающий блок P4b выполнен с возможностью совмещения концевой части заднего жатки 7b с поддоном P снизу, а зажимной блок C9b выполнен с возможностью зажима заднего жатки 7b.
Другими словами, передний подборщик 7a выравнивается с поддоном P с помощью пары выравнивающих узлов P4a, а затем зажимается с помощью пары зажимных узлов C9a, а задний подборщик 7b выравнивается с поддоном P с помощью пары центровочных узлов P4b, а затем зажимается с помощью пары зажимных узлов C9b. После зажатия переднего и заднего жаток 7а и 7b их прикрепляют к зажимным узлам.
Кроме того, выравнивающий блок P5 и зажимной блок C10 установлены на концевой части каждой из левой и правой секций 44c рычага, расположенных в центральной части опорной рамы 44.Узел P5 выравнивания выполнен с возможностью выравнивания концевой части дуги 7c крыши, собранной с внешней панелью 7B крыши, а узел C10 зажима предназначен для зажима дуги 7c крыши.
Зажимные узлы от C1 до C10, включительно, представляют собой обычные коленчатые рычаги, и каждый из них содержит зажимной рычаг 45 почти кривошипно-шатунной формы и воздушный цилиндр 46 для приведения в действие поворотного движения зажимного рычага 45, как показано на ИНЖИР. 6.
Центрирующие узлы от P1 до P5 включительно имеют общую конфигурацию, имеющую центрирующий штифт 47 и воздушный цилиндр 48 для приведения в движение вперед и назад центрирующего штифта 47.
Здесь отмечается, что, как показано на фиг. 6, зажимные устройства C6 и C7 для зажимного механизма боковой панели расположены таким образом, чтобы зажимать боковую внутреннюю панель 3, вставляя соответствующие зажимные рычаги 45 через открывающуюся секцию 3a, образованную в боковой внутренней панели 3.
Лоток для пакетов Узел зажимного механизма имеет опорную пластину 50, расположенную на задней верхней поверхности каждого из левого и правого крепежных оснований 34. На опорной пластине 50 поддерживается опорный элемент 51 с возможностью перемещения в продольном направлении кузов автомобиля.На задней стороне опорного элемента 51 поддерживается подвижная пластина 53, имеющая пару левых и правых опорных кронштейнов 52, каждый из которых проходит назад, чтобы иметь возможность перемещаться по вертикали. Подвижная пластина 53 поднимается или опускается с помощью цилиндра 54.
На опорном кронштейне 52 расположены четыре установочных штифта 55 для выравнивания узла 8 заднего лотка для пакетов и пара левого и правого зажимных устройств C11 для зажима. узел заднего лотка для пакетов 8.
Зажимные узлы C3 — C5 и выравнивающие узлы P1 и P2 крепятся к зажимному узлу JU через опорную раму 36, а прижимные узлы C6 — C8, выравнивающие узлы P3 и выравнивающие штифт 42 крепится к зажимному устройству JU через вертикальные стойки 40, подвижную пластину 38 и опорную пластину 39.Кроме того, зажимные элементы C11 и центрирующий штифт 55 устанавливаются на зажимном устройстве JU через опорный элемент 51 и подвижную пластину 53.
Как показано на фиг. 3, выравнивающие узлы и зажимные узлы перемещаются приводным механизмом (не показан) в положение установки, как показано сплошной линией на фиг. 3, когда элементы для структурирования кузовов транспортных средств установлены на сборочном узле JU. С другой стороны, выравнивающие узлы и зажимные узлы переводятся в положение вакуумирования, как показано пунктирной линией на фиг.3, чтобы обеспечить эвакуацию зажимного приспособления JU из секции 1a отверстия в полу (фиг. 5), не вызывая столкновения зажимного приспособления JU с верхней секцией 1 кузова транспортного средства, после того как верхняя секция 1 кузова будет собрана .
Затем будет приведено описание элементов конструкции кузова транспортного средства, которые должны быть подведены к белой линии BL кузова транспортного средства со ссылкой на фиг. 1.
Передняя часть кузова 2 включает в себя левую и правую переднюю раму, левый и правый подкрылки колес, нижнюю панель приборов, нижнюю часть передней панели (вторая поперечина) и т. Д. на, и передняя часть 2 кузова собирается на первой вспомогательной сборочной линии SL1.Здесь следует отметить, что панель кожуха, составляющая передний конец верхней части 1 кузова транспортного средства, соединяется с верхней частью 1 кузова транспортного средства после того, как верхняя часть кузова была собрана с нижней частью кузова транспортного средства и двигателем внутреннего сгорания. был загружен на кузов 1 транспортного средства или на него.
Задний элемент 5 пола в сборе включает панель заднего пола, левую и правую заднюю раму, четвертую поперечину, заднюю поперечину, пол багажника. и заднюю торцевую панель, и узел 5 заднего пола собирают на первой вспомогательной сборочной линии SL1.
Каждая из левой и правой внутренних панелей 3 содержит корпус внутренней панели, внутренний рельс крыши, противоударный кронштейн, колесную арку, элементы усиления подвески и так далее. Левая и правая боковые внутренние панели 3 собираются на второй линии SL2 сборки.
Передний коллектор 7a и задний коллектор 7b, служащие внутренними элементами крыши панели крыши, содержат, каждая, внутреннюю панель заголовка и внешнюю панель заголовка, и они собираются на третьей линии SL3 вспомогательной сборки.
Каждая из левой и правой боковых внешних панелей 4 содержит корпус внешней панели, усиливающий элемент переднего шарнира, усиливающий элемент заднего шарнира, усиливающий элемент центральной стойки, усиливающий элемент заднего фиксатора, угловую пластину и скоро. Боковая внешняя панель 4 собирается на четвертой вспомогательной сборочной линии SL4.
Наружная панель 7B крыши содержит корпус внешней панели и ветвь 7c крыши, а узел 8 заднего лотка для пакетов содержит лоток для пакетов, кронштейн и так далее.Кроме того, узел 6 обтекателя и передней панели содержит панель обтекателя и приборную панель. Эти элементы собираются на пятой вспомогательной сборочной линии SLS.
Капот и крышка багажника, служащие элементами крышки, собираются на вспомогательной сборочной линии (не показана). Каждая из четырех боковых дверей 15 содержит внутреннюю панель двери, внешнюю панель двери, створку, панель оконного стекла, стеклоподъемник и так далее, и они собираются на шестой вспомогательной сборочной линии SL6.
Теперь описываются процедуры сборки верхней части 1 кузова транспортного средства белой части кузова транспортного средства со ссылкой на фиг.1 и 7-12. Операции по сборке верхней части кузова на каждой из станций S1-S9 описаны в порядке от входа к выходу. На фиг. 1, зажимное приспособление JU исключено из иллюстрации, и станции S2-S7 соответствуют множеству соединительных станций.
ПЕРВАЯ СТАНЦИЯ S1
На первой станции S1, как показано на фиг. На фиг.7 блок JU зажимного приспособления, перемещаемый со станции ST зажимного приспособления, позиционируется и совмещается. Передняя часть 2 кузова транспортного средства и задний элемент 5 в сборе пола совмещены с зажимным устройством JU и затем зажаты.Передняя секция 2 кузова транспортного средства и задний элемент 5 в сборе пола поставляются с первой вспомогательной сборочной линии SL1.
Как показано на фиг. 2, передняя часть 2 кузова выровнена с зажимным устройством JU с помощью четырех центрирующих штифтов 31 с высокой точностью, а затем зажата четырьмя зажимными блоками C1 зажимного устройства JU. Кроме того, задний элемент 5 в сборе пола совмещается с зажимным устройством JU с помощью четырех центрирующих штифтов 33 с высокой точностью, а затем зажимается четырьмя зажимными блоками C2 зажимного блока JU.
ВТОРАЯ СТАНЦИЯ S2
На второй станции S2, как показано на фиг. 7, зажимное приспособление JU, транспортируемое с первой станции S1, выровнено. Левая и правая внутренние панели 3 подаются со второй сборочной линии SL2 на вторую станцию S2 и затем выравниваются по фиг. блок JU с высокой точностью с помощью центровочных блоков от P1 до P3 включительно. После этого они зажимаются зажимными узлами C3. до C7 включительно.
Теперь будет дано краткое описание конвейерной системы 60 для транспортировки левой и правой внутренних панелей 3 на вторую станцию S2 от первой станции S1.
Как показано на фиг. 10, направляющая (не показана) предусмотрена в области, расположенной над нижним по потоку концевым участком второй сборочной линии SL2, и в области, расположенной над второй станцией S2. К направляющей прикреплены левая и правая вертикальные рамы 61, выступающие вниз и расположенные с возможностью перемещения. Каждая из стоек 61 поддерживает рычаг 62 в консольном состоянии с возможностью перемещения в вертикальном направлении, а рычаг 62 поднимается или опускается с помощью механизма для подъема или опускания рычага 62, хотя не показано, расположенный на верхнем конце вертикальной рамы 61.
На боковой поверхности каждого рычага 62 установлена горизонтально идущая направляющая 63, которая, в свою очередь, поддерживает опорную пластину 64, которая приводится в действие цилиндром 65, чтобы иметь возможность перемещения в левом и правом направлениях. , как показано на рисунке. К опорной пластине 64 расположен цилиндр 66, проходящий в вертикальном направлении, и подвижная пластина 67 установлена на нижней концевой части поршневого штока 66а цилиндра 66. К подвижной пластине 67 с возможностью поворота прикреплен поддерживающий рычаг 68, так что расположен так, чтобы быть вставленным в секцию дверного проема каждой из боковых внутренних панелей 3, и рычаг 69, расположенный с возможностью поворота для предотвращения качания боковой внутренней панели 3.Боковая внутренняя панель 3 поддерживается подвижной пластиной 67 через поддерживающий рычаг 68, и она транспортируется от первой станции S1 ко второй станции S2, при этом боковая внутренняя панель 3 удерживается на рычаге 69, не заставляя боковую внутреннюю панель 3 соскальзывать. раскачивается во время транспортировки.
ТРЕТЬЯ СТАНЦИЯ S3
Как показано на РИС. Как показано на фиг.7, передний жаток 7a и задний жаток 7b подаются с третьей сборочной линии SL3 на третью станцию S3 и устанавливаются на уже выровненном зажимном блоке JU.
Как конкретно показано на фиг. 4, передняя жатка 7a и задняя жатка 7b выравниваются с помощью центровочных блоков P4a и P4b, а затем зажимаются зажимными блоками C9a и C9b, соответственно, с высокой точностью, с последующей временной сваркой обоих боковых концевых частей каждый из переднего коллектора 7a и заднего коллектора 7b к левой и правой боковым внутренним панелям 3 с помощью двух сварочных роботов 70, расположенных на третьей станции S3. Кроме того, каждая из торцевых сторон боковой внутренней панели 3 временно приваривается к левой и правой боковым внутренним панелям 3 соответственно, а боковые внутренние панели 3, в свою очередь, временно привариваются к заднему элементу 5 узла пола. .
ЧЕТВЕРТАЯ СТАНЦИЯ
На четвертой станции S4, как показано на фиг. 7, левая и правая боковые внутренние панели 3 дополнительно или постоянно приварены к передней части 2 кузова транспортного средства и заднему элементу 5 в сборе пола с помощью еще двух сварочных роботов 71. Кроме того, передний коллектор 7a и задний коллектор 7b соединен с левой и правой боковыми внутренними панелями 3.
ПЯТАЯ СТАНЦИЯ S5
Как показано на фиг. 8, левая и правая боковые внешние панели 4 подаются с четвертой вспомогательной сборочной линии SL4 на пятую станцию S5, а также выровнены и прикреплены к левой и правой боковым внутренним панелям 3, закрепленным к фиг.Unit JU.
ШЕСТАЯ СТАНЦИЯ
На шестой станции S6, как показано на фиг. 8, внешняя панель 7B крыши, узел 6 кожуха-передней панели и узел 8 заднего поддона для пакетов поставляются с пятой вспомогательной сборочной линии SL5 и устанавливаются на сборочный узел JU.
Как показано на фиг. 3, внешняя панель 7B крыши совмещается с зажимным устройством JU с помощью центровочных блоков P5 с высокой точностью, а затем зажимается на зажимном блоке JU с помощью зажимных блоков C10. Кроме того, узел 6 сборки обтекателя и приборной панели совмещается с зажимным устройством JU с помощью центрирующего штифта 42 с высокой точностью, а затем закрепляется на зажимном блоке JU с помощью зажимных узлов C8.Кроме того, узел 8 заднего лотка для пакетов совмещается с зажимным устройством JU с помощью центрирующих штифтов 55 с высокой точностью, а затем зажимается с помощью зажимного устройства JU с помощью зажимных узлов C11.
После этого боковая внешняя панель 4 временно приваривается к боковой внутренней панели 3 с помощью двух сварочных роботов 73. Аналогичным образом узел 6 кожух-передняя панель временно приваривается к боковой внутренней панели 3 и передней панели. секция 2 кузова транспортного средства. Кроме того, внешняя панель 7B крыши временно приваривается к переднему и заднему коллекторам 7a и 7b, а также к боковой наружной панели 4.Кроме того, узел 8 заднего лотка для пакетов временно приварен к боковой внутренней панели 3 и к заднему элементу 5 пола.
СЕДЬМАЯ СТАНЦИЯ S7
На седьмой станции S7, как показано на фиг. 8, элементы конструкции кузова транспортного средства, временно приваренные на шестой станции S6 и переданные оттуда к седьмой станции S7, дополнительно или постоянно привариваются с помощью двух сварочных роботов 74.
ВОСЬМАЯ СТАНЦИЯ S8
На восьмой станции S8, как показано на фиг.8 и 11, передние и задние боковые двери 15 поставляются одна за другой с шестой вспомогательной сборочной линии SL6 с помощью левого и правого роботов 75. Боковые двери 15 временно крепятся к соответствующим боковым наружным панелям. 4 путем соединения пары верхних и нижних шарнирных элементов 76, расположенных на боковых дверях 15, с гайками 79 соединительного блока 78.
Робот 75 имеет обычную конструкцию с несколькими шарнирами и, более конкретно, у него есть рука 75a, к которому крепится элемент 81 рамы через пару кулачковых зажимных узлов 80, расположенных так, чтобы их зажимные рычаги 80a могли вставляться через секцию оконного проема в боковую внутреннюю дверь 15 и удерживать дверную створку.Аналогичным образом элементы крышки, такие как капот и крышка багажника, временно устанавливаются на секции 1 кузова транспортного средства на восьмой станции S8.
ДЕВЯТАЯ СТАНЦИЯ S9
На девятой станции S9, как показано на фиг. 9 и 12, секция 1 кузова транспортного средства, собранная через первые станции S1 на восьмую станцию S8, поднимается с помощью подъемно-опускного устройства 82, тем самым позволяя подъемно-опускающемуся узлу 82. Узел JU должен быть эвакуирован и удален вниз из секции 1 кузова транспортного средства. После этого сборочный узел JU перемещается на станцию ST склада, а часть 1 кузова транспортного средства перемещается на станцию CS передачи линии CL сборки кузовов транспортного средства.
Как показано на фиг. 12 и 13, подъемно-опускной блок 82 расположен на девятой станции S9 и передаточной станции CS, и он содержит вертикальные стойки 83, расположенные на расстоянии друг от друга в продольном направлении через заранее определенные интервалы, а подъемно-опускающийся рычаг 84 поддерживается каждой из вертикальные стойки 83 с возможностью вертикального перемещения вдоль вертикальной стойки 83. К верхней концевой части подъемно-опускного рычага 84 установлена опорная рама 85, а направляющая 86 расположена между передней опорной рамой 85 и задняя опорная рама 85.Направляющая 86 также устроена так, чтобы ее можно было поднимать или опускать вместе с опорными рамами 85 и подъемно-опускным рычагом 84 с помощью приводного механизма 87.
Направляющая 86 имеет опорную пластину 88, подвешенную с возможностью перемещения. в продольном направлении, и опорная плита 88 имеет четыре опорных рычага 89, установленных на ее четырех угловых частях, чтобы шарнирно поддерживать верхнюю часть 1 кузова снизу. Каждый из поддерживающих рычагов 89 приводится в действие, чтобы закрываться, чтобы принять положение поддержки для поддержки верхней части 1 кузова транспортного средства, как показано пунктирной линией на фиг.12, или открываться для принятия положения освобождения для освобождения верхней части 1 кузова транспортного средства, как показано двухточечной штрихпунктирной линией на фиг. 12, через цилиндр 90, расположенный на секции 85a опорного рычага 85. Верхняя секция 1 кузова транспортного средства транспортируется с девятой станции S9 на передаточную станцию CS в таком состоянии, что верхняя часть 1 кузова поддерживается и подвешен на поддерживающих рычагах 89, как показано сплошной линией на фиг. 12. Когда верхняя секция 1 кузова опускается и эвакуируется из поддерживающих рычагов 89, она собирается с основным элементом 20 пола на сборочной линии CL кузова транспортного средства, на которой установлены различные детали, узлы и аксессуары, как показано на фиг.13.
Теперь обратимся к фиг. 13 и 14 будет дано описание схемы линии сборки кузова CL транспортного средства. Основной элемент 20 пола транспортируется от одной станции (не показана) к другой станции (не показана) в таком состоянии, что он помещается на блок JU и выровнен с поддоном P, расположенным на нем, и различными узлами, деталями и аксессуарами. монтируются один за другим к основному элементу 20 пола, в то время как основной элемент 20 пола транспортируется и переносится с одной станции на другую.Различные узлы, детали и аксессуары включают, например, коврик для пола, ремни безопасности слева и справа, передние сиденья 21 слева и справа, переключающий рычаг 22, а также левое сиденье. и правые задние сиденья 23. Основной элемент 20 пола, на котором были установлены различные части и так далее, затем транспортируется на передаточную станцию CS. В нижней части передаточной станции CS расположено монтажное устройство 91, которое, в свою очередь, выравнивает основной элемент 20 пола с верхней частью 1 кузова транспортного средства, которая должна питаться от девятой станции, и которое приваривает основной элемент 20 пола к стойке. на него опущена верхняя часть кузова 1.После этого, как показано на фиг. 9, полученный в результате узел кузова транспортного средства затем транспортируется на станцию RS для установки элементов крышки, в которой установлены элементы крышки, такие как капот 16, крышка 17 багажника, а также левое и правое передние крылья 18. к кузову автомобиля.
Как описано выше, боковые панели 3 и 4 кузова транспортного средства, а также панель крыши совмещаются с зажимным устройством JU, а затем устанавливаются на него, так что ни кронштейны, ни распорки, ни болты не требуются для крепления боковых панелей кузова транспортного средства и панель крыши, в отличие от обычных процедур.Использование зажимного устройства JU может упростить конструкции боковых панелей кузова транспортного средства и панели крыши и опустить традиционный этап временного монтажа части кузова транспортного средства.
Кроме того, поскольку зажимное приспособление JU выполнено с возможностью исключительного использования с верхней секцией 1 кузова автомобиля без установленной на нем панели пола, зажимное приспособление JU может быть легко эвакуировано из отверстия в полу верхней секции 1 кузова транспортного средства после установки. к верхней части кузова 1 завершена.Следовательно, зажимное приспособление JU может быть выполнено большого размера при условии, что оно может быть эвакуировано из отверстия в полу верхней части кузова 1 транспортного средства, а зажимное приспособление JU может быть снабжено таким количеством функциональных блоков, что функция зажимного приспособления Единица Ю легко может быть сделана множественной. Приспособление JU может быть выполнено настолько большим по размеру и многофункциональным, что верхняя часть 1 кузова может быть установлена с высокой эффективностью и точностью.
К кондукторной установке JU может быть смонтировано множество узлов, деталей и инструментов, в том числе зажимные узлы, электроды для сварки, головки и малогабаритные сварочные роботы.
Далее, после того, как верхняя часть 1 кузова транспортного средства была эвакуирована из кондуктора JU, основной элемент 20 пола устанавливается на верхнюю часть 1 кузова транспортного средства. Перед установкой на верхнюю часть 1 кузова транспортного средства различные детали, узлы а аксессуары, такие как сиденья, устанавливаются на основной элемент 20 пола, так что установка деталей, узлов и аксессуаров может быть осуществлена с легкостью и эффективностью.
Другие варианты осуществления
ФИГ. 15 и последующие относятся к другим вариантам осуществления настоящего изобретения.Те же элементы снабжены теми же ссылочными позициями, что и для первого варианта осуществления настоящего изобретения, как описано выше. Описание этих же элементов будет опущено.
Второй вариант осуществления (фиг. 15)
Фиг. 15 показан механизм выравнивания передней концевой части каждой из внутренних боковых панелей 3. К зажимному блоку JU установлен опорный элемент 96, расположенный так, чтобы его можно было перемещать в продольном направлении с помощью цилиндра 95, который предусмотрен на его верхнем конце. с центрирующим штифтом 97 и с центрирующим элементом 98.Выравнивающая секция 99 для выравнивания нижней части внутренней боковой панели 3 может быть установлена в вертикальном среднем положении опорного элемента 96. Внутренняя боковая панель 3 зажимается зажимным узлом, установленным на опорном элементе 96. На фиг. 15 позицией 100 обозначен сварочный пистолет для временной сварки внутренних боковых панелей 3 на третьей станции S3.
Третий вариант осуществления (фиг. 16)
Этот третий вариант осуществления представляет собой вариант первого варианта осуществления настоящего изобретения, как показано на фиг.1.
Ниже приводится краткое изложение линии BL сборки кузова транспортного средства для удобства ссылки на линию сборки кузова BL транспортного средства в первом варианте осуществления, чтобы подвести итог отличия от первого варианта реализации.
Первая сборочная линия SL1:
Сборка передней части корпуса 2 с полом
Сборочный элемент 5
Первая станция S1:
Настройка сборки передней части корпуса
2 с нижней частью 5 к зажимному устройству
JU
Вторая сборочная линия SL2:
сборка боковых внутренних панелей 3
Вторая станция S2:
установка боковых внутренних панелей 3 до
зажимное устройство JU
Третье сборочная линия SL3:
сборка передней жатки 7a и
задней жатки 7b
Третья станция S3:
Установка сборки передней жатки 7a
с задней жаткой 7b на зажимной блок JU
и временная сварка
Четвертая станция S4:
дополнительная сварка (для сварки дополнительно
или постоянно)
Четвертая линия вспомогательной сборки SL4:
Сборка боковых наружных панелей 4
Пятая станция S5:
Установка сборки боковых внешних панелей
панелей 4 на приспособление JU
Пятая линия вспомогательной сборки SL5:
сборка наружной панели крыши 7B,
сборка заднего поддона 8 и
сборочная единица капота и передней панели 6
Шестая станция S6:
установка сборки крыши
наружная панель 7B, задний лоток для пакетов
в сборе 8 и капот-панель приборов
, монтажный блок 6 к зажимному блоку JU и
, временная сварка
Седьмая станция S7:
дополнительная сварка (для сварки
дополнительно или постоянно)
Шестая вспомогательная сборочная линия SL6:
сборка элементов крышки, таких как
капот 210, крышка багажника 211,
боковые двери 15 и так далее
Восьмая станция S8:
временная установка узла из
элементов крышки, таких как капот
210, крышка багажника 211, боковые
двери 15 и т. Д.
Девятая станция S9:
снятие зажимного приспособления JU с транспортного средства
кузовная секция в сборе
Как показано на фиг.16, дополнительно расположена линия SL20 вспомогательной сборки для сборки внутренней боковой панели 3 с боковой внешней панелью 4 для образования боковой панели 25 кузова транспортного средства, которая, в свою очередь, подается с линии сборки SL20 на вторую станцию S2. . Левая и правая боковые панели 25 кузова транспортного средства выровнены с зажимным устройством JU и затем закреплены на нем.
Приспособление JU затем транспортируется по линии SL21 подсборки, где сборочный узел переднего крыла 7a с задним крылом 7b и внешней панели 7B крыши монтируется на панели 7A крыши.Кроме того, собирается каждый из узла 6 кожуха-передней панели и узла 8 заднего лотка для пакетов. Эти узлы 7A, 6 и 8 структурирования кузова транспортного средства затем подаются на третью станцию S21, где они устанавливаются на блок JU зажима.
На третьей станции S21 узлы 7A, 6 и 8, установленные на сборочном узле JU, временно свариваются с помощью двух сварочных роботов 92, а затем дополнительно или постоянно свариваются с помощью двух сварочных роботов 93, расположенных в четвертая станция S22.После того, как сварка закончена, зажимное приспособление JU перемещается на восьмую станцию S8 (фиг.1) первого варианта осуществления.
Четвертый вариант осуществления (фиг. 17-21)
Этот четвертый вариант осуществления настоящего изобретения представляет собой вариант блока JU зажимного приспособления, как показано на фиг. 2-4.
Как показано на фиг. 17-20, кондуктор JU снабжен четырьмя узлами 175 регулировки положения для совмещения левой и правой передних боковых дверей 15A, а также левой и правой задних боковых дверей 15B с соответствующими четырьмя дверцами. открывающиеся секции 4a верхней части 1 кузова автомобиля.
Узлы 175 регулировки положения установлены на левой и правой опорных пластинах 35, расположенных внутри верхней части кузова 1. Узлы 175 регулировки положения слева и справа имеют одинаковую конструкцию, а передний и Узлы 175 регулировки заднего положения идентичны по конструкции друг другу, за исключением положения, в котором установлен зажимной узел 176. Теперь будет дано описание, в качестве примера, блока 175 регулировки правого переднего положения для регулировки положения, в котором правая передняя боковая дверь 15A установлена на верхней секции 1 кузова.
Как показано на фиг. 17-20, приводной механизм 177 расположен на передней верхней части правой опорной пластины 35 для перемещения почти лежащей H-образной опорной рамы 178, расположенной под частью 4а дверного проема, в продольном, вертикальном и поперечном направлениях. Почти плоский J-образный соединительный элемент 179 расположен на конце каждой из секций 178a рычага опорной рамы 178, и каждый соединительный элемент 179 снабжен зажимным узлом 176.Зажимной узел 176 содержит зажимной рычаг 176а, способный вставляться через открывающуюся часть 15b, расположенную в четырех углах внутренней панели 15а двери, для регулировки или корректировки стеклоподъемника и цилиндр 176b для поворота зажимного рычага 176а. Внутренняя панель 15a двери передней боковой двери 15A зажимается четырьмя зажимными узлами 176 и поддерживается опорной рамой 178. Передняя боковая дверь 15A устанавливается в заданном положении части 4a дверного проема через опорную рамку 178 с помощь приводного механизма 177.Приводной механизм 177 имеет такой общий тип, что он содержит множество электродвигателей для регулировки небольшого расстояния в продольном, поперечном и вертикальном направлениях опорной рамы 178 и винтовой механизм или зубчатый механизм для приведения в действие электродвигателей.
Следует отметить, что сборочная линия BL кузова белого транспортного средства, на которой размещен блок JU, в основном имеет такую же структуру, что и показанная на фиг. 1. На восьмой станции S8 реализованы следующие операции.
Как показано на фиг. 20 и 21, на восьмой станции S8, левая и правая передние боковые двери 15A, а также левая и правая задние боковые двери 15B, снабжаемые шестой вспомогательной сборочной линией SL6 через средство транспортировки. (не показаны) удерживаются на своих боковых дверных внутренних панелях 15a четырьмя узлами 175 регулировки положения, и предварительно определенные положения дверных проемов, в которых затем устанавливаются боковые двери 15A и 15B, регулируются с последующим зажимом пары верхний и нижний шарнирные элементы 76 с боковыми наружными панелями 4 с помощью гайки 79 зажимного узла 78, расположенного снаружи верхней части 1 кузова.
В этом четвертом варианте осуществления передняя и задняя боковые двери 15A и 15B удерживаются изнутри верхней части 1 кузова транспортного средства, и их установка регулируется блоками 175 регулирования положения, так что работоспособность блоков 175 регулирования положения и узел 78 зажима улучшен без взаимного вмешательства, тем самым повышая точность установки передней и задней боковых дверей 15A и 15B.
ПЯТЫЙ ВАРИАНТ ОСУЩЕСТВЛЕНИЯ (фиг. 22)
Пятый вариант осуществления согласно настоящему изобретению представляет собой вариант блока 175 регулировки положения согласно четвертому варианту осуществления настоящего изобретения.
Будет приведено описание блока 175A регулирования положения согласно пятому варианту осуществления настоящего изобретения со ссылкой на фиг. 22.
На поддоне P расположена опорная плита 192, которая поддерживает подвижную плиту 194, с возможностью перемещения в продольном направлении кузова транспортного средства через пару направляющих 193. На подвижной плите 194 установлена опора. пластину 195 через пару направляющих 196 с возможностью перемещения в ее поперечном направлении.Подвижная пластина 194 и опорная пластина 195 перемещаются в продольном направлении относительно опорной пластины 192 с помощью приводного механизма 197, оснащенного электродвигателями и винтовым механизмом. Опорная пластина 195 перемещается в поперечном направлении относительно подвижной пластины 194 через пару цилиндров 198 и поворачивается под заданным углом в направлении, указанном стрелкой Z, в пределах зазора между направляющей 196 и элементом зацепления. (не показана) опорной плиты 195.
На опорной плите 195 расположена пара выступающих вперед и назад опорных втулок 199, на каждой из которых установлена подвижная рама 200 почти F-образной формы, которая может перемещаться в вертикальном направлении. Положение обеих подвижных рам 200 может регулироваться приводным механизмом 201 в вертикальном направлении относительно опорной пластины 195, приводной механизм 201 расположен на боковых поверхностях опорной втулки 199 и оснащен электродвигателями и винтовой механизм.К каждой из концевых частей верхних и нижних секций 200a подвижной рамы 200 расположен зажимной блок 176, а боковая дверца 15A или 15B удерживается подвижными рамами 200 через четыре зажимных блока 176. В этом состоянии, боковая дверь 15A или 15B совмещена с открывающейся частью 4a двери путем регулировки ее положений в продольном, поперечном и вертикальном направлениях и в направлении, указанном стрелкой Z, с помощью приводных механизмов 197 и 201 и пара цилиндров 198.
В четвертом и пятом вариантах осуществления в соответствии с настоящим изобретением элементы для структурирования кузова транспортного средства, такие как боковые внутренние панели 3, монтируются непосредственно на сборочном узле JU. Следовательно, временная установка корпуса кузова не требуется, так что ни кронштейны, ни распорки, ни болты не требуются для установки на элементы для структурирования кузова транспортного средства для временной установки, тем самым упрощая конструкцию элементов для структурирования кузова транспортного средства и пропуская этап временной установки корпуса автомобиля.
В этом пятом варианте осуществления, как описано выше, возможны частичные модификации. Например, боковая внутренняя панель 3 собирается заранее с боковой внешней панелью 4, чтобы сформировать сборку боковой панели кузова транспортного средства, в то время как передний коллектор 7a и задний коллектор 7b собираются заранее с внешней панелью 7B крыши для образования монтаж панели крыши. Узел боковой панели кузова транспортного средства и узел панели крыши подаются на сборочную линию BL кузова транспортного средства, и узел боковой панели кузова транспортного средства затем собирается с узлом панели крыши с помощью зажимного устройства JU.Кроме того, следует отметить, что этот способ сборки может применяться для сборки двухдверных автомобильных транспортных средств. Кроме того, элементы крышки, такие как капоты 16, крышки 17 багажника и т. Д., Могут быть установлены на верхней части 1 кузова с улучшенной эффективностью и с высокой точностью, если снабдить блок Jig Jig блоком регулировки положения для регулировки положение элемента крышки с его внутренней панелью и закрепленным на ней усилением.
Шестой вариант осуществления (фиг. 23-27)
Шестой вариант осуществления согласно настоящему изобретению представляет собой вариант зажимного устройства JU, показанного на фиг.2.
Как показано на фиг. 23-27, зажимное приспособление JU в этом шестом варианте осуществления содержит пару левосторонних и правосторонних сварочных агрегатов 301, первого сварочного робота 302 и второго сварочного робота 303.
Левосторонняя и правосторонняя сварка каждый из блоков 301 установлен на заднем верхнем конце соответствующей опорной рамы 41 таким образом, чтобы фиксированно или таким образом можно было регулировать положение сварочного блока 301. Кроме того, каждый из левого и правого сварочных агрегатов 301 устроен так, чтобы временно и дополнительно или постоянно сваривать участок вблизи нижнего конца передней стойки боковой внешней панели 4 с помощью сварочная головка 301а.
Первый сварочный робот 302 представляет собой многосуставный робот, который установлен в неподвижном вертикальном положении на поддоне P перед и рядом с передней вертикальной стойкой 43. Первый сварочный робот 302 расположен таким образом, чтобы временно и дополнительно или постоянно сварите часть боковой внешней панели 4, расположенную на внешней периферийной части секции переднего оконного проема, изнутри. С другой стороны, второй сварочный робот 303 представляет собой многосуставный робот, который закреплен в положении, расположенном между задней частью с двумя ответвлениями опорной рамы 44.Второй сварочный робот 303 выполнен с возможностью временной и постоянной сварки части боковой внешней панели 4, расположенной на внешней периферийной части секции проема заднего окна, изнутри.
Сборочная линия BL кузова транспортного средства с расположенным на ней зажимным устройством JU в основном имеет такую же конфигурацию, как показано на фиг. 1, и следующие операции выполняются на шестой станции S6 и седьмой станции S7.
На шестой станции S6 внешняя панель 7B крыши, узел 8 заднего уплотнительного лотка и узел 6 кожуха-передней панели сначала устанавливаются на узел JU зажима.
После этого боковая внешняя панель 4 временно приваривается к боковой внутренней панели 3 с помощью двух сварочных роботов 73, расположенных на шестой станции, а также двух сварочных узлов 101, расположенных на зажимном узле JU, и двух сварочных роботов 302 и 303 распорядился к нему. Узел 6 коровьей приборной панели временно приварен к боковой внутренней панели 3 и передней части 2 корпуса. Кроме того, внешняя панель 7В крыши временно приварена к переднему и заднему коллекторам 7а и 7b, а также к боковому внешнему краю. панель 4.Кроме того, узел 8 заднего упаковочного лотка временно приваривается к боковой внутренней панели 3 и к заднему элементу 5 пола.
На седьмой станции S7 временно приваренные части дополнительно или постоянно привариваются с помощью соответствующей сварки. роботы 74, 302 и 303. Как показано на фиг. 8, два сварочных робота 74 расположены на седьмой станции S7. Два сварочных робота 302 и 303 монтируются на кондукторном блоке JU.
В этом шестом варианте осуществления в соответствии с настоящим изобретением передняя часть 2 кузова транспортного средства и задний элемент 5 в сборе пола выровнены и прикреплены к зажимному блоку JU, к которому, в свою очередь, подаются боковая внутренняя панель 3, передний коллектор 7a. и задний жаток 7b.Внутренние элементы этих элементов выравниваются и фиксируются с помощью зажимного устройства JU, после чего происходит соединение левой и правой внутренних панелей 3 с передней секцией 2 кузова автомобиля, задним элементом 5 в сборе пола, передним жатка 7а и задняя жатка 7b. Эта компоновка позволяет осуществлять сборку с высокой точностью и с повышенной эффективностью. Кроме того, следует отметить, что ряд отверстий для сварки можно не выполнять из-за сварки внутренних элементов.
После того, как внутренние элементы были сварены и соединены, как описано выше, поставляются боковая внешняя панель 4 и внешняя панель 7В крыши.Другими словами, боковая внешняя панель 4 совмещена с боковой внутренней панелью 3, которая уже выровнена и соединена с высокой точностью. Кроме того, внешняя панель 7B крыши совмещена с внутренними элементами 7a и 7b крыши, которые уже выровнены и соединены с высокой точностью, и соединены с ними. Следовательно, эти внешние элементы могут быть выровнены с внутренними элементами с высокой точностью и прикреплены к внутренним элементам с высокой эффективностью.
За счет использования сварочных агрегатов 301 и сварочных роботов 302 и 303, которые были размещены на сборочном узле JU, временная и дополнительная или постоянная сварка боковых внешних панелей 4 может быть осуществлена даже изнутри верхнего транспортного средства. корпусная секция 1, так что сварочные операции могут выполняться с высокой эффективностью, а количество сварочных постов может быть уменьшено.
Седьмой вариант осуществления (фиг. 28-34)
Седьмой вариант осуществления согласно настоящему изобретению представляет собой вариант линии BL сборки кузова транспортного средства. Сборочная линия BL кузова транспортного средства седьмого варианта осуществления имеет восемь станций от S1 до S8 включительно, и сборочный узел JU, расположенный на этой сборочной линии BL кузова транспортного средства, имеет ту же конструкцию, что и использованный в шестом варианте осуществления, как показано на фиг. 23. К зажимному устройству JU монтируется сварочный блок 301, а также сварочные роботы 302 и 303.
Теперь будет приведено описание линии сборки кузова BL транспортного средства со ссылкой на фиг. 28 и тому подобное.
Передняя часть 2 кузова автомобиля содержит левую и правую переднюю раму, левый и правый подкрылки колес, нижнюю панель приборов, нижний элемент панели приборов (вторая поперечина) и так далее. А передняя часть 2 кузова собирается на второй вспомогательной сборочной линии SL2.
Следует отметить, что в этом седьмом варианте осуществления панель кожуха, расположенная на передней концевой части кузова транспортного средства, аналогичным образом собирается и устанавливается на верхнюю секцию 1 кузова транспортного средства после установки двигателя внутреннего сгорания.
Задний элемент 5 пола в сборе включает заднюю панель пола, левое и правое заднее пламя, четвертую поперечину, заднюю поперечину, пол багажника, заднюю торцевую панель и т. Д., А также узел 5 заднего пола собирается на первой вспомогательной сборочной линии SL1.
Левая и правая боковые внутренние панели 3 собраны каждая с корпусом внутренней панели, внутренним рельсом крыши, ударным кронштейном, колесной аркой, элементом усиления подвески и так далее.С другой стороны, левая и правая боковые наружные панели 4 собраны каждая с корпусом внешней панели, элементом усиления переднего шарнира, элементом усиления заднего шарнира, элементом усиления центральной стойки, элементом усиления заднего упора. член, угловая пластина и так далее. Кроме того, левая и правая боковые панели 4A кузова транспортного средства собираются каждая с боковой внутренней панелью 3 и боковой внешней панелью 4 на третьей линии SL2 вспомогательной сборки.
Каждый из переднего коллектора 7a и заднего коллектора 7b, как внутренний элемент крыши панели 7A крыши, состоит из внутренней панели заголовка, внешней панели заголовка и так далее.Наружная панель 7B крыши состоит из корпуса внешней панели крыши, ветви 7c крыши и так далее. Панель 7A крыши собирается вместе с внешней панелью 7B крыши, передним коллектором 7a, задним коллектором 7b и так далее на третьей сборочной линии SL3.
Узел 8 заднего упаковочного лотка содержит лоток для пакетов, кронштейн и так далее, а узел 6 сборки коровьей приборной панели содержит панель капота, приборную панель и так далее. Узел 8 заднего упаковочного лотка собран с узлом 6 «корова-панель» на третьей вспомогательной сборочной линии SL3.Основная секция 20 пола собирается на четвертой вспомогательной сборочной линии SL4.
Каждая из крышки 16 и крышки 17 багажника, как элементы крышки, собираются на пятой линии сборки SL5. Четыре боковые двери 15 собираются каждая с внутренней панелью двери, внешней панелью двери, створкой, панелью оконного стекла, стеклоподъемником и так далее на пятой вспомогательной сборочной линии SL5.
Первая станция S1
Как показано на фиг. 29, каждая из передней части 2 кузова транспортного средства и заднего элемента 5 в сборе пола выровнена с зажимным устройством JU и затем зажата соответствующими зажимными узлами на первой станции S1, по существу, таким же образом, как и в первом варианте осуществления, в соответствии с настоящее изобретение.Передняя секция 2 кузова транспортного средства и задний элемент 5 в сборе пола поставляются с первой вспомогательной сборочной линии SL1.
Вторая станция S2
Как показано на РИС. 29, зажимное приспособление JU, переданное с первой станции S1, совмещено со второй станцией S2, а левая и правая боковые панели 4А кузова транспортного средства, подаваемые со второй вспомогательной сборочной линии SL2, выровнены с зажимным блоком JU. с помощью центровочных узлов P1, P2 и P3, а также зажимаемых на их боковых внутренних панелях 3 соответствующими зажимными узлами от C3 до C7 включительно.
В качестве средства для переноса боковых панелей 4А кузова транспортного средства со второй линии сборки SL2 на вторую станцию S2 может использоваться передаточный блок 60, как показано на фиг. 10.
Третья станция S3
Как показано на РИС. 28, панель 7A крыши подается с третьей вспомогательной сборочной линии SL3 на третью станцию S3 и устанавливается на сборочный узел JU, как будет описано ниже. Передний коллектор 7a и задний коллектор 7b панели 7A крыши выровнены с зажимным блоком JU с помощью центровочных блоков P4a и P4b и зажаты зажимными блоками C9a и C9b.Наружная панель 7B крыши совмещается с зажимным устройством JU с помощью центрирующего элемента P5 и зажимается зажимным устройством C10.
После этого левая и правая боковые концевые части переднего коллектора 7а временно привариваются к левой и правой боковым внутренним панелям 3 соответственно с помощью сварочного робота 302. Аналогичным образом, левая и правая боковые концевые части заднего коллектора 7b временно приварены к левой и правой внутренним панелям 3 соответственно с помощью сварочного робота 303.
Далее, как показано на фиг. 29, левая и правая внутренние панели 3 временно приварены к передней части 2 кузова транспортного средства и к заднему элементу 5 в сборе пола с помощью двух сварочных роботов 70, расположенных на третьей станции S3. Аналогичным образом, внешние панели 7B крыши временно привариваются к левой и правой боковым наружным панелям 4.
На третью станцию S3 поставляются сборочный узел 6 приборной панели коровы и узел 8 заднего упаковочного лотка. с третьей подсборочной линии SL3 и устанавливают на отсадочную машину JU следующим образом.Другими словами, сборочный узел 6 «корова» совмещен с зажимным узлом JU через центрирующий штифт 42 и зажат зажимным узлом C8. С другой стороны, элемент 8 узла заднего уплотнительного лотка совмещен с зажимным устройством JU с помощью центрирующего штифта 55 и зажат зажимным устройством C11.
После того, как узел 6 в сборе с коровьей стойкой и задний элемент 8 подноса для пакетов были зажаты, узел 6 в сборе с коровьей стойкой временно приваривается к боковой внутренней панели 3 и передней части 2 кузова с помощью сварочный робот 70, расположенный вне секции кузова транспортного средства, и сварочный робот 302, расположенный внутри секции кузова транспортного средства, и элемент 8 узла заднего лотка для пакетов временно приварен к боковой внутренней панели 3 и элементу 5 узла заднего пола с помощью сварочный робот 70, расположенный вне секции кузова транспортного средства, и сварочный робот 303, расположенный внутри секции кузова транспортного средства.Часть боковой внутренней панели 3, расположенная рядом с нижней концевой частью передней стойки 12, временно приварена к сварочному узлу 301 и узлу 6 сборки коровьего упора.
Поскольку временная сварка может быть осуществлена из внутри верхней части 1 кузова транспортного средства с помощью сварочных роботов 302 и 303, а также сварочного агрегата 301, который расположен на сборочном узле JU, сварочные операции могут выполняться с высокой эффективностью и большим количеством сварочных аппаратов. станции для сварки можно уменьшить.
Четвертая станция S4
На четвертой станции S4 расположены два сварочных робота 71, как показано на фиг. 30, и они скомпонованы таким образом, чтобы дополнительно или постоянно сваривать соединения передней части 2 кузова транспортного средства, узла 5 заднего пола, левой и правой боковых панелей 4А кузова транспортного средства и панели 7А крыши.
Пятая станция S5
На пятой станции S5 верхняя часть 1 кузова поднимается вверх с помощью подъемно-опускного устройства 82 (ФИГ.12), а кондуктор JU откачивается из верхней части 1 кузова в направлении снизу. Блок JU зажимного приспособления перемещается на станцию хранения шаблонов ST, а верхняя часть 1 кузова перемещается и загружается на поддон CP шестой станции S6, как показано на фиг. 32. К поддону CP прикреплен сварочный робот 373, расположенный внутри верхней части 1 кузова транспортного средства.
Шестая станция S6
На шестой станции S6 два сварочных робота 72 расположены снаружи верхней части 1 кузова транспортного средства, поскольку показанный на фиг.33. Дополнительная или постоянная сварка дополнительно выполняется сварочными роботами 72, расположенными снаружи верхней части 1 кузова транспортного средства, и сварочным роботом 373, расположенным внутри верхней части 1 кузова транспортного средства. Следовательно, сварочные операции могут выполняться с высокой эффективностью и количество постов для сварки может быть уменьшено.
Седьмая станция S7
Как показано на фиг. 31, верхняя часть 1 кузова транспортного средства перемещается и перемещается с помощью подъемно-опускающегося узла, имеющего по существу такую же конструкцию, что и подъемно-опускающийся узел 82, от шестой станции S6 к седьмой станции S7, проходящей по прямой линии от первая-шестая станции S1-S6.С другой стороны, основной элемент 20 пола установлен на заранее определенном приспособлении, расположенном на седьмой станции S7. Верхняя часть 1 кузова подается на седьмую станцию S7 с шестой станции S6, а затем опускается сверху до основного элемента 20 пола, установленного на зажимном приспособлении. Затем верхняя секция 1 корпуса транспортного средства выравнивается с основным элементом 20 пола, который, в свою очередь, временно, а затем постоянно приваривается к верхней части 1 кузова транспортного средства с помощью сварочного робота 74, расположенного снаружи верхней части кузова, как конкретно показано на фиг. .34, тем самым формируя секцию 1 кузова транспортного средства с установленным на ней основным элементом 20 пола. Эта секция 1 кузова транспортного средства соответствует корпусу кузова транспортного средства.
Восьмая станция S8
Корпус транспортного средства переносится с седьмой станции S7 на восьмую станцию S8. Левая и правая боковые двери 15, капот 16, передние крылья 18 и крышка 17 багажника поставляются с пятой сборочной линии SLS. Левая и правая боковые двери 15 крепятся к боковым открывающимся частям корпуса транспортного средства с помощью монтажного робота, хотя это не показано.Капот 16 и передние крылья 18 аналогичным образом установлены на передней части 2 кузова транспортного средства, а крышка 17 багажника аналогичным образом установлена на задней части кузова транспортного средства. Затем после установки двигателя внутреннего сгорания монтируется кожух.
В этом варианте осуществления согласно настоящему изобретению зажимной блок JU снабжен парой сварочных блоков 301 и парой передних и задних сварочных роботов 302 и 303, так что часть временной сварки при установке кузова транспортного средства боковые панели 4A и панель 7A крыши выполнены с внутренней стороны верхней части 1 кузова.Кроме того, следует отметить, что сварочные роботы 302 и 303 могут быть скомпонованы так, чтобы выполнять дополнительную или постоянную сварку в дополнение к временной сварке.
Следует понимать, что настоящее изобретение не истолковывается как ограничивающееся в каких-либо отношениях описанными выше, которые описаны только в иллюстративных целях, и как охватывающее все изменения, вариации и модификации в пределах сущности и объема настоящее изобретение.
Как установить обвес
Установить обвес на автомобиль — довольно серьезное обязательство.Обвес состоит из переднего и заднего бамперов, спойлеров, боковых щитков и краски. Заводские детали будут удалены, и их место займут запасные части. Во многих случаях требуется модификация автомобиля для установки этого комплекта.
В отношении всего, что может кардинально изменить внешний вид автомобиля, важно набраться терпения и все измерить дважды, иначе конечный продукт может оказаться несовместимым и дешевым. Некоторые комплекты достаточно просто установить самостоятельно, но для большинства лучше всего, чтобы это сделал профессионал.Вот как найти работающий комплект и узнать, как его установить.
Часть 1 из 4: Поиск обвеса
Шаг 1. Найдите нужный обвес . Привыкайте часто использовать вашу любимую поисковую систему в процессе поиска обвеса, подходящего для вашего автомобиля и бюджета. Найдите время, чтобы просмотреть несколько примеров, которые показывают, какой внешний вид вы собираетесь использовать, и обратите пристальное внимание на любые названия компаний, которые часто всплывают, так как на них будет полезно ссылаться позже.
Вы можете создать папку с фотографиями для вдохновения и справки, но некоторые онлайн-приложения, такие как Pinterest, могут упростить и разнообразить этот процесс.
Составьте список, указав все компании (или топ-10), которые производят комплекты, подходящие для вашего автомобиля и которые вам нравятся. Для более непонятных машин может быть только один или два варианта. Для таких автомобилей, как VW Golf или Honda Civic, есть сотни, если не тысячи вариантов.
По каждому варианту ищите как можно больше отзывов клиентов.Найдите места, где клиенты упоминают, как подходит комплект, насколько сложна установка и какие проблемы могут возникнуть после установки. Например, иногда комплект приводит к трению шин о корпус или издает неприятный шум ветра на высокой скорости.
Изображение: ОбвесыШаг 2: Купите комплект . Приобретайте комплект, который в конечном итоге выбираете, и на протяжении всего процесса заказа учитывайте конкретную модель и компоновку вашего автомобиля. Для некоторых моделей фактические размеры будут отличаться в зависимости от региона, в котором они продаются.
При заказе онлайн позвоните и поговорите с сотрудником. Задайте любые вопросы, которые у вас на уме, перед оформлением заказа. Они смогут посоветовать вам, как его установить, и может ли комплект быть установлен даже непрофессионалом.
Имейте в виду, какие инструменты потребуются для установки комплекта. Некоторым нужны только отвертки и гаечные ключи, а некоторым требуется резка и сварка.
Шаг 3. Осмотрите комплект . Перед тем, как начать процесс установки, осмотрите каждую деталь комплекта и убедитесь, что она не только соответствует вашей модели автомобиля, но и что детали симметричны.
Разложите части на земле рядом с их соответствующими местоположениями на теле, общую длину и ширину можно будет легко проверить, если держать их рядом с заводской частью.
Если какие-либо детали повреждены или неисправны, замените их, прежде чем продолжить.
Часть 2 из 4: Установка обвеса на автомобиль
Необходимый материал
Сегодняшним покупателям доступно большое количество различных обвесов и разных стилей, поэтому каждый комплект будет иметь свои особенности и недостатки.Требуется определенное количество подгонок, так как комплекты редко бывают идеальными, и после того, как автомобиль использовался какое-то время, небольшие неровности и царапины могут привести к смещению панелей. Каждый автомобиль и каждый комплект индивидуальны, но есть несколько шагов, которые практически универсальны.
Шаг 1: Подготовьте детали комплекта для установки . Если вы не красите всю машину после установки комплекта, вам необходимо покрасить части комплекта перед установкой.
Если вы собираетесь красить детали набора, узнайте код вашего цвета краски у производителя.Краска на новых деталях будет выглядеть совершенно новой, поэтому после установки комплекта необходимо отполировать и детализировать остальную часть автомобиля, чтобы она выглядела единым целым.
- Совет . Вы можете получить советы о том, где найти код краски для каждой части вашего автомобиля, в Интернете.
Шаг 2: Снимите все заводские детали, которые будут заменены деталями комплекта . Обычно это бамперы и пороги / пороги.
На некоторых автомобилях это будет очень сложно и может потребоваться специальный инструмент.Заранее исследуйте процесс для вашей конкретной модели, чтобы не бегать в магазин каждые пару часов.
Шаг 3. Очистите открытые поверхности . Очистите все поверхности, на которые будут установлены новые детали, с помощью обезжиривателя. Это предотвратит попадание сажи и скопившейся грязи на комплект деталей кузова.
Шаг 4: Разложите обвес . Выровняйте части комплекта рядом с местами, где они будут установлены, чтобы убедиться, что отверстия, винты и другие элементы совпадают правильно.
Шаг 5: Присоедините каждую деталь комплекта . Начните прикреплять части обвеса, если возможно, начните с переднего бампера.
- Примечание : В некоторых комплектациях сначала необходимо надевать боковые юбки, чтобы избежать перекрытия с бамперами, но установка передней части в первую очередь и продвижение назад поможет всему комплекту подняться и течь вместе с автомобилем.
Подправьте переднюю часть так, чтобы она совпала с фарами и решеткой.Это может занять некоторое время методом проб и ошибок.
Установите и отрегулируйте боковую юбку, чтобы совместить с крыльями и передним бампером.
Совместите задний бампер с задними фонарями и боковыми юбками.
Сделайте шаг назад и оцените, насколько все подходит. Решите, нужно ли корректировать положение каких-либо фигур.
Шаг 5 : Для комплектов, в которых используется клей вместе с винтами для крепления деталей, есть дополнительная ступенька.
После того, как детали установлены и отрегулированы в нужное положение, возьмите жирный карандаш и наметьте контур деталей набора.
Наклейте липкую ленту и двусторонний скотч на части обвеса, а затем установите их все. На этот раз убедитесь, что они установлены достаточно надежно, чтобы избежать неправильного вождения по дороге.
- Примечание : Убедитесь, что детали идеально выровнены, когда наклеена двусторонняя лента.
Часть 3 из 4. Найдите магазин, где можно установить обвес
Если комплект, который вы выберете, слишком сложен для самостоятельной установки (некоторые популярные комплекты от Rocket Bunny требуют обрезки крыльев) или если ваш автомобиль просто слишком сложно разобрать дома, вам нужно найти уважаемый магазин, чтобы выполнить установку. .
Шаг 1. Изучите потенциальные магазины . Поищите в Интернете магазины, которые известны как установкой обвесов, так и работой с автомобилем вашей марки.
Прочитать отзывы покупателей. Особо ищите те, в которых указана цена и время выполнения заказа.
- Примечание : Магазин, который будет работать лучше всего, может находиться далеко от того места, где вы живете, поэтому выделите средства на доставку автомобиля, если вы решите выбрать место по всей стране.
Постарайтесь найти на разумном расстоянии магазин, имеющий положительные отзывы.Хорошее время выполнения работ и указание окончательной цены также важны, но для некоторых моделей количество магазинов, которые могли бы выполнить модификации, может быть настолько маленьким, что вам, возможно, придется довольствоваться хорошими отзывами. Попытайтесь увидеть некоторые из уже выполненных ими работ, чтобы убедиться в качестве их работы.
Шаг 2: Доставьте машину в магазин . Либо оставьте машину самостоятельно, либо отправьте ее в магазин. Включите все детали, необходимые для набора.
Срок выполнения зависит от сложности обвеса, степени модификации и окраски.
Если вы оставите автомобиль с уже покрашенным кузовным комплектом и комплект будет простым, то установка может занять несколько дней.
Если комплект нужно покрасить, но автомобиль остается того же цвета, то процесс займет немного больше времени. Ожидайте, что это займет одну-две недели.
На выполнение очень сложного комплекта или особенно обширного набора модификаций могут уйти месяцы. Если нужно покрасить всю машину, это займет значительно больше времени, чем получение деталей правильного цвета с самого начала.
- Примечание : Это время отражает время, которое проходит с момента начала работы на вашем автомобиле. В загруженных магазинах вы можете стоять в очереди за несколькими другими покупателями.
Часть 4 из 4: После установки обвеса
Шаг 1. Проверьте центровку . Проверьте колеса и посмотрите, насколько они подходят к новому обвесу. Возможно, вам понадобятся колеса большего размера, чтобы избежать неудобного зазора.
Вам не нужно слишком много места вокруг колеса или слишком большой свес от крыла.Получите комбинацию колеса / шины, которая адекватно заполняет крылья, не касаясь их при прогибе подвески.
Шаг 2: Проверьте высоту . Убедитесь, что дорожный просвет достаточен, чтобы бамперы и боковые юбки не подвергались чрезмерным злоупотреблениям при движении. Подвеска обычно занижается вместе с установленным обвесом, просто убедитесь, что вы можете иногда преодолевать лежачие полицейские.
Пневматическая подвеска позволяет водителю регулировать высоту своего автомобиля.Таким образом, он может сидеть ниже на гладкой дороге и выше на ухабистой.
Выполните пробную поездку на автомобиле и отрегулируйте подвеску, если колеса касаются колодцев крыльев или если подвеска не работает плавно. Потребуется несколько попыток, чтобы набрать его.
Убедитесь, что вы полностью довольны установкой нового обвеса, прежде чем платить за него, так как после того, как вы заплатили и уехали, договориться о любых изменениях будет сложнее. Если вы устанавливаете обвес самостоятельно, не торопитесь и выполняйте каждый шаг как можно точнее.Готовый продукт будет стоить того внимания, которое вы сейчас уделяете каждой детали.
Пластиковые автомобили | Как работает автомобиль
Упомяните пластиковые автомобили, и большинство людей думает о дырявых, скрипучих и безумных. кузов, столь распространенный на автомобилях из стекловолокна 1960-х годов.
Где используются пластмассы
Пластмассы и другие композитные материалы широко используются для изготовления внешних панелей, а иногда и целых кузовов. Материалы, которые, скорее всего, будут использоваться для бамперов, — это термопласты или полипропилен.Жесткие материалы, такие как армированный стекловолокном пластик и армированный полиэстер, лучше подходят для кузовных панелей. В Renault Espace используются пластиковые панели кузова, закрепленные на стальной раме шасси, защищенной цинком.Пластик по-прежнему имеет плохой имидж даже сегодня, поскольку его больше связывают с непрочным игрушки, чем передний край мотор отраслевые технологии. Но пластмассы все чаще используются в производстве автомобилей, в основном в результате езды к снижению веса для более низких топливо расход и большая экономия.
На протяжении многих лет проблема заключалась в том, что пластмассы недостаточно прочные, чтобы использоваться без армирования. Теперь сцена меняется, появляется больше сложные композитные материалы заменяют простые пластмассы. Эти новые материалы вносят изменения в дизайн и производственные процессы, но, прежде всего, предлагают большую экономичность вождения.
Пластиковый вентиль шины
Пластик Michelin VMP 413 шина клапан легче традиционного металлический клапан и состоит всего из четырех подвижных компонентов — три защелкивающихся вместе пластиковые детали и металлическая пружина.Пластик — это искусственная смола, называемая Делрин. Клапан лучше удерживает воздух на высоких оборотах и оказывает меньшее влияние по балансировке колес, чем обычный клапан из стали и латуни.Реакция литья под давлением
Реакционное литье под давлением
При реакционном литье под давлением используются два типа жидкость пластик вводится одновременно. Они вступают в химическую реакцию и затвердевают внутри формы. Процесс очень быстрый, на заполнение каждой панели уходит всего около 90 секунд.
Крылья и бамперы Reliant Scimitar SS1 сделаны таким же образом, но имеют дополнительную изысканность — сначала в форму укладывают мат из стекловолокна, а вокруг него выдавливается жидкий пластик. Отливки под давлением с усиленной реакцией (RRIM) могут быть очень гибкими, сохраняя при этом высокую прочность.
Машины из стекловолокна
Стекловолокно — более правильно известное как GRP, что означает армированное стекловолокном. полиэстер — сочетает легкость с прочностью.Вес на вес, стекловолокно намного прочнее стали, поэтому панели можно сделать легче. Много лет это был единственным пластиковым материалом, который использовался для изготовления деталей автомобилей, и до сих пор широко используется сегодня.
В корпусе кузова из стекловолокна маты из стекловолокна используются для усиления панель из полиэстера или эпоксидной смолы. Полученный материал относительно жесткий, но все еще имеет достаточную «отдачу», чтобы противостоять малой скорости удары . В 1950-х годах производители начали использовать материал для кузовов автомобилей.Первая машина на со стекловолоконным кузовом был Chevrolet Corvette 1957 года выпуска, но под ним все еще использовалась обычная сталь шасси чтобы придать ему силы.
В следующем году Lotus представила оригинальную Elite — первую в мире, цельностекловолоконный монокок. У него не было стального шасси, а двигатель , механизм коробка и подвески были прикручены непосредственно к стекловолоконной оболочке. Среди машин в настоящее время в производстве с этой конструкцией находится Midas, малотиражный специализированный автомобиль, который берет большую часть ходовой части от BL Mini и Метро.
Стеклопластик против стали
В качестве альтернативы стали конструкция из стекловолокна имеет значительную преимущества. Несмотря на то, что сечение намного толще, структура легкая и ржавчина. уходит в прошлое (кроме случаев, когда он прикреплен к металлу). Для производителя, затраты на оснастку ниже, чем для вагоностроения из стали потому что большие прессы обычно не нужны.
Несмотря на преимущества, автомобили из стекловолокна производились только небольшими производителей, как правило, привлекает невысокая стоимость оснастки.Для массового производства, это никогда не было действительно жизнеспособным предложением. Производство относительно медленно, так как каждую часть тела нужно вылечить в течение пары часов. Кузов автомобиля производство стали, с другой стороны, принесло гораздо больше преимуществ. инвестиции и развитие.
Литье из стекловолокна
Стекловолокно может изготавливаться как в цельной «открытой» форме, так и в двухкомпонентной. Нажмите. В открытой форме только одна сторона готовой панели будет иметь хорошая отделка, но форму сделать несложно.Этот метод обычно только используется для изготовления одноразовых панелей в домашних условиях. Использование двухкомпонентной формы приводит к получению панели точного размера, которая гладкие с обеих сторон, одинаковой толщины и качества с минимальными затратами риск появления пузырьков воздуха. Большинство автомобильных кузовных панелей изготавливаются в пресс-формах из двух частей. Тканое стекловолокно в нижнюю половину формы укладывается циновка, затем вторая часть упал сверху и зафиксировал на месте. Жидкая эпоксидная или полиэфирная смола закачивается в форму.Примерно через час формовка из стекловолокна станет затвердели, и плесень можно отделить. Lotus, которые используют технику двухкомпонентной формы, но используют сталь и кевлар. арматура, а также стекловолокно, делают свои тела в двух основных детали — верхняя и нижняя половина — которые склеиваются после формования. Lotus также использует секции пенопласта, обернутые стекловолокном, в пресс-форме для формирования жестких коробчатые секции для порогов кузова и других участков, требующих большего сила.Композиты
Citroen BX капот
Капот и задняя дверь BX изготовлены из полиэфирных смол.Усиление для придания жесткости обеспечивается сетками, отформованными на нижней стороне капота, и формованными длинными прядями из стекловолокна. После изготовления панели окрашиваются в цвет кузова.С первых дней стекловолокна, использование пластмасс и др. композиты прошли долгий путь с такими технологиями, как реакционная инъекция формование, позволяющее значительно ускорить производство цикл .
Большинство производителей в настоящее время используют пластик в той или иной форме для изготовления бамперов своих легковые автомобили. На заре производства пластмасс молдинг бампера был цельный кусок уродливого толстого пластика (полипропилена или термопласта) в черный или серый, обычно с металлической арматурой сзади для обеспечения адекватного сила и сопротивление к провисанию.
Бамперы Rover 800
Они формируются вокруг пенопласта, образуя прочную коробчатую секцию. Металлический каркас сзади добавляет прочности.В настоящее время прочность, скорее всего, достигается за счет литых коробчатых секций: кусок легкого пенопласта используется в качестве основы, вокруг которой остальная часть бампер литой. Сама по себе пена не имеет реальной прочности, но когда она используется как распорка он формирует из пластика прочную «полую» секцию.Ровер сделать бамперы 800-й серии таким образом, но Lotus разработала техника в той степени, в которой они могут использовать ее для основных структурных секций их автомобильных кузовов. Стальные детали также могут быть отформованы, чтобы обеспечить локализацию усиление для крепления дверных петель или замков, а также для защитных деталей, таких как дверные балки и рулонные дуги.
Многие из производимых в настоящее время автомобилей с пластиковым корпусом используют различные типы пластик для разных деталей. Бамперы должны быть деформируемыми, чтобы поглощать удары, и эластичны, чтобы избежать необратимых повреждений, поэтому они сделаны из различных специально модифицированные пластмассы с некоторыми каучуковидными свойствами (например, полипропилен или модифицированный термопластичный полиэстер).Для панелей типа багажника крышка лучше использовать более жесткий материал, например, довольно толстое стекло волокно или полиэстер, армированный холодным прессованием, чтобы водитель чувствовал солидность при ударе.
Картер дизельного двигателя Maestro
Чтобы снизить уровень шума, производимого дизельным двигателем, поддон сделан из ламината сталь-пластик-сталь.Использование множества различных материалов легко организовать, если тело состоит из из ряда различных частей, прикрученных к центральной конструкции, но Лотус, который делят свои тела на две основные части, умудряются совмещать несколько разных материалы в одну отливку.С автомобилями с индивидуальными панелями прикручен к отдельной стали Рамка , такие как Reliant Kitten и Scimitar и Renault Espace каждая панель может быть изготовлена только из одного материала или составной из двух.
При условии, что все используемые материалы могут быть адаптированы к однотипная система окраски, проблем с отделкой не будет.
Покраска пластиков
Ятаган Reliant SS1
Из-за того, что конструкция из нескольких панелей крепится на болтах, разные панели могут быть из разных материалов, в зависимости от выполняемой ими работы.Бамперы и крылья изготовлены из полуэластичного усиленного полиэстера, полученного методом литья под давлением, для минимизации повреждений от небольших ударов. Двери, крышка багажника и другие панели могут быть более жесткими и изготовлены из усиленного прессованного полиэстера. Огнестойкий кожух изготовлен из полиэстера, полученного методом вакуумного литья под давлением, с прослойкой из жесткого уретана.Полиэстер, армированный стекловолокном, подойдет обычная краска, как и другие материалы, такие как жесткий полиэстер, используемый для негибких частей тела.Большинство пластмассы не выдерживают температуры отверждения краски, поэтому обычным способом Решение проблемы заключается в использовании двухкомпонентной системы окраски, которая отверждается химическим путем. реакция, а не с теплом. Renault использует этот тип системы окраски для Espace, в краску которого также нанесены мелкие шарики из полиэстера. для участков с повышенным износом, таких как нижние панели, которые подвержены атакам со стороны грязь, песок и каменные осколки.
Не допускается самостоятельная окраска полиуретана высокой плотности и обычного краска не прилипала к нему, поэтому многие ранние бамперы были непривлекательными.С затем были введены новые материалы и специальные грунтовки, позволяющие бамперы покрасить.
Бамперы Austin Maestro и Montego, которые сделаны из PBT. (полибутадиен терафталат), распыляются одновременно с телом, чтобы обеспечить хорошее соответствие цветов. Они закрашены от тела, а затем установлен.
Другие части
GKN Пружина
Эта листовая рессора из полиэстера, армированного стекловолокном, используется на некоторых фургонах Sherpa.Пружина полностью отформована, поэтому она полностью гладкая. Он имеет различное поперечное сечение и имеет проушины на каждом конце, закрепленные стальными скобами.Хотя пластмассы все чаще используются для изготовления частей тела и мелких компоненты, недавние достижения означают, что пластик скоро может быть в широкое использование для более крупных компонентов. Стекловолокно рессоры уже использовался на Chevrolet Corvette 1980-х годов и в фургоне Sherpa.
Полиэстер холодного отжима
Этот метод используется, когда жесткие, точно обработанные панели с хорошей качество поверхности необходимо.Нижняя половина формы покрыта полиэфирной смолой, затем Сверху укладываются предварительно сформированные кусочки непрерывного стекловолокна. Форма закрывается, и катализированная огнестойкая смола вводится под давление . Он проходит через стекловолокно и вступает в реакцию с полиэфирная смола для твердого схватывания.Моделирование нескольких тел, часть 3: Как создать несколько тел
Сделать несколько тел из одной детали очень просто. Вот несколько способов сделать это:
Непересекающиеся твердые тела
Когда вы создаете твердые области, которые не соприкасаются друг с другом, они называются областями .Технически в одном теле может быть несколько областей. Итак, нарисуйте прямоугольник, выдавите его до твердого тела. Нарисуйте еще один прямоугольник и выдавите еще одно твердое тело в той же части, которое не касается первого твердого тела, и у вас есть 2 области, одно тело. Я как бы забиваюсь на это, потому что меня это сбивает с толку, поскольку я слишком много лет работал с другой системой. Из-за этой концепции «непересекающихся твердых тел» вы должны быть более осторожными при использовании термина «мульти-тела» в Solid Edge.
Если вы хотите скачать часть, использованную для создания этого изображения, она прикреплена к этому сообщению с именем mbm1.пар. Это очень просто, но вы должны легко увидеть, что было сделано, и поиграть с этим, не опасаясь сломать что-нибудь важное.
На изображении выше курсор находится над Design Body 1 на панели Обработки контуров, поэтому две области, составляющие это тело, выделены оранжевым. По умолчанию они будут прозрачно-серыми, потому что они неактивны. Design Body 2 — это отдельная область, которая является активным телом. Я создал запись Design Body 2 на панели Обработки контуров, используя инструмент Добавить тело, показанный справа.
Таким образом, при выдавливании непересекающихся эскизов создаются сплошные области, пока вы не воспользуетесь командой «Добавить тело». Это первый и самый простой способ создать несколько областей / тел в Solid Edge.
Вставить копию детали
Следующий инструмент, о котором стоит поговорить, — это команда «Вставить копию детали». Это позволяет вам вставлять одну часть в другую, где все, что отображается во второй части, является одним элементом. Мне непонятно, почему эта команда отображается в группе «Буфер обмена» на вкладке «Главная», но вы найдете ее именно там.Интерфейс можно настраивать, поэтому, если это действительно вас оскорбляет по какой-то причине, вы можете поместить его в другое место, которое имеет для вас больше смысла.
Когда вы используете эту функцию в синхронном режиме, она не ассоциативна. При первом использовании вы получите такое сообщение:
Я видел много людей, которые игнорируют подобные сообщения или считают, что никакие сообщения, отправляемые программой, не являются полезными. Не будь одним из таких людей. По крайней мере, прочтите сообщение, прежде чем судить о его полезности.Это довольно ясно. Поэтому, если вы внесете изменения в исходную модель, вставка копии детали не обновится. Иногда это именно то, что вам нужно, а иногда нет. Если вам нужна функция, которая будет обновляться с изменениями в исходном файле, переключитесь в упорядоченный режим и используйте таким образом Вставить копию детали.
Диалоговое окно «Параметры копирования детали» помогает вставить существующую деталь в новую. Существующая часть, которую я называю «родительской частью», может быть многотельной или многозональной.Например, я использовал часть mbm1.par, используемую в приведенном выше примере, в качестве родительской части, чтобы вставить ее в новую часть с помощью команды Insert Part Copy.
Чтобы использовать этот инструмент, просто создайте новую деталь или откройте существующую деталь. Эту часть я называю «дочерней частью». Затем нажмите «Вставить копию детали» на вкладке «Главная» в группе «Буфер обмена». Подтвердите сообщение, описанное выше, если вы находитесь в синхронном режиме.
Затем появится диалоговое окно справа. Это дает вам множество вариантов.
В раскрывающемся списке «Элемент семейства деталей» можно выбрать один конкретный элемент из семейства деталей родительской детали. Это может быть конкретный размер или версия с определенными функциями или без них.
«Копировать как тело проекта» вставляет тела родительской детали как тела проекта.
«Объединить твердые тела» объединит тела родительской детали с телами дочерней детали.
«Зеркальное тело», конечно же, дает вам деталь, противоположную оригиналу, и вы даже можете использовать инструмент «Масштаб» для равномерного или неравномерного масштабирования.
«Flatten» предназначен для корпусов из листового металла.
Перемещение тел в синхронном режиме довольно просто. Просто выберите тело на панели Обработки контуров и с помощью рулевого колеса переместите тело в новое место. Намного проще, чем другие программы, которые я использовал.
Вырезание тела
Я использовал mbm1.par для создания этого разреза. Сначала я активировал Design Body 1, затем нарисовал на нем прямоугольник и выдавил часть прямоугольника над блоком, чтобы сделать сквозной разрез.Это не создает другое тело, это создает область . Опять же, если вы понимаете эту концепцию «регионов», прошу прощения за это подчеркивание, я делаю это в первую очередь потому, что мне все еще трудно с этим. Отсюда мне непонятно, как разделить области на тела, если у вас есть необходимость в этом.
Split
Split, на мой взгляд, один из наиболее полезных инструментов MBM. Разделение позволяет разделить твердое тело на несколько тел с плоскостью, другим твердым телом или поверхностью.Это очень удобно. Одним из недостатков инструмента является то, что он работает только с одним телом за раз (вы не можете разделить несколько тел, хотя, опять же, вы можете разделить несколько областей в одном теле).
Divide
Я слышал об этой функции «разделения». Похоже, что он был спрятан в ST5 и, возможно, удален в ST6. Я не могу найти его в интерфейсе настройки. Похоже, что его заменила функция Multi-Body Publish. Может здесь кто-нибудь поправит / подтвердит.Трудно не быть экспертом . В любом случае Divide кажется устаревшей функцией.
Multi-Body Publish
Multi-Body Publish — это своего рода конец процесса MBM. Эта функция позволяет вынести каждое тело в отдельные файлы деталей. Это также объединит все эти отдельные части в сборку. Это здорово. Это классный инструмент, он делает то, что нужно, прост в использовании и не требует пояснений.
Как переоборудовать и построить новые кузова Chevy ’57 для развлечения и прибыли
Я хожу на выставку SEMA (Speciality Equipment Market Association) в Лас-Вегасе с 1981 года.В процессе я видел больше замысловатых коллекторов выхлопной системы и выбитых колес, чем я мог бы сосчитать на своем ноутбуке. Но я продолжаю возвращаться, потому что всегда нахожу что-то новое.
В этом году я заметил, что продавцы продают полностью новые кузова для старых автомобилей. Один стенд на выставке продавал свежие кузова Мустангов и Камарос 60-х. Другой предлагал новенькие кузова Chevy 57 года выпуска.
Это были не копии из стекловолокна, а изделия из штампованной стали, состоящие из панелей кузова, которые взаимозаменяемы со стандартными частями.Они готовы сочетаться с рамой, трансмиссией и подвеской, чтобы создать совершенно новый автомобиль.
Chevy 57-го года производится компанией EMI в Стерлинг-Хайтс, штат Мичиган, в 60 милях от нашей штаб-квартиры в Анн-Арборе, которая была основана в том же году, когда появился знаменитый Chevy. Вернувшись с выставки, я посетил компанию, чтобы увидеть, как она умудряется производить эти тела в небольших количествах по разумной цене.
Оказывается, EMI — Experi-Metal, Inc. — специализируется на производстве небольших партий металлических корпусных деталей.150 сотрудников EMI построили первые прототипы нынешних Ford Mustang и F-150, а также Pontiac Solstice. «Мы можем сделать белое тело полностью из математической модели за четыре месяца», — говорит генеральный директор Джерри Кинг.
EMI также производит восстановленные детали из листового металла для автомобилей от Ford Coupe 32-го до Chevy 57-го. Фактически, одна из причин, по которой компания решила сделать кузов 57-го года полностью, заключалась в том, что она уже производила около половины кузовных панелей в качестве запасных частей.
Эти панели производятся тем же способом, что и производственные кузовные детали: путем помещения плоских стальных листов между двумя металлическими штампами, имеющими форму конечной детали, и сжатия штампов вместе с усилием в несколько тысяч фунтов.
Основное различие между Chevy и прототипами заключается в конструкции штамповочных штампов. Штампы для прототипов начинаются с баз данных САПР или электронных представлений формы и размера кузова автомобиля, созданных при проектировании транспортных средств на экранах компьютеров. Для Chevy ’57 EMI пришлось создать собственную базу данных САПР, используя цифровые датчики для измерения контуров реальных панелей кузова Chevy.
Из этой базы данных сотрудники EMI определяют, как на детали следует поставить штамп.Это означает, что нужно выяснить, в каком направлении должны двигаться штампы и сколько ударов потребуется. Это не только наука, но и искусство, сочетающая в себе опыт — Кинг работает в области штамповки листового металла 34 года — а также специализированные компьютерные программы, такие как Dynaform, которые помогают определить, будут ли плоские стальные листы складываться или рваться по мере их образования из-за умирает.
После определения формы штампов используется фрезерный станок с компьютерным управлением для вырезания копий штампов из гигантских блоков пенопласта — для переднего крыла может потребоваться матрица длиной восемь футов, шириной пять футов и два фута. глубокий.
Эти копии из пенопласта помещаются в большие стальные рамы, где их набивают формовочный песок (песок с примесью клея). Затем пену удаляют, оставляя полость, заполненную расплавленным металлом. Металлом для штампов, используемых на автомобильных заводах, является сталь, которая обеспечивает прочную и долговечную матрицу. Но для прототипов и кузова Chevy EMI использует кирксит, цинковый сплав, который легче обрабатывать, чем сталь, и разливается только при 800 градусах, а не при 2800 градусах, необходимых для стали.Для более крупных инструментов требуется до 30 000 фунтов расплавленного кирксита.
После того, как металл затвердеет, песок удаляется, а штамп для чернового литья возвращается к фрезерному станку, который сбривает его до окончательного контура. Каждая деталь из листового металла нуждается в головке и головке, которые прикреплены к гигантским штамповочным прессам. Самый большой EMI может сжимать инструменты вместе с силой в 2000 тонн или четыре миллиона фунтов, которая создается гидравлически. Такой пресс стоит около 3 миллионов долларов и возвышается примерно на 30 футов над цехом, а также простирается более чем на 20 футов ниже.
После того, как плоскому стальному листу придана его окончательная форма, деталь измеряется электронными датчиками, чтобы убедиться, что она имеет правильную форму. Металл всегда имеет упругую отдачу, а это означает, что он не является точной копией формы в штампе. Это учтено в конструкции штампов, но обычно требуются некоторые корректировки методом проб и ошибок, прежде чем детали станут идеальными.
А поскольку киркситовые штампы изнашиваются быстрее, чем стальные, часто проводятся проверки у мастера, чтобы гарантировать, что детали остаются точными.При тщательном контроле и периодическом восстановлении инструмента набор штампов может штамповать несколько тысяч деталей.
Излишки материала удаляются с готовых штамповок с помощью компьютеризированной лазерной обрезной машины, которая продается за 1,2 миллиона долларов. После выполнения любых других операций по гибке и перфорации детали готовы для сварки в готовое тело.
EMI выполнила этот процесс для около 200 деталей, чтобы создать Chevy ’57. Единственная не переделанная деталь — это капот / противопожарная стена.Эту деталь сложно штамповать, и, согласно EMI, ее довольно легко получить из различных источников. Используя оригинальный капот — даже тот, который требует некоторого восстановления — EMI экономит деньги, а также позволяет классифицировать весь кузов как восстановленный, а не полностью новый автомобиль.
Стоимость кузова в белом цвете — 34 500 долларов. Превращение одного в полноценный автомобиль будет стоить от 70 000 до 120 000 долларов, в зависимости от того, сколько экзотических запчастей вы используете. Когда один из этих автомобилей будет собран на современном шасси, мы будем первыми в очереди на испытания.
Этот контент создается и поддерживается третьей стороной и импортируется на эту страницу, чтобы помочь пользователям указать свои адреса электронной почты. Вы можете найти больше информации об этом и подобном контенте на сайте piano.io.
Производство кузова в белом | KUKA AG
Можно ли производить автомобильные кузова с высоким качеством и экономичностью? Никто не может заморачиваться с этим вопросом. С 1950-х годов мы являемся партнером многих ведущих брендов, а также малых и средних производителей в автомобильной промышленности.Уже тогда заказчики обнаружили, что они могут положиться на наш опыт при сварке целых корпусов. Мы устанавливаем новые стандарты с нашим многоточечным позиционированием, предшественником современных приложений для роботов.
С тех пор мы в еще большей степени усовершенствовали искусство производства изделий из белого тела. В настоящее время клиенты во всем мире полагаются на наши гибкие технологические пакеты , которые можно оптимально адаптировать к выполняемой работе: для автоматизированных и масштабируемых производственных систем вплоть до индивидуально конфигурируемых производственных ячеек.
Энергоэффективность при производстве кузова в белом
KUKA работает с партнерами в автомобильной промышленности над созданием решений , которые систематически экономят энергию в производственном процессе , включая меры по минимизации потребления энергии во время простоев.
Сегодня усовершенствования роботов, используемых для классических методов производства тела в белом, приводят к более эффективному использованию ресурсов. К ним относятся, например, снижение веса робота, оптимизированное планирование пути и энергоэффективные двигатели, которые позволяют системе работать с оптимальным потреблением ресурсов на протяжении всего срока службы.Общий эффект — на более низкое потребление электроэнергии и, следовательно, более низкие выбросы CO 2 .
Кроме того, наши инструменты моделирования позволяют виртуально моделировать энергопотребление всего производственного предприятия. Это позволяет нам предлагать нашим клиентам экологически безопасные альтернативные концепции.
Технологии соединения, используемые KUKA
Отдельные прессованные детали соединяются в геометрические приспособления с использованием различных технологий:
Кузов в белом производстве: днище
Нижняя часть кузова представляет собой базовую конструкцию для всех сборочных частей, таких как двигатель и шасси.KUKA предлагает специальные решения для соединения всех основных узлов и узлов: передний пол, средний пол, задний пол, полная сборка днища кузова
Технологии: преимущественно точечная сварка и клеевое соединение.
Корпус в белом производстве: Конфигурация
При сборке кузова автомобиля необходимо выбрать подходящую технологию соединения. KUKA знает этот процесс и преимущества отдельных технологий лучше, чем кто-либо другой.Системы KUKA создают высококачественные сборки
Технологии: преимущественно точечная сварка, склеивание и лазерная пайка.
Body-in-white производство: Дополнительные детали
Двери, капоты, крылья или задние двери являются видимыми (класс A-) дополнительными деталями, с которыми конечный покупатель будет обращаться напрямую. Это означает, что они являются элементами очень требовательных к качеству. KUKA обеспечивает высокое качество обработки с помощью подходящих решений.
Технологии: преимущественно точечная сварка, подгибка и высококачественные лазерные технологии соединения
Элементы специальных систем в производстве кузовов автомобилей
Вы хотите оставаться максимально гибкими? Вы хотите производить много разных моделей на одной линии, сохраняя при этом максимально возможное качество? Мы можем предложить все подходящие системные элементы для вашей производственной среды:
- KS Framer: Во время каркаса кузова крыша и боковые стенки прикрепляются к днищу.Эта геометрическая станция имеет решающее значение, поскольку именно здесь определяется окончательная форма транспортного средства. Обрамщик KUKA KS может производить до шести различных моделей — решающий уникальный аргумент в пользу продажи.
- KS PULSE: Эта гибкая транспортная система позволяет перемещать отдельные части автомобиля с одной рабочей станции на другую. Таким образом, на одной системе можно изготовить до четырех различных конструкций кузова.
- Технология кромки: аккуратная отделка особенно важна для видимых деталей, таких как двери и дополнительные детали.Компания KUKA разработала собственные концепции и приложения, обеспечивающие особую гибкость при подшивке роликовыми кромками частей тела в белом цвете. К ним относятся системы подшивки люков на крыше и колесных арок.
- Кузовной цех Matrix: наиболее гибкое решение для производства кузовов автомобилей, где процесс соединения осуществляется независимо от поставки компонентов. Эта общая система позволяет производить бесконечное количество возможных производных.