Центробежное литье металлов
Содержание.
Центробежное литье. Этот метод, заимствованный из зубоврачебной техники, уже много десятилетий используется и в ювелирном деле. Каждое ювелирное предприятие должно использовать этот метод литья. Производство оригинальных восковых моделей и сам процесс получения по ним металлических образцов при этом виде литья открывают широкие возможности для получения высокохудожественных ювелирных изделий любой сложности. Так, например, новые центробежные литейные машины отливают 50 колец за одну заливку.
Метод центробежного литья имеет следующие преимущества:
1) возможность получения отливок по моделям любой сложной формы сравнительно простым способом;
2) значительное снижение возможности образования усадочных раковин;
3) уменьшение расхода металла из-за отсутствия прибылей, потребность в которых отпадает.
Ручное центробежное литье по выплавляемой восковой модели . Рассмотрим пример отливки массивного слона высотой 30 мм (рис. 1).
Рис. 1. Элементы формы для центробежного литья:
а — опока с отверстиями; б — восковая модель; в — проволочный каркас
Изготовление модели. Сначала делают проволочный каркас восковой модели из того же материала, который используется для литья. Вокруг этого каркаса лепят из воска модель. Для моделирования можно применять красный или голубой воск, используемый в зубоврачебной технике. Воск нагревают, и с помощью подогретого металлического шпателя производят лепку модели. Готовую модель выглаживают шабером. Для выглаживания можно очень быстро пронести модель через пламя. При этом она слегка оплавляется, и выглаживание производится легко и быстро.
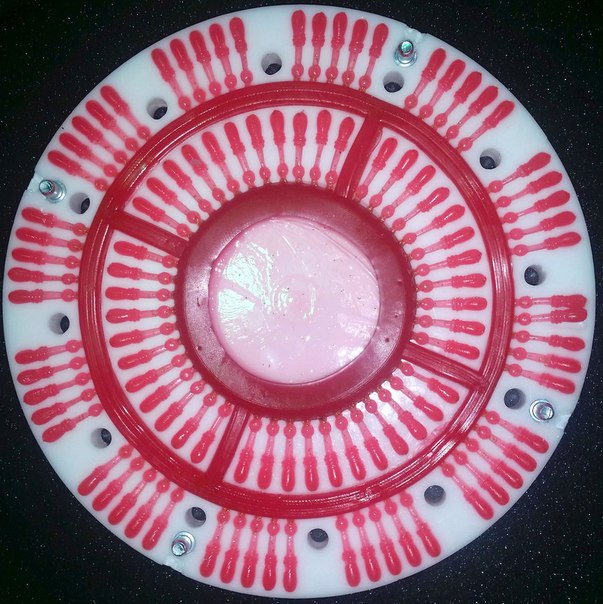
Четыре ноги слона удлиняются восковыми штифтами, сходящимися в восковом шаре. Эти штифты и шар выполняют ту же роль, что и литейные штифты.
Формовка. Готовую модель обезжиривают погружением в спирт для того, чтобы формовочная масса плотно прилегала к модели. Из воска изготавливается и сферическая стойка, в которую вдавливаются литьевые штифты, как это показано на рис. 1, б.
Расстояние между моделью и стойкой должно быть по возможности коротким, чтобы расплаву не было необходимости проделывать столь долгий путь. Модель, кроме того, должна быть так размещена, чтобы все части ее располагались в направлении литья.
В качестве формовочной массы применяют препараты, используемые в зубоврачебной технике. Формовочную массу разводят в дистиллированной воде, тщательно размешивают и вакуумированием удаляют из нее воздух. Формовочная масса должна быть жидкотекучей, сметанообразной, без комочков. Мягкой кисточкой наносят ее на модель. При этом на ней не должно появляться пузырьков воздуха. Этот первый слой припудривается, что препятствует обезвоживанию и предотвращает образование трещин при высыхании формы. По истечении 2-3 мин наносят еще слой формовочной массы и это продолжают до тех пор, пока восковую модель не покроет слой толщиной около 5 мм. Подготовленную таким образом модель помещают в опоку и заливают формовочной массой. Поверхность опоки имеет множество отверстий, благодаря которым быстрее происходит высыхание массы. При заполнении ее следует обернуть бумагой, чтобы формовочная масса не вытекала.
Сушка и прокаливание. Готовую форму не следует оставлять надолго бездействующей. Когда формовочная масса схватилась, восковую полусферу и литьевые штифты удаляют. При сушке и вытапливании восковой модели форму устанавливают в нормальной печи или в печи для эмалирования при низкой температуре так, чтобы отверстие было направлено вниз и воск мог вытекать. После медленной просушки формы производят ее прокаливание. Нагрев при прокаливании должен осуществляться медленно, в противном случае форма может разрушиться. Температуру нагрева при этом повышают до тех пор, пока литниковые каналы не будут накалены до вишнево-красного цвета.
Заливка. Нагретую форму помещают на тарелке центрифуги, и производят заливку металла, который должен быть расплавлен с небольшим количеством буры. Для ювелиров, редко имеющих дело с центробежным литьем, наиболее доступной является настольная центрифуга (рис. 2). Конструкция ее настолько проста, что ее легко можно изготовить самостоятельно. При литье изделий большого размера, к которым относится и приведенный пример, на другую тарелку ставят соответствующий противовес. Сразу же после заливки формы натягивают шнур, и труба, на которой крепится коромысло с тарелкой, начинает вращаться с большой скоростью вокруг неподвижной оси. Преимущество этого способа заключается в простоте обслуживания, большой скорости вращения и безопасности. После нескольких тренировок того же успеха можно достичь и с ручной центрифугой (рис. 3), хотя в этом случае результат зачастую зависит от субъективных причин, а опасность получения дефектов литья возрастает.
Рис. 2. Простейшая настольная центрифуга
Рис. 3. Ручная центрифуга
Литье на центробежных машинах. Рассмотрим процесс получения на центробежной машине литых медалей с двусторонним рельефом (рис. 4). Для получения восковой модели потребуется изготовить резиновую пресс-форму.
Изготовление эталона модели. Так как вулканизация резины происходит при повышенной температуре, то эталон (образец) модели нельзя изготавливать из дерева, пластмассы или легкоплавких металлов. Кроме того, при вулканизации резины выделяется небольшое количество азотной кислоты, поэтому эталон не следует изготовлять из серебра и его сплавов, а также из сплавов золота 333 пробы. Для изготовления эталона модели очень хорошо подходит сплав золота 585 пробы, особенно если поверхность его покрыта родием. Поверхность эталона необходимо тщательно обработать и отполировать. Лучше затратить несколько лишних минут на обработку этого образца, чем потом терять часы при последующей чистовой обработке партии отливок. В заключение следует обратить внимание на то, что отливка из-за усадки металла получается несколько меньшей и еще дополнительно уменьшается в размерах при обязательной чистовой обработке.
Рис. 4. Схема процесса получения изделий центробежным литьем
Изготовление эластичной пресс-формы. Для этой цели необходима опока, подобная литейной при литье в песчаные формы, с направляющими штифтами. Литьевое отверстие необязательно. Опока с направляющими штифтами укладывается на гладкую опорную плиту основанием вниз, например стеклянную, и заполняется пластилином, в который вдавливают до половины эталон модели (рис. 4, 1, 2). Устанавливают вторую опоку и заполняют ее раствором гипса. После затвердевания гипса форму переворачивают, пластилин удаляют, а эталон остается в гипсовой форме. В гипсе делают несколько углублений, которые позднее должны стать направляющими выступами резиновой формы. Сырую резину разрезают на мелкие кусочки, которыми наполняют верхнюю половину формы (рис. 4, 3). Опоки зажимают между двумя стальными пластинами, перекрывающими стенки опок.
Преимущество эластичных резиновых пресс-форм заключается в простоте их изготовления, в легком извлечении из них восковых моделей и в их долговечности.
К недостаткам следует отнести невозможность изготовления спиралевидных полостей и получения очень тонких сечений. Толщина стенки отливки не должна быть меньше 0,4 мм, так как при запрессовке воска форма должна быть зажата и поэтому стенки полуформ могут соединиться вплотную.
Другие методы изготовления эластичных пресс-форм. При изготовлении пресс-форм для простой модели достаточно поместить ее эталон между двумя резиновыми пластинами соответствующей толщины и вулканизировать их под прессом. Эталон вдавливается в размягченную резиновую массу. Недостаток этого метода заключается в том, что обе резиновые пластины <свариваются> и пресс-форму необходимо разрезать, чтобы извлечь эталон и отлить затем восковую модель
Получение восковых моделей. Для заливки воском резиновых пресс-форм применяется восковой инжектор (рис. 4, 8). В бачке находится расплавленный воск, постоянная температура которого поддерживается с помощью электронагрева. Необходимое давление в бачке создается сжатым воздухом, последний выпрессовывает воск через штуцер в литниковый канал пресс-формы. Жидкий воск можно ввести в форму центробежным методом, используя для этого металлическую центрифугу. При этом стенки резиновой пресс-формы перед каждым заполнением воском должны изолироваться эвкалиптовым маслом или смесью, состоящей из одной части воды и одной части глицерина.
Подготовка формы и заливка. Как схематично изображено на рис. 4, 9, готовые восковые модели размещаются вокруг воскового стояка, с которым они соединяются с помощью восковых штифтов. <Восковую елку> напаивают на восковой цоколь и устанавливают на резиновом основании, поперечное сечение которого видно на этом же рисунке. Далее блок восковых моделей обрабатывают так же, как это было описано выше: обезжиривают, покрывают кисточкой формовочной массой, помещают в цилиндрическую опоку и заливают ее провакуумированной формовочной массой. После затвердевания формовочной массы опоку помещают в муфельную печь (рис. 4, 10) и в течение часа при 200° С выплавляют воск. Затем температуру повышают до 1000° С и выдерживают форму при этой температуре еще 15 мин. После этого ее вынимают из печи, помещают в центробежную машину (рис. 4, 11) и производят заливку. Готовый блок отлитых медалей с литниками, полученный после выбивки опоки, показан на рис. 4, 12.
По материалам книги ‘Теория и практика ювелирного дела’, 1975 год
Следующая статья >>Центробежное литье цветных металлов в Казани
Это специфический метод формирования отливок, которое происходит в результате свободной заливки металла в специальные формы, которые затем вращаются от центробежных сил.
Используемые металлы для центробежного литья:
-
Алюминий
-
Медь
-
Чугун
-
Цинк
-
Сталь
-
Титан
-
Магний
Изделия, которые получаются благодаря этому методу
-
подшипники качения;
-
трубы разного диаметра;
-
кольца;
-
втулки;
-
бандажи для вагонов поездов и трамваев.
Примеры
Продукции
Металлообработка
Другие услуги
Наше оборудование и технологии центробежного литья
-
Специальные машины с вертикальными или горизонтальными осями, которые вращаются.
-
Для литья используются такие виды форм, как песчаные, металлические, оболочковые, а также специфические формы по выплавляемым моделям.
Особенности центробежного литья
Благодаря этому способу, получаются довольно тонкостенные изделия, которые изготавливаются из сплавов, которые отличаются низкой текучестью.
Формы для литья (изложницы) чаще всего делают таких металлов, как чугун или сталь. Когда происходит литье, снаружи формы подвергают остыванию либо воздухом либо водой.
Для более долговечной работы изложницы обрабатывают специальным теплозащитным покрытием и перед началом работы их нагревают минимум до 200 градусов.
Изложница работает за счет электродвигателя.
Технология производства
Металл, который предварительно расплавился, подвергается воздействию центробежных сил, за счет чего равномерно распределяется по стенкам формы, а затем затвердевает. Благодаря этому получаются отливки, чаще всего пустотелая, которая в последствии широко применяется в промышленности.
Преимущества центробежного литья
Повышенная заполняемость форм.
-
Отливки отличаются высокой плотностью и отличными механическими свойствами.
-
Можно получить двухслойные заготовки при очередной заливке разных сплавов.
-
Из-за отсутствия литниковой системы происходит значительная экономия сплава.
-
Заготовки труб с полостями внутри получаются без использования специальных стержней.
Минусы центробежного литья
-
Имеет место усадочная пористость и появление разных компонентов неметаллического происхождения на внутренних стенках.
-
Может случаться неточность размеров поверхностных отливок.
-
Есть риск появления некоторых дефектов, таких как газовые пузыри, продольные и поперечные трещины.
-
Преобладание склонности к ликвидации компонентов сплава.
-
Особые требования к качеству литейных форм.
Консультация
Задать вопрос
Оставьте заявку и получите расчет стоимости
Линия для центробежного литья в силиконовые формы Nicem (Италия) Б/У
Линия для изготовления отливок методом центробежного литья в в силиконовые формы пр-во Nicem S.p.a.
в хорошем состоянии, последние 5 лет не работала.
наличными дешевле на 8%
Линия для производства малогабаритных деталей методом центробежного литья из легкоплавких металлических сплавов (цинк, олово, висмут, эвтектические сплавы и свинец),
полиэфирные, эпоксидные и полиуретановые смолы с производительностью до 300 отливок в час.
Область применения линии:
Производители мебели для изготовление мебельной фурнитуры — ручки, накладки, скобы, прочее.
Литье ювелирных украшений
Производство пряжек для кожаных изделий и обуви
Производство оловянных изделий — игрушечные солдатики, миниатюры и модели автомобилей
Производство сувениров
Религиозные предметы – крестики, ладанки, прочее.
Линия состоит из:
1.Вулканизатор для изготовления форм для литья P 400 MATIC
2.Охлаждающий стол для форм с принудительной циркуляцией воздуха TRA MATIC
3.Автоматическая установка центробежного литья на 8 станций TRSE 350/8 F350
Характеристики линии.
Вулканизатор:
Диаметр формы для вулканизации — до 400 мм
Максимальное усилие закрытия — 16 000 кг
Установленная мощность — 5 кВт
Охлаждающий стол:
Емкость — 2 000 м³ / ч
Установленная мощность — 550 Вт
Напряжение трехфазное — 230/400 В
Автоматическая установка центробежного литья:
Количество отливок – до 300 отливок в час.
Диаметр пресс-форм – 350 мм.
Количество станций литья – 8 шт.
Число оборотов центрифугирования — от 0 до 1500 об / мин
Емкость плавильного котла – 350 кг.
Установленная мощность – 20 кВт
Вес машины – 1400 кг.
ЦАМ активно используют в автомобилестроении – из него отливают радиаторные решетки, корпуса карбюраторов и бензонасосов. Детали из ЦАМ можно обнаружить в пищевом оборудовании и кухонной технике – от блендера до холодильника. Пуговицы, кнопки и застежки-молнии – все это тоже ЦАМ. А также элементы часов, детали велосипедного тормоза, затворы стрелкового оружия, рыболовные катушки, ключи, игрушечные солдатики, сувениры, значки и многое другое. Даже спиннеры.
Еще из ЦАМ делают дверную фурнитуру. Это ручки, накладки, петли, детали замков, задвижек, шпингалетов, доводчиков и т. д. именно ЦАМ (а точнее – сплав ЦАМ4-1) сейчас материал №1 в производстве замочно-скобяных изделий.
Специальные способы литья — Литейное производство
Специальные способы литья
Категория:
Литейное производство
Специальные способы литья
Современная технология литейного производства стремится создать заготовки, по форме и размерам наиболее близкие к готовым деталям. Это сокращает операции механической обработки и приводит к снижению стоимости изделий.
Передовые способы литья получили общее название специальных. Они все больше распространяются в промышленности Советского Союза благодаря их высокой производительности и возможности получения с их помощью отливок, требующих меньшей механической обработки или совсем не требующих ее.
К специальным способам литья относят литье в металлические формы (кокили), центробежное литье, литье под давлением, литье по выплавляемым моделям и литье в оболочковые формы.
—
Литье в металлические формы (кокильное литье). Литейная форма изготовленная из формовочной смеси, служит для заливки один раз и при освобождении из нее отливок разрушается.
Применение для заливки металлических форм позволяет производить заливку в них многократно. Этот процесс в современных литейных широко применяется для цветных сплавов, а также для отливки деталей из чугуна и стали. В металлическую форму, имеющую внутреннюю полость, отвечающую очертаниям отливки, заливают жидкий сплав, где он затвердевает. Когда сплав в форме затвердел, ее открывают и из нее выбивают отливку. Затем форме дают несколько охладиться, снова собирают и повторяют заливку. Форма может быть из одной части (для более простых отливок), двух и более частей. Изготовляют ее из стали или чугуна.
Рис. 1. Металлическая форма для литья алюминиевых сплавов:
1 — неподвижная половина формы; 2 — подвижная половина формы; 3 — плита формы; 4 — отливка с литниковой системой
Для увеличения стойкости металлических форм в процессе работы их облицовывают специальными огнеупорными облицовками или красками.
В отличие от литья в песчаные формы процесс литья в металлические формы легче поддается механизации, снижает расход металлов на изделие. При литье в металлические формы отпадает необходимость в применении формовочной смеси; отливки по размерам получаются более точными.
Центробежное литье. Способ центробежной отливки заключается в том, что металл заливается в быстро вращающуюся еталлическую форму, изложницу, под действием центробежных сил прижимается к ее стенкам и, затвердевая, принимает цилиндрическую форму.
Способ центробежного литья наибольшее распространение находит для отливки труб и втулок.
Ось вращения изложницы может быть вертикальной или горизонтальной.
При вращении изложницы вокруг горизонтальной оси сплав в нее поступает сбоку через желоб, в изложницы с вертикальной осью вращения — сверху, непосредственно в изложницу.
Рис. 2. Формы для центробежного литья:
а — форма с вертикальной осью вращения; б — форма с горизонтальной осью вращения: 1 — планшайба; 2 —вал; 3 — форма; 4 — крышка формы; 5 — отливка; 6 — желоб
Литье под давлением. Способ литья под давлением заключается в том, что расплавленный металл заполняет металлическую форму под принудительным давлением. Создаваемым давлением на жидкий металл обеспечивается хорошая заполняемость формы. Этим методом можно получить отливки с тонкими стенками и отверстиями диаметром до 1 мм. Детали, отлитые под давлением, получаются настолько точными, что в большинстве случаев не требуют последующей механической обработки. Применяется этот способ в массовом производстве для деталей из сплавов цветных металлов.
Для создания давления, под которым металл подают в форму, применяют различные специальные машины, которые могут быть разделены на два основных типа: машины компрессорного действия, в которых давление на металл создается сжатым воздухом, и машины поршневого действия, в которых давление на металл создается поршнем.
На рис. 3 дана схема поршневой машины литья под давлением в трех положениях. Металл, расплавленный’ вне машины, заливают в камеру давления. После этого на металл давит поршень. Под действием давления опускается вниз поршень и металл через отверстия в стенке цилиндра и литниковый канал выпрессовывается в пресс-форму. При обратном подъеме поршень выталкивает остаток металла. После удаления отливки пресс-форма закрывается, и цикл повторяется.
Рис. 3. Схема поршневой машины для литья под давлением:
а — положение при заливке металла в камеру давления; б — положение при давлении на металл; в — положение при удалении отливки: 1 — камера давления; 2 — верхний поршень; 3 — форма; 4 — нижний поршень; 5 — остаток металла; 6—отливка
Литье по выплавляемым моделям (точное литье). Способ литья по выплавляемым моделям основан на применении моделей из омеги легкоплавких материалов (парафин, воск, и др.).
Для получения отливок по этому методу применяют весьма точные по размерам пресс-формы, в которых отливают под давлением восковые модели будущих отливок; из мелких моделей составляют блок, соединяя их обшей литниковой системой, изготовленной из тех же материалов. Затем блок модели облицовывают слоем краски и заформовывают, применяя для этих целей особые формовочные смеси. Полученную форму ставят в сушильный шкаф, где восковые модели и литниковая система при нагреве выплавляются. Далее форму прокаливают при температуре 800—850° и производят заливку.
На рис. 4 дана схема литейной формы, изготовленной по восковым моделям.
Рис. 4. Схема литейной формы:
1 — восковые модели; 2 — литниковый стояк; 3 — формовочный материал; 4 — опока
Литье в оболочковые формы. Литейная форма в этом процессе изготовляется по металлической модели из формовочной смеси, состоящей из кварцевого песка и искусственной смолы (4—6%). В отличие от обычной песчаной литейной формы оболочковая форма имеет сравнительно небольшую толщину (8—12 мм). Сущность процесса изготовления оболочковой формы состоит в следующем. На подогретую до 175—200° модельную плиту а особом приспособлении — формовочном бункере насыпают формовочную смесь и выдерживают некоторое время. Слой формовочной смеси, прилегающий к модельной плите, сплавляется благодаря наличию в смеси смолы и образует корочку (оболочку) толщиной 8—12 мм; лишняя смесь, в которой не произошло сплавления, сбрасывается.
Рис. 5. Схема получения оболочковой формы:
1 — бункер; 2 — модель; 3 — оболочка; 4 — отжигательная печь; 5 — металлический ящик
Модельная плита с образовавшейся на ней оболочкой помещается в печь, где в течение некоторого времени выдерживается при 200—300°. Под действием такой температуры оболочка становится прочной, ее снимают с плиты и передают на сборку. Литейная форма, как правило, состоит из двух оболочек, которые при сборке скрепляют и для заливки устанавливают в ящик. Перед заливкой, чтобы предохранить оболочковую форму от разрушения, свободное пространство в ящике засыпают землей или другими материалами.
Литьем в оболочковые формы производят отливки цветных сплавов, чугуна и стали.
Реклама:
Читать далее:
Сущность обработки металлов давлением
Статьи по теме:
Центробежное литье. Установка центробежного литья. Технология центробежного литья.
При центробежном литье сплав заливается во вращающиеся формы. Формирование отливки осуществляется под действием центробежных сил, что обеспечивает высокую плотность и механические свойства отливок. Центробежным литьем изготавливают отливки в металлических, песчаных, оболочковых формах и формах для литья по выплавляемым моделям на центробежных машинах с горизонтальной и вертикальной осью вращения.
Металлические формы изложницы изготовляют из чугуна и стали. Толщина изложницы в 1,5…2 раза больше толщины отливки. В процессе литья изложницы снаружи охлаждают водой или воздухом. На рабочую поверхность изложницы наносят теплозащитные покрытия для увеличения срока их службы. Перед работой изложницы нагревают до 200о C.
Технология центробежного литья
При получении отливок на машинах с вращением формы вокруг вертикальной оси (рисунок, позиция а) металл из ковша 4 заливают во вращающуюся форму 2, укрепленную на шпинделе 1, который вращается от электродвигателя. Под действием центробежных сил металл прижимается к боковой стенке изложницы. Литейная форма вращается до полного затвердевания отливки. После остановки формы отливка 3 извлекается. Отливки имеют разностенность по высоте – более толстое сечение в нижней части. Применяют для получения отливок небольшой высоты – коротких втулок, колец, фланцев.
При получении отливок типа тел вращения большой длины (трубы, втулки) на машинах с горизонтальной осью вращения (рисунок, позиция б) изложницу 2 устанавливают на опорные ролики 7 и закрывают кожухом 6. Изложница приводится в движение электродвигателем 1. Расплавленный металл из ковша 4 заливают через желоб 3, который в процессе заливки металла перемещается, что обеспечивает получение равностенной отливки 5. Для образования раструба трубы используют песчаный или оболочковый стержень 8. После затвердевания металла готовую отливку извлекают специальным приспособлением.
Скорость вращения формы зависит от диаметра отливки и плотности сплава, определяется по формуле:
где γ – плотность сплава; r – внутренний радиус отливки.
Центробежным литьем изготавливают отливки из чугуна, стали, сплавов титана, алюминия, магния и цинка (трубы, втулки, кольца, подшипники качения, бандажи железнодорожных и трамвайных вагонов). Масса отливок от нескольких килограммов до 45 тонн. Толщина стенок от нескольких миллиметров до 350 мм. Центробежным литьем можно получить тонкостенные отливки из сплавов с низкой текучестью, что невозможно сделать при других способах литья.
Недостатки: наличие усадочной пористости, ликватов и неметаллических включений на внутренних поверхностях; возможность появления дефектов в виде продольных и поперечных трещин, газовых пузырей.
Преимущества: получение внутренних полостей трубных заготовок без применения стержней, экономия сплава за счет отсутствия литниковой системы, возможность получения двухслойных заготовок, что получается поочередной заливкой в форму различных сплавов (сталь–чугун, чугун–бронза).
Используют автоматические и многопозиционные карусельные машины с управлением от ЭВМ.
Литьё металлов и сплавов
Литье металла является одним из самых востребованных на сегодняшний день технологических процессов, позволяющий изготовить металлические детали практически любой формы, структуры, микро- и макрогеометрией поверхности, имеющих как маленькую массу от нескольких грамм, так и большую – до нескольких тонн. Различных эксплуатационных свойств изделий можно добиться путем заливки расплавленного металла под давлением, либо естественным путем в формующую полость. Когда металл охладится и затвердеет, он примет форму той полости, с которую его залили.В настоящее время большинство деталей (до 90%), используемых в производстве, машиностроении, строительстве, приборостроении и прочих отраслях, произведены при помощи технологий литья. Метод литейного производства изделий способствует разумному распределению металла по форме, а также позволяет изменять толщину сечения на участках, испытывающих наименьшие или наибольшие нагрузки.
Металлосервисный центр «Ионмет» специализируется на специальных литейных технологиях, включая литьё в разовые неразъёмные, а также постоянные и полупостоянные разъёмные формы, и выполняет все виды работ по промышленному литью – от изготовления модельной оснастки и уникальных изделий до крупносерийных партий высокоточных деталей, не нуждающихся в дополнительной механической обработке на станках.
Технология литья выбирается в зависимости от ряда таких технологических условий, как размер, форма заготовки, литейные свойства металла и сплавов (жидкотекучести, линейной и объёмной усадки, склонности к ликвации и образованию трещин, поглощению газов, пористости), сплава, нужного качества поверхности и т.д. Также тщательно анализируются технико-экономические условия всех этапов производства.
Производственная компания «Ионмет» оказывает услуги литья из различного металла: стали, чугуна, литье из меди, алюминия и цинка, в том числе для оболочковых форм и стержней, пресс-форм для литья цветных металлов и сплавов под давлением (с ползунами, гидроцилиндрами, наклонными толкателями, вкладышами, одногнездные и многогнездные и т. д.), стержневых ящиков, сложных тонкостенных моделей, фиксаторов, толкателей, окантовочных рамок и т. п.
ВИДЫ ЛИТЬЯ
Отливание расплавленного металла в специальную форму, или кокильное литье, является одним из самых точных и качественных методов для получения отливок. В переводе с французского языка, кокиль значит скорлупа или раковина. Расплавленный металл заливается в специализированную многократно используемую форму. При помощи технологии литься в кокиль можно получить детали с плотным строением, обладающие хорошей герметичностью, хорошими физико-механическими свойствами, точными размерами, а шероховатость может быть Ra = 40…10 мкм.
Технология кокильного литья хорошо подходит для выпуска средних и мелких отливок массой не более 250 кг в условиях крупносерийного и массового производства. Обычно с помощью данной технологии производятся детали из сплавов алюминия и меди, в связи с этим главными составляющими кокиля являются вставки, полуформы, плиты, стержни и т.д.
Используя один кокиль, за год возможно произвести более 20 крупных или 400 единиц маленьких чугунных отливок, а если при использовании сплавов алюминия – до 700.
Литье под давлением (ЛПД) еще называется пресс-литьем. Это один из видов точного литья, в процессе которого высокое давление воздействует на расплавленный металл, в результате чего он заполняет разъемную форму и кристаллизуется. С помощью такого метода литься можно получить отливки деталей с тонкими стенками (до 0,5 мм) из сплавов алюминия, меди, магния, цинка. Кроме того, таким способом доступно изготовление армированных отливок.
Отливки, произведенные при помощи технологии ЛПД, имеют точные формы и высокое качество поверхности, однако существует и ряд ограничений, касающихся сложности контура, толщине стенок, химическому составу сплавов и марок. Таким образом, масса отливки может значительно варьироваться от нескольких десятков килограммов до нескольких граммов, в то время как толщина стенки изделия может быть менее 1 мм. Технология отливки деталей под давлением находит применение в массовом и серийном производстве деталей для авиационной и автомобильной отрасли, электронной и радиопромышленности.
Способ литья по выплавляемым моделям известен с древних времен. Его еще называют литьем по восковым моделям или литьем в разрушаемую форму. Это один из сложнейших и самых трудоемких видов литья. Такую технологию отливки применяли в Китае и Египте более четырехсот лет назад, а в России этот вид литья использовался для отливки пушек, колоколов и даже скульптур.
В производстве литье по выплавляемым моделям начали применять в середине прошлого века. Это было связано с активным развитием промышленности и наращивании производственных мощностей.
На сегодняшний день, методом литья по выплавляемым моделям изготавливаются средне-и малосерийные детали со сложным контуром, тонкими стенками, имеющие малую поверхностную шероховатость, минимальный припуск на обработку изделия резанием и т.д. Кроме того, значительно сокращается количество металлической стружки при изготовлении арматуры, деталей для машин, турбинных лопаток, хирургических инструментов и ювелирных изделий.
В ходе технологического процесса используются получаемые по разовым моделям неразъемные формы из керамики, где применяются жидкие смеси для формовки. Перед тем как залить расплавленный металл, из формы удаляется модель, это происходит путем выжигания, растворения или выплавления. Чтобы упрочнить изделие и удалить остатки модели, форма подвергается сильному нагреванию до высоких температур.
Предшествующее заливке прокаливание формы способствует наилучшем заполнению расплавом металла.
Процесс кронинга еще называют литьем в оболочковые формы, — является самым рациональным методом, при помощи которого из сталей , высокопрочного чугуна, жаропрочных сплавов, латуни, бронзы производятся ответственные детали. Например, рабочие и направляющие колеса, вентили, коленчатые валы и многие другие изделия.
Технология кронингового литья была запатентована еще в 1940-хх гг. в Германии И. Кронингом. В данном методе в качестве связующих элементов используются смолы. В результате, при производстве изделий с помощью литья в оболочковые, в полтора раза повышается точность и шероховатость поверхности отливок по сравнению с литьем в песчано-глинистые формы. Помимо этого, припуск на механическую обработку уменьшается в полтора раза.
Технологические свойства оболочковых форм обладают такими заметными преимуществами как прочность, податливость, газопроницаемость, негигроскопичность.
При помощи технологии центробежного литья выпускаются отливки труб, барабанов, ободов, втулок, изделий дискообразной формы, зубчатых и маховых колес, а также иных тел вращения. В пресс-форму, совершающую вращение вокруг горизонтальной, вертикальной, наклонной осей, заливается расплавленный металл, который остается там до кристаллизации.
Благодаря центробежным силам, оказывающим дополнительное воздействие на расплавленный металл, метод центробежного литья является высокоэффективной технологией производства, поскольку, помимо всего прочего, позволяет увеличить плотность металла отливки, повышает жидкотекучесть и существенно снижает расход металла.
Центробежное литье используется при производстве изделий из углеродистых, легированных сталей, чугуна, цветных сплавов, кроме того, возможен выпуск биметаллических отливок.
На каждом производственном этапе осуществляется контроль качества, на этапе выплавки ведется контроль химического состава металла.
Литьё чёрных и цветных металлов, включая литьё фасонных изделий со сложным контуром на заказ, осуществляется на основе предоставленной конструкторской документации, технического задания, моделей или пресс-форм. По индивидуальному заказу клиента возможно изготовление литых изделий в соответствии с ТУ, ОСТ, либо иными документами, которые разработаны и действуют на предприятии заказчика.
6. Центробежное литье | Материаловед
Центробежное литье – это способ формирования отливок под действием центробежных сил при свободной заливке металла во вращающиеся формы. Центробежным способом получают отливки из чугуна, стали, сплавов на основе меди, алюминия, цинка, магния, титана и др.
Формирование отливки осуществляется под действием центробежных сил, что обеспечивает высокую плотность и механические свойства отливок.
Центробежное литье осуществляют на центробежных машинах с горизонтальной и вертикальной осями вращения в металлических, песчаных, оболочковых формах и формах для литья по выплавляемым моделям.
Центробежным литьем изготавливают отливки из чугуна, стали, сплавов титана, алюминия, магния и цинка (трубы, втулки, кольца, подшипники качения, бандажи железнодорожных и трамвайных вагонов).
Масса отливок – от нескольких килограммов до 45 тонн. Толщина стенок от нескольких миллиметров до 350 мм. Центробежным литьем можно получить тонкостенные отливки из сплавов с низкой текучестью, что невозможно сделать при других способах литья.
Металлические формы изложницы изготовляют из чугуна и стали. Толщина изложницы в 1,5…2 раза больше толщины отливки. В процессе литья изложницы снаружи охлаждают водой или воздухом.
На рабочую поверхность изложницы наносят теплозащитные покрытия для увеличения срока их службы. Перед работой изложницы нагревают до 200 ºC.
При получении отливок типа тел вращения большой длины (трубы, втулки) на машинах с горизонтальной осью (рис. 6.1) вращения изложницу 1 устанавливают на опорные ролики и закрывают кожухом 2. Изложница приводится в движение электродвигателем. Расплавленный металл из ковша 4 заливают через желоб 3, который в процессе заливки металла перемещается, что обеспечивает получение равностенной отливки 5. Для образования раструба трубы используют песчаный или оболочковый стержень. После затвердевания металла готовую отливку извлекают специальным приспособлением 6.
При получении отливок на машинах с вращением формы вокруг вертикальной оси (рис. 6.2) металл из ковша 4 заливают во вращающуюся форму 1, укрепленную на шпинделе, который вращается от электродвигателя.
Под действием центробежных сил металл прижимается к боковой стенке изложницы. Литейная форма вращается до полного затвердевания отливки. После остановки формы отливка 5 извлекается.
Отливки, полученные на машине с вертикальной осью вращения, имеют разностенность по высоте – более толстое сечение в нижней части. Применяют для получения отливок небольшой высоты – коротких втулок, колец, фланцев.
Недостатки центробежного литья: наличие усадочной пористости, ликватов и неметаллических включений на внутренних поверхностях; возможность появления дефектов в виде продольных и поперечных трещин, газовых пузырей.
Преимущества центробежного литья: получение внутренних полостей трубных заготовок без применения стержней, экономия сплава за счет отсутствия литниковой системы, возможность получения двухслойных заготовок, что получается поочередной заливкой в форму различных сплавов (сталь – чугун, чугун – бронза).
Для изготовления фасонных отливок центробежный способ применяется сравнительно редко, за исключением литья тонкостенных деталей из титановых сплавов.
На рис. 6.3 показана схема изготовления фасонных отливок центробежным способом в металлических (а) и песчаных (б) формах.
Используют автоматические и многопозиционные карусельные машины с управлением от ЭВМ.
Для центробежного литья применяются машины с горизонтальной (рис. 6.1) и вертикальной (рис.6.2) осями вращения.
Рис. 6.1. Машина для центробежного литья с горизонтальной осью вращения
Рис. 6.2. Машина для центорбежного литья с вертикальной осью вращения
Рис. 6.3. Изготовление фасонных отливок центробежным литьем
Изготовление фасонных отливок центробежным литьем: а — металлическая форма; б — песчаная форма; 1 — стояк; 2 — металлическая форма; 8,4,7 — стержни; 5 — нижняя полуформа; 6 — верхняя полуформа
На рис. 6.3 показана схема изготовления фасонных отливок центробежным способом в металлических (а) и песчаных (б) формах.
Посмотрите учебный фильм «Центробежное литье».
Удачного просмотра!
Отливка центрифуг своими руками | Shane | Engineer
В этой статье я покажу, как я отлил самодельное кольцо с помощью литья по выплавляемым моделям, используя старый велосипед, превращенный в центрифугу. Центрифуга позволяет изготавливать гораздо более сложные и детальные отливки, в этой инструкции показано создание кольца, но с помощью этого процесса можно сделать почти все, что угодно маленькое и металлическое. Центрифуга очень быстро вращает форму по большой дуге, заставляя расплавленный металл попадать в форму. Это очень интересный и полезный проект.Поскольку я использовал старый велосипед, собрать центрифугу довольно легко, потребовались лишь незначительные модификации велосипеда.
Я использовал ту же печь, что и в своей отливке, для плавки металла, а также, по сути, ту же процедуру изготовления литейной формы. Хотя я еще раз подробно остановлюсь на изготовлении пресс-форм, так как есть некоторые важные отличия.
ОТКАЗ ОТ ОТВЕТСТВЕННОСТИ
При работе такой центрифуги существует огромная вероятность разбрызгивания расплавленного металла.Расплавленный металл + глаза = слепые. Наденьте защитные очки и хорошие перчатки. Также не пытайтесь отливать треснувшую форму. Силы, приложенные к форме, огромны, и если она треснет, она сломается, а затем ударится о хвост велосипеда и разлетится на множество пылающих горячих частей. Это случилось со мной, по общему признанию, это было очень круто, это все еще не то, чего вы хотите.
Зачем тратить время на создание центрифуги, если я могу просто вылить металл в формы? Причина одна:
.Вы можете получить невероятно детализированное / сложное литье, фактически, вы можете отлить что угодно с помощью центрифуги.При обычном литье вы должны беспокоиться о том, потечет ли металл, получите ли вы детали, остынет ли металл до того, как он заполнит форму и т. Д. На самом деле это не проблема центрифуги. Для сравнения посмотрите на два отливки ниже. Первый, колье, было изготовлено методом обычного литья. Красивое колье, но довольно незамысловатое. Инициалы мне пришлось выгравировать с помощью дремеля, и мне пришлось просверлить отверстие для цепного кольца, потому что я не мог получить их путем литья. Второй — кольцо, которое я сделал методом центрифужного литья.Когда он вышел из формы, на нем была каждая деталь, вплоть до крошечных царапин, которые я нанес на воске своими инструментами для резьбы. Кольцо выглядит так, как будто у него ужасная отделка, но крошечные царапины, которые вы видите, отполированы, и их можно было бы предотвратить, если бы я лучше подготовил восковой узор. Отделка воскового рисунка определяет отделку литой детали. (Хотя полировка всегда будет необходима из-за окисления и других факторов, препятствующих безупречной отделке)
Если бы я сделал ожерелье на центрифуге, мне бы не потребовалось гравировать инициалы или просверливать отверстие для кольца цепи.Это дало бы мне возможность проделать некруглое отверстие или вырезать более точные инициалы.
Необходимые материалы
Форма:
-Трубка с восковым кольцом. Я использовал воск для колец, купленный на http://www.alpha-supply.com/file-a-wax-ring-tube-c-bl.html, это были самые низкие цены, которые я когда-либо видел, и они доставляются очень быстро. По сути, это длинная трубка с отверстием в центре в грубой форме кольца. Вы отрезаете столько, сколько вам нужно, и вырезаете из него кольцо.
-Votive Candles.Это чрезвычайно дешевые «Т-образные свечи». Я использую их для изготовления литника формы и таких вещей, как камера, в которой изначально находится расплавленный металл.
-Штукатурка Парижская. Это то, из чего сделана форма. Хотя подойдет любой вид, я рекомендую «Faster Plaster». Это быстро схватывающаяся штукатурка, которую можно разводить в микроволновой печи. У нее более мелкое зерно, чем у других штукатурок, и она чрезвычайно удобна, потому что ее можно разогреть в микроволновой печи после часа схватывания. Это значительно ускоряет процесс изготовления колец.
-Что-то для вырезания из воска.Я использую точный нож с лезвием №11 и набор из 12 инструментов для резьбы по воску с ebay (5 долларов и того стоит)
-Источник тепла для плавления и соединения различных восковых компонентов (я использую зажженную свечу)
-Форма для гипса
— Лента
— Восковая бумага
— Печь / печь / решетка для выжигания воска из формы
Центрифуга:
-Старый байк, чем больше колеса, тем лучше. Я рекомендую горный велосипед вместо шоссейного, потому что там гораздо больше зазора для формы. (Шоссейные велосипеды имеют очень тонкие колеса, из-за которых на их спицах не может образоваться плесень)
— Ножовка по металлу для отрезания одной из педалей
— Гаечный ключ для демонтажа различных компонентов велосипеда
— Что-то маленькое ~ 2 фунта для стойки вес
— Доска, которую можно положить между собой и велосипедом, чтобы защитить ноги от летящего металла (подойдет фанера 2 на 2 дюйма)
— Листовой металл для изготовления держателя формы на колесе велосипеда
— Паяльная лампа для плавления металл / печь в зависимости от используемого металла (информацию о печи см. в этой статье)
-Металл для ювелирных изделий
Вырежьте восковой узор
Процесс для этого сильно различается в зависимости от конструкции кольца и сам по себе является целым изделием.Есть отличное руководство по вырезанию платинового обручального кольца, которое дает отличный обзор процесса.
http://www.instructables.com/id/Making-a-custom-Platinum-Diamond-engagement-ring./
Первый и самый важный шаг — это планирование. Вы ненавидите это делать, я ненавижу это делать, все ненавидят планирование, когда они очень рады начать проект. Но выхода нет. Спланируйте дизайн кольца. Нарисуйте его под разными углами. Нарисуйте чертежи в масштабе, чтобы вы могли получить представление о реальном размере детали.Выясните, какой размер кольца на пальце будет на нем. Убедитесь, что продумана каждая деталь дизайна. Как только вы начнете вырезать, осознание того, что вы делаете, значительно ускорит процесс, но избавит от бесконечных головных болей и половинного старта. Слишком сложно снова нанести воск после того, как вы его снимете.
Я знал, что хочу сделать кольцо, в которое каким-то образом включается калла. Я смотрел на различные кольца каллы, пока не сообразил, как должно выглядеть мое кольцо, а затем начал делать наброски.Конечный результат штурма моего наброска показан на изображении ниже. Поскольку мой окончательный дизайн был нарисован в масштабе, я, наконец, смог приступить к резьбе. Ножовкой я вырезал кусок воска для колец от длинной трубки немного шире, чем ширина кольца.
Если вы никогда раньше не вырезали воск из воска, я предлагаю вам сделать несколько «тренировочных колец», чтобы нащупать инструменты. Лучший способ вырезать из воска — начать с грубых форм кольца и время от времени улучшать его детали. Я оставляю вырезание ремешка напоследок, так как оно очень хрупкое, и его легко случайно сломать, пока вы вырезаете другие детали.Хороший способ точно передать эскиз, который вы нарисовали, на воск — это вырезать профили различных деталей кольца, вырезать их, а затем обвести их на заготовке кольца с помощью точного ножа. Это можно увидеть на фотографиях с этикетками «А» и «Б». Буква обозначает разные части / виды колец, чтобы помочь мне организовать.
Я начал с вырезания вида сбоку, чтобы все было пропорционально, затем на глаз вырезал все остальные детали одну за другой.Порядок резьбы особого значения не имеет. Я оставил все хрупкие детали напоследок, такие как полоса, тычинка в цветке, маленькая круглая деталь «бусинка» напротив листа. Просто вырезайте, пока не будете довольны своим дизайном.
Еще раз хорошенько осмотрите кольцо, чтобы убедиться, что все именно так, как вы хотите. Убедитесь, что нет неровностей и все гладко. Кольцо будет отлито в точности так, как выглядит воск, поэтому, если от ножа будут небольшие зазубрины, они останутся на последней части.Найдите время, чтобы сгладить их. Поверхностную отделку по воску выполнить намного проще, чем по металлу. После того, как вы вырежете кольцо, вы готовы к следующему шагу — добавлению литника!
Подготовьте кольцо для формы
На этом этапе вы добавляете так называемый литник к вашему только что вырезанному кольцу (или какому-либо другому, что вы сделали). Когда вы центрифугируете отливку, ваша форма имеет две камеры, одна из которых открытая, как чаша (называемая тиглем), — это то, куда вы изначально помещаете расплавленный металл.На боковой стороне первого тигля есть небольшое отверстие, ведущее в полость формы, образованную кольцевым шаблоном. Отверстие, соединяющее их, сделано так называемым литником. Когда изделие отлито, металл течет из тигля через это отверстие в узор. Поскольку любые углубления в форме создаются путем вырезания их из воска, закрепления их в гипсе и последующего выжигания, мы должны сделать так называемый литник и прикрепить его к нашему кольцевому образцу.
Обычно, когда используются двухкомпонентные формы для центрифужного литья, есть форма, которая прижимается к тиглю (которая представляет собой полость, в которую помещается расплавленный металл). Причина использования двухкомпонентной формы — это позволяет повторно использовать тигель, сокращая затраты. , размеры пресс-форм и т. д.В основном это позволяет производить более крупные объемы. Поскольку я делал только одно кольцо, а создание системы форм из двух частей значительно усложнило бы мою конструкцию, у меня есть узор, литник и тигель как одно целое.
Используя воск из вотивных свечей, сначала вырежьте две маленькие «палочки» размером примерно 1/8 дюйма и полдюйма длиной. Я использовал две, потому что хотел убедиться, что есть путь для выхода воздуха, но мне сказали этот будет очень хорошо работать для такой маленькой детали. Я обрезал концы под углом, чтобы они хорошо стыковались с кольцом.Используя горячий точильный нож, нагретый в пламени свечи, расплавьте концы палочек, а затем приклейте их к кольцу, пока их концы еще расплавлены. Повторно нагревая лезвие, расплавьте воск вокруг области, где восковая палочка прикрепляется к кольцу, чтобы убедиться, что есть хорошее соединение без зазоров. (См. Первое изображение ниже)
Затем снимите фитиль с новой свечи и вырежьте две выемки в верхней части, соответствующие размеру двух палочек, прикрепленных к кольцу. Вставьте две «палочки», затем с помощью горячего точильного ножа расплавьте воск вокруг них, чтобы они приклеились к свече.(См. Второе изображение ниже) На втором изображении вы можете видеть, что нижняя поверхность тигля плоская и держит кольцо параллельно столу. Плоская поверхность необходима для прикрепления тигля к форме на следующем этапе.
Сделать форму
Пришло время изготовить форму. Я нашел небольшой прямоугольный пластиковый контейнер, в который моя сборка формы / литника / тигля удобно поместилась, чтобы использовать ее в качестве гипсовой формы. Я хотел, чтобы форма была многоразовой, и поскольку в ней не было сквозняков, было бы невозможно извлечь штукатурку после того, как она затвердела, не сломав пластиковый контейнер или форму.Чтобы решить эту проблему, я выложил форму вощеной бумагой. Вощеная бумага препятствовала прилипанию гипса к стенкам контейнера и давала мне что-то натянуть, чтобы вытащить гипсовую форму. Это было немного утомительно, и с тех пор я сделал форму со съемными сторонами, чтобы избежать этого шага. Как вы можете видеть на изображении ниже, я сложил бумагу, чтобы она хорошо подходила, а затем приклеил ее по бокам изолентой. (на нескольких изображениях вы можете увидеть картон под вощеной бумагой, я сделал это изначально, но понял, что в этом нет необходимости, и прекратил его использовать).
Следующее, что нужно было сделать, это прикрепить нашу кольцевую сборку к форме, чтобы она не двигалась при заливке гипса. Я прикрепил кольцевую форму к дну контейнера горячим клеем.
Теперь просто перемешайте гипс и вылейте его в форму. Я вылил пластырь примерно на 1/3 дюйма выше, чем кольцо. Я использовал ручной массажер сбоку от формы, чтобы избавиться от пузырьков воздуха. У меня был пластырь, который можно разогреть в микроволновой печи, поэтому после первоначального отверждения в течение часа я мог удалить его с плесень (что очень важно.Обработка его в микроволновой печи разрушит вашу форму и может вызвать небольшой «взрыв», так как давление захваченного водяного пара будет сброшено) и микроволновую печь в течение одной минуты 9 раз на самой низкой настройке (обычно литник и тигельная форма сделаны из вотива. свечи выпадают в микроволновке из-за низкой температуры плавления). После этого я отнес его к грилю и, начиная примерно через час на слабом огне, поднял температуру до максимума. Это займет много времени, но в конце концов вы увидите, как синий воск начинает капать из отверстия литника и выгорать.После того, как он начал это делать, я оставил его еще на полтора часа, пока не перестал дым.
Вы можете сжечь воск в духовке, это сделал я. Один раз. Если у вас нет духовки с особенно хорошим внутренним вытяжным вентилятором или внешней духовки, у вас будут проблемы с дымом и едким запахом гари воска в вашем доме по крайней мере в течение дня
Как только вы все сожжете, у вас будет что-то вроде этого.В приведенной ниже форме есть этот странный двухкомпонентный тигель, потому что это была экспериментальная конструкция формы, которая не имела никакого значения. (Большая сторона принимает металл, маленькое отверстие — выпуск воздуха)
Строительство центрифуги
Когда я впервые задумал этот проект, я знал, что мне придется построить центрифугу, но я не знал точно, как я собираюсь это сделать. После того, как я сел и нарисовал несколько рисунков, у меня был дизайн из дерева, у него был цепной привод, который вращался с помощью рукоятки.Глядя на дизайн, я понял, что он очень похож на заднюю часть велосипеда. Вместо того, чтобы пережить кошмар сборки цепного привода с нуля, я решил заменить старый велосипед.
В итоге я отрезал одну из педалей (левую, если вы сидите на велосипеде), чтобы велосипед мог лежать боком на земле. Удаление тормозов, передней вилки и руля (хотя я оставил задний переключатель передач прикрепленным к переключателю для переключения передач), шины и сиденья.По сути, я разделил его до рамы с одной педалью, задним колесом, задним переключателем и задним переключателем.
Я построил держатель формы из листового металла, который у меня был. На самом деле не имеет значения, как это делается, пока форма надежно удерживается между спицами (хотя лента не рекомендуется, форма сильно нагревается, и лента плавится / сгорает / выходит из строя. Убедитесь, что при установке формы между спицами и колесом повернут так, чтобы оставался зазор и он не сталкивался ни с одной частью велосипеда.
Последним этапом подготовки центрифуги является добавление противовеса. Это зависит от формы, я использовал пластиковую коробку с болтами. Я мог добавлять или снимать болты в зависимости от того, насколько тяжелой была моя форма. Я закрепил противовес малярной лентой.
Cast Something
На данный момент все, что было сделано. Кастинг что-нибудь! Процесс сотворения чего-либо довольно прост:
- Наденьте модные защитные очки
- Осторожно нагрейте форму, затем установите форму в центрифугу (осторожно обращайтесь с ней — очень жарко!)
- Расплавьте металл в печи или тигле с помощью паяльной лампы, если это возможно.
- Поместите металл в тигельную сторону формы, держите на нем горелку, пока не будете готовы вращать форму, чтобы она не затвердела
- прислоните доску к вашим ногам между центрифугой и вами, чтобы летящие куски металла не задели ваши ноги (поверьте мне, металл действительно отбрасывается). Я также рекомендую носить брюки, длинные рукава и перчатки.
- снимите резак и сразу же быстро проверните педали. Я продолжаю крутить педали как минимум 45 секунд, чтобы дать металлу время застыть
- Оставьте форму на час, затем откройте ее
Вот и все.Полировка дремелем действительно подчеркивает блеск и избавляет от мелких дефектов поверхности. Надеюсь, эта статья была информативной и полезной!
Центробежное и вакуумное литье ювелирных изделий: пошаговое руководство
IGS может получать комиссию за привлечение клиентов от компаний, перечисленных на этой странице. Учить больше.Почему стоит попробовать восковое литье?
Литье из воска — это техника, используемая художниками для создания больших и малых скульптур. Восковая модель объекта используется для создания слепка.Затем расплавленный металл можно вылить в форму для создания скульптуры. Этот метод использовался тысячи лет в культурах по всему миру. Ближе к нам по времени стоматологи в 1940-х годах использовали эту технику для создания изделий для стоматологической работы. Потребность ювелиров в создании небольших ювелирных изделий привела к тому, что многие адаптировали методы воскового литья из стоматологии для изготовления ювелирных изделий.
Ювелиры могут найти восковое литье очень полезным по ряду причин. С помощью этого метода легче создать индивидуальные настройки и крепления для камней произвольной формы, а также защитные конструкции для мягких драгоценных камней, таких как диоптаза и опал.(Варианты — это хорошо. Обертывание лицевой проволокой камней через некоторое время может утомить). Ювелиры также могут создавать резиновые формы для оригинальных изделий и использовать их для изготовления восковых моделей для копий.
Возможно, лучшее в восковом литье — это то, как оно может помочь раскрыть творческий потенциал ювелира. Воску можно придать практически любую форму, которую только можно вообразить. Также легко экспериментировать с различными текстурами и украшениями. Если ювелиры не добиваются желаемых результатов, просто приложите немного тепла, и они вернутся к совершенно новой рабочей поверхности.Возможность настраивать индивидуальные настройки воскового литья также означает, что ювелиры не ограничены в использовании купленных форм для установки цен.
Эти протезы были созданы студентами Школы стоматологических технологий, Военно-морской учебный центр, Фаррагут, штат Иллинойс, в 1945 году. Среди представленных здесь частей есть восковая резьба. «09-8018-3» от Navy Medicine. Всеобщее достояние.
Существует множество методов литья из воска. При литье в песчаные формы в качестве материала формы используется песок. Литье из туфа включает в себя вырезание формы из туфа, мелкозернистого вулканического пепла.Литье каракатицы включает вырезание формы или вдавливание модели в каракатицу. Литье водой — интересный способ создания объектов произвольной формы. Расплавленный металл медленно выливается в воду и остывает, приобретая необычные, случайные формы, которые можно использовать для изготовления форм. Литье с водяным паром использует силу пара, чтобы заставить металл погрузиться в форму.
В этой статье основное внимание уделяется центробежному и вакуумному литью с использованием метода выплавляемого воска (так называемого, потому что восковая модель разрушается или теряется при литье металла).
Инструменты и принадлежности для центробежного и вакуумного литья
Есть два типа людей, которые прочтут следующий список: те, кто решит, что эта техника не для них, и те, кто попытается заполучить средства на учебу своего ребенка, чтобы получить здесь все.
- Модель или воск для моделей . Модель или выкройку можно сделать из воска или любого полностью горючего материала. Ключевые слова здесь «полностью горючие». Материал модели, который оставляет какие-либо остатки, вызовет проблемы с литой частью, от неприглядных пятен до потери деталей.Удивительное разнообразие типов воска доступно в магазинах и в Интернете. Есть воск, который можно подпиливать, и водорастворимый воск для полых форм. Восковая проволока бывает круглой, полукруглой, квадратной и треугольной формы. Вы можете найти восковые листы и воск для литников. Воск — самый универсальный из всех материалов для моделирования, он не так токсичен и вреден, как другие варианты.
- Воск литниковый . Рекомендуется диаметр 3/8 дюйма для главного литника и меньшие калибры для крепления моделей к главному литнику.
- Основания литников и колбы . Купить базы и фляги> в комплекте. Колбы должны иметь достаточно большой диаметр, чтобы обеспечить зазор 3/8 дюйма между моделью и стенкой колбы, и быть достаточно высокими, чтобы покрыть модель как минимум 1/2 дюйма паковочной массы. Если не обеспечить адекватных вложений, форма может взорваться и разрушить модель. (Выдувание при использовании центробежной машины может привести к выбросу большого количества расплавленного металла по вашей мастерской. Удар всего одного кусочка расплавленного металла, вероятно, гарантирует, что вы не забудете вложить достаточно средств, чтобы покрыть модель в следующий раз).
- Инвестиции . Поставщики осуществляют инвестиции в малых и больших количествах. Однако инвестиция — это водный магнит, поэтому покупайте только то, что собираетесь использовать в течение шести месяцев или около того. Имейте в виду, что большие инвестиции высушат ваши руки. (Так что купите хороший лосьон для рук).
- Масштаб . Лабораторные весы для взвешивания металла, воска и паковочной массы.
- Смесительное оборудование . Гибкая резиновая миска для смешивания, совок и что-то для перемешивания паковочной массы.Рекомендуется ручной миксер только с одним венчиком. Электрический миксер может вызвать пузыри в паковке, чего следует избегать. Внимание: никогда не используйте повторно миксер для паковочной массы для приготовления пищи, потому что паковочная масса никогда не будет полностью удалена с миксера.
- Дебубблизатор . Вибрирующая платформа для удаления пузырей в модели и паковке.
- Обжиговая печь с пирометром . Требовалось сжечь модель. Печь с пирометром сразу покажет точную температуру в печи.
- Горелка . Кислородно-ацетиленовая горелка для плавки металла. Наконечник «бутон розы» используется для более быстрого плавления металла.
- Средства защиты глаз . Найдите достаточно темные очки, чтобы защитить ваши глаза от яркого света фонарика и при этом позволить вам хорошо видеть, чтобы перемещаться по мастерской.
- Защита рук . Термостойкие перчатки для извлечения горячих колб из печи и щипцы для работы с горячими колбами.
- Тигель . Возьмите достаточно большой тигель, чтобы в нем поместилось достаточно расплавленного металла для отливки.Если металла недостаточно для заполнения формы, вы потеряете отливку.
- Штанга для перемешивания . Я использую угольный стержень для перемешивания металла, чтобы убедиться, что он полностью расплавлен, и для удаления примесей из расплава.
- Флюс . Рекомендуется Twenty Mule Team Borax.
- Ведро на пять галлонов . После заливки колбы наполнить водой для закалки.
- Огнетушитель .
И последнее, но не менее важное, литейная машина.
«IMG_0853», машина центробежного литья, StonesoftheEarth, имеет лицензию CC By 2.0
Центробежные и вакуумные литейные машины
Центробежная разливочная машина
использует вес металла и центробежную силу (даже если только кажущуюся силу) для заполнения формы. Машина для вакуумного литья использует вакуум для всасывания расплавленного металла в форму.Сила необходима для преодоления поверхностного натяжения расплавленного металла. В противном случае металл превратится в каплю и просто останется там.Если ваша модель хрупкая, потребуется больше силы, чтобы протолкнуть расплавленный металл в крошечные участки формы. Слишком небольшое усилие — форма не заполняется должным образом. Слишком большое усилие — риск выдувания формы. Идея состоит в том, чтобы иметь устойчивое постоянное давление, толкающее или втягивающее расплавленный металл в форму.
Центробежная машина должна быть надежно закреплена болтами на ровной поверхности с защитным ограждением вокруг нее. Можно использовать металлический таз для стирки или барабан от сушилки для белья. В ограждении не должно быть отверстий для предотвращения утечки расплавленного металла в случае выброса.
Вы можете рассчитывать хотя бы на один выброс. Продувки могут значительно повысить вашу осведомленность о безопасности.
Центробежная машина должна находиться на удобной рабочей высоте. Помните, что вы будете работать с горячими колбами, расплавленным металлом и пылающим факелом. Вы не хотите принимать неудобные и небезопасные позы. Сделайте все необходимое, чтобы сделать этот процесс максимально простым.
Каждая колба, используемая при центробежном литье, должна быть сбалансирована.Выполните следующие действия:
- Поместите залитую, но не сгоревшую колбу в центробежную машину.
- Вставьте тигель в форму и поместите предварительно отмеренный металл для этой колбы в тигель.
- Ослабьте центральную гайку, чтобы рычаг качнулся.
- Отрегулируйте противовесы так, чтобы при легком прикосновении рука двигалась вверх или вниз.
- Убедитесь, что вы затянули гайку груза и центральную гайку. Проверьте их еще раз, а затем еще раз, чтобы убедиться.Если вы работаете с другими, даже если вы наблюдаете, как они затягивают гайки, проверьте их сами.
Если вы понимаете физику центробежного процесса, вы поймете необходимость обеспечения безопасности работы.
Установки для вакуумного литья дорогие. Если вы можете себе это позволить, обязательно купите его. (Одно из преимуществ вакуумного литья заключается в том, что вам не нужно выполнять утомительную процедуру балансировки, описанную выше). Доступны отличные пакеты машин и принадлежностей.
Процедуры центробежного и вакуумного литья
Различия между центробежным и вакуумным литьем будут объяснены в пошаговом руководстве ниже. В противном случае эти шаги применимы к любому методу.
- Сделайте или купите восковую модель или выкройку.
- Проверить модель на наличие дефектов и при необходимости отремонтировать. Чем более закончена модель, тем меньше потребуется очистки готовой отливки. С модельными материалами работать легче, чем с металлом.
- Взвесьте и отметьте резиновые основания литников.
- Закрепите воск для дерева на основании литника. Расплавьте воск там, где встречаются воск литника и основание литника. Можно использовать спиртовую лампу и большую швейную иглу, воткнутую в конец деревянного дюбеля. Нагрейте иглу и используйте ее, чтобы растопить и нанести воск. Также доступны коммерческие восковые ручки.
- Установите на модель небольшой литник, желательно в таком месте, которое не будет видно на готовой детали. Поместите галстук из воска там, где литник прикреплен к модели.
- Прикрепите модель с литниками к дереву.Делайте литник модели как можно короче. Модель с литником можно прикрепить с помощью «липкого воска» или снова использовать горячую иглу. Поместите полоску из воска в место пересечения литника модели и дерева. При установке нескольких моделей начните с верхней части литника дерева и двигайтесь к основанию. Размещайте модели на расстоянии не менее 1/8 дюйма друг от друга. Проверьте зазор между моделями и стенкой колбы.
- Соберите колбу и основание и еще раз проверьте зазоры. Модели должны располагаться на расстоянии не менее 3/8 дюйма от стенки колбы.Оставьте не менее 1/2 дюйма для паковочной массы, чтобы покрыть модель.
- Снимите колбу с основания и взвесьте литниковое основание. Вычтите вес основания литника, и вы получите вес ваших моделей и литников. Чтобы подсчитать, сколько металла потребуется, вам придется немного посчитать. См. «Как рассчитать количество литейного металла» ниже. Отметьте колбу, чтобы отличать ее от других.
- Снова соедините колбу и литниковое основание. Еще раз проверьте свои зазоры. ( Для литья под вакуумом нарежьте соломинки содовой на 1/2–3 / 4 дюйма короче высоты колбы. P один конец проушины с воском и закрепите его на боковой стенке колбы с помощью шпильки и запечатайте конец. Это увеличивает вакуум, создавая канал в форме, где соломинки выгорели. После того, как колба вставлена, удалите заклепки ).
- Инструкции по смешиванию паковочной массы прилагаются к паковочной массе. В общем, налейте воду в резиновую миску для смешивания. Затем добавьте вложение. Смешайте паковочную массу до консистенции теста для блинов.Убедитесь, что нет комков. Если вы положите паковочную массу в миску, а затем добавите воды, у вас появятся комочки.
- Вибрируйте миксерную чашу на вибрирующей платформе. ( Если вы используете , используя a вакуум машина , поместите миксерную чашу на паковочный стол. Паковочная масса «закипит» и станет пенистой — это воздух, вытянутый из паковочной массы под действием вакуума.Пена немного утихнет. Пылесосьте около полутора минут. O или вакуумная очистка вызовет пузыри в паковке ) .
- Наклоняя колбу, медленно вылейте паковочную массу в колбу, пока она не наполнится. Если у вас недостаточно смешанных вложений для полного наполнения колбы, вылейте ее и смешайте больше вложений. Использование двух наливов для наполнения колбы просто вызывает проблемы. ( ) Если вы ‘re собираетесь лить в вакууме, убедитесь, что колба герметично закрывается. C Убедитесь, что на ободе колбы нет паковок. Небольшой канал можно выцарапать в паковке там, где он встречается со стенкой опоки ) .
- Вибрируйте колбу на вибрирующей платформе или пропылесосьте колбу так же, как и миксерную чашу. Встряхивая колбы, постучите по бокам металлическим стержнем или отверткой. Это поможет избавиться от пузырей. (Если вы литье под вакуумом, для колб потребуется воротников из жесткого гибкого материала.Хомуты предохраняют инвестиционный стол от разлива по всему инвестиционному столу, когда он вспенивается. Воротник удерживается на резинке. Пылесосить около полутора минут ) .
- Позвольте инвестициям установиться. Сделайте отметку о личности на инвестиции.
- Снимите резиновый литник вращающим движением.
- Перед тем, как поместить опоки в печь, найдите способ убрать расплавленный воск со дна печи. Без этой защиты печь долго не прослужит.Хорошо подойдет керамическая плитка с бороздками для удерживания воска до его испарения. Вы можете удалить воск с колб, поместив их в тостер, установленный на температуру плавления воска. Не делайте этого в кухонной духовке! Подставьте под колбы поддон для сбора расплавленного воска.
- Удалите засохшую паковочную массу с внешней стороны опок и с кромки, если вы выполняете вакуумное литье. Поставьте колбы в холодную печь. Убедитесь, что между колбами есть свободное пространство.
- Следуйте «графику выгорания» в зависимости от размера колб.Купите и изучите хорошую книгу по кастингу. Я рекомендую Practical Castin g: Studio Reference от Тима МакКрайта.
- У вас должны быть емкости с отвешенным металлом для каждой колбы. Используйте металл, который не плавился с момента получения с завода, или металл, который плавили только один раз (например, старые кнопки и литники от предыдущих отливок), плюс не менее пятидесяти процентов по весу нового металла. Литые литники и кнопки можно дважды переработать для литья металла.
- Выключите печь по окончании цикла выгорания.Дайте колбам остыть до температуры на 300–400 градусов ниже точки плавления используемого металла.
- Флюс и разогрейте тигель.
- Поместите горячую колбу в центробежную машину, проверяя выравнивание. Вставьте тигель в отверстие колбы.
- Расплавьте металл. Используйте палочку для перемешивания, чтобы проверить расплав на наличие комков. Сдвиньте любые примеси на край тигля, наиболее удаленный от горловины колбы. Не кипятите металл. Если расплав закипает, добавьте в смесь немного флюса и снова включите горелку, пока металл не остынет.
- Когда металл расплавится, снимите горелку и плавным движением отпустите литейный рычаг. Дайте машине перестать вращаться и снимите фляжку с машины. Ставьте еще горячую колбу на огнеупорную поверхность, пока она не остынет до тускло-красного цвета. Затем охладите колбу в ведре с водой или дайте ей постоять, пока вы наливаете другие колбы. ( Для литья под вакуумом, выньте опоку из печи и поместите ее застежкой на литейную площадку. Включите вакуум и убедитесь, что у вас есть хорошее уплотнение между опокой и разливочной площадкой.Когда будет достигнут самый высокий вакуум, расплавьте и разлейте металл. Оставьте вакуум, пока металл не затвердеет. Отложите колбу в сторону для охлаждения, закалки или продолжения литья ) .
- Используя щипцы, охладите фляги в ведре с водой, покачивая им взад и вперед. Вода удалит отливки из паковочной массы. Подождите немного, прежде чем забрать отливки. Они все еще будут горячими.
- Теперь у вас есть уродливый кусок металла, покрытый паковочной массой и черным оксидом.Очистите отливки зубной щеткой и удалите как можно больше паковочной массы.
- Вырежьте отливки и их литники из дерева. При необходимости уберите больше вложений. Вырежьте литники из модели. Очистите место, где был прикреплен литник. Нагрейте и протравите отливки. Обработайте детали пайкой, опиливанием и полировкой.
Готово!
Как рассчитать количество литого металла
Количество металла, необходимое для заполнения формы = (W x SG w x SG м ) + 15.55 грамм.
Когда:
- W = Граммы воска или другого модельного носителя.
- SG w = Удельный вес воска или другой модельной среды.
- SG m = Удельный вес металла, используемого для литья.
В следующем примере в качестве модельного материала используется воск, а в качестве металла — серебро.
Допустим, вес основания литника, модели и литников составляет 325 граммов. База весит 144 грамма. 325 граммов минус 144 грамма равняются 181 грамму восковой модели и литников.
Воск имеет удельный вес 1. Стерлинговое серебро имеет удельный вес 10,4.
Итак, 181 грамм x 1 x 10,4 = 1882,4 грамма серебра.
Чтобы обеспечить достаточное количество металла для заполнения формы, добавьте 10 центов металла для пуговицы. Один пеннивейт (dwt) равен 1,555 грамма, так что 10 пенни равняются 15,55 грамму.
1882,4 + 15,55 = 1897,95 грамма. Чтобы наполнить колбу, округлите полученное количество до 1898 граммов стерлингов.
Соблюдайте меры предосторожности при изучении центробежного и вакуумного литья
Вы будете работать с пылающими факелами, расплавленным металлом и горячими колбами.В вашей мастерской будет температура, которая может серьезно повредить любой материал. Найдите время, чтобы узнать об инструментах, оборудовании, материалах и процедурах, которые вы будете использовать.
Самостоятельное центробежное или вакуумное литье несложно. Однако, как и в случае с любым новым опытом, у него есть кривая обучения. Спланируйте размещение оборудования и выполните пробный прогон один или два (или двенадцать) раз, пока не почувствуете себя комфортно с процедурами. Держите под рукой огнетушитель.
Если вы проводите литье в помещении, вам потребуется отличная вентиляция. Достаточной вентиляции здесь не будет. Пары горелки и парафин ядовиты. Другие материалы модели могут быть хуже. Помните о своем здоровье и здоровье других людей.
Последнее предупреждение: не выбрасывайте инвестиции в канализацию. Он застынет как бетон. В конце концов, ты отправишь детей водопроводчика в колледж.
«180320081781.jpg», эксперименты по вакуумному литью, компания IK’s World Trip находится под лицензией CC By 2.0
Что такое центробежное литье и как оно работает?
Обзор
Центробежное литье — это процесс, позволяющий получать компоненты с высокой прочностью материала. В результате это технология, которую выбирают для таких применений, как корпуса компрессоров реактивных двигателей, гидроизоляционные кольца, многие продукты военного назначения и другие высоконадежные области применения. Это также оказалось рентабельным средством получения сложных форм с меньшими требованиями к механической обработке и более низкими производственными затратами по сравнению с поковками и фабрикациями.
В процессе центробежного литья расплавленный металл заливается в предварительно нагретую прядильную головку. Матрица может быть ориентирована либо по вертикальной, либо по горизонтальной оси в зависимости от конфигурации желаемой детали.
При вращении формы во время заливки расплавленного металла центробежная сила распределяет расплавленный металл в форме под давлением, в 100 раз превышающим силу тяжести. Комбинация этого приложенного давления и инженерной механики контролируемого затвердевания и вторичного рафинирования позволяет получать компоненты высочайшего качества.
Когда матрица начинает заполняться, более плотный расплавленный металл прижимается к стенке прядильной матрицы. Направленное отверждение прочного металла происходит от O.D. по направлению к каналу, в то время как менее плотный материал, включая примеси, «всплывает» к внутреннему диаметру.
После затвердевания отливки деталь удаляют из матрицы, а остаточные загрязнения в внутреннем диаметре. подвергаются механической обработке, в результате чего получается бездефектная конструкция без полостей и газовых карманов.
Типы центробежного литьяСуществует два типа процессов центробежного литья — вертикальное и горизонтальное.Кроме того, некоторые производители предлагают формование, близкое к чистому, которое сочетает в себе преимущества центробежного литья с формированием внешнего диаметра, возможно, даже с готовой деталью отливки по выплавляемым моделям.
Вертикальное центробежное литье
Некоторые производители производят центробежные компоненты, в том числе некоторые с внешним диаметром, в фильерах, вращающихся вокруг вертикальной оси. Эти вертикальные отливки могут обеспечить такой внешний диаметр. формование путем вставки графитовых, песчаных или керамических форм в матрицу, что приводит к значительному сокращению постобработки, такой как механическая обработка или изготовление.
Детали на внешней поверхности отливки могут быть изменены по сравнению с истинной круглой формой путем введения фланцев или выступов на внутренний диаметр кристаллизатора. Готовая деталь не обязательно должна быть симметричной, но в некоторых случаях литейная форма поддерживает баланс при прядении.
Внутренний диаметр и, следовательно, толщина стенки отливки зависят от количества металла, залитого во вращающуюся форму, и количества обработанного металла. При вертикальной отливке высота отливки обычно меньше, чем в два раза ширины.
Посмотрите наше видео о процессе вертикального центробежного литья здесь .
Горизонтальное центробежное литье
Некоторые центробежные литейные машины производят только горизонтальные отливки, в которых матрица вращается вокруг горизонтальной оси. Это рентабельный метод производства высококачественных трубчатых компонентов.
Этот процесс особенно подходит для длинных цилиндрических деталей, длина отливки которых значительно превышает их внешний диаметр.Сюда входят прямые трубные секции, длинные цилиндры с концевыми фланцами или короткие детали, такие как кольца или фланцы, где из прямого цилиндра можно эффективно обрабатывать несколько деталей.
394Длинная стальная литейная форма вращается с высокой скоростью, когда она расположена горизонтально. Скорость вращения пресс-формы высокая, чтобы компенсировать гравитационные силы. Крышки закреплены на каждом конце формы, чтобы удерживать расплавленный металл, а разливочная воронка используется для доставки металла заданного веса внутрь формы.
Как и при вертикальном литье, внутренний размер формы определяет внешний диаметр. размер детали, а количество металла, залитого в форму, определяет внутренний диаметр. размер.
Посмотрите наше видео о процессе горизонтального центробежного литья здесь.
Вакуумное центробежное литье
Центробежное литье в вакууме используется, когда детализация детали и контроль воздействия атмосферы имеют решающее значение, поскольку некоторые сплавы, включая суперсплавы никель-кобальт, реактивны по отношению к кислороду.Помимо преимуществ литья в вакууме, достигается высокая целостность металла, присущая центробежному литью, включая направленное затвердевание, отсутствие пористости и формирование сетки. Вакуумное центробежное литье обеспечивает очень высокую надежность изделий, часто используемых в аэрокосмической и военной промышленности.
Направленное отверждение
Ключевой динамикой центробежного процесса является то, что отверждение происходит в одном направлении.Внешний размер и форма отливки определяются поверхностью штампа (формы), которая действует как холод, инициируя затвердевание. С помощью экзотермических материалов, которые могут быть добавлены к I.D. после заливки вместе с радиатором формы на внешнем диаметре градиент температуры приводит к направленному отверждению от внешнего диаметра. к I.D. Жидкий металл постоянно доступен для подачи в отливку, обеспечивая прочный металл до I.D. если окончательно затвердеет.
Наружная обработка обычно выполняется для удаления шероховатости поверхности и сохранения соосности с отверстием.Однако в некоторых приложениях внешний диаметр в литом корпусе поверхность приемлемая. Любая усадка центробежного механизма происходит на внутреннем диаметре, который всегда удаляется механической обработкой.
Когда выбирать центробежное литье
- Симметричные детали, которые могут вращаться вокруг оси.
- Статические свойства литейного материала недостаточны.
- Усадка по средней линии является проблемой при использовании других процессов литья.
- Limited I.D. Особенности.
- Крупные детали, до 135 000 фунтов./ 61 350 кг и более.
- Высокие затраты на обработку наружного диаметра. формирование.
- Когда требуется, сплав не будет работать или непригоден для других процессов.
- Требуется однородная зернистая структура.
- Требуется сохранность размеров.
Более пристальный взгляд на процесс отливки металла
Отливка металла — это процесс изготовления, при котором расплавленный металл заливается в специально разработанную форму, которая оставляет отрицательное впечатление от желаемой детали или продукта.После того, как металл остынет и затвердеет внутри формы, он сохраняет форму и размер конструкции формы.
В следующей статье мы даем обзор процесса литья металла, описывая различные доступные методы, используемые материалы и факторы, которые следует учитывать при планировании проекта.
Типы методов литья металловМетоды литья металлов можно разделить на две группы: одноразовые и многоразовые формы. Ниже мы описываем разницу между ними и приводим примеры процессов.
Процессы литья металла с использованием сменных формФормы одноразовые — это формы одноразового использования, разрушаемые в процессе литья. Некоторые из методов литья, в которых они используются, включают:
- Литье по выплавляемым моделям: Литье по выплавляемым моделям — также называемое литьем по выплавляемым моделям — использует керамические формы, изготовленные для формирования керамического материала поверх восковых моделей, полученных литьем под давлением. К концу процесса литья и восковая модель, и керамическая форма разрушаются, образуя отливку.
- Литье в песчаные формы: Литье в песчаные формы — один из наиболее часто используемых методов литья металлов. Он использует плотно утрамбованный песок для формирования формы, которую позже взбалтывают, чтобы удалить готовую отливку.
- Литье в гипсовую форму: Литье в гипсовую форму аналогично литью в песчаные формы. Тем не менее, он использует гипс, а не песок, чтобы создать форму для отливки.
В отличие от одноразовых форм, многоразовые формы спроектированы и сконструированы для использования в нескольких производственных циклах.Некоторые из методов приведения, в которых они используются, включают:
- Литье под действием силы тяжести: Процессы литья под действием силы тяжести основаны на силе тяжести, которая направляет расплавленный металл из емкости или ковша в изложницу. Примеры включают постоянную форму, полупостоянную форму, слякоть и непрерывную разливку.
- Отливка в постоянные и полупостоянные формы: В процессе литья в постоянные формы используются формы, изготовленные из прочных металлов с более высокими температурами плавления, чем у литейного материала. Они простые и часто более толстые, чем формы, используемые при других методах литья.В процессе полупостоянного литья используются постоянные металлические формы с одноразовыми песчаными стержнями для создания деталей и изделий с более сложной внутренней конструкцией.
- Непрерывное литье: Процесс непрерывного литья включает подачу расплавленного металла в форму с водяным охлаждением для создания непрерывной полосы или стержня. После того, как отливка застынет, ее разрезают на отрезки определенной длины с помощью круглой пилы.
- Литье под давлением: В процессах литья под давлением для добавления материала в форму используются силы, отличные от силы тяжести, такие как пневматическое давление, вакуум или центробежная сила.Примеры включают литье под давлением, центробежное литье и вакуумное литье.
- Литье под давлением: В процессе литья под давлением используется система впрыска для нагнетания расплавленного металла в форму под высоким давлением.
- Центробежное литье: Процесс центробежного литья включает вращение формы с высокой скоростью при добавлении и охлаждении материала. Возникающая центробежная сила равномерно распределяет материал по стенкам полости.
- Вакуумное литье: В процессе вакуумного литья используется вакуум для втягивания расплавленного металла в форму.
В процессе литья подаются самые разные металлы. По сути, если металл можно расплавить, его можно и отлить. Некоторые из наиболее распространенных материалов, используемых при литье, включают:
- Алюминий и сплавы на его основе
- Цинк
- Сталь
- Нержавеющая сталь
- Медь и сплавы на основе меди
- Утюг
- Магний
- Никель
- Инструментальная сталь
Поскольку существует множество методов литья металла, каждый из которых предлагает уникальные преимущества и ограничения, бывает сложно определить, какой из них подходит для конкретного производственного проекта.Некоторые из факторов, которые следует учитывать при принятии решения о том, какой метод использовать, включают:
- Строительные материалы: Какие материалы вы используете для отливки?
- Производственные потребности: Сколько единиц требуется для этого прогона, и является ли это разовым или повторяющимся заказом?
- Обработка поверхности: Какую отделку вы ищете в готовом изделии?
- Диапазон допуска: Какие допуски размеров вам требуются?
- Минимальная необходимая толщина стенки
- Требования к обработке: Какой степени обработки будет подвергнута постпроизводственная обработка литой детали?
- Затраты на инструменты: Каков бюджет на затраты на инструменты?
Если вы ищете партнера по литью металла, обратитесь к экспертам Mardek.Наша обширная партнерская сеть известных зарубежных производителей позволяет нам выполнять широкий спектр требований к литью металлов, от мелких и хрупких деталей до крупных и тяжелых сборок. Предлагаем следующие услуги по литью металла:
- Литье под давлением
- Литье по выплавляемым моделям
- Отливка в неразъемную форму
- Литье в песчаные формы
В дополнение к нашим возможностям литья металла, мы также предоставляем другие услуги по изготовлению и отделке, чтобы облегчить доставку готовых литых деталей и изделий.Эти услуги включают прецизионную механическую обработку, термообработку, сборку, анодирование, покрытие, полировку, порошковое покрытие и покраску.
Чтобы узнать больше о наших возможностях литья металлов, посетите нашу страницу «О нас» или свяжитесь с нами сегодня. Для получения подробной информации о ценах запросите расценки.
Центробежное литье — детали, изготовленные на заказ, кованые, литые и гальванические
На протяжении веков литье играло жизненно важную роль в производстве. Литье металлов остается актуальным и сегодня.Это облегчает производство многих промышленных деталей.
В процессе литья металлов производитель использует нагрев и одну (или несколько) форм для постоянного изменения формы твердого металла. Жидкий металл, например, охлаждается до формы, определяемой формой.
Процесс центробежного литьяЦентробежное литье (или «роторное литье») представляет собой узкоспециализированный вид литья. Этот процесс, изобретенный Альфредом Круппом, позволяет массовое производство цилиндрических деталей, металлических колец и дисков с использованием форм для прядения.Производители полагаются на центробежные силы для равномерного распределения расплавленного металла по форме. В результате получаются мелкозернистые и плотно уплотненные металлические детали.
Первоначально производитель готовит центробежную форму, нанося одно или несколько покрытий на поверхность и нагревая форму до желаемой температуры. После того, как форма начинает вращаться с выбранной скоростью вращения, производитель устанавливает бегунок и начинает процесс заполнения.
Центробежные силы помогают равномерно распределить расплавленный материал.Металл остывает, пока форма продолжает вращаться. Производители могут выбрать поддержание постоянной высокой температуры в течение определенного периода времени за счет избирательного использования охлаждающих жидкостей. После того, как расплавленный металл затвердеет и остынет, производитель вытаскивает заготовку из формы, например с помощью съемника труб. Сегодня многие крупносерийные производственные предприятия полностью автоматизируют процесс центробежного литья.
Типы центробежного литьяПроизводители металлических деталей используют различные типы процессов центробежного литья:
Истинное центробежное литьеПроцесс
Истинное центробежное литье не требует использования внутреннего стержня формы.Вращение симметричной формы вокруг ее центральной оси заставляет металл распределяться по форме и создавать цилиндрическую отливку с полой закругленной внутренней частью.
Преимущества
При тщательно контролируемых условиях эта форма литья эффективно использует расплавленный металл.
Приложения
Производители производят различные металлические детали, используя истинное центробежное литье, в том числе цилиндры двигателей, кольцевые поршни и трубы.
Полуцентробежное литьеПроцесс
Во время полуцентробежного литья добавление центрального стержня к кристаллизатору определяет форму внутреннего отверстия в отливке. Производственный процесс по-прежнему основан на вращающихся формах для получения мелкозернистых отливок.
Преимущества
Этот процесс позволяет изменять форму внутренней полости литого кольца или цилиндра.
Приложения
Некоторые продукты, изготовленные с использованием полуцентробежного литья, включают опорные колеса, колеса железнодорожных вагонов и маховые колеса.
Центрифужное литьеПроцесс
Литье на центрифуге включает вращение нескольких небольших форм вокруг центральной оси, подобно тому, как вращаются пробирки, расположенные внутри центрифуги. Сгруппированные таким образом отдельные формы могут включать асимметричные формы.Обычно расплавленный металл поступает в форму через центральный литник и рассеивается внутри по сети предварительно вырезанных каналов.
Преимущества
В ходе этого процесса образуется несколько мелких деталей с компактным мелким зерном.
Приложения
Производители часто используют центрифужное литье для формования шестерен и других металлических деталей в форме дисков.
Центробежное литье позволяет производить большие объемы деталей, пригодных для механической обработки.Это позволяет производителям удобно и экономично создавать цилиндрические, дисковые или кольцевые заготовки:
МатериалыВ этом веке производители промышленных деталей применяют центробежное литье как процесс создания деталей из различных металлов и металлических сплавов. Некоторые популярные сырьевые материалы для этого типа литья включают чугун, нержавеющую сталь, сталь, алюминий, медь и никель.
Предприятия могут инвестировать значительные суммы в создание постоянных форм, используемых во время центробежного литья.Поскольку производство с помощью этого процесса включает в себя как высокие температуры, так и необходимость вращать формы с контролируемой скоростью, заводы могут нести сравнительно более высокие затраты на производство энергии, чем при некоторых других процессах литья. Центробежное литье поддается автоматизации, поэтому, несмотря на первоначальные вложения, оно часто обеспечивает очень эффективный производственный процесс, особенно для фирм, занимающихся крупносерийным производством.
ПриложенияЦентробежное литье имеет множество применений.Первоначально разработанный для изготовления более прочных и однородных колес поездов, сегодня этот процесс также способствует производству множества других промышленных металлических деталей.
Например, производители могут использовать этот процесс для создания металлических труб и трубок различных размеров без необходимости сваривать швы. Кроме того, центробежное литье позволяет производить металлические кольца и диски, а также очень тонкостенные цилиндрические детали. Он может помочь компаниям в производстве труб с прочной внутренней оболочкой.Другие распространенные области применения включают производство катушек, втулок, подшипников, компонентов шкивов и колес.
Преимущества центробежного литьяЦентробежное литье дает множество преимуществ. Во-первых, поскольку эти литые детали затвердевают с более мелко уплотненными металлическими зернами, чем отливки, полученные с помощью других производственных процессов, они, как правило, обеспечивают более прочные и более устойчивые к коррозии заготовки для обработки и чистовой обработки. Производители могут обнаружить, что использование этого процесса для формования отливок помогает снизить процент брака, например, во время чистовой обработки.
Во-вторых, процесс центробежного литья хорошо сочетается с автоматизацией. Поскольку каждый элемент этого процесса литья требует тщательного контроля (включая подготовку расплавленного металла, количество используемого сырья, скорость разливки, скорость вращения формы, температуру формы во время вращения и длину время вращения формы), автоматизация этого процесса помогает создавать более однородные отливки.
В-третьих, центробежное литье доказывает свою универсальность.Изготавливает симметричные отливки практически любого диаметра и длины. Эти изделия обладают отличными механическими свойствами.
СВЯЗАТЬСЯ С БАНТИ ООО
Для получения дополнительной информации о наших услугах свяжитесь с нами через удобную форму на веб-сайте или отправьте запрос на расценки напрямую.
Мы приветствуем ваши запросы.
Услуги компаний центробежного литья| Справочник IQS
Отраслевая информация
Центробежные отливки
Этот тип производственного процесса обычно используется с бетоном, смолой, гипсом или металлом и использует центробежную силу для создания широкого ассортимента изделий цилиндрической формы.Центробежное литье, очевидно, получило свое название от использования центробежной силы в приложении, но этот метод литья можно использовать для создания любого количества изделий, от реквизита для фильмов до зеркал. Из-за такого широкого спектра применений важно изучить производителей центробежных отливок и центробежных отливок перед покупкой. Другая форма центробежного литья известна как полуцентробежное литье, которое имеет тот же процесс, что и центробежное литье, но только при гораздо более низких скоростях.Какими бы ни были ваши потребности, весь процесс начинается с изготовления формы в соответствии с вашими требованиями и требованиями.
После изготовления формы в нее заливается материал по вашему выбору. Отсюда форма начинает вращаться, именно здесь применяется центробежная сила, которая выталкивает более плотные жидкости за пределы формы, в результате чего образуется ровный слой вокруг всей формы. Как только это будет завершено, форме дают остыть, а после охлаждения форму открывают, обнажая желаемый продукт.Как указывалось ранее, полученный продукт может принимать любое количество форм. Центробежное литье широко распространено даже в ювелирной промышленности для мелкосерийного производства, также известного как изготовление серебра. Причина, по которой центробежное литье так востребовано в производственном мире, заключается в том, что из-за центробежной силы готовый продукт имеет равномерную толщину по всему изделию. Центробежное литье часто используется для производства котлов , маховых колес, промышленных труб, сосудов высокого давления и многих других промышленных изделий.
Понимание того, что вам нужно от производителя центробежного литья, почти так же важно, как и выбор подходящего производителя для вашей работы. Процесс центробежного литья позволяет использовать самые разные материалы, от стекла до металлических сплавов, поэтому ищите производителя, который специализируется или имеет опыт работы с материалом, который вам нужен для вашего готового продукта. Выбор подходящего производителя — это первый шаг к получению идеального центробежного литья для вашего применения.
Центробежные отливки — Ferralloy Inc. | Центробежные отливки — Ferralloy Inc. |
Все, что вам нужно знать о центробежных отливках
Центробежное литье — это распространенный метод изготовления отливок, при котором жидкий металл заливается в форму, и эта форма быстро перемещается вокруг фиксированной оси.Форма имеет полую полость, форму которой стремится создать производственное подразделение.
Когда горячий, текучий металл заливается в форму, он сразу принимает желаемую форму. Затем ему дают остыть и затвердеть. После этого закаленную деталь вынимают, сильно ударяя ею по внешней поверхности формы или разбивая о землю. Как видите, этот процесс больше всего подходит для отливок по выплавляемым моделям , которые являются прочными и могут выдерживать удары, возникающие в результате разрушения или биения.
Центробежное литье обычно программируется таким образом, чтобы жидкий металл, когда он касается прядильной формы, также подвергался сильному давлению. Это давление или сила, на языке физики, также известна как центробежная сила; так процесс получил свое название. Другое название этого метода — «роторное литье», потому что он считается лучшим методом литья цилиндрических материалов.
Центробежная сила обеспечивает лучшее заполнение формы в дополнение к хорошей форме для окончательной отливки.Помимо этого, отливка также обеспечивает высокую плотность зерна. Высокое давление и нулевая плотность зерна с точки зрения пористости повышают качество продукта.
Ротор можно запрограммировать на вращение вертикально или горизонтально. Однако движение формы во многом зависит от типа материала, который вы собираетесь производить. Например, горизонтальное центробежное литье может быть идеальным, если вы производите трубчатые материалы. Тем не менее, метод вертикального заброса является наиболее предпочтительным.
Преимущества центробежного литья
- Создание обработки любого размера, любой длины и любого диаметра — это одно из самых больших преимуществ этой техники.
- Используйте метод роторного литья для производства длинных труб, толстых цилиндров и маховиков.
- Добейтесь другой уникальной толщины отливки.
- Работайте без сердечников — создавайте полые интерьеры без сердечников.
- Добейтесь превосходной отделки поверхности без сложных отделочных операций.
- Простое и быстрое изготовление тяжелых деталей.
- Наслаждайтесь очень высокой производительностью, которая помогает вашей организации поддерживать баланс между спросом и предложением.
- Уменьшает вероятность попадания примесей.
- Ограничьте использование затворов и стояков — все точки процесса работают без сбоев.
- Получение продуктов с высокой плотностью и сверхмелкой крупнозернистой структурой.
Это десять наиболее привлекательных преимуществ центробежного литья; однако у этого процесса есть несколько недостатков.
Недостатки центробежного литья
- Неточность может проявиться на внутренней поверхности отливки. Однако его можно уменьшить с помощью квалифицированного обращения.
- Производители, использующие этот метод, могут обрабатывать все металлы (включая сжиженные металлы) при производстве отливок.
Информационное видео о центробежном литье
Центробежное литье
Центробежное литье как категория включает центробежное литье, полуцентробежное литье и центрифугирование.
Центробежное литье : При центробежном литье постоянная изложница вращается вокруг своей оси с высокими скоростями (от 300 до 3000 об / мин) по мере разливки расплавленного металла. Расплавленный металл центробежно отбрасывается к внутренней стенке формы, где после охлаждения затвердевает. Отливка обычно представляет собой мелкозернистую отливку с очень мелкозернистым внешним диаметром, которая устойчива к атмосферной коррозии, типичной для труб. Внутренний диаметр содержит больше примесей и включений, которые можно удалить механической обработкой.
С помощью этого процесса можно изготавливать только цилиндрические формы. Ограничения по размеру — до 3 м (10 футов) в диаметре и до 15 м (50 футов) в длину. Толщина стенки может составлять от 2,5 мм до 125 мм (0,1–5,0 дюйма). Допуски по внешнему диаметру могут составлять 2,5 мм (0,1 дюйма), а по внутреннему диаметру — 3,8 мм (0,15 дюйма). Степень чистоты поверхности составляет от 2,5 мм до 12,5 мм (0,1 — 0,5 дюйма) среднеквадратичное значение.Типичными материалами, которые можно отливать с помощью этого процесса, являются железо, сталь, нержавеющая сталь и сплавы алюминия, меди и никеля.Два материала могут быть отлиты путем введения второго материала во время процесса. Типичными деталями, изготавливаемыми с помощью этого процесса, являются трубы, котлы, сосуды под давлением, маховики, гильзы цилиндров и другие акси-симметричные детали.
Полуцентробежное литье : Используемые формы могут быть постоянными или одноразовыми, при необходимости их можно штабелировать. Скорость вращения ниже, чем при центробежном литье. Центральная ось детали имеет дефекты включения, а также пористость и поэтому подходит только для деталей, где она может быть обработана механической обработкой.Этот процесс используется для изготовления колес, сопел и подобных деталей, когда ось детали удаляется путем последующей обработки.
Центрифугирование : Центрифугирование используется для выталкивания металла от центральной оси оборудования в отдельные полости формы, расположенные по окружности.