7 интересных поделок из алюминия
Алюминий — универсальный материал. Что самое интересное: из него можно сделать много полезных поделок и приспособлений своими руками.
Содержание
Формовочная масса для литья алюминия
Надо отлить деталь из алюминия?
Тогда без формовочной массы не обойтись. Потребуется песок и немного кошачьего наполнителя. Сырье необходимо подготовить, затем смешиваем все в строго определенной пропорции.
Увлажняем смесь водой, перемешиваем миксером. Формомасса получается полусухой — идеально подходит для формовки.
Подготовка сырья
Чтобы приготовить формовочную массу, никаких специальных навыков не нужно. Терпение и труд — залог успеха. Основные материалы — это морской песок и бентонитовый наполнитель для кошачьих туалетов.
Сначала необходимо просеять песок с помощью сита.
Это надо для того, чтобы удалить крупные фракции, а также избавиться от камушков и ракушек, которые в нем присутствуют.
После этого надо подготовить кошачий наполнитель.
Первым делом его необходимо измельчить — насыпаем небольшое количество сырья в электрическую кофемолку и перемалываем. Делаем так несколько раз, пока не подготовим нужное количество материала.
Обязательно просеиваем измельченный наполнитель через ситечко.
Пошаговый рецепт
Далее песок и бентонитовый наполнитель надо будет смешать. Берем 7 частей песка и 1 часть измельченного наполнителя. Перемешиваем и пересыпаем в чистую емкость — например, пластиковый таз или ведро.
Увлажняем смесь водой, затем перемешиваем миксером до однородной консистенции.
При необходимости подливаем воду — смесь должна быть полусухой.
Сделайте простой тест: сожмите часть формомассы в руке — она должна держать форму. Все готово.
Теперь, используя формовочную массу, приготовленную по нашему рецепту, вы сможете приступить к литью алюминия. Удачный проектов!
Видео
Как работает формовочная смесь из песка и наполнителя для кошачьих туалетов в реальных условиях — смотрите ниже.
Masa formierska domowym sposobemДверной колокольчик из алюминия своими руками
В данном обзоре автор показывает, как сделать своими руками дверной колокольчик из алюминия. Механический звонок — это не только практично, но и красиво.
Первым делом необходимо будет напилить восемь дощечек подходящего размера из досок или фанеры. Также потребуется деревянных реек.
Затем из дощечек и реек автор собирает две части опалубки, которые будут стыковаться между собой.
Рекомендуем прочитать:
- Как самому сделать тигель для плавки алюминия
- Бюджетный вариант получения алюминия в домашних условиях
Основные этапы работ
На ровное основание устанавливаем нижнюю часть опалубки и засыпаем песком, хорошо утрамбовывая его.
В качестве формы для отливки дверного колокольчика автор использует часть стеклянного бокала без ножки.
Затем устанавливаем вторую часть опалубки и засыпаем все песком. Не забываем оставить отверстие под литник.
Расплавляем в тигеле нужное количество алюминия, после чего заливаем жидкий металл в литник.
На следующем этапе разбираем опалубку и извлекаем из нее отлитую алюминиевую деталь.
После этого останется только установить язычок внутри колокольчика и сделать крепление, чтобы можно было подвесить механический дверной звонок на нужной высоте.
Видео
Подробнее о том, как изготовить дверной колокольчик из алюминия своими руками, смотрите в видеоролике на сайте.
Alquimia do Alumínio. Como derreter alumínio e transformar em objetos decorativo.Алюминиевая ручка для старого топора
Изготовление алюминиевой ручки для старого топора — процесс больше для удовольствия. Какой-либо пользы для дома от такой самоделки не будет, поскольку топорище будет вдвое тяжелее, чем обычная деревянная ручка.
Основная цель данной работы:
- восстановить старый топор и дать ему вторую жизнь;
- сделать своими руками оригинальный топор, который не будет использоваться для колки дров или других, а просто будет стоять на видном месте в качестве красивого экспоната.
В первую очередь необходимо очистить поверхность топора от ржавчины.
Один из эффективных способов — электрохимическая реакция (электролиз) в растворе карбоната натрия и воды.
Сам топор подключаем к «минусу» автомобильного аккумулятора, а стальные стержни — к «плюсу».
Изготовление алюминиевой ручки
На заготовке из пенопласта рисуем эскиз будущего алюминиевого топорища, после чего вырезаем при помощи специального станка для горячей резки пенополиуретана (или же можно использовать другие доступные способы). Готовый образец шлифуем наждачной бумагой.
На следующем этапе приклеиваем заготовки из пенопласта к топору при помощи термоклея. Затем приклеиваем литники.
Получившуюся форму обмазываем гипсовой штукатуркой для качественного литья. Слой штукатурки должен быть тонким.
Далее помещаем «рогатую» форму с топором в деревянный ящик с песком, на литники надеваются стальные колпаки, и заполняем их песком. Затем расплавляем алюминием и заливаем топорище. В итоге получилась хоть и массивная, но оригинальная ручка для старого топора.
Видео
Подробный процесс изготовления шаблона из пенопласта и литься алюминия можете посмотреть в видеоролике на сайте.
Antique Hatchet Restoration. Third Time’s a Charm!Бейсбольная бита из алюминия своими руками
В данном обзоре автор показывает, как изготовить своими руками бейсбольную биту из алюминия.
Для игры в бейсбол такая бита, конечно же, не подойдет, но можно использовать ее в качестве декоративного элемента в интерьере.
Первым делом автор склеивает вместе две доски, положив между ними газету. В итоге должен получиться брус квадратного сечения. После этого нужно обработать заготовку на токарном станке, придав ей форму биты.
Далее при помощи стамески мастер разделяет заготовку на две половинки. Благодаря прослойке из газеты это несложно будет сделать.
Рекомендуем также прочитать статью: как из дисковой бороны сделать нож керамбит своими руками.
Основные этапы работ
На следующем этапе из досок автор изготавливает две части (верхнюю и нижнюю) формы. Помещаем заготовку в опалубку, после чего надо засыпать ее формовочной смесью и тщательно утрамбовать.
В итоге у нас должно получиться две части формы с оттиском модели. Далее надо сделать отверстия для заливки алюминия.
Собираем форму, фиксируем ее, а затем расплавляем алюминий и заливаем его в отверстие. Далее нужно подождать, пока алюминий застынет.
На ленточной пиле срезаем наплывы и все лишнее, после этого обрабатываем изделие на токарном станке и полируем. На последнем этапе автор красит верхнюю часть биты черной краской.
Видео
Подробнее о том, как отлить бейсбольную биту из алюминия, вы можете посмотреть в видеоролике на нашем сайте.
Как отлить проставку опорного подшипника из алюминия
В данном обзоре автор показывает, как в условиях домашней мастерской можно отлить проставку опорного подшипника из алюминия. При наличии горна это не займет много времени.
Собственно, по данной технологии можно без проблем отлить и любые другие детали из алюминия. Поэтому берите себе на заметку.
Если у вас в мастерской нет горна, но вы планируете сделать его своими руками, полезную информацию вы можете найти в статье на нашем сайте: кузнечный газовый горн из вермикулита своими руками.
Также рекомендуем прочитать полезный и интересный обзор на тему: как сделать инжекционную газовую горелку для горна своими руками.
Основные этапы работ
Первым делом необходимо будет подготовить деталь-шаблон к формовке и залепить пластилином отверстия (их автор будет сверлить потом).
Причем пластилин нужно немного утопить, чтобы после отливки было понятно, где именно сверлить отверстия.
На следующем этапе потребуется формовочная смесь.
Ее можно купить уже готовую или сделать самостоятельно из строительного песка и бетонитовой глины. Сама смесь должна быть чуть влажной (нужно добавить небольшое количество воды).
Из деревянных брусков и металлических уголков собираем рамку, внутрь которой необходимо поместить образец.
Чтобы легко отделить форму от формовочной смеси, автор использует детскую присыпку.
Подготовка к заливке
Деревянную рамку необходимо заполнить подготовленной формовочной смесью. Ее нужно утрамбовать, а верх — выровнять.
Переворачиваем рамку и слегка постукиваем по детали молотком. Потом вкручиваем в пластилин саморезы и аккуратно вынимаем образец.
Далее надо будет расплавить алюминий. Шлак, который образуется на поверхности, перед заливкой формы необходимо убрать.
Обратите внимание, что заливать форму нужно предельно аккуратно, но в то же время — быстро, чтобы алюминий не успел схватиться. После остывания останется только обработать деталь и просверлить отверстия.
Видео
Литьё Алюминия Запчасть Для Автомобиля Своими РукамиРучка из алюминия для кухонного топорика
Деревянная ручка на топорике рассохлась, в результате чего пришла в негодность, поэтому автор решил сделать ей достойную замену — но уже не из дерева, а из алюминия.
Первым делом автор убирает «огрызки» деревянной ручки и удаляет заклепки. Нужно обрезать один край заклепок болгаркой, а потом просто выбить стержни из отверстия.
После этого автор чистит сам топор и его хвостовую часть от ржавчины, и сверлит в рукоятке дополнительные отверстия.
Далее из экструдированного пенополистирола необходимо вырезать две заготовки и приклеить их к рукоятке топорика.
На поверхность пенополистирола автор с помощью кисточки наносит жидкий гипсовый раствор.
Основные этапы работ
На следующем этапе помещаем топорик с «хвостом» в подходящую по размеру емкость (в данном случае автор использует картонную коробку) и засыпаем песком.
После этого плавим алюминий, и заливаем его в литник. Пенополистирол мгновенно расплавляется, и алюминий заполняет пространство внутри гипсового «кокона».
Затем надо разбить гипс и охладить алюминиевую ручку в воде. На ленточной пиле отрезаем все лишнее.
Далее при помощи напильника с крупной насечкой и наждачной бумаги автор придает алюминиевой ручке необходимую форму и благородный вид.
Завершающий этап работ — это полировка алюминиевой ручки и заточка лезвия топора.
Видео
Подробно о том, как сделать ручку из алюминия для кухонного топорика, смотрите в видеоролике на сайте.
Insanely Big Butcher Cleaver Restoration. SORT OF…Крючки для одежды из алюминия своими руками
В данном обзоре автор поделится с нами собственным опытом литья алюминия в песчаную форму на примере изготовления крючков для одежды.
Крючки можно использовать как по отдельности — в прихожей или ванной комнате, так и для изготовления настенной вешалки.
Первым делом необходимо изготовить деревянную модель крючка для одежды (мастер делает ее из тополя).
Возможно, вам также интересно будет прочитать, как из старой бочки сделать небольшую печь для плавки алюминия.
После этого автор собирает форму для литья алюминия, которая состоит из двух основных частей.
В обеих частях сверлим отверстия, потому в одну из них — вставляем деревянные шканты, и отпиливаем их до нужной длины (чтобы удобно было разбирать форму).
Основные этапы работ
В одну из частей формы насыпаем песок, трамбуем его. Потом укладываем сверху деревянную модель, вдавливаем.
Устанавливаем вторую часть формы, и заполняем ее песком, трамбуем. Прикручиваем крышку.
В качестве разделителя обычно используется тальк, но можно взять и графитовый порошок.
Убираем деревянную модель, соединяем две части формы вместе, фиксируем дополнительно с помощью струбцины.
После этого расплавляем алюминий и заливаем его в форму через литьевое отверстие в торце.
Разбираем форму, и извлекаем отлитую деталь. Ее нужно будет обработать напильником и отшлифовать.
Таким же образом изготавливаем остальные крючки.
Видео
Подробно о том, как лить алюминий в песчаную форму, можно посмотреть в авторском видеоролике (источник — YouTube канал «Юрий Романов»).
Как отлить самодельные струбцины из алюминия
В данном обзоре автор показывает самый простой способ, как самому отлить самодельные струбцины из алюминия. Идея стоящая, поскольку позволяет сэкономить на покупке новых струбцин.
Для изготовления алюминиевых струбцин потребуется сам алюминий, образец струбцины, литейная форма, тигель, формовочная смесь и два короба из досок или фанеры.
Также необходимо будет предварительно сделать форму из гипса с оттиском струбцины по центру.
Посыпаем гипсовую платформу тальком, устанавливаем струбцину, и ставим нижний деревянный короб. Затем засыпаем короб формовочной смесью, утрамбовываем и выравниваем ее.
После этого аккуратно снимаем короб и переворачиваем его, чтобы оттиск струбцины находился сверху, посыпаем тальком, и после этого устанавливаем струбцину.
Основные этапы работ
На следующем этапе устанавливаем второй (верхний) деревянный короб и заполняем его формовочной смесью. Утрамбовываем ее и выравниваем.
С помощью круглой металлической трубки делаем литейные отверстия. Затем снимаем аккуратно верхний короб, убираем струбцину и делаем «дорожки».
Далее собираем обратно литейную форму и устанавливаем сверху два литника. Расплавляем алюминий, и заливаем его в форму.
Получившиеся готовые изделия нужно обработать напильником. Потом останется только просверлить отверстия и нарезать резьбу под винты.
Видео
Подробно о том, как своими руками отлить самодельные струбцины из алюминия, можно посмотреть в видеоролике на нашем сайте.
литьё алюминия струбциныАндрей Васильев
Задать вопрос
Технология литья в песчаные формы
Определения литья в землю
Определим, какими терминами называют литейную технологию заливки металла в формы на основе песка
. Аналогичными считаются формулировки:
— Литье в песчаные формы, смеси;
— Литье в песчано-глинистые формы, смеси;
— Литье в землю.
Все эти термины обозначают одну и туже технологию литья. Применение далее любого из названий, будем считать аналогами.
Литье в песчаные формы – метод литья металлов и сплавов, при котором расплавленный металл заливается в форму сделанную из плотно утрамбованного песка. Для связи песчинок между собой, песок смешивают с глиной, водой и другими связующими материалами.
Более 70% всех металлических отливок производится с помощью процесса литья в песчаные формы.
Основные этапы
Есть шесть шагов в этом процессе:
Поместить модель в опоку с песком, чтобы создать форму.
-В необходимых местах присоединяются литниковая система и выпоры.
-Удалить из опоки модель и соединить полуформы.
-Заполнить полость формы расплавленным металлом.
-Выдержать застывающий металл в опоках согласно технологии.
-Выбить отливку и освободить от литников и выпоров.
По чертежам и литейным технологиям, разработанных технологом или конструктором, опытный модельщик изготавливает модель детали из дерева, металла или пластмассы или пенополистирола.
Металл в процессе охлаждения даёт усадку, и кристаллизация может быть неоднородной из-за неравномерного охлаждения. Таким образом, модель должна быть чуть больше, чем готовая отливка, с применением, так называемого, коэффициента усадки металла. Различные усадочные коэффициенты используются для различных металлов. Модели в процессе формовки оставляют в песке полости-отпечатки в форме, в которые помещают стержень из песка. Такие стержни иногда усиливается проволочной арматурой, которые используются для создания полостей, которые не могут быть сформированы основной моделью, например, внутренние проходы клапанов или места охлаждения в блоках двигателей.
Литниковая система для входа металла в полости формы представляют собой направляющую и включает воронку, литники, которые поддерживают хороший напор жидкого металла, для более равномерного заполнения полости формы. Газ и пар, образующихся при литье выходят через проницаемые пески или через стояки, которые изготавливаются либо в самой модели, или в виде отдельных частей.
Опоки для формовочных материалов
Для формовки используют две или несколько опок. Опоки изготавливаются в виде ящиков, которые могут быть соединены друг с другом и скреплены между собой. Модель утапливается в нижней части опоки вплоть до её самого широкого поперечного сечения. Затем монтируется верхняя часть модели. К нижней части опоки зажимами прикрепляется верхняя и туда добавляется и утрамбовывается формовочная смесь таким образом чтобы она полностью закрывала модель. В необходимых местах устанавливаются литники и выпора. Затем опока половинится и из неё вынимается модель, деревянные литники и выпора.
Для управления кристаллизацией структуры металла, в форму можно поставить металлические пластины, холодильники. Соответственно быстрое локальное охлаждения образует более детальную структуру металла в этих местах. В черной отливке эффект аналогичен закалке металла в кузнице. В других металлах, холодильники могут быть использованы для управления направленной кристаллизации отливки. При управлении способом охлаждения литья можно предотвратить внутренние пустоты или пористость внутри литья.
Производство
Для получения полостей в отливке, например, для охлаждающей жидкости в блоке двигателя и головок цилиндров используются стержни. Обычно стержни для литья ставятся в форму после удаления модели. После сушки опоку с формой устанавливают на литейный плац для заполнения расплавленным металлом, обычно сталь, бронза, латунь, алюминий, магний и цинк. После заполнения жидким металлом опоки не трогают до охлаждения отливки. После выбивки отливки, стержни удаляются из литья. Металл литников и прибылей любым способом должен быть отделен от отливки. Различные термические обработки могут быть использованы для снятия напряжений от первоначального охлаждения и добавить твёрдости в случае закалки в воде или масле. Поверхность литья может быть дополнительно упрочена дробеструйной обработкой, которая добавляет устойчивости к растрескиванию, растягивает и разглаживает шероховатую поверхность.
Чтобы было возможным удалить модель не нарушая целостности формовочной смеси все части модели должны быть предварительно рассчитаны технологом и иметь знаковые части для установки стержней. Небольшой уклон должен использоваться на поверхностях, перпендикулярных линии разъема, для того, чтобы была возможность удалить модель из формы. Это требование также распространяется на стержни, так как они должны быть удалены из полостей, которые они образуют. Выпора и стояки должны быть расположены так, чтобы обеспечить оптимальный поток металла в форму и газов из неё для того, чтобы избежать недолива литья.
Способы литья в землю
Различают два способа литья в песчаные формы, первый с использованием «сырого» песка, так называемые сырые формы, а второй метод — жидкостекольный.
Сырые формы
Мокрый песок, используются, чтобы сделать форму в опоке. Название произошло от того, что мокрым песком пользуются в процессе формования. «Сырой песок» – это смесь:
-кремнеземистый песок (SiO2), или хромистые пески (FeCr2O), или циркониевый песок (ZrSiO4), от 75 до 85%, и другие составляющие, включая графит, глину от 5 до 11%, воды от 2 до 4%, других неорганических элементов от 3 до 5%, антрацит до 1%.
Есть много формовочных смесей с глиной, но все они различны по пластичным свойствам смеси, качеству поверхности, а также возможностью применения в литье расплавленного металла в отношении пропускной способности для выхода газов. Графит, как правило, содержится в соотношении не более 5%, он частично сгорает при соприкосновении с расплавленным металлом с образованием и выделением органических газов. Сырые смеси как правило для литья цветных металлов не используются, так как сырые формы приводят к сильному окислению, особенно медного и бронзового литья. Сырые песчаные формы для литья алюминия не используют. Для алюминиевого литья используют более качественные формовочные смеси. Выбор песка для формовки зависит от температуры заливки металла. Температура заливки меди, стали и чугуна выше других металлов, поэтому, глина от воздействия высокой температуры далее не регенерируется. Для заливки чугуна и стали на основе железа как правило, работают с кварцевым песком – он относительно недорог по сравнению с другими песками. Так как глина выгорает, в новую порцию песчаной смеси добавляют новую порцию глины и некоторую часть старого песка. Кремний является нежелательным в песке, т.к. зерна кварцевого песка имеют тенденцию взрываться при воздействии высокой температуры во время заливки формы. Эти частицы находятся во взвешенном состоянии в воздухе, что может привести к силикозу у рабочих. В литейном цехе имеется активная вентиляция для сбора пыли. Мелкие древесные опилки (древесная мука) добавляется, чтобы создать место, при ее выгорании, для зерен песка, когда они расширяются без деформации формы.
Технология ЖСС (жидко-стекольная смесь)
Эта технология состоит в следующем:
в состав формовочной смеси входит прокаленный песок без глины, затем его в специальной емкости перемешивают с жидким стеклом и перемешанной массой заливают модель. Залитую форму накалывают для последующего подвода углекислоты. Опоку накрывают колпаком и подают газ СО2. После чего залитый формовочный состав ЖСС приобретает твердость.
В обоих методах, песчаная смесь остается вокруг модельной оснастки, образуя полости формы для заливки металла. Формовка жидкостекольными смесями позволяет получить две полуформы, которые после затвердевания собирают. Модель удаляется, образуя полость формы. Эту полость заливают жидким металлом. После того, как металл остыл отливки очищают от формовочного состава. Форма из ЖСС полностью разрушается при извлечении отливки.
Точность литья напрямую связана с типом формовочной смеси и формовки. Сырые формы создают на поверхности отливки повышенную шероховатость. Поэтому литье в землю можно сразу отличить от литья по ЖСС и ХТС. Литье в формы из мелкого песка значительно чище и менее шероховато. Технология ЖСС позволяет изготавливать отливки с гладкой поверхности, особенно при использовании пластиковых моделей. В отдельных случаях, например при литье корпусных деталей, можно обойтись даже без механической обработки на больших поверхностях – это позволяет отливать крупногабаритные чугунные блоки цилиндров. Остатки пригоревшей к отливке формовочной смеси удаляются дробеструйной обработкой.
С 1950 года, частично автоматизированные литейные процессы литья были переработаны для полностью автоматизированных производственных линий.
Использование органических и неорганических связующих, которые укрепляют формы для литья химически связывают песок. Этот тип формовки получил свое название от того, что он не требует просушки, как другие виды песчаной формовки. Литье в ХТС является более точным, чем литье в землю. Размеры форм ХТС меньше, чем при литье в песчаные смеси, но дороже. Таким образом, ХТС используется реже, в тех случаях, когда требуется более качественное литье. Наше предприятие готово поставлять вам отливки по ХТС.
Формы из холодно твердеющей смеси, требуют быстрой формовки, в отличие от песчано-глинистых смесей, т.к. они содержат быстро твердеющие жидкие смолы, ускорители затвердевания и катализаторы. Вместо трамбовки смеси (как при литье в землю), формовочную смесь ХТС заливают в опоку и дожидаются, когда смола затвердеет. Обычно затвердевание происходит при комнатной температуре в течение 20 минут. Литье в ХТС значительно улучшает качество необработанных поверхностей стальной отливки по сравнению с другими технологиями литья в песчаных формах. Обычно для изготовления модельной оснастки по ХТС используют дерево, металл или пластик МДФ. Чаще других формовка холодно твердеющими смесями применяется при литье меди, литье алюминия, углеродистой стали, жаропрочной и нержавеющей стали, а также легированного чугуна, так как значительно снижает вероятность образования литейного брака.
Greensand — Lost & Foundry
Опубликовано автором
Литейный песок называют «зеленым песком» из-за небольшого содержания влаги.
Сочетание песка, глины и воды.
Foundry Sand/Greensand
В коммерческих литейных цехах песок используется снова и снова тысячи раз. Между использованием песок омолаживается путем добавления воды и измельчения (перемешивания и измельчения). Зернистость песка определяется так же, как наждачная бумага. 150 очень мелкий, а 50 грубый. Мелкий песок даст хорошую детализацию, крупный песок даст галечную или грубую текстуру. Если вы посмотрите на песок через микроскоп, вы увидите щели и пустоты, как на губке. Любая влага, которая превращается в газ во время заливки, может выйти через поры (зазоры).
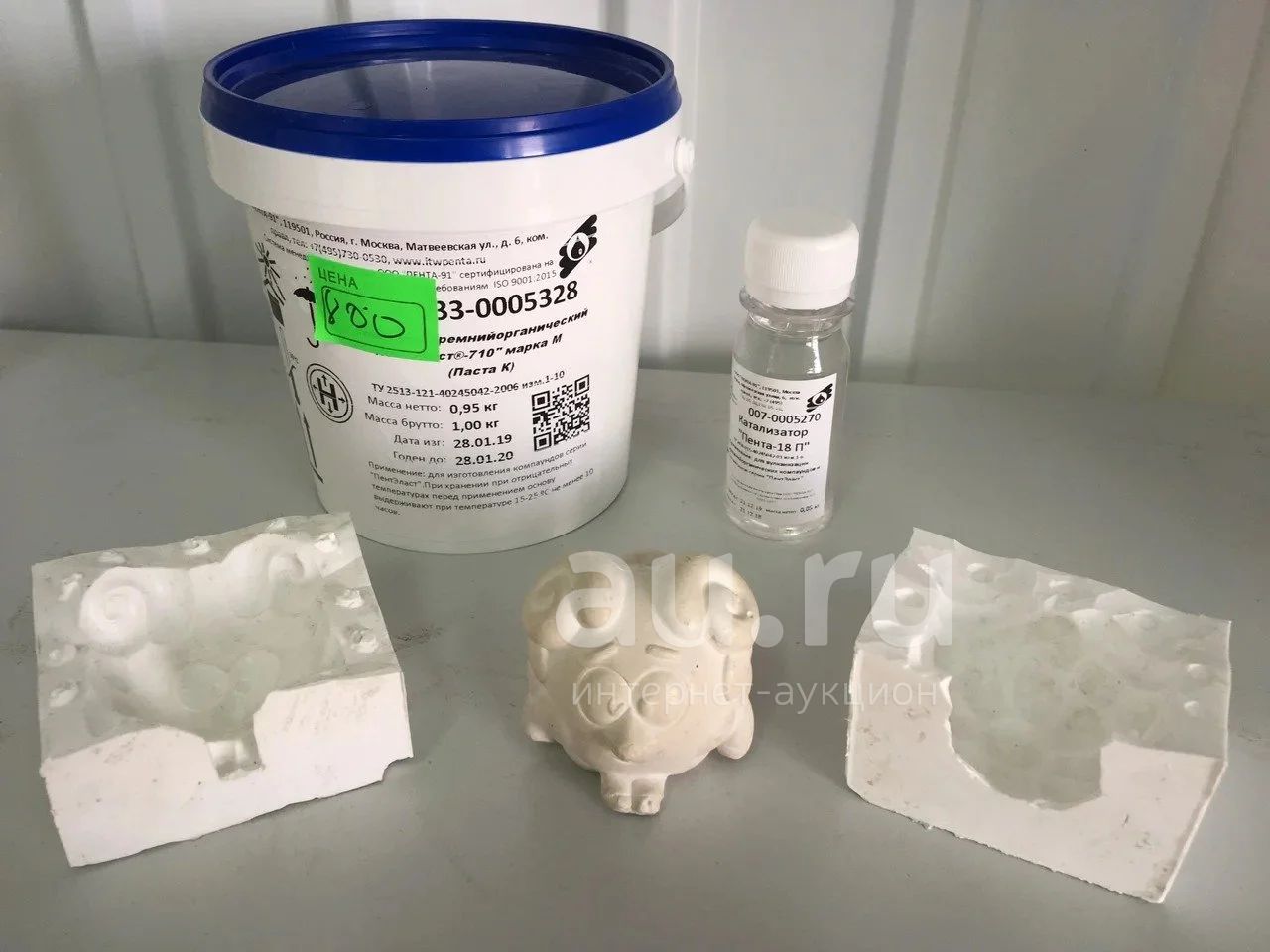
Mulling
Mulling покрывает каждую песчинку бентонитом, разбивая и раздавливая под весом. В литейном цеху используют большую кадку с 2-мя большими колесами, чтобы разбивать, 2-мя шнеками, чтобы вспахивать (смешивать вверх), фрезой. Вам не нужен мюллер.
Смешивание зеленого песка без наполнителя:
1. На чистый пол насыпьте 100 фунтов мелкого кварцевого песка и распределите его толщиной около 1 дюйма (около 6 футов).
2. Равномерно вылейте 1 галлон воды на песок из садовой лейки, тщательно перемешайте лопатой и граблями.
3. Рассыпьте примерно 1 дюйм толщиной и равномерно посыпьте 12 фунтами порошкообразного бентонита на песок/воду. Вмешайте бентонит граблями и переверните лопатой, чтобы тщательно перемешать.
4. Разбейте смесь ногами до упора, затем встряхните ее лопатой, перемешав смесь. Повторите этот шаг еще 2 раза .
Пожалуйста, посмотрите это видео…….
СНАЧАЛА смешайте песок и воду, затем добавьте бентонит.
https://www.facebook.com/foundry101/videos/2036175736492532
Использование песка
1. Насыпьте песок в колбу, плотно утрамбовав его. После снятия модели и формирования литниковой полости можно прожечь литейную полость (форму) для удаления лишней влаги.
2.После заливки, охлаждения и встряхивания (извлечение опоки и отливки из песка) сбрызните песок водой. В основном на твердом, хрустящем песке, который касался отливки. Около 2 чашек воды на 25-фунтовую форму. НЕ добавлять слишком много воды !
3. Храните песок в герметичном контейнере, когда он не используется, чтобы сохранить влагу. Если вы держите песок влажным, вам не нужно мульчировать. Если вы позволили песку полностью высохнуть, его необходимо перемульчировать.
Мощный процесс литья в песок
Процесс литья в песок
Даже ребенок, играющий на пляже или в песочнице, сразу поймет, как работает литье в песок. Когда вы видите, как ребенок смешивает воду с песком, чтобы облегчить формирование из него замка из песка, этот ребенок демонстрирует, как сочетание песка и воды так прекрасно работает для создания формы.
В самом простом случае процесс литья в песчаные формы для литейного цеха представляет собой не что иное, как создание полости в песке желаемой формы, заливку расплавленного металла в полость и охлаждение. Человечество занимается этим уже тысячи лет. Песок жаростойкий и легко доступен практически в любой точке земного шара.
Если вы когда-нибудь замечали, как следы, оставленные на мокром песке, сохраняют свою форму, вы можете легко себе представить, что, вероятно, вдохновило первых древних мастеров по металлу использовать мокрый песок для придания формы своим отлитым металлам. Все после этого просто усовершенствовало и усовершенствовало основной процесс.
Что такое литье в зеленый песок? Термин зеленый san d не имеет ничего общего с цветом материала для литья в песчаные формы. Это означает, что в песке есть влага; когда говорят, что песок зеленый, это означает, что плесень не обожжена и не высушена. Этот вид формовочной смеси является очень экономичным и универсальным материалом. При желании литейный завод может добавить некоторые добавки, которые сделают сырой песок более подходящим для конкретной цели. Зеленый песок используется в наиболее распространенных процессах литья в песчаные формы.
Оборудование для литья в песчаные формы в литейном цехе может быть очень простым или весьма продвинутым, в зависимости от производимых изделий. Как правило, песок помещают в формовочный ящик, известный как опока . Выкройка или модель помещается в подготовленный песок внутри колбы, чтобы получилась форма. Узор удаляется, оставляя идеальную форму на песке. Форма заполняется расплавленным металлом, которому дают остыть. Когда металл достаточно остынет, песчаная форма может быть разрушена.
Более сложные изделия можно отливать, комбинируя верхнюю и нижнюю секции. Верхняя форма известна как копия , а нижняя половина известна как перетяжка . После того, как накидка и обрешетка будут готовы, их можно скрепить вместе, чтобы в образовавшуюся полость можно было залить расплавленный металл. Возможна дальнейшая детализация при добавлении ядра . Стержень — это нечто, помещаемое внутрь формы для образования отрицательного пространства, которое не заполнит расплавленный металл. Примером может служить середина блока двигателя или любого другого литого предмета, для которого требуется пустое пространство.
Отливки, изготовленные с наплавкой и волочением, должны обеспечивать способ подачи расплавленного металла в форму. Это может быть простой вертикальный проход, известный как литник . Литник и его канал заполнятся расплавленным металлом, который затвердеет, и его нужно будет обработать, чтобы придать изделию окончательный вид.
Как работает процесс литья в песчаные формы? В современной литейной или литейной промышленности знание того, как каждый сплав будет реагировать с каждой потенциальной формой формы и каждой потенциальной добавкой, позволяет рабочему сделать выбор, чтобы придать готовому изделию желаемые характеристики. Литье металлов – это и искусство, и наука.
Когда расплавленный металл остывает и затвердевает, он выделяет газы. Формы спроектированы с учетом этого и, при необходимости, будут сконструированы таким образом, чтобы газы могли выходить на протяжении всего процесса литья в песчаные формы.
Для чего используется литье в песчаные формы?Велика вероятность, что сейчас вы находитесь менее чем в 10 футах от хотя бы одного литого предмета, прошедшего процесс литья в песчаные формы. Вряд ли найдется отрасль, в которой не было бы потребности в литых материалах. Некоторые литые изделия большие и могут весить сотни фунтов, в то время как другие литые изделия крошечные и сложные.
Какие металлы обычно используются при литье в песчаные формы? Практически любому металлу можно придать форму с помощью подходящего оборудования для литья в песчаные формы. Латунь и бронза отлиты очень хорошо и являются одними из первых предметов, отлитых в древние времена. Литье алюминия в песчаные формы довольно распространено. Чугун, как следует из названия, также изготавливается методом литья.
- Глина : Это может быть бентонитовая глина (скорее всего, кальциевый бентонит) или другой вид глины. Для особых тонких и высокодетализированных изделий, таких как украшения, можно использовать делфтскую глину, которая импортируется из Нидерландов.
- Угольная пыль : Также известная как Морской уголь , добавляется для получения более ровной поверхности и облегчения извлечения отливки из формы. Он также производит отливки с меньшим количеством дефектов.
- Кукурузная мука : Хотите верьте, хотите нет, но немного кукурузной муки, добавленное во влажный песок, придает песку большую прочность и пластичность.
- Декстрин: Декстрин, полученный из кукурузного крахмала, используется в качестве связующего вещества. Улучшает прочность сухой поверхности песка.
- Смола: Изготовлена из мягкого угля, добавление небольшого количества смолы в песок улучшает качество поверхности.
- Древесная мука: Этот горючий материал, который, как и другие горючие добавки, помогает создать пространство для расширения песчинок без изменения формы формы.
- Кварцевая мука: Этот материал представляет собой просто мелкоизмельченный песок, который смешивают с литейными материалами для получения более прочной формы.
Относительно новой технологией в современном литейном производстве являются модели и формы, напечатанные на 3D-принтере.
Новейшее оборудование для 3D-печати способно изготовить песчаную форму и стержень всего за несколько часов. В некоторых случаях это может значительно сэкономить время и деньги.
После изготовления модели литье в песчаные формы проходит как обычно, но возможность использовать 3D-принтер для изготовления модели, форм и стержней значительно ускоряет процесс, потенциально снижая производственные затраты и повышая точность литья. Если образец предмета для литья в песчаные формы уже существует, его можно легко отсканировать для создания 3D-модели.
После того, как программа изготовления песчаной формы и стержня будет усовершенствована, ее можно воспроизвести любое количество раз. Такое оборудование для литья в песчаные формы является растущей частью индустрии литья металлов. Сегодняшние достижения в литье песка, несомненно, поразили бы мастеров литья песка сто лет назад, не говоря уже о тысячелетней давности!
Почему некоторые литые изделия требуют механической обработки? В некоторых случаях изделие, изготовленное методом литья в песчаные формы, требует механической обработки, покраски или другого процесса, чтобы довести его до конца. Часто предмет будет иметь посторонний материал, необходимый для создания хорошего слепка, но не предназначенный для того, чтобы быть частью готового дизайна. В других случаях необходима тонкая детализация, которую можно добавить после завершения отливки. Компания Cast Technologies располагает станочным цехом с ЧПУ, чтобы поставлять готовый продукт, отвечающий вашим потребностям. Это позволяет нам лучше обслуживать наших клиентов, так как мы берем на себя ответственность за все процессы, необходимые для соответствия детали ее проектным спецификациям.
Свяжитесь с нами по всем вопросам, связанным с литьем металлов. У нас есть опыт работы с производителями из самых разных отраслей. Мы можем помочь вам в прототипировании или обратном проектировании деталей. Мы порекомендуем сплавы и процессы, которые наилучшим образом удовлетворят ваши потребности. У нас есть современное оборудование и опытные и преданные своему делу сотрудники, готовые служить вам.