мелкосерийное производство по доступной цене
Для выпуска серийных товаров, как правило, используют технологию литья в пресс-формы (металлические оснастки). Это дорогостоящие решения в плане первоначального расхода средств на подготовку производства, да и временные затраты с момента начала работ и до получения первых единиц продукции занимают порядка 3–4 месяцев. Сейчас уже большинство компаний знакомы с аддитивными технологиями, и до производства пресс-формы и литья изготавливается прототип будущего изделия для проверки собираемости и физико-механических свойств будущей детали, однако для многих остается загадкой, как получить максимально приближенный к конечному изделию прототип и в плане функционала, и в плане внешнего вида. Для этих задач нам на помощь приходит уже довольно давно используемая технология вакуумного литья в силиконовые формы, которая, к сожалению, в России для многих остается загадкой. Она будет также актуальной, если вы планируете вывести на рынок небольшое количество продукции (до 500–1 000 единиц), и не только сэкономит ваши деньги, но и позволит добиться оптимального качества готового изделия за максимально короткие сроки.
Так что же это за технология? И как она устроена?
Технология
Саму работу по мелкосерийному производству пластиковых и резиноподобных изделий можно разделить на 5 основных этапов. По каждому этапу, в зависимости от задачи, есть различные пути решения. Используются различные материалы как для мастер-моделей, так и для производства форм и отливок, но эта тема отдельной статьи, поэтому мы тезисно опишем каждый этап для общего понимания технологии производства.
1. 3D-моделирование и производство прототипа изделия. Речь идет о проектировании математической модели с последующей ее распечаткой на 3D-принтере или фрезеровкой на ЧПУ.

3. Изготовление силиконовой формы для литья. Для производства формы, или, как ее еще называют, матрицы, мастер-модель помещается в опалубку — герметичную емкость из твердого материала. Затем устанавливают систему трубок (литниковую систему), предназначенных для подачи в форму жидкого двухкомпонентного материала. После этого силикон, который предварительно прошел дегазацию в вакуумной камере, заливают в опалубку.
4. Тестовая отливка и доработка формы. Если после тестовой отливки детали полученное изделие отличается от мастер-модели, производится доработка формы. Как правило, модернизация силиконовой матрицы не занимает много времени и в основном заключается в усовершенствовании литниковой системы и каналов вывода воздуха из формы при заливке на основе полученного первого образца.

Благодаря быстроте изготовления оснастки данный метод уже через несколько дней позволяет получить небольшую партию пластиковых изделий.
Преимущества
Сильные стороны эластичных форм не заканчиваются на их дешевизне и быстром изготовлении, о чем было сказано в самом начале.
Во‑вторых, силиконовые емкости безопасны. Они не горят, являются химически инертными. Есть также пищевой силикон, форму из которого можно использовать для создания уникальных кондитерских изделий.
В‑третьих, такие формы просты в использовании. Изделие отделяется от матрицы легко, а поскольку форма имеет высокую гибкость, то и требования к изделию предъявляются не такие жесткие, как к производству такого же образца, но на пресс-форме.
В‑четвертых, в изделия без проблем внедряются металлические закладные разных типов начиная от стандартных втулок и заканчивая жестким металлическим каркасом корпуса.
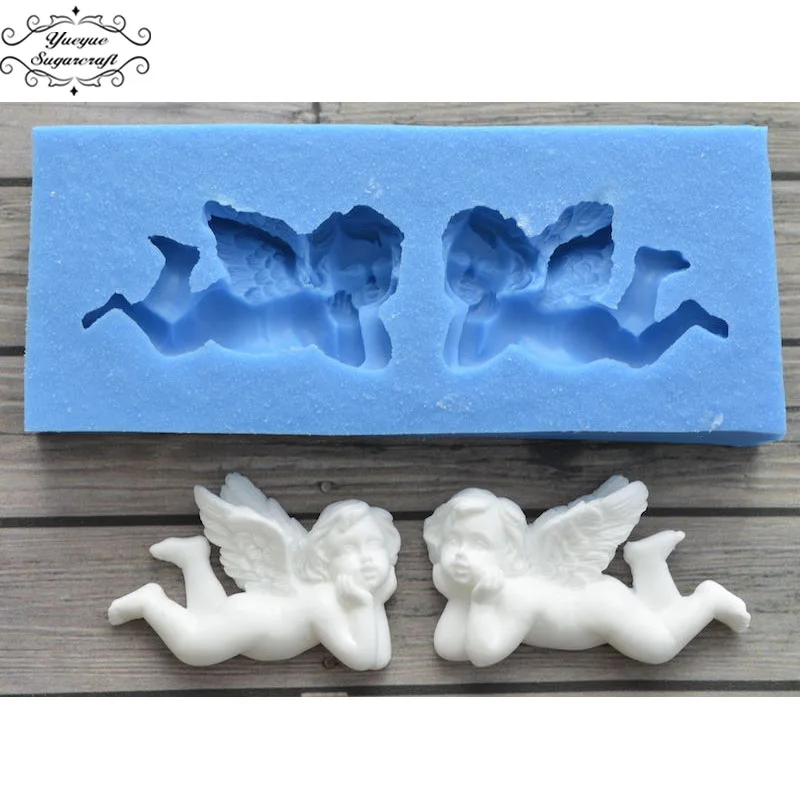
И наконец, в‑пятых, с помощью данной технологии можно изготавливать изделия с компоновкой разных материалов на одной детали, к примеру, жесткий пластик и резиноподобный материал.
Предназначение
Мелкосерийное производство деталей предполагает создание небольших партий изделий, например, изготовление корпусов уникальных приборов, макетов для проверки качества дизайнерских работ, качественных прототипов для проведения презентаций. Выпуск продукции малым тиражом также необходим в случаях функционального тестирования деталей. Небольшая партия отлитых изделий поможет исследовать отклик или провести сертификацию продукции одновременно с производством крупной партии. Подобный подход позволяет выпустить новый продукт на рынок в сжатые сроки при небольших затратах на изготовление.
В Центре объемных технологий 3DVision вы можете заказать услугу литья пластмасс в силиконовые формы. Наши специалисты работают исключительно с оригинальными полимерами на сертифицированном оборудовании, ставя во главу угла качество итоговых изделий.
Услуги: [email protected]
Поставки оборудования и расходных материалов: [email protected]
Тел.: +7 (812) 385–72–92
+7 (495) 662‑98‑58, 8 (800) 333‑07‑58
https://3dvision.su
https://www.instagram.com/3dvision.su
https://vk.com/3dvisionsu
Изготовление силиконовых форм для литья из пластика

— Проектирование пресс-форм проводится специалистами на основании предоставленных заказчиком моделей, прототипов или документации. На этом этапе выполняются расчёты по термостатированию (температура массива внутри пресс-формы должна быть одинаковой), рациональной заливке, учитывается скорость течения пластмассового расплава, требования к прочности пресс-формы, выбор посадок деталей, которые будут сопрягаться.
— Доводка и испытание. Завершающий этап, позволяющий выпустить первые опытные образцы и отправить их на согласование заказчику.

Литьё из пластика под давлением применяется для изготовления изделий из термопластов под давлением от 80 до 140МПа. Работы производятся на специальных поршневых и винтовых машинах с высокой степенью механизации и автоматизации. Машины для литья из пластика самостоятельно дозируют гранулированное сырьё, подогревают его до вязкотекучего состояния и под давлением подают в литьевую форму. После этого форму выдерживают под давлением до затвердевания, размыкают и выталкивают готовые изделия. Завершающей фазой является в случае необходимости, снятие облоя и шлифовка готовых деталей.
На термопластавтоматах изготавливаются средние и большие партии деталей сложной формы, полностью соответствующие проектной документации заказчика. По расположению узла, производящего впрыскивание, бывают:
— автоматы горизонтального впрыскивания, в которых форма расположена в вертикальной плоскости, пластмасса подаётся горизонтально, сбоку;
— автоматы вертикального впрыскивания, в которых форма расположена горизонтально, а пластик подаётся сверху вниз.
Аппараты вертикального впрыскивания используются для получения деталей с закладными.
Существуют способы литья под давлением с использованием дополнительных агентов, улучшающих качество готовых деталей. Это может быть литьё под давлением с использованием инертного газа, который уплотняет пластик и делает его более равномерным. Также существует литьё из пластика с предварительным прогревом пресс-формы водяным паром, позволяющее получать гладкие поверхности и детали, не требующие дополнительной механической обработки. Часто используется также литьё с водой, двухкомпонентное литьё, литьё с применением дополнительного декорирования.
Создание пресс-форм из силикона: практическое руководство
На протяжении истории для изготовления разных вещей, от оружия в бронзовом века до современных потребительских товаров, ремесленники использовали пресс-формы. Первые пресс-формы делали из камня, но современная наука позволила получить материалы, с которыми проще работать, например силикон.
Сегодня литье в силиконовых пресс-формах используется компаниями во многих отраслях. Чтобы создать модель в одном экземпляре или несколько ее партий, силиконовые пресс-формы используют все, от разработчиков продукции и инженеров до любителей творчества и даже шеф-поваров.
В этом практическом руководстве по созданию пресс-форм из силикона мы рассмотрим все вопросы, которые нужно знать перед началом работы. Мы также расскажем о том, что вам для этого потребуется, и пошагово продемонстрируем, как использовать силиконовые пресс-формы в любых проектах.
Технический докладВ этом докладе содержатся практические примеры компаний OXO, Tinta Crayons и Dame Products, иллюстрирующие три различных случая применения литья в силиконовых пресс-формах для разработки и производства продукции, в том числе многослойное литье и литье со вставкой.
Скачать технический докладСиликон — это надежное решение для изготовления пресс-форм. Он обладает множеством преимуществ. С помощью литья в силиконовых пресс-формах можно создавать проекты по индивидуальным параметрам. Сами пресс-формы получаются достаточно прочными. Их можно использовать несколько раз, и они не сломаются. Силикон — это неорганический материал. По сравнению с каучуком, своим органическим аналогом, он обладает высокой устойчивостью к теплу и холоду, воздействию химических веществ и даже образованию плесени. Пресс-формы из силикона обладают следующими преимуществами:
Силикон — гибкий материал. Благодаря этому с ним легко работать. Силиконовые пресс-формы можно сгибать; они мало весят по сравнению с более жесткими материалами, например пластмассой. Из них также легко извлекать отлитые модели. Силикон обладает хорошей гибкостью. Поэтому вероятность того, что силиконовые пресс-формы или отлитые в них модели сломаются, меньше. Пресс-формы из силикона, созданные по индивидуальным параметрам, можно использовать для изготовления любых изделий, от сложных инженерных компонентов до кубиков льда и сладостей к празднику.
Силикон способен выдерживать температуру от -65 до +400 градусов Цельсия. В зависимости от формулы он обладает удлинением до 700 %. У него высокая стойкость к широкому ряду условий: силикон можно поместить в печь или холодильник и растянуть его после этого.
В большинстве случаев одну силиконовую пресс-форму можно использовать много раз. Однако нужно понимать, что срок службы разных пресс-форм может сильно отличаться. Чем чаще выполняется литье и чем сложнее форма создаваемой модели, тем быстрее пресс-форма будет изнашиваться. Чтобы максимально продлить срок службы пресс-форм из силикона, их нужно очищать слабым мыльным раствором, тщательно высушивать и хранить по отдельности, не складывая друг на друга.
Силикон обладает массой преимуществ, но у него есть и ряд ограничений:
Силикон дороже латекса или органического каучука. Если заглянуть на Amazon, то можно найти много предложений по продаже силикона за 100 долларов США, что почти в два раза дороже латекса.
Несмотря на хорошую гибкость, силикон может порваться, если его сильно растянуть.
Силикон создают, применяя разные формулы. Поэтому его и другие материалы для производства нужно покупать у надежного поставщика.
Как любители, так и профессионалы используют пресс-формы из силикона из-за их универсальности и простоты в применении. Вот несколько отраслевых примеров и случаев применения, где их используют для производства продукции:
Литье в силиконовых пресс-формах используется для прототипирования и разработки продукции в различных отраслях. Стоимость силиконовых пресс-форм значительно ниже, чем жестких инструментов для традиционных производственных процессов, таких как литье под давлением. Литье в пресс-формах из силикона отлично подходит для прототипирования конструкций изделий, а также для создания образцов, чтобы проверить потребительский спрос на новую продукцию на рынке. Если 3D-печать лучше подходит для создание моделей в одном экземпляре, то литье в силиконовых пресс-формах и из полиуретана — идеальное решение для мелкосерийного производства моделей.
Ювелиры используют силиконовые пресс-формы для дублирования созданных вручную или напечатанных на 3D-принтере моделей из воска. Это дает им возможность постепенно отказаться от трудоемкой работы, вырезая модели из воска для каждого нового изделия, но при этом продолжать использовать этот материал для литья. Благодаря этому можно совершить значительный скачок в серийном производстве и использовать литье по выплавляемым моделям в заданных масштабах. Так как силиконовые пресс-формы позволяют хорошо передать детали, ювелиры могут создавать изделия с мелким орнаментом и замысловатой геометрической формой.
Силиконовая пресс-форма с вулканизацией при комнатной температуре, наложенная на созданный на 3D-принтере образец.
Мастера используют силиконовые пресс-формы, чтобы создавать изделия ручной работы с индивидуальными параметрами, например, мыло или свечи. Чтобы изготовить продукцию, такую как мел и ластики, пресс-формы из силикона используют даже производители школьных принадлежностей.
Например небольшая австралийский компания Tinta Crayons применяет пресс-формы из силикона для производства цветных восковых мелков с забавной формой и высоким качеством поверхности.
Цветные восковые мелки в виде роботов компании Tinta Crayons, отлитые в силиконовых пресс-формах (источник изображения).
С помощью силиконовых пресс-форм для еды можно создавать различные кондитерские изделия причудливой формы, в том числе шоколад, фруктовый лед и леденцы. Так как силикон выдерживает температуру до 400 градусов Цельсия, такие пресс-формы можно также использовать для запекания. Кроме того, в них хорошо поднимаются маленькие мучные изделия, такие как булочки и кексы.
Независимые художники и любители творчества используют литье в силиконовых пресс-формах для создания уникальных изделий. Их можно применять для придания формы любым предметам и изготовления их копий, от бомб для ванной до лакомств для собак. Возможности практически безграничны. Детям будет интересно создать копию своей руки с помощью литья в силиконовых пресс-формах. Нужно лишь убедиться в том, что используемый силикон безопасен для кожи.
Образец — это модель, которую используют для получения точного ее отпечатка в силиконовой пресс-формы. Если вы просто хотите сделать копию существующего объекта, имеет смысл использовать его в качестве образца. Нужно лишь убедиться в том, что этот объект способен выдержать процесс создания пресс-формы.
Для получения новой конструкции или прототипа сначала нужно изготовить образец. Для этого есть несколько способов. Среди них следующие:
Лепка: если вы талантливый скульптор или создаете модель с относительно простой конструкцией, для изготовления образца можно использовать глину. Лепка образца также будет интересна детям и представляет собой экономичное решение для любителей творчества.
Резьба: образец можно создать с помощью резьбы по дереву. Образцы, вырезанные из дерева, — это отличный выбор для создания плиток и плоских конструкций.
3D-печать: многие профессионалы и проектировщики в компаниях выбирают печать образцов на 3D-принтере. Настольные 3D-принтеры обладают множеством преимуществ. Они дают широкие возможности для проектирования в программном обеспечении САПР, обеспечивают высокую детализацию, легкость при внесении изменений в прототипы, а также быстрое создание моделей.
Получив образец, можно начинать изготовление силиконовой пресс-формы.
Для создания базовой пресс-формы из силикона потребуется следующее:
Образец
Жидкий силикон, например, Smooth-On OOMOO 30
Емкость или беспористый контейнер в качестве корпуса для пресс-формы
Смазка для пресс-формы, например, Smooth-On Universal Mold Release
Воск, полимер или другой материал для конечного использования
Прежде чем приступить к созданию пресс-форм, нужно решить, какие вам нужны.
Однокомпонентные силиконовые пресс-формы похожи на лоток для кубиков льда. В них заливают материал и дают ему затвердеть. Однако, как и в случае с кубиками льда, у которых верхняя поверхность плоская, однокомпонентные пресс-формы подходят только для создания моделей, у которых одна из сторон ровная. Если у вашего образца есть глубокие канавки, после затвердевания силикона его и готовые модели будет сложнее извлечь, не повредив.
Если у вашего образца другая конструкция, то однокомпонентные силиконовые пресс-формы идеально подойдут для непрерывного 3D-воспроизведения всей его поверхности.
Однокомпонентные силиконовые пресс-формы — наилучшее решение для изготовления моделей с плоской стороной и без глубоких канавок.
Для 3D-воспроизведения образца без плоской стороны или с глубокими канавками лучше подойдет двухкомпонентная пресс-форма. Она состоит из двух элементов, которые соединяются и образуют трехмерную полость (аналогично тому, как осуществляется литье под давлением).
У двухкомпонентных пресс-форм нет плоских поверхностей, и с ними проще работать, чем с формами, состоящими из одного компонента. Из недостатков: их немного сложнее изготовить. Также на поверхности моделей могут оставаться швы, если компоненты пресс-формы не расположить вровень друг с другом.
С помощью двухкомпонентных пресс-форм можно воспроизводить образцы с любой конструкцией (источник изображения)
Сначала нужно решить, какую пресс-форму использовать: одну- или двухкомпонентную. Процесс их изготовления схож, но на создание двухкомпонентной пресс-формы потребуется немного больше времени. Для изготовления силиконовых пресс-форм можно использовать следующие пошаговые инструкции.
Создайте образец вашего изделия: это ваш окончательный проект модели, которая будет воспроизведена из другого материала. При печати на стереолитографическом 3D-принтере используйте стандартные полимеры с высотой слоя 50 мкм. На детализированной поверхности не должно быть следов от поддерживающих структур.
Промойте модели с помощью ИПС. Если поверхность остается липкой, это может повлиять на процесс литья в силиконовых пресс-формах.
Создайте корпус для пресс-формы: популярное решение для изготовления емкости для пресс-формы — ДВП с порошковой окраской, но подойдет и обычный пластиковый контейнер. Материалы должны быть беспористыми и с плоским дном.
Расположите образец и нанесите смазку для литья: нанесите немного смазки на внутреннюю поверхность корпуса для пресс-формы. Поместите образцы в емкость так, чтобы их детализированная поверхность была обращена вверх. Нанесите на них небольшой слой смазки для литья. Подождите 10 минут, пока они полностью высохнут.
Приготовьте силикон: смешайте силиконовый каучук в соответствии с указаниями на упаковке. Для удаления пузырьков воздуха можно использовать устройства, создающие вибрацию, такие как ручная электрошлифовальная машина.
Залейте силикон в корпус для пресс-формы: осторожно залейте смешанный силиконовый каучук в емкость узкой струей.
Сначала заливайте каучук в нижнюю часть емкости (основание) и постепенно поднимайтесь по контурам образца, напечатанного на 3D-принтере. Толщина слоя каучука сверху образца должна быть не менее одного сантиметра. В зависимости от типа и торговой марки силикона процесс затвердевания займет от одного часа до дня.
Извлеките силикон из емкости: после того как силикон затвердеет, извлеките его и образцы из емкости. Полученная форма будет использоваться наподобие лотка для льда, чтобы изготовить продукцию для конечного использования.
Отлейте вашу модель: рекомендуется нанести небольшой слой смазки на силиконовую пресс-форму и дать ей высохнуть в течение 10 минут. Залейте материал для конечного использования (например, воск или цемент) в полости и дайте ему затвердеть.
Подготовьте пресс-форму к следующей заливке: силиконовую пресс-форму можно использовать много раз. Перейдите к седьмому пункту и повторите процесс.
Чтобы создать двухкомпонентную силиконовую пресс-форму, выполните первые два действия, указанные выше: создайте образец и корпус для пресс-формы. После этого выполните следующие действия:
Расположите образцы в корпусе, поместив их в глину: чтобы сформировать половину пресс-формы, используйте глину. Глину нужно выложить в корпус для пресс-формы. Образец нужно вставить в глину наполовину.
Приготовьте силикон и залейте его: приготовьте силикон, следуя указаниям на его упаковке, и осторожно залейте его поверх глины и образцов. Залитый слой силикона — это первая половина двухкомпонентной пресс-формы.
Извлеките все содержимое из корпуса для пресс-формы: после того как первая половина затвердеет, извлеките ее, образцы и глину из корпуса для пресс-формы. При извлечении содержимого допускается отделение слоев друг от друга.
Выполните очистку от глины: полностью очистите первую половину пресс-формы и образцы от глины.
Образцы и полученная часть пресс-формы должны быть абсолютно чистыми.
Поместите пресс-форму и образцы обратно в корпус: снова поместите полученную часть пресс-формы со вставленными в нее образцами в корпус так, чтобы они были обращены вверх, а не вниз.
Нанесите слой смазки для литья: чтобы проще было извлечь второй компонент пресс-формы, нанесите тонкий слой смазки на верхнюю поверхность образца и первой части пресс-формы.
Приготовьте силикон и залейте его для получения второй части пресс-формы: следуя приведенным ранее указаниям, приготовьте и залейте силикон в корпус, чтобы получить второй компонент пресс-формы.
Дождитесь, пока вторая часть пресс-формы затвердеет: прежде чем извлечь второй компонент пресс-формы из корпуса, дождитесь, пока она затвердеет.
Извлеките модели: извлеките обе части пресс-формы из корпуса и аккуратно отсоедините их друг от друга.
Будь то еда, фигурки или коммерческие компоненты, единственно верного способа производства продукции в целом не существует. Для достижения наилучших результатов зачастую используется сочетание разных методов. Чтобы принимать наиболее эффективные решения в рамках своего проекта, важно знать о преимуществах и недостатках каждого из них.
Хотите узнать о других методах литья в пресс-формах и случаях их применения? Скачайте наш технический доклад «Прессование из силикона для разработки продукции».
Технология
Технология
Технология литья в силиконовые формы заключается в том, что конечный результат является точной копией образцовой формы. Форма производится посредством заливания силикона вокруг модели. Затем силикон затвердевает в процессе охлаждения. Модель изымается из разрезанной формы и продукция готова.
Смолы для литья в вакуумной среде помогают воспроизвести любые текстуры и цвета объекта. Это помогает имитации различных использующихся на современном производстве пластмасс и полимеров.
Полный цикл предлагаемого мелкосерийного производства деталей из пластмассы включает в себя следующие этапы.
Этап 1.
Создание мастер-модели методами 3D печати, сканирования и т.д.
Все начинается с создания, так называемой «мастер-модели», на базе которой будет создаваться оснастка (форма) из силикона. Мастер-модель должна иметь точные геометрические формы и размеры. В простейшем случае подобную модель предоставляет Заказчик, но, чаще всего, такой прототип создается нашими специалистами с применением методов 3D-печати, например, из гипсополимера или фотополимера.
В качестве основы для 3D-печати используется трехмерная компьютерная модель (CAD-модель), которая может разрабатываться «с нуля» или на основе доработки результатов 3D-сканирования.
Этап 2.
Подготовка мастер-модели, монтаж опалубки и формирование литниковой системы.
Для получения качественной формы необходимо выполнить ряд мероприятий по подготовке самой мастер-модели к заливке и продуманному формированию будущей литниковой системы.
На все сквозные отверстия мастер-модели с одной из сторон наклеивается специальный скотч (он очень тонкий), который обеспечит разделение силикона на выбранном конце отверстия. Несквозные отверстия модели скотчем не заклеиваются.
Также с помощью наклейки скотча формируется будущая линия разъема (разделения) силиконовой формы. Обычно клейкая лента наклеивается на один из торцов модели, по которой в будущем форма будет разделяться. Применение тонкого скотча позволяет получать очень ровные кромки будущих отливок из полиуретана.
Если будущее изделие должно иметь поверхность, отличную от гладкой, то на поверхность мастер-модели может быть нанесен лак с различными наполнителями, имитирующими требуемую текстуру (матовую, шагрень, древесины, порошкового покрытия и т.д.).
В дальнейшем мастер-модель помещается (подвешивается) в заранее подготовленную опоку (опалубку). С помощью трубок формируется литниковая система, т.е. система каналов и полостей в будущей силиконовой форме, предназначенная для плавной подачи полиуретана, управления его плавным затвердеванием и вывода воздуха.
Значимое преимущество использования вакуумной камеры, состоит в том, что за счет дифференциальной системы организации разрежения нет необходимости в создании сложных лютниковых систем с множеством прибылей, коллекторов и пр. В данном случае достаточно трубки для поступления полиуретана и трубки (выпора) для удаления из формы воздуха. За счет вакуума пластик полностью заполнит все пространство формы, и нет необходимости прилагать дополнительные усилия для устранения усадочных раковин и прочих возможных дефектов, присущих традиционному литью пластмасс.
Этап 3.
Формирование силиконовой формы.
Чем качественнее будет изготовлена форма, тем качественнее будет результирующая продукция. Именно поэтому мы применяем только высококачественный итальянский силикон. Для его приготовления используются два компонента, которые перемешиваются на воздухе с помощью специальной мешалки.
Разумеется, при активном перемешивании в структуру силикона попадает множество воздушных пузырьков. Для их удаления силикон, после перемешивания, помещается на 10-15 минут в вакуумную камеру V 1500 A, где происходит так называемая дегазация силиконовой массы.
После дегазация емкость с силиконом вынимается из вакуумной камеры и силикон заливается в подготовленную опалубку с мастер-моделью и литниковой системой. После заливки, в течение примерно 16 часов происходит застывание силикона.
Отметим, что с помощью одной силиконовой формы можно отлить до 20-30 (иногда до 80) изделий из полиуретана. Если заказ превышает данное количество, мы изготовим необходимое дополнительное количество таких форм.
Этап 4.
Литье пластмасс в форму из силикона.
Дальнейшие этапы работы осуществляются гораздо быстрее. Для начала литья необходимо вновь собрать силиконовую форму. Для этого все ее части «складывают» и скрепляют с помощью скотча и скоб степлера. Особое внимание уделяется закреплению элементов формы, формирующих в заготовке сквозные отверстия. По готовности формы она, уже без деревянной опалубки, помещается в вакуумную камеру. Для закрепления силиконовой формы в ней используются специальные микролифты камеры.
После помещения в вакуумную камеру силиконовой формы и компонентов полиуретана, в камере создается разрежение (в пределе до 0,5 мбар). В условиях вакуума происходит смешивание и дегазация компонентов полиуретана. Далее готовая смесь через воронку и лютниковую систему заливается в форму. При этом через выпор из формы удаляются остатки воздуха.
После того, как заготовка полностью станет твердой, форма разбирается (удаляются скобы степлера, надрезается скотч), готовое изделие извлекается. В дальнейшем форма может быть использована еще 20-30 раз.
Получившиеся изделия из полиуретана можно механически обрабатывать (шлифовать, сверлить и пр.), окрашивать и т.д.
Литье пластмассовых изделий в силиконовые формы
Литье пластмассовых изделий в силиконовые формыВакуумное литье в силиконовые (эластичные) формы (Vacuum Casting) – это процесс производства пластмассовых изделий или изделий из резины, а также копий деталей из пластика. Это могут быть прототипы, опытные образцы, а также небольшие партии деталей из пластика практически любой сложности и габаритов без использования металлической дорогой оснастки. Изготовление формы происходит путем заливки силикона в опалубку с расположенной внутри мастер-моделью. После полимеризации силикона осуществляется литье в силиконовые формы.
Технология позволяет за несколько дней получать небольшие (от 1 до 1000 шт.) партии пластиковых изделий благодаря быстроте изготовления оснастки.
ударопрочные пластики
Эмитируют ABS и ПВХ. Подходят для ударопрочных деталей, тонкостенных деталей со сложной структурой поверхности
резины разной твердости
Износостойкие резины. Твердость по Шору А от 30 до 90. Имеют необычайную прочность и устойчивость к истиранию.
био-силиконы
Биосовместимый, гипоаллергенный силикон, сертифицирован по ISO 10993-10. Медицинский силикон
самозатухающий пластик
Материалы соответствуют стандартам FAR 25. 853 по пожаробезопасности. Сертификация ВИАМ
термостойкие пластики
Прекрасно выдерживают нагрев до 100C°, не проявив при этом деформации, сохраняют целостность и форму
прозрачные пластики
Прозрачные, гибкие, стойкие к УФ- излучению. Яркие цвета, а также цветовые эффекты достигаются добавкой пигментов
Или почему вам нужно заказать именно у нас
01. ФАКТУРА ПОВЕРНОСТЕЙ
Ровная матовая, крупный и мелкий песок, глянцевая, шагрень. Фактура полностью повторяет фактуру оригинала, вплоть до отпечатков пальцев.
02. ЦВЕТ ИЗДЕЛИЙ
Окрашивание материалов из палитры RAL. Цвет резины — любой, кроме белого и светло-бежевого, т.к. изначально резина янтарного цвета. Подбор цвета по оригиналу или по RAL.
03. ЗАКЛАДНЫЕ ЭЛЕМЕНТЫ
Возможно армирование деталей различными закладными элементами. Обрезинивание металлических элементов, ручек, рычагов.
04. ПРОИЗВОДСТВО МАСТЕР-МОДЕЛЕЙ
Если у вас нет образца для снятия формы, мы изготовим его для вас.
Сделать расчет
×
Мне нужен расчет
×
Получить консультацию
×
Обратная связь
×
Литье пластмасс и полиуретанов в силиконовые формы в Санкт-Петербурге
На современных производствах пластмассовых изделий используются разные технологии литья пластика. Это может быть литье полиуретанов с помощью газа, с подачей водяного пара, многокомпонентное литье или с одновременно выполняемой сборкой.
«Инженерные технологиии» используют инновационный метод в данной производственной сфере — литье пластиков в силиконовые формы в вакууме.
Такая технология позволяет изготовлять пластиковые отливки в гибкой оснастке — это особенно важно в тех случаях, когда необходимо в точности повторить текстуру и очень мелкие детали.
Благодаря 3д печати и литью пластика в силиконовые формы производство вышло на новый уровень: теперь не нужно тратиться на дорогие материалы пресс-форм, а срок изготовления таких партий заметно сократился. Теперь нет необходимости ориентироваться на крупносерийное производство: выпуск небольшого количества изделий — более распространенный тип заказа для среднестатистического заказчика.
Изготовление силиконовых форм для литья — отдельный процесс, который достоин пристального внимания потребителя. Данная технология обладает целым рядом преимуществ: силиконовая форма производится намного быстрее, чем пресс-форма, она дешевле, чем ее металический аналог. Одна форма может заливаться до 20-30 раз — этот фактор зависит от конкретного типа используемого полиуретана.
Теперь опишем технологию литья в нескольких этапах:
Подготовка прототипа детали
Крайне важный этап, на котором доводится мастер — модель, что станет образцом для всей партии. Особое внимание уделяется требованиям по шероховатости и точности исполнения деталей. В качестве прототипа здесь выступает образец выполненный методом 3d печати из фотополимера.
Изготовление силиконовых форм
После того, как прототип готов, он помещается в специальную опалубку и надёжно фиксируется в ней. В полученную систему запивается силикон, который полимеризуется по определенному технологическому режиму и становится формой для литья.
Изготовление партии пластмассовых изделий
На финальном этапе литья пластмасс в силиконовые формы, в основном, используются полиуретаны фирмы Synthene. Вы всегда можете подобрать тот, который по своим физико-механическим свойствам больше всего будет подходить по цвету и максимально соответствовать материалу серийного изготовления изделия.
Литье в силиконовые формы на заказ, заказать изделия и услугу литья деталей в силиконовые формы в Санкт-Петербурге
Компания Go&Make изготовит пластиковые изделия методом литья в силиконовые формы. Способ подходит для серийного производства – сделанные один раз пресс-формы из силикона позволяют отлить до 50 экземпляров полностью идентичных образцов. Работа выполняется в несколько этапов: сначала на 3d-принтере печатают прототип, по нему делают силиконовые пресс-формы, которые служат формообразующей оснасткой для литья в них разогретого до температуры плавления пластика.
Заказать литье в силиконовые формы
Стоимость
Стоимость отливки партии пластиковых изделий складывается из нескольких составляющих:
- Оплаты услуги компьютерного моделирования.
- Расходов на прототипирование – печать на 3d-принтере макета, отливку по нему силиконовых форм.
- Вида материала, из которого отливаются изделия (реактопласты, полимерные смолы).
- Тиража – 10–50 штук.
Чем больше образцов отливаются из пресс-формы, тем дешевле себестоимость одного экземпляра. Мы делаем силиконовые формы достаточно стойкие, чтобы без дефектов отлить большую партию.
Сроки выполнения
На выполнение каждого вида работ требуется определенное время:
- проектирование 3d-модели – 1–3 дня;
- печать прототипа на 3d-принтере – 1–7 дней;
- изготовление литьевых форм из силикона по прототипу – до 5 дней;
- литьё в пресс-формы из силикона – 1–10 дней.
Сроки выполнения заказа согласовываются с клиентом заранее, прописываются в договоре. Мы стараемся выдать готовую продукцию в оговоренный срок, работаем быстро.
Требования для файлов
Файл с 3д-моделью принимаем в формате .obj или . stl. Услуги по конвертации из другого формата файла оплачиваются дополнительно. Если 3d-модели нет, заказать 3д-моделирование можно у нас, выслав чертежи, фото или предоставив готовый образец.
В каких случаях заказывают литье в силиконовые формы
Частные лица и организации могут заказать у нас разноплановую пластиковую продукцию:
- запчасти для промышленной или бытовой техники, которые дорого заказывать у производителя;
- дубликаты или точные копии потребительских товаров;
- тестовые образцы деталей перед запуском их в производство;
- изделия небольшим тиражом, которые невозможно или невыгодно изготавливать самому.
Наши расценки невысокие, обоснованы себестоимостью, а литье выполняется с соблюдением технологий. Каждую партию сдаем в срок.
Заказать литье в силиконовые формы
Mold Star ™ 15 SLOW Информация о продукте
Инструкции
Примечание. Этот продукт не отверждает поверхности, содержащие серу, даже в герметичном состоянии.
Безопасность — Использование в хорошо проветриваемом помещении (вентиляция «размером с комнату»). Надевайте защитные очки, длинные рукава и резиновые перчатки, чтобы свести к минимуму риск загрязнения. Используйте только виниловые перчатки. Латексные перчатки препятствуют отверждению резины. Храните и используйте материал при комнатной температуре (73 ° F / 23 ° C). Более высокие температуры резко сокращают рабочее время и время отверждения. Хранение материала при более высоких температурах также сократит срок годности неиспользованного материала. Эти продукты имеют ограниченный срок хранения, и их следует использовать как можно скорее.
Ингибирование отверждения — Силиконовый каучук дополнительного отверждения может ингибироваться определенными загрязнителями в или на формованном шаблоне, что приводит к липкости на границе раздела шаблона или к полному отсутствию вулканизации по всей форме. Латекс, серные глины, некоторые деревянные поверхности, недавно отлитый полиэстер, эпоксидная смола или уретановый каучук могут вызывать ингибирование. Если совместимость резины и поверхности вызывает беспокойство, рекомендуется провести небольшой тест. Нанесите небольшое количество резины на некритическую область рисунка. Ингибирование произошло, если резина стала клейкой или неотвержденной по прошествии рекомендованного времени отверждения. Чтобы предотвратить ингибирование, обычно эффективно наносят одно или несколько слоев прозрачного акрилового лака на поверхность модели.Перед нанесением резины дайте герметику полностью высохнуть.
Даже с герметиком силиконы Mold Star ™ не отверждают поверхности, содержащие серу. Если вы не уверены, что ваша глина содержит серу, сделайте небольшой тест на совместимость, прежде чем использовать ее для важного проекта.
Применение разделительного агента — Хотя обычно в этом нет необходимости, разделительный агент облегчит извлечение из формы при заливке в большинство поверхностей. Ease Release ™ 200 — это хорошо зарекомендовавший себя разделительный агент для отделения силикона от силикона или других поверхностей.Продукты Mann Ease Release ™ можно приобрести у Smooth-On или у вашего дистрибьютора Smooth-On.
Поскольку нет двух совершенно одинаковых приложений, рекомендуется небольшое тестовое приложение для определения пригодности для вашего проекта, если производительность этого материала находится под вопросом.
Измерение и смешивание — Перед тем, как начать, предварительно смешайте компоненты A и B по отдельности. После внесения необходимого количества частей A и B в емкость для смешивания (1A: 1B по объему), тщательно перемешайте , убедившись, что вы поскребите по бокам и дну емкости для смешивания несколько раз. Резина должна быть однородного цвета без разводов.
Дополнительно … Вакуумная дегазация — Хотя это и не обязательно, вакуумная дегазация помогает удалить любой воздух, захваченный в жидкой силиконовой резине. После смешивания частей A и B, вакуумируйте материал в течение 2–3 минут при давлении 29 дюймов ртутного столба, убедившись, что в контейнере остается достаточно места для расширения продукта.
Заливка — Для достижения наилучших результатов вылейте смесь в одну точку в самой нижней точке защитного поля.Пусть резина ищет свой уровень. Равномерный поток поможет свести к минимуму попадание воздуха. При использовании в качестве материала пресс-формы жидкая резина должна выравниваться по крайней мере на 1/2 дюйма (1,3 см) над самой высокой точкой поверхности модели.
Отверждение — Силиконовый каучук Mold Star ™ 15 SLOW должен затвердеть в течение 4 часа при комнатной температуре (73 ° F / 23 ° C) перед извлечением из формы.
Тепловое отверждение — Время демонтажа формы можно сократить, приложив умеренный нагрев. Пример: После заливки резины Mold Star ™ 15 при комнатной температуре поместите форму в горячий ящик или промышленную печь при 140 ° F (60 ° C). Это сократит время извлечения из формы секции толщиной 1/2 дюйма (1,3 см) примерно до 10 минут. Примечание: Время зависит от толщины формы.
Добавление соответствующего количества ускорителя отверждения Plat-Cat ™ также сократит время извлечения из формы. Жизнеспособность и время отверждения можно увеличить с помощью замедлителя отверждения Slo-Jo ™ .Не вулканизируйте резину при температуре ниже 18 ° C / 65 ° F.
Производительность и хранение пресс-формы — Физический срок службы пресс-формы зависит от того, как вы ее используете (литье материалов, частота и т. Д.). Отливка абразивных материалов может быстро разрушить детали формы, в то время как отливка неабразивных материалов (воск) не повлияет на детали формы. Перед хранением форму следует очистить мыльным раствором и вытереть насухо. Должны быть собраны две (или более) части формы. Формы следует хранить на ровной поверхности в прохладном и сухом месте.
Mold Star ™ 30 Информация о продукте
Инструкции
Безопасность — Использование в хорошо проветриваемом помещении (вентиляция «размером с комнату»). Надевайте защитные очки, длинные рукава и резиновые перчатки, чтобы свести к минимуму риск загрязнения. Используйте только виниловые перчатки. Латексные перчатки препятствуют отверждению резины. Храните и используйте материал при комнатной температуре (73 ° F / 23 ° C). Более высокие температуры резко сокращают рабочее время и время отверждения.Хранение материала при более высоких температурах также сократит срок годности неиспользованного материала. Эти продукты имеют ограниченный срок хранения, и их следует использовать как можно скорее.
Ингибирование отверждения — Силиконовый каучук дополнительного отверждения может ингибироваться определенными загрязнителями в или на формованном шаблоне, что приводит к липкости на границе раздела шаблона или к полному отсутствию вулканизации по всей форме. Латекс, серные глины, некоторые деревянные поверхности, недавно отлитый полиэстер, эпоксидная смола или уретановый каучук могут вызывать ингибирование.Если совместимость резины и поверхности вызывает беспокойство, рекомендуется провести небольшой тест. Нанесите небольшое количество резины на некритическую область рисунка. Ингибирование произошло, если резина стала клейкой или неотвержденной по прошествии рекомендованного времени отверждения. Чтобы предотвратить ингибирование, обычно эффективно наносят одно или несколько слоев прозрачного акрилового лака на поверхность модели. Перед нанесением резины дайте герметику полностью высохнуть.
Даже с герметиком силиконы Mold Star ™ не отверждают поверхности, содержащие серу.Если вы не уверены, что ваша глина содержит серу, сделайте небольшой тест на совместимость, прежде чем использовать ее для важного проекта.
Применение разделительного агента — Хотя обычно в этом нет необходимости, разделительный агент облегчит извлечение из формы при заливке в большинство поверхностей. Ease Release ™ 200 — это хорошо зарекомендовавший себя разделительный агент для отделения силикона от силикона или других поверхностей. Продукты Mann Ease Release ™ можно приобрести у Smooth-On или у вашего дистрибьютора Smooth-On.
Поскольку нет двух совершенно одинаковых приложений, рекомендуется небольшое тестовое приложение для определения пригодности для вашего проекта, если производительность этого материала находится под вопросом.
Измерение и смешивание — Перед тем, как начать, предварительно смешайте части A и B по отдельности. После внесения необходимого количества частей A и B в емкость для смешивания (1A: 1B по объему), тщательно перемешайте , убедившись, что вы несколько раз соскоблите по бокам и дну емкости для смешивания. Резина должна быть однородного цвета без разводов.
Дополнительно … Вакуумная дегазация — Хотя это и не обязательно, вакуумная дегазация помогает удалить любой воздух, захваченный в жидкой силиконовой резине. После смешивания частей A и B, вакуумируйте материал в течение 2–3 минут при давлении 29 дюймов ртутного столба, убедившись, что в контейнере остается достаточно места для расширения продукта.
Заливка — Для достижения наилучших результатов вылейте смесь в одну точку в самой нижней точке защитного поля. Пусть резина ищет свой уровень. Равномерный поток поможет свести к минимуму попадание воздуха. При использовании в качестве материала пресс-формы жидкая резина должна выравниваться по крайней мере на 1/2 дюйма (1,3 см) над самой высокой точкой поверхности модели.
Отверждение — Mold Star ™ 30 Перед извлечением из формы необходимо дать отвердеть в течение 6 часов при комнатной температуре (73 ° F / 23 ° C).
Тепловое отверждение — Время демонтажа формы можно сократить, приложив умеренный нагрев. Пример: После заливки резины Mold Star ™ 16 при комнатной температуре поместите форму в горячий ящик или промышленную печь при 140 ° F (60 ° C). Это сократит время извлечения из формы секции толщиной 1/2 дюйма (1,3 см) примерно до 10 минут. Примечание: Время зависит от толщины формы.
Добавление соответствующего количества ускорителя отверждения Plat-Cat ™ также сократит время извлечения из формы. Жизнеспособность и время отверждения можно увеличить с помощью замедлителя отверждения Slo-Jo ™ . Не вулканизируйте резину при температуре ниже 18 ° C / 65 ° F.
Производительность и хранение пресс-формы — Физический срок службы пресс-формы зависит от того, как вы ее используете (литье материалов, частота и т. Д.). Отливка абразивных материалов может быстро разрушить детали формы, в то время как отливка неабразивных материалов (воск) не повлияет на детали формы.Перед хранением форму следует очистить мыльным раствором и вытереть насухо. Должны быть собраны две (или более) части формы. Формы следует хранить на ровной поверхности в прохладном и сухом месте.
Mold Star ™ 16 FAST Информация о продукте
Инструкции
Примечание. Этот продукт не отверждает поверхности, содержащие серу, даже в герметичном состоянии.
Безопасность — Использование в хорошо проветриваемом помещении (вентиляция «размером с комнату»).Надевайте защитные очки, длинные рукава и резиновые перчатки, чтобы свести к минимуму риск загрязнения. Используйте только виниловые перчатки. Латексные перчатки препятствуют отверждению резины. Храните и используйте материал при комнатной температуре (73 ° F / 23 ° C). Более высокие температуры резко сокращают рабочее время и время отверждения. Хранение материала при более высоких температурах также сократит срок годности неиспользованного материала. Эти продукты имеют ограниченный срок хранения, и их следует использовать как можно скорее.
Ингибирование отверждения — Силиконовый каучук дополнительного отверждения может ингибироваться определенными загрязнителями в или на формованном шаблоне, что приводит к липкости на границе раздела шаблона или к полному отсутствию вулканизации по всей форме. Латекс, серные глины, некоторые деревянные поверхности, недавно отлитый полиэстер, эпоксидная смола или уретановый каучук могут вызывать ингибирование. Если совместимость резины и поверхности вызывает беспокойство, рекомендуется провести небольшой тест. Нанесите небольшое количество резины на некритическую область рисунка. Ингибирование произошло, если резина стала клейкой или неотвержденной по прошествии рекомендованного времени отверждения. Чтобы предотвратить ингибирование, обычно эффективно наносят одно или несколько слоев прозрачного акрилового лака на поверхность модели.Перед нанесением резины дайте герметику полностью высохнуть.
Даже с герметиком силиконы Mold Star ™ не отверждают поверхности, содержащие серу. Если вы не уверены, что ваша глина содержит серу, сделайте небольшой тест на совместимость, прежде чем использовать ее для важного проекта.
Применение разделительного агента — Хотя обычно в этом нет необходимости, разделительный агент облегчит извлечение из формы при заливке в большинство поверхностей. Ease Release ™ 200 — это хорошо зарекомендовавший себя разделительный агент для отделения силикона от силикона или других поверхностей.Продукты Mann Ease Release ™ можно приобрести у Smooth-On или у вашего дистрибьютора Smooth-On.
Поскольку нет двух совершенно одинаковых приложений, рекомендуется небольшое тестовое приложение для определения пригодности для вашего проекта, если производительность этого материала находится под вопросом.
Измерение и смешивание — Перед тем, как начать, предварительно смешайте компоненты A и B по отдельности. После внесения необходимого количества частей A и B в емкость для смешивания (1A: 1B по объему), тщательно перемешайте , убедившись, что вы поскребите по бокам и дну емкости для смешивания несколько раз. Резина должна быть однородного цвета без разводов.
Дополнительно … Вакуумная дегазация — Хотя это и не обязательно, вакуумная дегазация помогает удалить любой воздух, захваченный в жидкой силиконовой резине. После смешивания частей A и B, вакуумируйте материал в течение 2–3 минут при давлении 29 дюймов ртутного столба, убедившись, что в контейнере остается достаточно места для расширения продукта.
Заливка — Для достижения наилучших результатов вылейте смесь в одну точку в самой нижней точке защитного поля.Пусть резина ищет свой уровень. Равномерный поток поможет свести к минимуму попадание воздуха. При использовании в качестве материала пресс-формы жидкая резина должна выравниваться по крайней мере на 1/2 дюйма (1,3 см) над самой высокой точкой поверхности модели.
Отверждение — Дайте силиконовому каучу Mold Star ™ 16 FAST отвердеть в течение 30 минут при комнатной температуре (23 ° C) перед извлечением из формы.
Тепловое отверждение — Время демонтажа формы можно сократить, приложив умеренный нагрев. Пример: После заливки резины Mold Star ™ 16 при комнатной температуре поместите форму в горячий ящик или промышленную печь при 140 ° F (60 ° C). Это сократит время извлечения из формы секции толщиной 1/2 дюйма (1,3 см) примерно до 10 минут. Примечание: Время зависит от толщины формы.
Добавление соответствующего количества ускорителя отверждения Plat-Cat ™ также сократит время извлечения из формы. Жизнеспособность и время отверждения можно увеличить с помощью замедлителя отверждения Slo-Jo ™ .Не вулканизируйте резину при температуре ниже 18 ° C / 65 ° F.
Производительность и хранение пресс-формы — Физический срок службы пресс-формы зависит от того, как вы ее используете (литье материалов, частота и т. Д.). Отливка абразивных материалов может быстро разрушить детали формы, в то время как отливка неабразивных материалов (воск) не повлияет на детали формы. Перед хранением форму следует очистить мыльным раствором и вытереть насухо. Должны быть собраны две (или более) части формы. Формы следует хранить на ровной поверхности в прохладном и сухом месте.
Mold Star ™ 31T Информация о продукте
Характеристики
Mold Star ™ 31T при отверждении превращается в мягкую, прочную резину, устойчивую к разрыву и демонстрирующую очень низкую длительную усадку. Формы, изготовленные из Mold Star ™, прослужат долго в вашей библиотеке форм и подходят для литья воска, гипса, смол и других материалов. Бесконечное количество цветовых эффектов может быть достигнуто путем добавления силиконовых пигментов Silc Pig ™ или порошковых эффектов Cast Magic ™.
Mold Star ™ 31T обладает термостойкостью до 450 ° F (232 ° C) и подходит для литья низкотемпературных расплавов металлических сплавов.
Примечание. Этот продукт не будет отверждать против поверхностей, содержащих серу, даже в герметичном состоянии.
Cured Mold Star ™ 31T безопасен для кожи и сертифицирован независимой лабораторией.
› Нажмите здесь, чтобы увидеть больше силиконовых продуктов Mold Star ™.Инструкции
Безопасность — Использование в хорошо проветриваемом помещении (вентиляция «размером с комнату»).Надевайте защитные очки, длинные рукава и резиновые перчатки, чтобы свести к минимуму риск загрязнения. Используйте только виниловые перчатки. Латексные перчатки препятствуют отверждению резины.
Хранить и использовать материал при комнатной температуре (73 ° F / 23 ° C) . Более высокие температуры резко сократят рабочее время и время отверждения. Хранение материала при более высоких температурах также сократит срок годности неиспользованного материала. Эти продукты имеют ограниченный срок хранения, и их следует использовать как можно скорее.
Ингибирование отверждения — Силиконовый каучук дополнительного отверждения может ингибироваться определенными загрязнителями в или на формованном шаблоне, что приводит к липкости на границе раздела шаблона или к полному отсутствию вулканизации по всей форме.Латекс, серные глины, некоторые деревянные поверхности, недавно отлитый полиэстер, эпоксидная смола, силиконовый каучук, отверждаемый оловом, или уретановый каучук могут вызывать ингибирование. Если совместимость резины и поверхности вызывает беспокойство, рекомендуется провести небольшой тест. Нанесите небольшое количество резины на некритическую область рисунка. Ингибирование произошло, если резина стала клейкой или неотвержденной по прошествии рекомендованного времени отверждения. Чтобы предотвратить ингибирование, обычно эффективно наносят одно или несколько слоев прозрачного акрилового лака на поверхность модели.Перед нанесением резины дайте герметику полностью высохнуть.
Даже с герметиком Mold Star ™ 31T не отвердит против поверхностей, содержащих серу. Если вы не уверены, что ваша глина содержит серу, сделайте небольшой тест на совместимость, прежде чем использовать ее для важного проекта.
Нанесение разделительного агента — Хотя обычно в этом нет необходимости, разделительный агент облегчит извлечение из формы при заливке в большинство поверхностей. Ease Release ™ 200 — это хорошо зарекомендовавший себя разделительный агент для отделения силикона от силикона или других поверхностей.Продукты Mann Ease Release ™ можно приобрести у Smooth-On или у вашего дистрибьютора Smooth-On. B , поскольку нет двух совершенно одинаковых приложений, рекомендуется небольшое тестовое приложение для определения пригодности для вашего проекта, если производительность этого материала находится под вопросом.
ИЗМЕРЕНИЕ И СМЕШИВАНИЕ …
Перед тем, как начать, отдельно предварительно смешайте Часть A и Часть B. После внесения необходимого количества частей A и B в емкость для смешивания (1A: 1B по объему или весу), тщательно перемешайте, убедившись, что вы несколько раз соскребли стенки и дно емкости для смешивания.
Дополнительно … Вакуумная дегазация — Хотя это и не обязательно, вакуумная дегазация помогает удалить любой воздух, захваченный в текучей силиконовой резине. После смешивания частей A и B, вакуумируйте материал в течение 2–3 минут при давлении 29 дюймов ртутного столба, убедившись, что в контейнере остается достаточно места для расширения продукта.
РАЗЛИВКА, ОТВЕРЖДЕНИЕ И РАБОЧИЕ ХАРАКТЕРИСТИКИ …
Заливка — Для достижения наилучших результатов вылейте смесь в одну точку в самой нижней точке защитного поля.Пусть резина ищет свой уровень. Равномерный поток поможет свести к минимуму попадание воздуха. При использовании в качестве материала пресс-формы жидкая резина должна выравниваться по крайней мере на 1/2 дюйма (1,3 см) над самой высокой точкой поверхности модели.
Отверждение — Перед извлечением из формы дайте резине застыть в течение 23 минут при комнатной температуре (73 ° F / 23 ° C). Отверждение при нагревании — Время демонтажа формы можно сократить с помощью умеренного нагрева. Пример: После заливки Mold Star ™ 31T при комнатной температуре поместите форму в горячий ящик или промышленную духовку при 140 ° F (60 ° C).Это может существенно сократить время извлечения из формы. Примечание — время зависит от толщины формы.
Создание кисти на форме? — Силикон Mold Star ™ 20T может быть загущен с помощью загустителя THI-VEX ™ для нанесения кистью и создания эффектов. Не используйте другие силиконы серии Mold Star ™ для изготовления форм кистью.
Производительность и хранение пресс-формы — Физический срок службы пресс-формы зависит от того, как вы ее используете (литье материалов, частота и т. Д.). Отливка абразивных материалов может быстро разрушить детали формы, в то время как отливка неабразивных материалов (воск) не повлияет на детали формы. Перед хранением форму следует очистить мыльным раствором и вытереть насухо. Должны быть собраны две (или более) части формы. Формы следует хранить на ровной поверхности в прохладном и сухом месте.
Смолы для изготовления форм и литья
COVID-19 ОБНОВЛЕНИЕ ЯНВАРЯ 2021 ГОДА.
Свобода
делать
то, что хочешь НОВИНКА!
Удивительная машина для изготовления форм
Amazing Mold Maker — это простой в использовании материал для изготовления силиконовых форм на основе платины, который снимается с формы за 30 минут и собирает сложные детали.Amazing Mold Maker идеально подходит для высокодетализированных, быстро затвердевающих форм.
Создавайте отливки из эпоксидной смолы, смолы, бетона, свечей, мыла, шоколада и многого другого!
СМОТРЕТЬ СТРАНИЦУ ПРОДУКТАУдивительное быстрое пальто
Amazing Quick Coat — это простая в использовании двухкомпонентная эпоксидная смола, которая при отверждении дает прочное глянцевое покрытие, соответствующее требованиям FDA при точном измерении, правильном смешивании и полном отверждении.
Эта формула быстрого отверждения становится менее липкой всего за 4 часа при 75 ° F.
СМОТРЕТЬ СТРАНИЦУ ПРОДУКТАУдивительная глубокая заливка
Готовы читать глубже и четче, чем когда-либо прежде? Представляем эпоксидную смолу Amazing Deep Pour — поверните ее, отлейте, используйте для покрытия.Возможности безграничны!
Amazing Deep Pour идеально подходит для речных столов, заготовок из смолы для токарной обработки на токарных станках, заполнения широких зазоров в древесине или любого другого применения, требующего глубины более 3/8 дюйма. ADP также можно наслоить для проектов, требующих толщины более 2 дюймов.
ПОСМОТРЕТЬ СТРАНИЦУ ПРОДУКТА УЗНАТЬ БОЛЬШЕПосмотрите, что возможно
Наша миссия — предоставить вам инструменты, необходимые для открытия неограниченных возможностей, существующих в мире изготовления форм и литья.Мы готовы помочь, предлагая продукцию и услуги высочайшего качества в отрасли.
Смотреть сейчас
ПРОДОЛЖАЙТЕ УЧИТЬСЯ, ПРОДОЛЖАЙТЕ ДЕЛАТЬ
Если вы хотите начать работу или вывести свои проекты на новый уровень, мы вам поможем. Посетите наши учебные курсы, чтобы познакомиться с основами, повысить свои навыки или попробовать что-то новое.
Начало работы
Изучите продукты, которые делают возможным
КУПИТЬ СЕЙЧАС
Учебное пособие по изготовлению форм: силиконовая форма для скульптуры из глины
Джон Кэннон из The Whimsical Гарденс привез его глиняную скульптуру к нам, чтобы слепить ее, а затем воспроизвести его в пластике на ротационной литейной машине.Подробная скульптура изображена ниже из разных углы.
В этой статье подробно описаны шаги, которые мы предприняли на протяжении всего процесса изготовления и литья формы:
Шаг 1: Выбор метода изготовления формы и формы
Резина
Шаг 2: Построение коробки для пресс-формы и подготовка
Скульптура
Шаг 3: Силиконовая форма для измерения, смешивания и заливки
Резина
Шаг 4: Demold
Step 5: Вырезание формы
Step
6: Ротационное литье
Шаг 1: Выберите метод изготовления пресс-формы и пресс-форму для резины
Метод изготовления пресс-формы
Для этой скульптуры мы выбрали метод «заливной блочной формы».
Вот причины, по которым мы отказываемся от других методов:
Формы для нанесения кистью: Мы обеспокоены тем, что пузырьки воздуха могут образовываться в сложных деталях на основе скульптура. Кроме того, формы, наносимые кистью, имеют, как правило, толстые и тонкие пятна — тонкие пятна в конечном итоге становятся слабыми местами плесень.
Форма для заливного одеяла: Одним из этапов процесса формования наливного одеяла является формирование слоя глины сверху. оригинальной модели ( см. учебник по форме для литого одеяла ).Этот шаг, скорее всего, деформирует глина оригинал.
Исходя из формы скульптуры, мы также знаем, что для формы потребуется вырез, чтобы удалить оригинальная скульптура и последующие отливки.
Формовочная резина
Для этого конкретного проекта мы также знаем, что хотим использовать силиконовую формовочную резину, потому что она не требует разделительный агент при заливке полиуретановой смолы. Разделительный агент может быть трудно применить в сложных областях и его может быть трудно удалить с отливки.Остаточный разделительный агент может предотвратить прилипание краски к отливки.
Отверждение платиной по сравнению с силиконовым каучуком, отвержденным оловом
Силикон Polytek делится на две основные категории: отвержденный платиной и отвержденный оловом. Основные сравнения между двумя варианты представлены в таблице ниже:
Тип резины | Преимущества | Недостатки | Литейные материалы | Методы |
Отвержденные платиной силиконовые резины для форм | Отсутствие усадки при отверждении, отвержденная резина имеет длительный срок хранения | Жидкая резина может страдать от ингибирования отверждения некоторыми материалами (например,г., сера глина, силиконы олова, Bondo, некоторые пластмассы, напечатанные на 3D-принтере, латексный каучук). | Большинство материалов, особенно смолы, пены и некоторые легкоплавкие металлы. | Налить, Кисть, Распылить. |
Силиконовые резины для форм, отвержденные оловом | Без ингибирования отверждения, немного дешевле, чем системы с платиновым отверждением | Усадка при отверждении (~ 1%), более короткий срок службы библиотеки (2-5 лет.), чем системы с платиновым отверждением. | Большинство материалов, особенно смолы, пены и некоторые легкоплавкие металлы. Может ингибировать полиуретан каучук, отвержденный платиной силикон и отливки из полиоптической смолы серии 14. | Налить, Кисть, Распылить. |
Силиконовые каучуки, отверждаемые платиной, имеют преимущества по сравнению с силиконовыми каучуками, отверждаемыми оловом (например, отсутствие усадки при отверждении, более длительный срок службы библиотеки), но может страдать от ингибирования отверждения при воздействии определенных материалов.Сера, для например, является известным ингибитором и присутствует в некоторых модельных глинах.
Мы не уверены, что скульптура Джона содержит серу, поэтому проводим небольшое тестовое лечение.
Для проведения теста мы смешиваем и заливаем быстротвердеющий платиновый силиконовый каучук (PlatSil ® 71-10) в глину. область сдерживания против небольшой секции на задней стороне скульптуры.
Через 30 минут мы удаляем силиконовый каучук, чтобы определить, правильно ли он затвердел.Мы находим, что резина, которая коснулась скульптуры, оставалась липкой, в то время как стороны резины подвергались воздействию воздуха и глина застыла должным образом. Это указывает на наличие загрязнений внутри или на глине, которые могут помешать любая силиконовая резина, отвержденная платиной, от должного отверждения.
На основании этих результатов мы выбрали силиконовую резину, отвержденную оловом, в качестве материала формы: TinSil ® 80-15 Силикон. Резинка. Выбираем мягкий силикон (Shore A15) из-за глубоких поднутрений на скульптура.Более твердую резину сложнее удалить без повреждений.
TinSil 80-15 Силикон Резина: Технические условия Твердость: по Шору A15 Mix Соотношение: 1A: 10B Время заливки: 30 минут Смешанная вязкость: 12000 сП Время извлечения: 24 часа Отвержденный цвет: Персиковый Удельный объем: 25.3 дюйма³ / фунт
Шаг 2: Постройте коробку для формы и подготовьте скульптуру
Для начала конструируется фанерная коробка необходимых размеров (т.е., по крайней мере, на 1 дюйм за скульптурой в во всех направлениях), а затем залил вазелином.
ПРИМЕЧАНИЕ: Хорошая идея — сузить внутреннюю часть формы для формования, чтобы форму можно было легче снимается, когда формовочная коробка перевернута вверх дном.
Pol-Ease ® 2500 Разделительный агент затем наносится на глиняную скульптуру.
ПРИМЕЧАНИЕ: Используйте Pol-Ease ® 2300 при изготовлении полиуретановой резиновой формы.
Формовочная коробка помещается вокруг подготовленной скульптуры, чтобы убедиться, что ее размеры подходят.
Мы оцениваем количество резины, необходимое для пресс-формы, следующим образом:
Объем пресс-формы = ~ 1716 дюймов 3
Объем скульптуры = ~ 84,78 дюймов 3
Объем пресс-формы — Объем скульптуры: 1,716 дюймов 3 — 84.78 из 3 = 1631,22 дюйм 3
1631,22 дюйм 3 ÷ 23,7 дюйма 3 / фунт (удельный объем TinSil 80-15) = 68,8 фунта силиконового каучука TinSil 80-15
68,8 фунта — это большое количество резины, и мы понимаем, что есть возможность уменьшить
эту сумму за счет добавления угловых вставок и других заглушек.
Мы добавляем несколько блокировок, но по-прежнему сохраняем расстояние не менее 1 дюйма между скульптурой и формой.
боксы / перегородки.
После закрепления всех блокировок пресс-форма снимается для герметизации новой фанеры.
дополнения вазелином и заделать все края утепленным пластилином
глина. Уплотнение краев помогает предотвратить утечку при заливке жидкого силикона в форму.
коробка позже.
Скульптура помещается обратно в пресс-форму, а затем пресс-форма фиксируется с помощью
винты.
Шаг 3: Измерение, смешивание и заливка силиконовой резины для пресс-формы
На основании новых размеров пресс-формы мы определили, что примерно 40 фунтов силикона TinSil 80-15 Резина нужна для изготовления формы.
Как упоминалось ранее, TinSil 80-15 имеет соотношение смеси 1A: 10B. Компоненты измеряются по весу, а затем тщательно перемешать.
ПРИМЕЧАНИЕ: Не пытайтесь измерять продукты с соотношением компонентов смеси 1A: 10B по объему — всегда измеряйте масса.
Из-за количества резины, необходимого для этого проекта, мы смешиваем две отдельные партии, используя турбонагнетатель.
Смеситель.
Каучук перемешивают до получения однородного цвета.
ПРИМЕЧАНИЕ: Избегайте ударов турбомиксером по стенкам емкости для смешивания, так как это может привести к попаданию воздуха в смесь.
Затем партии смешивают вручную с помощью Poly Paddle.
ПРИМЕЧАНИЕ: Это
важно несколько раз очистить стенки и дно емкости для смешивания, так как именно здесь
материал имеет свойство цепляться.
Силикон заливается в самую нижнюю точку формовочной коробки и дает ему подняться.
Резину заливают до тех пор, пока она не достигнет высоты не менее 1,0 дюйма над самой высокой точкой скульптуры.
Мы даем резине затвердеть при комнатной температуре в течение ~ 24 часов. Тепловые лампы могут помочь ускорить
излечивать.
ПРИМЕЧАНИЕ. Время снятия зависит от продукта. Ознакомьтесь с техническими бюллетенями по продуктам для
эта информация.
Шаг 4: Извлечение формы
Перед извлечением из формы места стенок формовочной коробки и заглушек помечаются ручкой.Это сделано для того, чтобы Формовочную коробку можно правильно собрать для последующего литья.
Все края формы отделяются от плинтуса шпателем перед всем
плесень удаляется.
При снятии формы с плинтуса скульптура раскалывается пополам, оставляя верх
половина в форме.
Шаг 5: Вырежьте форму
Чтобы удалить остатки скульптуры и последующие отливки, мы готовимся сделать разрез на одной стороне формы.Фотографии скульптуры распечатываются, чтобы определить подходящее место для вырезания.
ПРИМЕЧАНИЕ: Если возможно, лучше разрезать по линии, которая уже существует на скульптуре или в незаметное расположение (т.е. избегайте лица).
Для разреза используется скальпель.
ПРИМЕЧАНИЕ: Важно
для создания нерегулярного рисунка разреза (например, гребня и паза или зигзагообразной резки), чтобы две стороны совпадали
колодец для литья ( для получения общей информации по резке резиновых форм, посетите эту статью ).
Остаток скульптуры вынимается из формы, а вся глина остается в форме.
очищается.
Шаг 6: Ротационное литье
Форму помещают обратно в пресс-форму и затем фиксируют.
Поскольку мы планируем использовать машину для ротационного литья, мы создаем крышку литейной формы с отверстием для заливки.
В это отверстие заливается быстро схватывающаяся смола, когда формовочная коробка находится на ротационной литейной машине.
Деревянные бруски добавлены по бокам ящика, чтобы установить и прикрепить его к вращающемуся
литейная машина.
Силиконовая заглушка позже будет использоваться для закрытия отверстия при заливке.
Опалубку загружают на ротационную литейную машину и фиксируют с помощью C-образных зажимов.
EasyFlo 120 Liquid Plastic — это продукт, который мы
Чаще всего рекомендуют для ротационного литья или литья под давлением.Он предназначен для постепенного затвердевания над его
рабочее время, в отличие от «схватывания» (как характеристики отверждения EasyFlo 60, другого продукта с
Серии EasyFlo). Это постепенное загущение в течение последних 30-45 секунд рабочего времени помогает обеспечить
ровное пальто.
EasyFlo 120 Жидкость Пластик: Технические характеристики
Твердость: Shore D65
Mix Соотношение: 1A: 1B по объем, 100A: 90B по весу
Время заливки: 2-2.5 минут
Смешанный Вязкость: 120 сП
Время извлечения: 15-30 минут
Отвержденный Цвет: Белый
Удельный объем: 26,9 дюйм³ / фунт
Примерно 2 фунта EasyFlo 120 тщательно перемешивают и заливают в форму.
ПРИМЕЧАНИЕ: В идеале эту смолу следует перемешать и залить менее чем за минуту.
Заливное отверстие закрывается силиконовой пробкой, после чего машину включают.
Примерно через 30 минут форму снимают с ротационной разливочной машины, а затем отливку.
снимается с формы.
Для следующего цикла мы смешиваем EasyFlo 120 + Коричневый краситель PolyColor + Бронзовый порошок для получения холодного литья.
бронзовая копия.
Вот несколько фотографий детали из бронзы, отлитой методом холодного литья, до полировки стальной ватой (стальная вата
используется для обнажения бронзового порошка на поверхности отливки).Изначально отливки будут казаться шоколадными.
коричневый; вы заметите небольшое пятно на его щеке, которое было начищено до блеска.
Процедура формования силикона
Процедура изготовления силикона39-245
Быстрый дизайн за счет виртуального и физического Прототипирование
Карнеги-Меллон Университет
Весна 1997 г.
Процедура изготовления силиконовых форм
Материалы
Силиконовая лепка проста и аккуратна и многим простит ошибки.Идея состоит в том, чтобы начать с мастер-части. Эта часть может быть инкапсулирован формовочным материалом, и тогда можно сделать множество деталей из получившегося негатива. Этот мастер может быть инкапсулирован поддерживая его на распорках и заключая в удерживающую раму.Перед тем, как приступить к изготовлению формы из силиконовой резины, необходимо: сначала соберите все необходимые инструменты, материалы и защитное снаряжение. Важно, чтобы все было готово и под рукой, так как рабочий срок службы полимеров, т.е.время, которое они могут течь, не очень велико.
Необходимые инструменты для процесса — нож, скальпель, пара кусачки, напильник, отвертка и шпатель для перемешивания.
Чтобы установить нашего мастера на место, вам понадобится опорная плита, регулируемая. формовочная стенка, тонкая проволока, сам мастер и распорки.
Дополнительное оборудование включает в себя контактную бумагу, бумажные полотенца, 2 смешивания. мензурки, туба с воронкой, малярный скотч, гипс и суперклей.
Силиконовый каучук состоит из двух компонентов, которые смешиваются соотношение объемов 1: 1. Пропаноловый спирт используется для очистки полимеры до отверждения. Материал литья, используемый для изготовления частей также смешивается в соотношении 1: 1 по объему. Наконец, вам понадобится разделительный агент.
Поскольку полимеры токсичны, вы должны носить респираторную маску во время обработка полимеров. Необходим лабораторный халат, латексные перчатки и защитные очки. для предотвращения любого контакта тела с полимерами, вызывающими раздражение.
Этапы процедуры
Перед запуском формы из силиконовой резины поверхность мастера которые вы хотите воспроизвести, должны быть тщательно изучены на предмет несовершенства. Это критический шаг, потому что силиконовая резина пресс-форма и ее полиуретановые детали будут точно повторять поверхность оригинальный мастер. Для обеспечения качественной поверхности на полиуретановая литая деталь, можно использовать гладкую поверхность с зернистостью # 400 наждачная бумага. В приведенном ниже примере мастер был очень гладким и не требовалась полировка.
Поднимите мастера с земли, прикрепив к нему опору. В цель поднятия мастера над землей — позволить силикона, чтобы сформировать стенку пресс-формы толщиной не менее 1/2 дюйма на Нижний. Если стена тоньше 1/2 дюйма в любом месте, форма может быть достаточно слабым, чтобы порваться во время извлечения из формы. Мы повысили нашу мастера, приклеив саморез суперклеем как указано. Поскольку полимер из которых будут отливаться новые детали, будут входить в силиконовую форму снизу воздух из формы должен иметь выход.Это может быть достигается путем суперклейки тонкой проволоки на самых верхних краях мастер, то есть края, где будет задерживаться воздух. Мы режем относительно тонкую проволоку с помощью кусачков и отшлифовать один край до плоской увеличить площадь соединения проводов.
Перед закреплением мастера на пластине (дне формы) пластина обработана таким образом, чтобы материал формы не прилипал к ней. Мы использовали контактная бумага, чтобы избежать использования восковых паст. Мы закрепили мастера к пластине с помощью суперклея приклеиваем винт к нижней пластине поверхность.В некоторых случаях пластилин можно использовать для закрепления мастер к пластине вместо этого. Если мастер не прикреплен к пластина, расслоение может произойти при заливке силиконовой резины в и вокруг мастера.
Затем нанесите слой смазки для воска на все основные поверхности. Этот облегчит отделение мастера от готового силикона резиновая форма.
Поместите регулируемую стенку пресс-формы вокруг мастера, помня, что он не должен быть ближе 1/2 дюйма, чтобы стенка силиконовой формы будет достаточно толстым.Используйте пластилин, чтобы заполнить пустоты, где силиконовая резина может протечь. Будьте осторожны во время этого шаг. Если силикон протекает, это очень сложно остановить, так как нет Материал, смоченный силиконом, может прилипнуть и остановить утечку.
Теперь вы готовы смешать материалы из силиконовой резины и залить их. в форму.
Рассчитайте приблизительно объем силиконового каучука. требуется для заполнения формы. Подготовьте еще около 20% для учета проигрывает.Поскольку силиконовый материал смешивается в соотношении 1: 1 на объем, один половина необходимого материала должна поступать из каждого компонента. Использовать одноразовые емкости со шкалой объема для замешивания материала.
Убедитесь, что материал тщательно перемешан, помня о том, что перемешивание следует делать осторожно, чтобы в материал не попал воздух. Сведение к минимуму пузырей важно, потому что мы пропустим дегазацию. процесс, требующий коммерческого оборудования. Если ты видишь воздух пузыри на поверхности, вытолкните их концом отвертки открыто.Имейте в виду, что срок службы силиконовой резины материал составляет 15-20 минут, что означает, что когда компоненты находятся в прикоснуться друг к другу, у вас есть не более 20 минут, чтобы смешать и вылить их.
Налейте силикон медленно, чтобы вокруг не оставалось воздушных карманов. мастер стены. Форму можно наклонить под небольшим углом. если присутствует большая горизонтальная поверхность. Наклон уменьшит вероятность попадания воздушных карманов под большие горизонтальные поверхности.
Как только форма будет заполнена, дайте ей застыть в течение 24 часов. прежде чем разбирать его.
Чтобы силиконовые банки оставались должным образом закрытыми в будущем. используйте, распылите разделительное средство вокруг покрытия преполимера силиконовый компонент. Если разделительный агент не используется, эти компоненты имеет тенденцию к образованию корки, которая снижает герметичность крышки из-за время.
По истечении времени отверждения извлеките конструкцию из формы.С тех пор, как мы сделали цельную форму (только одну заливку), вырезаем финальную кусок силиконовой резины на две половинки. (Резки можно избежать, если изготовление формы из двух частей.)
Используйте скальпель, чтобы разрезать форму. Несколько проходов скальпелем могут быть необходимо до того, как будет достигнут мастер. Не беспокойтесь о гладкость среза. Напротив, неравномерный разрез снижает вероятность неправильного позиционирования двух частей формы. Однако не преувеличивать. Горизонтальная линия разъема на вертикальной эталонной поверхности дает наилучшие результаты литья.Это работа двух человек, где один человек «раздвигает» форму так, что скальпель перемещается легче во время резки, в то время как другой человек режет.
Имейте в виду, что это самый опасный шаг в процесс изготовления силиконового литья.
По завершении резки осторожно разведите две части формы. Затем вытащите мастер из полуформ. Силиконовая резина гибкий и выдерживает большое растяжение. Однако осторожность должна быть приняты, чтобы не разрывать резиновый материал
Теперь, когда у вас есть форма, вы можете отливать детали.
Нанесите слой разделительной смазки на силиконовую форму, чтобы предотвратить литьевой полимер от прилипания к силиконовой резине.
Так как наилучшие результаты литья дает заливка полимера из снизу вверх мы использовали отверстие для опорного винта в качестве приемного устройства для полимера. полость.
Заливка осуществляется путем помещения трубки в силиконовую форму и воронку. на другом конце трубки. Чтобы предотвратить утечку, закройте трубку. отверстие для вставки с гипсом.Затем поместите форму на подставку так, чтобы что трубка может плавно изгибаться вверх. Закрепите две части формы так, чтобы что они не развалятся при заливке полимера. Мы использовали ленту сделать так.
Смешайте полимер в соотношении 1: 1 по объему, необходимый для репликация мастера с учетом объема мастера как потери, которые возникнут в стенках пробирки и контейнера. Снова, лучше всего использовать одноразовый стакан, так как процесс очистки может быть трудный.Трубку нельзя очистить. Если воронок мало или дорогие, их можно очистить пропаноловым спиртом перед полимер отверждает.
После смешивания литейного полимера держите воронку над верхнюю поверхность формы и медленно влейте полимер.