Технология производства арболита
ТЕХНОЛОГИЯ «РУССКИЙ АРБОЛИТ»
Компания «Русский Арболит» совместно с партнёрами является автором технологии массового производства строительных материалов из арболита. В её основе лежит тщательная подготовка древесного сырья и особый метод формовки изделий из арболитовой смеси. Вместе с конструкторскими бюро и производителями нестандартного оборудования мы проектируем и производим специализированные линии для производства арболита по нашей фирменной технологии.На этой странице мы вкратце расскажем про ключевые моменты технологии «Русский Арболит», полную инструкцию и обучение мы предоставляем только нашим производителям сети.
Хороший арболитовый блок – это правильное сырье, специализированное оборудование и неукоснительное соблюдение технологий. При отклонении от любого из требований мы получаем блок, который не обладает правильной геометрией или нужными тепловыми, звукоизоляционными и прочностными характеристиками.
Отбор и подготовка сырья для арболита
Как и в любом производстве, от правильно выбранного сырья и его обработки зависит качество конечного продукта. Арболит тут не исключение. Скорее наоборот, этот материал требует внимательного отношения к подбору сырья и щепетильному походу к каждому этапу его подготовки.
Сортировка древесины
Основой правильного арболита является древесина. Без примесей песка и различных добавок. Допускается наличие коры не более 5%. Для переработки используются исключительно хвойные породы дерева, в них меньше всего сахаров, которые являются «цементными ядами» и мешают отвердеванию цемента в смеси.На производство завозятся отходы пилорам: горбыль или срезки. Не рекомендуется использовать для сырья древесные поддоны, бывшие в употреблении. Также не допускается применять горелый лес и древесину с очагами поражения плесенью.
Дробление щепы
В начале 90-х годов мы начали работу над изучением оптимальной формы щепы. Опытным путем было определено, что для арболита с самоармирующей внутренней структурой оптимальна плоская игольчатая форма щепки. Если щепа будет слишком мелкой, пропадёт изгибная прочность блока.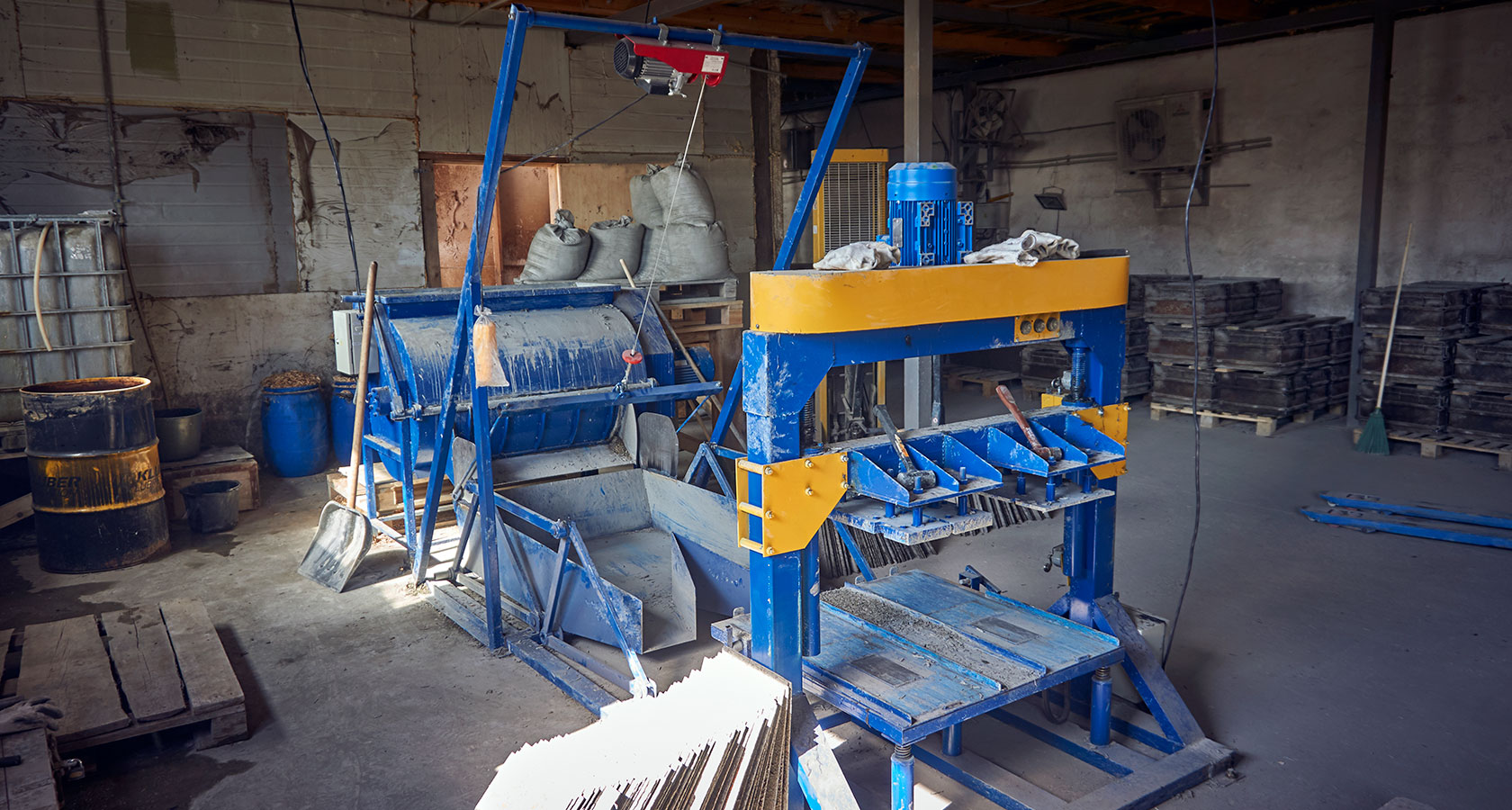
Поэтому совместно с сибирской компанией, специализирующейся на производстве дробильного оборудования, был разработан первый в России арболитовый измельчитель древесины. Определенная форма ножей у диско-молотковой системы в сочетании с калибровочным ситом дает оптимальную для арболитового блока щепу.
Сепарация щепы
При производстве легких бетонов с различными наполнителями есть прямая корреляция между размером частицы наполнителя и конечной марочной прочностью бетона. Чем меньше диаметр частиц, тем больше нужно нужно цемента, чтобы эффективно обволакивать их поверхность для связывания частиц друг с другом.Поэтому, при проектировании нашего щепореза мы учли это явление и добавили в конструкцию лопастной вентилятор, который отделяет в воздушном потоке мелкую стружку и опил. Для дополнительной сепарации рекомендуется применять сепаратор-сеялку, это позволяет снизить потребление цемента до 20%. Это обосновано экономическим эффектом при производстве арболитовых блоков.
Увлажнение древесины
Роль уровня влажности щепы при производстве имеет большое значение. При недостатке воды для затворения цемента значительно снижается марочная прочность готового изделия. Поэтому на предприятиях «Русского Арболита» работает технолог, который определяет влажность каждой партии древесины и делает специальные пропорциональные расчёты при подготовке арболитовой смеси.
Минерализация щепы для арболита
Древесина – это органика и арболит является бетоном на органических заполнителях. Как известно, арболит – весьма капризный строительный материал, который требует к себе внимания. Виной тому его сложный химический состав и структура древесины.При производстве арболита в щелочной среде цементного теста проявляется химическая агрессивность заполнителя растительного происхождения по отношению к цементу. Еще в советское время проводились исследования ученых, направленных на нейтрализацию их вредного влияния. В работах Исаака Наназашвили подробно описано какое вредное воздействие на арболит оказывают легкорастворимые простейшие сахара: сахароза, глюкоза, фруктоза. Количество и активность «цементных ядов» напрямую зависит от породы древесины, времени года и сроков ее хранения.
Технология компании «Русский Арболит» в сотрудничестве с Ивановским государственно химико-технологическим университетом определили наиболее безопасный и экономически обоснованный нейтрализатор «цементных ядов» и оптимальное его количество. Все производители арболита федеральной сети «Русский Арболит» получают чёткие рекомендации и точный пропорциональный состав минерализатора.
Процесс производства арболитовых блоков
Для изготовления изделий из арболита требуется отформовать смесь щепы и цемента – придать ей форму конечного продукта. Технология формовки «Русского Арболита» направлена на получение изделий повышенной точности и серийного качества. Для этого мы запечатываем арболитовую смесь на 8–12 часов в стальных формах. Более 10 лет назад в тесном сотрудничестве с компанией «ОКБ Сфера» мы разработали и внедрили на рынке первый вибропресс для арболита. Сегодня же мы производим мощный производственный арболитовый комплекс, на котором уже работают десятки наших партнеров по всей России.
Выбор форм для блоков
Для получения арболитовых блоков или панелей с ровным гранями требуется использование прочных стальных форм с надежными элементами фиксации. Мы самостоятельно производим такие формы на станках лазерной резки. Это гарантирует точный раскрой метала.Так как наша технология подразумевает прессование под воздействием вибрации, для изготовления форм применяется металл увеличенной толщины. Поэтому, для производства арболита по нашей технологии, различные формы от пенобетонных блоков не подходят.
Распалубка и подготовка форм
Качество поверхности изделий из арболита зависит от предварительной подготовки форм. Перед использованием требуется их очистка после распалубки и обработка эмульсолом марки ЭКС-2 или ЭКС-А. Можно применять другой аналогичный составом для смазки опалубки. Главное, чтобы состав соответствовал нормативам ГОСТ 6243-75 и ГОСТ 2517-2012.
Раз в месяц требуется обслуживание форм, осмотр сварных швов и элементов замка. Тотальная очистка от цементного камня на внутренних плоскостях и в углах форм.
Дозирование сырья
Прочность арболита и его теплотехнические свойства напрямую зависят от точности дозировки готового сырья. Для древесной щепы применяется мерная емкость, рассчитанная по литражу на один замес в бетоносмесителе. Для цемента мы рекомендуем нашим партнерам применять систему точной электронной дозации, основанной на использовании тензометрических датчиков.Минерализатор разводится в определенной пропорции с водой, которая применяется для затворения цемента. Подача раствора на линии «Русский Арболит 2» осуществляется автоматически, с помощью насосной станции и системы форсунок, смонтированных на корпусе бетоносмесителя.
Подготовка арболитовой смеси в бетоносмесителе
Для достижения гомогенности арболитовой смеси применяются плугообразные лопасти на активаторах бетоносмесителя.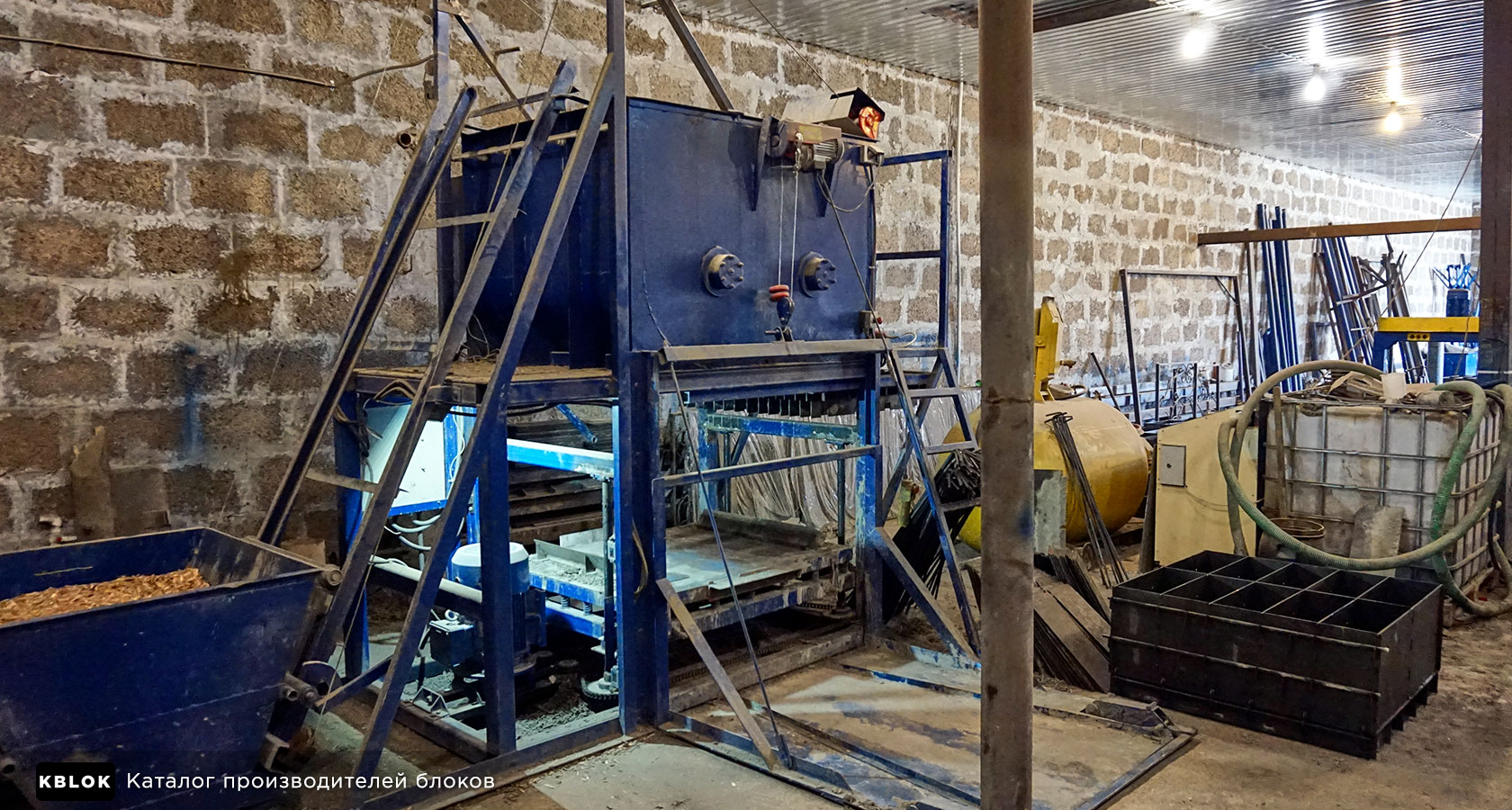
При подготовке смеси нужно следить за влажностью щепы. Только опытный технолог в состоянии определить, требует ли смесь долива воды и точно настроить дозатор, в зависимости от первичной влажности партии сырья.
Время замеса тоже имеет значение, поэтому компания «Русский Арболит» проводит обучение и консультирует своих будущих партеров, помогая наладить выпуск качественной продукции.
Формовка смеси и получение арболитовых блоков
По достижении готовности арболитовой смеси, на вибропресс для арболита монтируются пустые стальные формы. Далее их наполняют с чередованием вибрации и подачи смеси. Это очень важно, потому что позволяет получать изделия из арболита с одинаковой по всему объему плотностью.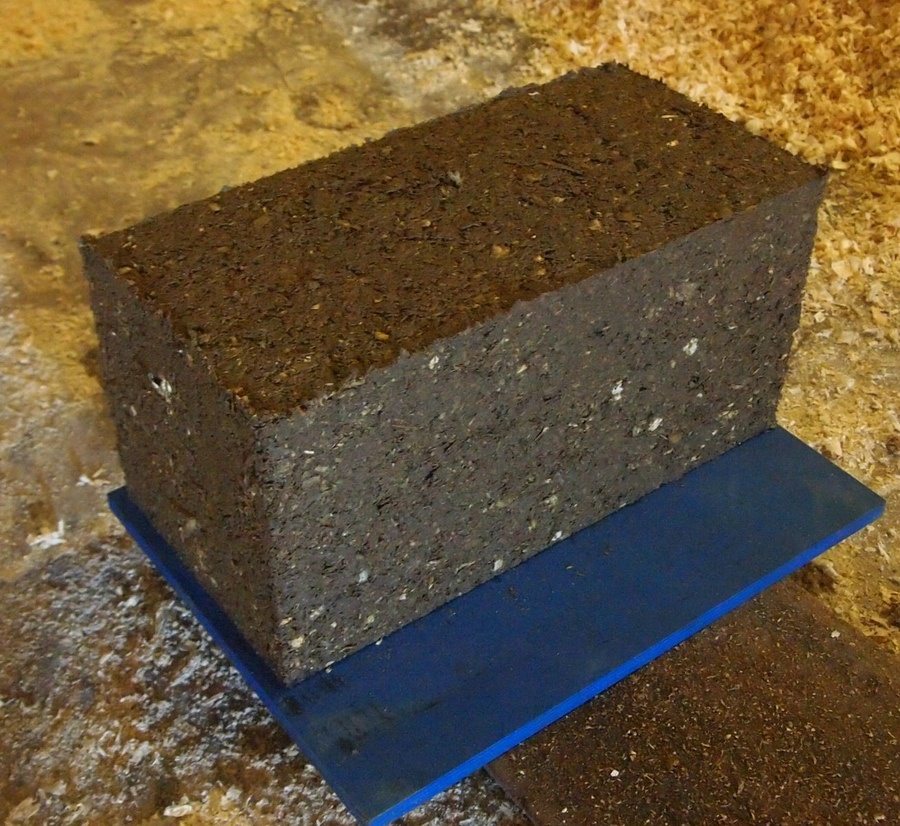
Время вибрации зависит от объема производимого изделия и его назначения: конструкционного или теплоизоляционного.
После заполнения форм их укрывают контактными пластинами, которые зажимаются прессом. Далее пластины надежно фиксируются в формах, тем самым арболитовая смесь полностью запечатывается со всех сторон, обеспечивая минимальное отклонение ребер от прямолинейности и граней от плоскостности.
Далее форму с арболитом снимают с вибростола и вывозят на сушильный склад.
Штабелирование форм и сушка блоков
После формовки арболит должен набрать начальную передаточную прочность. Для этого формы вывозятся в теплое помещение сушильной камеры. Время выдержки составляет от 8 до 12 часов, в зависимости от температуры внутри помещения.
Для экономии площади сушильной камеры в конструкции форм нами предусмотрено их складирование друг на друга через деревянные бруски сечением не менее 3 на 3 см.
После набора прочности происходит распалубка форм и извлечение изделий из арболита с последующим их укладыванием на деревянные паллеты. Упаковка блоков аналогична упаковке других строительных блоков из ячеистых и легких бетонов.
Планируете начать производство арболита? Обращайтесь к нам!
Начать производство |
Мини-завод по производству арболитовых блоков
Представленный ниже материал будет интересен энергичным людям, которые хотят организовать весьма прибыльный производственный бизнес или разнообразить уже имеющийся.Мало для кого является секретом, что одним из наиболее стабильных и востребованных производств на рынке является производство строительных материалов. Объемы строительства в нашей стране увеличиваются с каждым годом, и все большее количество людей предпочитают жилью в многоквартирных домах индивидуальное строение на собственном земельном участке.
Наряду с большим выбором строительных материалов, представленных на рынке, существует один, который является не только конкурентноспособным, но и единственным, объединяющим положительные свойства каждого из них, сохраняя при этом полную экологичность и долговечность. Называется этот материал АРБОЛИТ.
В СССР арболит был разработан в 60-х годах ХХ века и прошел все технические испытания, был сертифицирован и стандартизирован. Именно из этого материала была построена станция в Антарктиде.
Арболит представляет собой композиционный материал, сформованный в виде блока или панели, состоящий из наполнителя, каждая частица которого обернута цементной оболочкой. В качестве наполнителя используются различные природные материалы: древесина, отходы льнопроизводства, отходы маслосемян и т.п. Однако наиболее перспективным наполнителем является древесина в виде щепы определенного размера и фракции. При этом нет необходимости использовать деловой круглый лес, так как подойдут любые отходы лесозаготовок, отходы деревообрабатывающих производств и т.п.
По своим прочностным характеристикам данным материал является конструкционным, а по теплопроводным характеристикам – теплоизоляционным. Учитывая тот факт, что арболит изготавливается из полностью природных материалов, это ставит его вне конкуренции.
Цена на арболит, на первый взгляд, может показаться высокой по сравнению с некоторыми другими материалами, однако стоимость готового дома оказывается минимум на 30 % ниже, чем при строительстве из любого другого материала при полном соответствии строительным нормам (СниПам). Экономия получается за счёт толщины стен, отсутствия дополнительных утеплителей, облегченного фундамента, дешевизны отделки (как наружной, так и внутренней). Известны случаи, когда строительные компании, построив несколько домов из арболита, полностью отказываются строить из других материалов.
Целью данной статьи является обоснование производственных подходов по изготовлению арболитовых блоков.
Одним из основных тормозов развития данной темы до недавнего времени было отсутствие качественной технологии производства и разработанного под эту технологию оборудования. Однако в настоящее время эта проблема решена предприятием «Опытно-Конструкторское Бюро «СФЕРА». Основной вид деятельности фирмы – разработка и изготовление нестандартного оборудования. У конструкторов данного предприятия имеется многолетний опыт в проведении научно-исследовательских и экспериментальных работ, в том числе с оборонной и деревообрабатывающей промышленностью.
Последние три года предприятие вплотную занимается технологией и оборудованием по изготовлению арболита. Проведенный патентный поиск за последние 50 лет по нескольким странам мира позволил определить состояние вопроса и сделать выводы о возможности применения полученных знаний в современных условиях. Кроме того, был проведен анализ арболитовых блоков современных производителей на предмет соответствия производимого материала ГОСТу, который еще никто не отменял. Данная работа проводилась совместно с предприятием ООО «ЭкоДревПродукт». Выводы оказались неутешительными: ни по прочности, ни по геометрии; исследуемый материал ГОСТу не соответствовал. Основной причиной являлась неправильная формовка блока с последующей моментальной распалубкой. На основании полученных данных стало очевидно, что основным оборудованием, отвечающим за качество производимого материала, являются вибропресс и формы. Данное оборудование было спроектировано и изготовлено на предприятии ООО «ОКБ «СФЕРА». На сегодняшний день оборудование прошло эксплуатационные испытания и стадию доводки. При этом используемая технология предполагает запечатывание арболитовой смеси в блоке с последующей выдержкой. Уплотнение смеси в форме обеспечивается вибрацией формы на столе вибропресса в процессе ее заполнения с последующим сжатием. Таким образом, плотность получаемого блока, его прочность и геометрия полностью обеспечиваются.
Однако только основного оборудования для производства арболитовых блоков недостаточно. Необходимо иметь измельчитель (шредер), который производит щепу определенного размера из отходов древесины, а также бетоносмеситель.
Компоновка технологической линии может сильно отличаться в зависимости от уровня механизации всего технологического процесса. Именно поэтому предприятием были разработаны две производственные линии для изготовления арболитовых блоков. Качество получаемого материала на обеих линиях одинаково и соответствует ГОСТу, однако стоимость оборудования отличается в десятки раз. При этом суммарная производительность отличается незначительно. К тому же использование большого количества вспомогательного оборудования (нории, транспортеры, пневмотранспорт, компрессоры, бункеры-накопители и т.д.) требуют квалифицированного обслуживания. Такая сложная линия была установлена и успешно эксплуатируется в г. Тейково Ивановской области.
Однако мы считаем, что наибольший коммерческий интерес имеют линии с минимальным набором вспомогательного оборудования, где механизированы только очень тяжелые (в физическом плане) операции. К тому же такие линии являются весьма мобильными и не требуют сложной инфраструктуры помещений. Эти производства можно поставить где угодно, лишь бы по близости был источник сырья. Все оборудование находится в одном ярусе, и достаточна высота от пола до потолка 2,5 м.
На схеме представлена технологическая линия мини-производства по изготовлению арболитовых блоков.
Вновь открытый старый материал: деревобетон
Дерево и бетон — два материала, которые едва ли могут быть более разными. Каждый из них имеет свои качества, преимущества и недостатки по сравнению с другим, и поэтому в основном это принципиальный вопрос, строить ли с одним или с другим. Но сейчас есть комбинации этих двух материалов, которые пользуются большой популярностью. А вот композит из двух — как деревянно-бетонный — встречается гораздо реже. До сих пор он в основном использовался для ненесущих компонентов, например, в дизайне интерьера или дизайне фасада. Ученые из Национальной исследовательской программы Resource Wood в Швейцарии усовершенствовали композитный материал для несущих стен и потолков.
© iTEC/HTA-FR
Композитные материалы из дерева и цемента не являются чем-то новым. В 1930-х годах голландец Ричард Хандл запатентовал «способ производства легкого строительного материала из древесных отходов и цемента». Во время Второй мировой войны в Германии в жилищном строительстве использовалось арболита . Чтобы восполнить нехватку цемента, связанную с войной, использовались заменители, такие как шлак из бурого угля, но с ограниченным успехом из-за плохой защиты от влаги. В ГДР, напротив, хорошая тепло- и звукоизоляция достигалась за счет ненесущих плит, изготовленных из более качественной арболитовой смеси.
Современный арболитовый бетон
Интерес к арболитовому бетону возродился благодаря общему повышению осведомленности об устойчивости в последние годы. С начала тысячелетия Мюнхенский технический университет занимается исследованиями деревянных легких бетонов . Основное внимание уделяется потенциалу противопожарной защиты и визуальному дизайну фасадов и интерьеров. В Университете Баухаус в Веймаре green:house , экспериментальное деревянно-бетонное здание, было построено в период с 2009 по 2010 год, в котором сочетались положительные структурные и физические свойства дерева (например, способность к диффузии) и свойства бетона (например, звукоизоляция), и в то же время его можно было предварительно изготовить и обработать в каркасной конструкции, как дерево. Композитный материал состоял исключительно из древесной стружки и цемента.
Инновация: экологичный деревянно-бетонный дом
Уже построен первый цельный деревянно-бетонный дом с использованием облегченных методов строительства. Но теперь ученые разработали несущий древесно-бетонный материал в рамках Национальной исследовательской программы (NRP 66) «Ресурсная древесина» в Швейцарии, который даже может заменить обычный бетон в бетонном строительстве. Прекрасная полированная древесина заменяет обычный гравий и песок. Исследователи экспериментировали с различными составами разного веса, каждый из которых весил не более половины веса обычного бетона. В самой легкой смеси объем древесины составляет более 50 процентов, а вес арболита настолько мал, что он даже плавает на воде.
Помимо малого веса, новый арболит характеризуется повышенной огнестойкостью и лучшей теплоизоляцией по сравнению с обычным бетоном. Кроме того, доля деревянного, безусловно, тоже положительно влияет на экологию. И последнее, но не менее важное: древесина с песком и гравием имеет большое преимущество в том, что она возобновляема. И, прежде всего, энергию можно получать из арболита после его сжигания на мусоросжигательном заводе.
Заключение
Этот очень интересный композитный древесно-бетонный материал, сочетающий в себе преимущества двух очень разных материалов экологически чистым способом, во многих случаях может заменить обычный бетон в долгосрочной перспективе. Но, вероятно, пройдет еще некоторое время, прежде чем вновь обнаруженный старый строительный материал действительно «принесет пользу» в строительной отрасли. На данный момент исследователи проекта NRP 66 все еще изучают вопрос, какая смесь для каких целей лучше всего подходит.
Изготовление бетона из дерева | Университет Северной Британской Колумбии
На этой фотографии показана деталь изделия из бетона и дерева. Загрузите изображение с высоким разрешением.
«Мы видим все виды дополнительных применений, от столешниц до напольных покрытий».
Британская Колумбия столкнулась с большим вопросом: что делать с миллиардами деревьев, уничтоженными жуком горной сосны?Сорин Паска не знает полного ответа, но у него есть конкретное предложение.
Помимо пиломатериалов и фанеры, исследовательская группа, состоящая из Паски и профессоров Рона Тринга и Яна Хартли, обнаружила, что древесина горного соснового жука (MPB) на самом деле является отличным ингредиентом для производства бетона. Бетон производится путем смешивания цемента с водой и заполнителем. Обычно заполнитель состоит из камней или горных пород, но древесина MPB является новым вариантом.
«Обычно цемент отталкивает органические материалы, такие как дерево», — говорит Паска, который недавно получил степень магистра в UNBC, исследуя эту тему. «Но по какой-то причине цемент прилипает к сосне, и эта совместимость становится еще сильнее, когда дерево было убито — или, можно сказать, усилено — жуком горной сосны».
От древесины жука до готового продукта. Сорин Паска с разными образцами бетонной древесины. Загрузите изображение с высоким разрешением.
«Первоначальная идея заключалась в том, чтобы посмотреть, сможет ли древесно-цементный продукт заменить гипсокартон или гипсокартон», — говорит Паска. «Я думаю, что это отличная альтернатива, но теперь, когда исследование завершено, мы видим все виды дополнительных применений, от столешниц до напольных покрытий. Это прекрасный продукт, который сочетает в себе все структурные преимущества бетона с эстетическими качествами дерева».
Исследование имеет огромное значение для лесной промышленности Британской Колумбии, которая ищет альтернативные продукты из древесины, дополняющие производство пиломатериалов, фанеры, древесных гранул и ориентированно-стружечных плит. Исследования UNBC, а также опыт операторов лесопилки показали, что древесина MPB сильно растрескивается вскоре после гибели. В результате многие части дерева перестают быть полезными для мельниц, производящих обычную продукцию.
«Вопрос о том, как мы можем максимизировать каждое дерево, жизненно важен для лесной промышленности и многих сообществ провинции, выживание которых зависит от лесного хозяйства», — говорит Ян Хартли, заместитель декана программ для выпускников UNBC, который участвовал в исследовании и является экспертом в области качества древесины. «Это исследование дало новый продукт, который заслуживает дальнейшего изучения».