12 методов изготовления изделий из пластика и примеры их использования [Часть 1]
Производство пластмасс необходимо для большинства отраслей промышленности. От полистироловой упаковки для пищевых продуктов до промышленных компонентов, изготовленных из полиэфирэфиркетона инженерного класса, производство пластмасс вносит огромный вклад в жизнь, какой мы ее знаем. Без возможности изготовления пластмассовых изделий нам пришлось бы разрабатывать принципиально новые системы производства.
Однако производство пластмасс включает в себя множество различных методов. Литье под давлением, экструзия пластика и 3D-печать FDM — все это методы изготовления пластмасс, и кроме них существует множество других. Эти различные методы изготовления подходят для разных пластиковых деталей, и выбор между ними не всегда прост. Бюджет, дизайн детали и материал — вот лишь некоторые из факторов, которые влияют на выбор метода изготовления пластмасс.
В этой первой части данной статьи мы рассмотрим 6 различных методов изготовления пластмасс, раскроем их основные процессы и то, почему они эффективны.
1. Литье под давлением
Литье под давлением является наиболее распространенным процессом изготовления пластмасс. Данный метода подходит для обработки термопластичных и термореактивных полимеров.
Этот метод быстрого изготовления пластмасс заключается в нагревании пластиковых гранул до расплавления, затем расплавленный пластик заливается в металлическую форму с помощью возвратно-поступательного шнека. Расплавленный материал остывает, затвердевает и принимает форму полости формы. Затем твердая деталь извлекается из формы.
Литье под давлением подходит для огромного разнообразия материалов и деталей. Детали должны иметь тонкие и ровные стенки, но в остальном могут иметь различные формы и размеры.
Примеры литья под давлением: одноразовые подносы для еды, приборные панели автомобилей, детали LEGO.
2. Выдувное формование
Выдувное формование — это процесс литья пластмасс, который используется реже, чем литье под давлением. Он имеет три разновидности: экструзионно-выдувное формование, выдувное формование под давлением и выдувное формование с растяжением.
Этот процесс изготовления пластмасс работает с использованием пресс-формы и расплавленной термопластичной трубки, называемой заготовкой (вместо полностью расплавленных гранул). Сжатый воздух поступает в заготовку, заставляя пластик расширяться и соприкасаться с внутренними стенками формы, в конечном итоге принимая вид полости формы.
Выдувное формование подходит для полых пластиковых деталей, таких как пластиковые бутылки для воды, с наиболее распространенным материалом HDPE.
Примеры выдувных деталей: бутылки, бочки, топливные баки.
3. Ротационное формование (центробежное формование )
Ротационное формование — это еще один процесс литья пластмасс, в котором для формирования пластмассовых деталей используются высокие температуры и низкое давление. Он осуществляется путем вращения формы для перемещения пластикового материала внутри нее.
В процессе ротационного формования порошкообразный пластик помещается в форму, которая нагревается и вращается вокруг двух (или более) осей. Благодаря этому вращению расплавленный пластик покрывает всю внутреннюю поверхность формы и принимает форму полости.
Преимущества ротационного формования включают более простую оснастку, постоянную толщину стенок и прочные внешние углы. Однако процесс может быть медленным, поскольку перед извлечением детали вся форма должна остыть.
Примеры ротационного формования: контейнеры, емкости для хранения, игрушки.
4. Вакуумное литье
Вакуумное литье — это процесс изготовления пластмассы, обычно применяемый для изготовления небольших партий разноцветных прототипов. Для изготовления уретановых пластиковых деталей используются силиконовые формы.
Во время этого процесса оператор заливает уретановую смолу в силиконовую форму; затем с помощью вакуума удаляются воздушные карманы и пузырьки, в результате чего получается исключительно гладкая готовая деталь. Затем уретановые детали полимеризуются в печи.
Вакуумное литье — популярный процесс изготовления пластика для частично прозрачных деталей, таких как опытный экземпляр.
Примеры деталей: корпуса и крышки для электроники, различные прототипы и опытные образцы.
5. Обработка пластмасс
Обработка пластмасс — это очень популярный процесс изготовления изделий из пластика. Он включает в себя фрезерование с ЧПУ, токарную обработку с ЧПУ и другие смежные процессы.
Хотя разные станки работают по-разному, обработка пластмасс обычно подразумевает вырезание участков из пластмассовой заготовки с помощью ручных или управляемых компьютером режущих инструментов.
Обработка пластика также полезна для совмещения деталей, изготовленными с использованием других методов, таких как экструзия.
Примеры обработанных деталей: различные промышленные детали, оснастка и приспособления, автомобильное освещение.
6. Моделирование методом послойного наплавления
Моделирование методом послойного наплавления (FDM) — это наиболее распространенный процесс 3D-печати для изготовления изделий из пластика. Он работает с обычными термопластами, такими как ABS и PLA, а также с такими современными материалами, как PEEK.
FDM работает путем нагрева экструдированной термопластичной нити, а затем выкладывания ее в точные формы из движущегося сопла (прикрепленного к печатающей головке) в соответствии с компьютерными инструкциями. 2D-фрагменты детали печатаются слой за слоем, пока не будет создан полный 3D-объект.
В небольших количествах FDM является очень быстрым и экономически эффективным и может производить широкий спектр форм, включая формы со сложной внутренней геометрией. Однако он не дает особо прочных деталей.
Примеры деталей FDM: различные прототипы, запасные части, композитные промышленные детали.
Литье пластмасс в силикон — доступное мелкосерийное производство в домашних условиях / Хабр
Многие из тех, кто печатает на 3D-принтере сталкиваются или с необходимостью получить партию моделей в короткие сроки, или скопировать удачно получившуюся деталь, или получить изделия с прочностными характеристиками, превосходящими таковые у пластиков для домашней 3d-печати.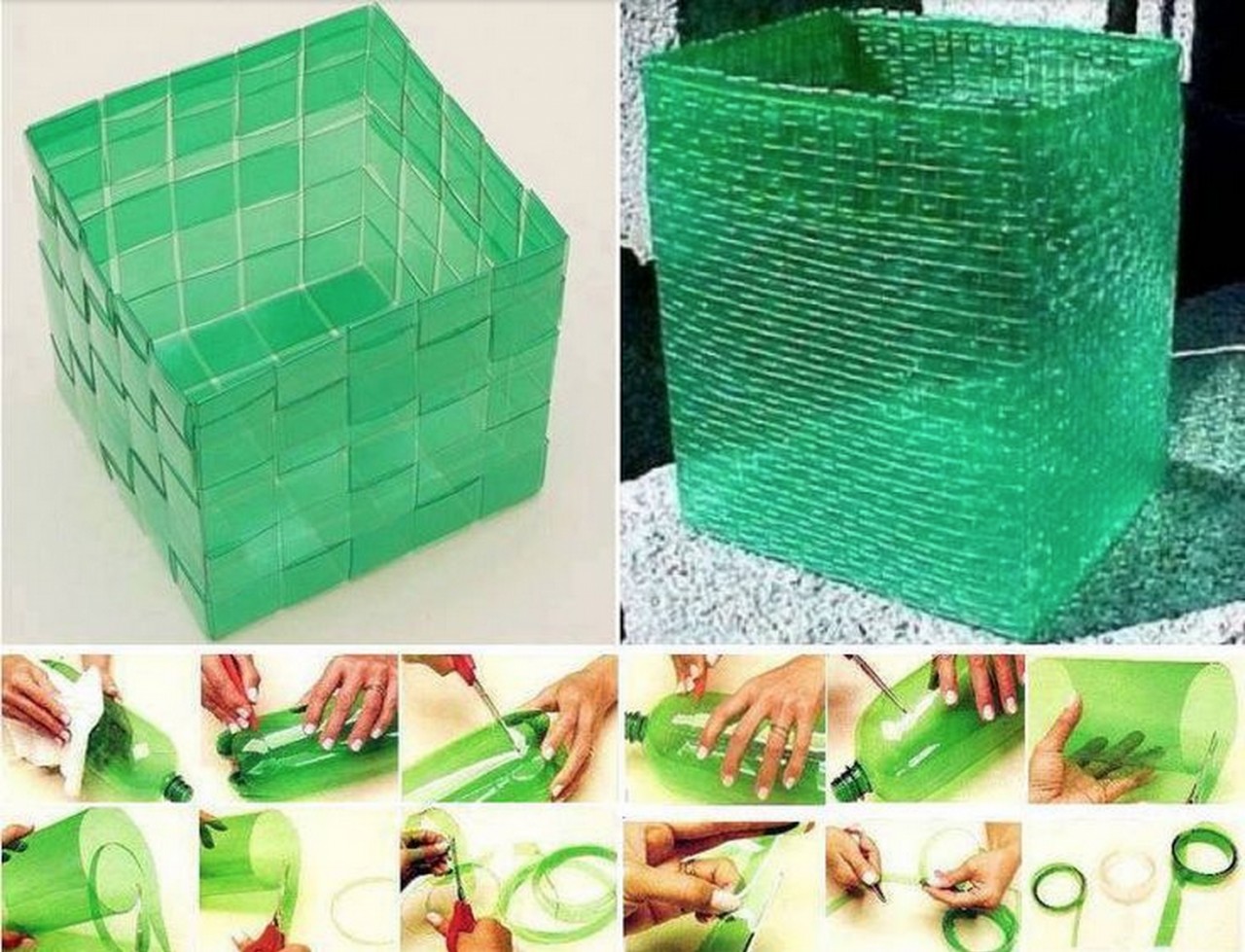
3D-принтер далеко не всегда способен выполнить такие задачи, но отлично подойдет для создания единственного образца, или мастер-модели. А дальше на помощь нам приходят материалы производства компании Smooth-On, наверное, самого популярного производителя материалов холодного отверждения.
В этом обзоре мы сравним самые основные и популярные силиконы, полиуретаны и добавки к ним, кратко посмотрим на основные способы создания форм и изделий, подумаем, где это может найти применение и, наконец, создадим свою силиконовую форму и модель.
Обзор процесса
Процесс создания изделий методом литья практически всегда одинаков: создаем модель, с её помощью создаем силиконовую форму, заливаем в нее материал, получаем изделие. Но в зависимости от модели, необходимых свойств, количества отливок, каждый этап может кардинально меняться. Существует несколько способов как создания формы, так и готового изделия.
Пару слов о подготовке моделей, напечатанных на 3D-принтере. Компания Smooth-On обратила своё внимание на эту технологию и выпустила специальный лак под названием XTC-3D. Он прекрасно сглаживает характерные для напечатанных моделей огрехи, видимые слои, которые обязательно перейдут на силиконовую форму, и придает поверхности гладкость и глянцевый вид.
Методы создания форм
• Сплошная заливка
Самый простой способ: модель помещается в опалубку (специальную герметичную емкость из обычного оргстекла, пластика или другого материала), фиксируется в ней и заливается силиконом. Хорошо подходит для простых двухмерных моделей, рельефов, сувенирной и брендинговой продукции.
• Разрезная форма
Аналогичен предыдущему, только модель размещается с учетом того, что форма будет разрезаться полностью или частично для облегчения съема. Модель может быть подвешена с помощью проволоки или размещена на тонкой опоре. Способ предназначен для более сложной геометрии, технических изделий, сложных фигур.
• Двухсоставная форма
Это один из самых сложных способов. Заключается в помещении модели на глиняную или пластилиновую основу, которая делит силиконовую форму пополам.
На основе размещаются специальные замки, которые будут обеспечивать точное совмещение двух форм и отсутствие смещений. Вокруг основы собирается опалубка, герметизируется горячим клеем или пластилином, и в неё заливается первая половина формы. Затем, после отверждения силикона, форма переворачивается, глина или пластилин счищаются, силикон покрывается разделительным составом, и заливается вторая половина формы.
• Метод «в намазку»
Этим методом создаются так называемые «чулочные» формы, когда силикон точно повторяет форму объекта и имеет толщину от 3 мм до нескольких сантиметров. Для создания формы «в намазку» необходим достаточно вязкий силикон, который бы не стекал с модели.
Можно использовать как специально предназначенные для этого силиконы, называемые тиксотропными, так и обычные, но модифицированные с помощью загустителей.
Силикон наносится кисточкой или шпателем в несколько слоёв, в которых чередуется вязкость и скорость отвердевания, чтобы форма была максимально детализированной и прочной. После того, как все слои готовы, с помощью специального состава создается жесткая внешняя оболочка, которая будет держать форму.
Методы заливки пластиков
Самый простой метод заключается в обычной заливке пластика в форму, он подходит для домашнего использования и позволяет достичь приемлемого качества. Но, по необходимости, для более качественного результата возможно использование установок высокого давления, что позволит практически полностью убрать пузырьки воздуха.
Для этого форма вместе с залитым пластиком помещается в камеру, в которой создается повышенное до 4 атмосфер давление. Форма должна оставаться в камере все время отвердевания полиуретана.
Еще один метод, так называемая заливка «в обкатку», используется для создания полых изделий. В форму заливается небольшое количество пластика, около 10% от общего объема, отверстие для заливки закрывается, и начинается вращение формы по всех плоскостях, вручную или на специальной ротационной машине. При этом пластик отвердевает на стенках формы, создавая полую модель, что позволяет существенно снизить вес изделия и экономить материал.
Обзор силиконов
• Серия Mold Star 15, 16, 30
Силиконы для создания форм на основе платины. Застывают при комнатной температуре, образуют прочную, гибкую и очень детализированную форму. Предназначены для литья силикона, полиуретана, смол, полиэстера, воска и других материалов. Химически чувствительны и не способны работать с латексом, серой и некоторыми другими соединениями.
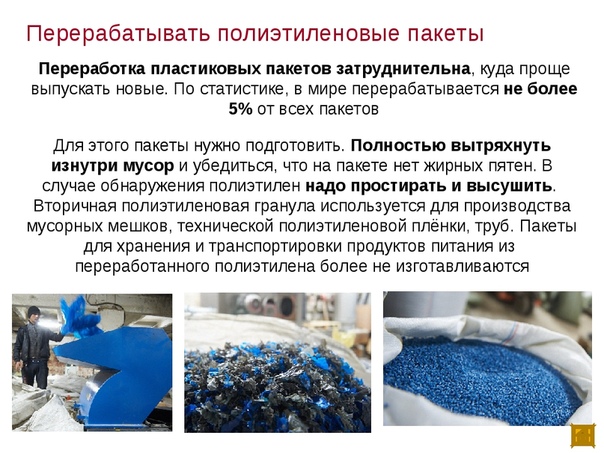
• Серия Rebound 25, 40
Серия силиконов для создания форм методом «в намазку», который состоит в том, чтобы наносить силикон кистью или шпателем на поверхность модели. Обладает высокой вязкостью, возможностью модификации свойств с помощью загустителей и ускорителей для создания качественной многослойной формы. Двухкомпонентный, смешивается в соотношении 1:1 по объему.
• Серия Equinox 35, 38, 40
Силиконовые пасты с временем жизни 1, 4 и 30 минут. Предназначены для ручного смешивания, по консистенции напоминают густое тесто. Цифры соответствуют твердости по Шору А. Обладает крайне высокой прочностью на разрыв и долговечностью. В отвержденном состоянии является безопасным для заливки шоколада, карамели и других ингридиентов.
• Серия SortaClear 18, 37, 40
Серия полупрозрачных силиконов. Такая особенность, как оптическая прозрачность, используется для создания сложных разрезных форм — изделие прекрасно просматривается, что позволяет сделать точный разрез. Как и серия Equinox, является безопасным при контакте с пищевыми продуктами.
Также к силиконам существует большое количество добавок, обладающих самыми разными эффектами. Accel-T и Plat-Cat являются ускорителями отверждения, Slo-jo — увеличивает время жизни силикона, Thi-Vex увеличивает вязкость силикона и позволяет намазывать его кистью или шпателем на модель, Silc-Pig — это концентрированные пигменты для окрашивания.
Обзор полиуретанов
• Серия Smooth-Cast
Самая основная и популярная серия полиуретанов для создания конечных изделий. Линейка включает в себя более 10 наименований различных пластиков с самыми разными свойствами, позволяющими подобрать материал именно для Вашего проекта. Например, Smooth-Cast 300 обладает коротким временем жизни в 3 минуты и временем отверждения в 10 минут, что позволяет быстро воспроизводить большие партии деталей. Smooth-Cast 305 аналогичен предыдущему, но «живет» уже 7 минут, что позволяет провести дегазацию смешанных компонентов и получить еще более качественное изделие. ONYX обладает глубоким черным цветом, которого не достичь с помощью красителей, 65D ROTO предназначен для создания полых моделей с помощью метода «в обкатку», 325 незаменим для точного воспроизведения цвета, 385 отверждается практически без усадки и максимально точно копирует изделие.
• Серия TASK
Серия полиуретанов специального назначения. Разработана для промышленного применения и обладает специфическими свойствами для конкретных задач.
Для Вашего удобства мы сформировали специальные фильтры по сферам применения:
• Пищевые:
Smooth-Sil 940, серия Sorta Clear, серия Equinox, TASK 11.
• Архитектурные, заливка бетона и других абразивных материалов:
Серия VytaFlex, серия Brush-On, серия Ez-Spray, серия PMC.
• Медицинские: симуляция тканей и органов
Серия Dragon Skin, добавки Slacker, Ecoflex 0030, Ecoflex Gel, Body Double.
• Прототипирование:
Практически любые полиуретаны и силиконы, в зависимости от задач и требований. Серии Mold Max, Mold Star, Smooth-Cast, TASK.
• Спецэффекты и грим:
Skin Tite, Body Double, Dragon Skin, Alja-Safe, Ecoflex, Soma Foama, Rubber Glass, Encapso K.
Стоит отметить, что это деление все же условное, и дано, чтобы примерно представить возможности широкого ассортимента компании Smooth-On.
Обзор процесса
Мы будем использовать только те материалы и оборудование, которые можно применить в домашних условиях. Мы попробуем создать самую сложную в изготовлении двухсоставную форму.
Нам понадобятся:
• Платиновый силикон Mold Star 30
• Заливочный полиуретан Smooth-Cast 300
• Лак для 3D-моделей XTC-3D
• Упаковка виниловых перчаток
• Несколько одноразовых пластиковых стаканчиков
• Емкости для смешивания
• Термоклеевой пистолет
• Материал для опалубки (пластиковые панели)
• Скульптурная глина
• Несколько малярных кистей
В роли мастер-модели выступит модель довольно популярного среди печатников тестового болта. Мы распечатали его черным PLA пластиком на Picaso 3D Designer с толщиной слоя 100 микрон. Сделали мы это специально для того, чтобы продемонстрировать эффект XTC 3D, поскольку далеко не каждый 3D принтер может печатать с качеством 50 микрон.
Далее — обработка, чтобы отлитая модель не переняла слоистость напечатанного объекта. Обрабатываем болт лаком XTC-3D (подробнее об этом процесс можно прочитать тут), а затем шкурим, чтобы получить гладкую матовую поверхность.
Теперь модель готова к заливке силиконом. Помещаем её на глиняную основу, с помощью которой мы создадим силиконовую форму из двух частей.
Модель должна быть погружена в глину ровно наполовину, так что начинаем процесс выравнивания глины. Края должны быть максимально ровными и полностью прилегать к модели, от этого зависит качество разделения силиконовых половинок. Убираем лишнюю глину и заключаем модель в пластиковую опалубку.
Все стыки пластика обрабатываем термоклеевым пистолетом и закрываем опалубку, окончательно обрабатываем глиняную основу, делаем в ней выемки для замков.
Все готово к заливке силикона. Поскольку двухкомпонентные силиконы и полиуретаны склонны к разделению на фракции, перед каждым использованием их необходимо тщательно перемешивать в емкости.
После перемешивания отмеряем равное количество двух компонентов по объему и приступаем к смешиванию.
Для данной марки силикона дегазация в вакуумной камере необязательна, что очень удобно: исключены появления пузырьков, которые могут испортить нашу форму. Медленно заливаем силикон в опалубку, в самую нижнюю её точку.
И оставляем застывать. Время застывания для этой марки силикона составляет 6 часов. По истечении этого времени освобождаем модель от опалубки.
Затем убираем глину, тщательно очищаем модель от её остатков, смазываем силикон разделительным составом. В случае его отсутствия, можно использовать и обычный вазелин, но качество будет немного хуже.
И дальше полностью повторяем процесс, заливая вторую половину силиконовой формы.
Спустя еще 6 часов силиконовая форма готова. С помощью лезвия аккуратно разъединяем половинки, вынимаем деталь и оцениваем, что у нас получилось.
Хорошо видны замки, закладывавшиеся в глиняной основе, хорошая детализация, несмотря на то, что разделительная линия проходила по довольно сложным местам, вроде вдавленных букв.
На самом деле, для данной модели это не самый оптимальный способ создания формы. Но нам было интересно протестировать именно этот метод, несмотря на сложности.
Итак, все готово к заливке полиуретана. Соединяем две половинки формы, используя элементы опалубки для жесткости, скрепляем с помощью резинок, скотча или другим способом, и приступаем к подготовке полиуретана.
Хорошо перемешиваем оба компонента, встряхивая их в течение 5-10 минут. После этого даем немного отстояться, чтобы вышли образовавшиеся пузыри. Все остальное точно так же, как и с силиконом: отмеряем равное количество по объему и смешиваем их. А дальше действовать нужно быстро: время жизни этого полиуретана составляет всего 3 минуты, а время начинает идти сразу, как вы смешали два компонента вместе. Так что мешаем быстро, но аккуратно, чтобы не создавать лишних пузырьков, и сразу заливаем в форму.
Примерно через 3 минуты, в зависимости от объема материала, произойдет быстрое схватывание пластика, а через 10 минут деталь готова к извлечению.
Модель готова. Переданы абсолютно все детали оригинала.
Заключение
Хочется отметить, что поистине огромные возможности использование материалов Smooth-On открывает в совокупности с 3D-печатью.
Теперь Вы можете получать изделия из огромного количества материалов с самыми различными свойствами, а не ограничиваться лишь классическими PLA и ABS. К тому же, доступным станет мелкосерийное производство: распечатав всего один экземпляр и должным образом его обработав, Вы сможете в довольно короткие сроки создать необходимое Вам количество копий в домашних условиях. Для достижения приемлемого результата вовсе не обязательно использование дорогостоящего оборудования.
В случае если Вам необходимы услуги мелкосерийного производства Top 3D Shop к вашим услугам.
Как делают пластик? Пошаговое объяснение
Как делают пластик? В этой статье рассматривается весь процесс изготовления пластика с подробным объяснением всех его этапов.
В 1950-х годах производилось около 2 миллионов тонн пластика в год. К 2015 году это число увеличилось в 200 раз, а к 2021 году в мире насчитывалось примерно 8,3 миллиарда тонн пластика. Благодаря своей универсальности, простоте изготовления и низкой стоимости этот материал используется в самых разных областях: от одноразовых очков до мебели для дома, автомобильных запчастей, самолетов и оборудования связи. Но сначала:
Что такое пластик?
Пластмасса представляет собой синтетический или природный полимер, который благодаря своей структуре легко формуется и формуется под воздействием тепла и давления. Это свойство известно как пластичность, отсюда и название этого материала. Кроме того, пластик химически устойчив, легок, водо- и ударопрочен, имеет низкую теплопроводность, обладает хорошими изоляционными свойствами.
Полимеры — это большие молекулы, образованные химическим соединением ряда более простых единиц, называемых мономерами, что создает цепочечную структуру. Эти вещества, помимо того, что служат основой для пластика, являются основным компонентом многих других материалов, таких как стекло, бумага и резина. Кроме того, полимеры являются основой таких минералов, как алмаз, кварц и полевой шпат, а также материалов живых организмов, таких как белки, целлюлоза и нуклеиновые кислоты. В зависимости от назначения полимеры могут обладать многочисленными свойствами, такими как отражательная способность, ударопрочность, хрупкость, прозрачность, пластичность и эластичность.
Схема полимерной структуры поликарбоната, состоящего из кислорода, углерода и водорода.Изображение предоставлено: petrroudny43/Shutterstock
Чаще всего пластик подразделяется на две отдельные группы; термопласты и реактопласты. Между этими двумя группами существует несколько основных различий, главное из которых заключается в том, что термопласты можно многократно нагревать и изменять форму, в то время как термореактивные материалы затвердевают до постоянной формы под воздействием тепла. Более того, молекулярная масса термопластов колеблется от 20 000 до 500 000 AMU (атомная единица массы), тогда как считается, что термореактивные материалы имеют бесконечную молекулярную массу.
Из чего сделан пластик?
Большинство используемого сегодня пластика производится из углеводородов — органических молекул, полностью состоящих из углерода и водорода. Эти углеводороды получены из материалов биологического происхождения, встречающихся в земной коре, известных как ископаемое топливо. Ископаемое топливо создается из окаменевших, погребенных останков растений и животных, существовавших миллионы лет назад. Некоторые примеры ископаемого топлива:
- Сырая нефть – также известная как жидкая нефть. Его можно найти в нефтеносных песках (битуминозных песках), подземных резервуарах, а также в щелях и порах осадочных пород. Его можно получить путем бурения на суше или в море, либо путем добычи полезных ископаемых.
- Природный газ – также известный как газ метан.
В зависимости от того, где он находится под землей, природный газ классифицируется как традиционный или нетрадиционный. Обычный тип можно найти в проницаемых коренных породах или смешать с нефтяными резервуарами и его можно извлечь с помощью обычных методов бурения. С другой стороны, нетрадиционная добыча природного газа требует специальных методов, таких как фрекинг, поскольку обычная технология бурения может быть слишком дорогостоящей и сложной.
- Уголь — это твердая, богатая углеродом горная порода, которая подразделяется на четыре типа в зависимости от содержания углерода: бурый уголь, полубитуминозный, битуминозный и антрацит. Добыча угля осуществляется либо подземным способом, при котором используются машины для добычи угля из глубоких подземных пластов, либо открытым способом, при котором соскребают слои почвы, чтобы добраться до угольных залежей.
Важно отметить, что пластик можно производить из других, более экологически чистых источников, которые заменяют ископаемое топливо. Этот пластик, известный как возобновляемый пластик или биопластик, создается из возобновляемой биомассы, такой как терпены, лигнин, целлюлоза, растительный жир, бактерии, древесные волокна, углеводы, переработанные пищевые отходы и т. д. Биоразлагаемый пластик не содержит потенциально опасного химического вещества BPA. и, скорее всего, рассосется через пару месяцев. Кроме того, в течение своего срока службы биопластик выделяет гораздо меньше парниковых газов по сравнению с обычным пластиком.
Как производится пластик?
В этом разделе будет рассказано все, что вам нужно знать обо всем процессе производства пластика, начиная с добычи сырья и заканчивая его изготовлением.
Извлечение сырья M МатериалыКак упоминалось выше, подавляющее большинство производимого пластика производится из ископаемого топлива. Поэтому добыча сырой нефти, природного газа, а иногда и угля из-под земли является первым шагом.
Уточнение Ископаемые виды топлива отправляются на нефтеперерабатывающие заводы, где они перерабатываются в различные нефтепродукты, такие как бензин, асфальт, топливо для реактивных двигателей, воски и смазочные масла. Здесь также создаются строительные блоки из пластика, этана и пропана. Как это работает?
Сырая нефть нагревается в печи перед испарением и подается в колонну фракционной перегонки. Дистилляционная колонна имеет температурный градиент, причем верх холоднее, чем низ. В зависимости от температуры кипения (температуры, при которой происходит фазовый переход от жидкости к газу) и веса жидкости и газы в колонне разделяются. Пары более легких фракций, таких как бензин и нефтяной газ, дрейфуют наверх колонны, а более тяжелые, такие как мазут, остаются внизу. Все эти фракции в башне содержат углеводороды с сопоставимым количеством атомов углерода, при этом более мелкие молекулы находятся вверху. Сжиженный природный газ (ШФЛУ), такой как этан и пропан, а также нафта являются наиболее важным сырьем для производства пластика. Однако, чтобы быть полезными, эти углеводороды должны быть отправлены на установку крекинга и подвергнуты процедуре, называемой крекингом.
Схема дистилляционной колонны, используемой для сортировки углеводородов, используемых при производстве пластика.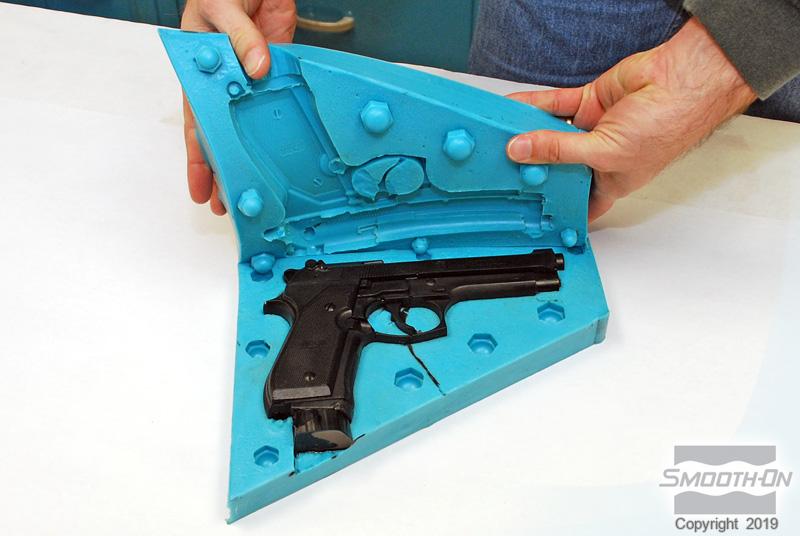
Изображение предоставлено Стивом Симро/Shutterstock
Растрескивание
При использовании высокой температуры, давления и иногда катализаторов сложные углеводороды расщепляются на более простые низкомолекулярные алкены/алканы. Этот процесс важен, потому что он превращает упомянутый выше этан в этилен, а пропан в пропилен. Существует два типа крекинга: паровой крекинг и каталитический крекинг.
Процесс парового крекинга осуществляется в установках парового крекинга, которые являются чрезвычайно сложными и энергоемкими установками. Здесь химикаты сначала смешиваются с паром, а затем нагреваются до 1430-1610 градусов по Фаренгейту внутри трубчатого реактора. Чтобы сырье не образовывало нагар, что может произойти при таких температурах, его подают по трубам печи очень быстро и при очень низком давлении. Поток здесь играет две роли; во-первых, предотвращает коксование, а во-вторых, предотвращает возможные утечки, которые могут привести к попаданию воздуха в исходное сырье и созданию взрывоопасной смеси. В конце концов, крекинг-сырье быстро охлаждают с использованием ряда методов, таких как сжатие, абсорбция, сушка, охлаждение, фракционирование и селективное гидрирование.
Процесс каталитического крекинга не требует таких высоких температур или давления благодаря присутствию катализатора. Во-первых, в фазе реакции сырье контактирует с катализатором при температуре около 900 градусов по Фаренгейту, и происходит реакция крекинга. Пропорции продукта определяются температурой, временем пребывания и катализатором. На этапе регенерации катализатор удаляется из продуктов, регенерируется на воздухе путем сжигания накопленного углерода, а затем перерабатывается. В конце концов, для разделения крекинг-углеводородов используется фракционирующее оборудование – процедура, известная как фракционирование. Этилен и пропилен превращаются таким образом в мономеры, а затем перерабатываются в полимеры.
Полимеризация При полимеризации мономеры соединяются в результате химической реакции с образованием полимеров. Это может быть достигнуто либо добавлением, в результате которого все атомы мономера присутствуют в полимере, либо конденсацией, что приводит к образованию побочного продукта в виде крошечной молекулы. Давайте подробнее рассмотрим оба метода полимеризации:
Аддитивная полимеризация – мономеры просто «добавляются» вместе, и в ходе этого процесса атомы не теряются и не приобретаются. Мономеры с двойными связями представляют собой простейшую химическую структуру, в которой может происходить полимеризация. Для запуска процесса полимеризации можно использовать тепло и давление, ультрафиолетовый свет или другое более реактивное химическое вещество, такое как перекись. В результате реакции двойная связь разрывается и высвобождаются высокореакционноспособные неспаренные электроны, известные как свободные радикалы. Полимерная цепь начинает формироваться, когда эти радикалы реагируют с другими радикалами или с другими двойными связями. Примерами аддитивных полимеров являются полиэтилен, полипропилен, ПТФЭ, акрил и каучук.
Конденсационная полимеризация – большинство природных полимеров образуются в результате конденсационной полимеризации. Этот тип полимеризации более сложен, чем предыдущий. Помимо полимеров, эта реакция приводит к образованию еще одной небольшой молекулы. Эта небольшая молекула, известная как побочный продукт, часто представляет собой воду. Иногда побочные продукты могут быть сырьем, которое перерабатывается в исходное сырье. Некоторые примеры конденсационных полимеров включают нейлон и ПЭТ.
После этой стадии этилен превращается в полиэтилен, а пропилен — в полипропилен.
Полиэтилен — наиболее часто используемый пластик в мире. Он очень пластичен и устойчив; области применения варьируются от газопроводных и водопроводных сетей до изоляции кабелей передачи данных. Полипропилен даже тверже полиэтилена и более термостойкий. Его можно найти в автомобильных деталях и медицинских шприцах.
Производство пластмасс Изготовление — это последний этап, на котором пластик приобретает окончательную форму. Для облегчения транспортировки пластиковые смолы чаще всего перерабатываются в гранулы. Затем эти гранулы превращаются в различные пластиковые изделия. Существуют различные методы изготовления пластика; некоторые из наиболее часто используемых:
- Экструзия – расплавленный полимер выдавливается через отверстие определенного поперечного сечения (фильеру) для формирования непрерывной формы с поперечным сечением, сравнимым с сечением отверстия. Экструзия может производить различные изделия, в том числе пленку, лист, трубы, трубы, изоляцию и обшивку дома. Профиль в каждом случае определяется геометрией штампа, а затвердевание достигается за счет охлаждения. Дополнительную информацию можно найти в нашем руководстве по экструзии пластика.
- Литье – жидкий пластик заливают в определенную емкость или форму и затвердевают в определенной форме. Существуют различные типы формования: литье под давлением, выдувное формование, ротационное формование, реактивное литье под давлением, компрессионное формование и формование в мешках.
Если вы хотите приобрести формовочное оборудование, но у вас все еще есть вопросы, возможно, вам стоит прочитать это руководство по закупкам Томаса о типах формовочного оборудования и его поставщиках.
- Сварка – две или более заготовок соединяются вместе путем их плавления при высокой температуре. Сварку можно выполнять различными способами, включая выбросы горячих газов, высокочастотную вибрацию, вращение и контактную сварку. Оборудование для сварки пластика различается в зависимости от метода и вида используемого пластика.
Если вы хотите узнать больше о различных производственных процессах, ознакомьтесь с нашим руководством, в котором рассматриваются методы изготовления пластика.
Вывод
Пластик может быть искусственным полимером, но в основном он создается из ископаемого топлива, такого как сырая нефть, природный газ и уголь. В этой статье дается подробное объяснение всего процесса производства пластика, включая его этапы от добычи сырья, переработки ископаемого топлива и крекинга углеводородов до полимеризации и изготовления. Теперь вы должны лучше знать, что такое пластик, его основные ингредиенты и то, как ископаемое топливо превращается в один из наиболее часто производимых материалов на Земле. Если вы хотите узнать больше о других темах, связанных с пластмассами, не стесняйтесь обращаться к нашей библиотеке технических руководств, чтобы узнать больше.
- https://recyclecoach.com/resources/7-revealing-plastic-waste-statistics-2021/
- https://www.britannica.com/science/пластик
- https://www.britannica.com/science/polymer
- https://www.thoughtco.com/what-is-a-polymer-820536
- https://www.thoughtco.com/plastic-chemical-composition-608930
- https://www.bpf.co.uk/plastipedia/how-is-plastic-made.aspx
- https://www.britannica.com/science/fossil-fuel
- https://www.britannica.com/science/crude-oil
- https://www.britannica.com/science/natural-gas
- https://www.britannica.com/science/coal-fossil-fuel
- https://homeguides.
sfgate.com/benefits-biodegradable-plastic-79207.html
- https://www.essentialchemicalindustry.org/processes/cracking-isomerisation-and-reforming.html
- https://fqechemicals.com/catalytic-cracking/
- https://www.britannica.com/science/polymerization
- https://www.britannica.com/science/plastic/The-processing-and-fabrication-of-plastics
- https://adamsplastics.com/plastics/
- https://www.wshampshire.com/plastic-materials/
- https://ppprecycle.com/services/plastic-reprocessing/
- https://www.jamestownplastics.com/reduce-reuse-and-recycle
- Реакционное литье под давлением
- Изделия, созданные с помощью экструзии пластика
- Основы литья под давлением
- Производство пресс-форм для литья под давлением
- Дефекты пластикового литья
- Процесс формования пакетов
- Процесс экструзии пластмасс
- Стандартные пластиковые профили
- Типы пластиковых шнеков для экструзии
- Сравнение термореактивных и термопластичных материалов
- ПЭТ-пластик: экономия денег и энергии благодаря вторичному пластику
- Коэкструзия пластика
- Машина для экструзии пластмасс – процесс и методы
- Ведущие компании по литью под давлением в США
- Производство пластиковых преформ
- Технологии и методы изготовления пластмасс
- Как металлизировать пластик
- О пластиковых вставках
- Литье под давлением и литье поверх — в чем разница?
- Ведущие компании и поставщики экструзии пластмасс в США
Больше из пластика и резины
Руководство по производственным процессам пластмасс
Пластмассы являются наиболее распространенными материалами для производства деталей и изделий конечного использования, от потребительских товаров до медицинских устройств. Пластмассы — это универсальная категория материалов с тысячами вариантов полимеров, каждый из которых имеет свои особые механические свойства. Но как изготавливаются пластиковые детали?
Было разработано множество процессов производства пластмасс, охватывающих широкий спектр областей применения, геометрий деталей и типов пластмасс. Для любого дизайнера и инженера, занимающегося разработкой продукции, очень важно знать о доступных сегодня вариантах производства и новых разработках, которые показывают, как детали будут производиться завтра.
В этом руководстве представлен обзор наиболее распространенных производственных процессов для изготовления пластиковых деталей, а также рекомендации, которые помогут вам выбрать наилучший вариант для вашей области применения.
При выборе производственного процесса для вашего продукта учитывайте следующие факторы:
Форма: У ваших деталей есть сложные внутренние особенности или жесткие требования к допускам? В зависимости от геометрии конструкции варианты изготовления могут быть ограничены или может потребоваться значительная оптимизация конструкции для производства (DFM), чтобы сделать их производство экономичным.
Объем/стоимость: Какой общий или годовой объем деталей вы планируете производить? Некоторые производственные процессы имеют высокие первоначальные затраты на инструменты и настройку, но производят детали, которые недороги в расчете на одну деталь. Напротив, производственные процессы с малым объемом производства имеют низкие начальные затраты, но из-за более медленного времени цикла, меньшего количества автоматизации и ручного труда стоимость одной детали остается постоянной или снижается лишь незначительно при увеличении объема.
Время выполнения: Как быстро вам нужно изготовить детали или готовую продукцию? Некоторые процессы создают первые детали в течение 24 часов, в то время как подготовка и настройка для некоторых крупносерийных производственных процессов занимают месяцы.
Материал: Каким нагрузкам и напряжениям должен противостоять ваш продукт? Оптимальный материал для данного применения определяется рядом факторов. Стоимость должна быть сбалансирована с функциональными и эстетическими требованиями. Рассмотрите идеальные характеристики для вашего конкретного применения и сравните их с доступными вариантами в данном производственном процессе.
Загрузите версию этой инфографики в высоком разрешении здесь.
ВидеоруководствоНе можете найти лучшую технологию 3D-печати для ваших нужд? В этом видеоруководстве мы сравниваем технологии FDM, SLA и SLS с учетом популярных соображений покупателей.
Смотреть видеоПластмассы бывают тысяч разновидностей с различным базовым химическим составом, производными и добавками, состав которых обеспечивает широкий спектр функциональных и эстетических свойств.
Чтобы упростить процесс поиска материала, наиболее подходящего для данной детали или продукта, давайте сначала рассмотрим два основных типа пластика: термопласты и реактопласты.
Термопласты являются наиболее часто используемым типом пластика. Главной особенностью, которая отличает их от реактопластов, является их способность проходить через многочисленные циклы плавления и затвердевания без существенной деградации. Термопласты обычно поставляются в виде небольших гранул или листов, которые нагревают и придают им желаемую форму с использованием различных производственных процессов. Процесс полностью обратим, так как не происходит химического связывания, что делает возможной переработку или плавление и повторное использование термопластов.
Распространенные типы термопластичных материалов:
- Акрил (ПММА)
- Акрилонитрилбутадиенстирол (АБС)
- Полиамид (ПА)
- Полимолочная кислота (PLA)
- Поликарбонат (ПК)
- Полиэфирэфиркетон (PEEK)
- Полиэтилен (ПЭ)
- Полипропилен (ПП)
- Поливинилхлорид (ПВХ)
В отличие от термопластов, термореактивные пластмассы (также называемые термореактивными) остаются в постоянном твердом состоянии после отверждения. Полимеры в термореактивных материалах сшиваются в процессе отверждения под действием тепла, света или подходящего излучения. Этот процесс отверждения образует необратимую химическую связь. Термореактивные пластмассы разлагаются при нагревании, а не плавятся, и не восстанавливаются при охлаждении. Переработка термореактивных материалов или возврат материала обратно в его основные ингредиенты невозможна.
Распространенные типы термопластичных материалов:
- Сложный эфир цианата
- Эпоксидная смола
- Полиэстер
- Полиуретан
- Силикон
- Вулканизированная резина
- 3D-печать
- Обработка с ЧПУ
- Полимерное литье
- Ротационное формование
- Вакуумное формование
- Литье под давлением
- Экструзия
- Выдувное формование
3D-принтеры создают трехмерные детали непосредственно из моделей САПР, слой за слоем создавая материал, пока не будет сформирована полная физическая деталь.
- Настройка печати: Программное обеспечение для подготовки к печати используется для ориентации и компоновки моделей в объеме сборки принтера, добавления поддерживающих структур (при необходимости) и разделения поддерживаемой модели на слои.
- Печать: Процесс печати зависит от типа технологии 3D-печати: моделирование методом наплавления (FDM) расплавляет пластиковую нить, стереолитография (SLA) отверждает жидкую смолу, а селективное лазерное спекание (SLS) сплавляет порошкообразный пластик.
- Постобработка: По завершении печати детали удаляются из принтера, очищаются или промываются, подвергаются постотверждению (в зависимости от технологии) и удаляются опорные конструкции (если применимо).
Поскольку 3D-принтеры не требуют инструментов и требуют минимального времени настройки для новой конструкции, стоимость изготовления нестандартной детали незначительна по сравнению с традиционными производственными процессами.
Процессы 3D-печати, как правило, медленнее и трудоемче, чем производственные процессы, используемые для массового производства.
По мере совершенствования технологий 3D-печати стоимость одной детали продолжает снижаться, открывая более широкий спектр приложений для малых и средних объемов.
3D-печать | |
---|---|
Форма | Высокая степень свободы |
Менее 24 часов | |
Время цикла | |
Стоимость установки | $ |
Стоимость одной детали | $$$ |
Применение в малых и средних объемах (~1-1000 деталей) |
В то время как для большинства процессов производства пластмасс требуется дорогостоящее промышленное оборудование, специальные помещения и квалифицированные операторы, 3D-печать позволяет компаниям легко создавать пластмассовые детали и быстрые прототипы на месте.
Компактные настольные или настольные системы 3D-печати для создания пластиковых деталей доступны по цене и требуют очень мало места и не требуют специальных навыков, что позволяет профессиональным инженерам, дизайнерам и производителям ускорить итерации и производственные циклы с дней или недель до нескольких часов.
На рынке представлено множество типов 3D-принтеров и технологий 3D-печати, а доступные материалы зависят от технологии.
Материалы для 3D-печати | |
---|---|
Моделирование наплавлением (FDM) | Различные термопласты, в основном ABS и PLA |
Стереолитография (SLA) | Термореактивные смолы | 9 0343
Селективное лазерное спекание (SLS) | Термопласты, обычно нейлон и его композиты |
Ищете 3D-принтер для печати ваших 3D-моделей в высоком разрешении? Загрузите наш информационный документ, чтобы узнать, как работает SLA-печать и почему это самый популярный процесс 3D-печати для создания моделей с невероятной детализацией.
Убедитесь сами и убедитесь в качестве Formlabs. Мы отправим бесплатный образец детали в ваш офис.
Запросить бесплатный образец Деталь
Обработка с ЧПУ включает в себя фрезерные станки, токарные станки и другие субтрактивные процессы, управляемые компьютером. Эти процессы начинаются с твердых блоков, стержней или стержней из металла или пластика, которым придают форму путем удаления материала путем резки, сверления, сверления и шлифования.
В отличие от большинства других процессов производства пластмасс, обработка с ЧПУ представляет собой вычитающий процесс, при котором материал удаляется либо вращающимся инструментом и неподвижной частью (фрезерование), либо вращающейся частью с неподвижным инструментом (токарный станок).
- Настройка задания: На станках с ЧПУ требуется промежуточный этап создания и проверки траекторий (из CAD в CAM). Траектории инструмента управляют тем, где перемещаются режущие инструменты, с какой скоростью и какой сменой инструмента.
- Обработка: Траектории инструмента отправляются на станок, где начинается данный процесс вычитания. В зависимости от желаемой формы конечного продукта может потребоваться установить заготовку в новое положение, чтобы головка инструмента могла достигать новых областей.
- Постобработка: После изготовления деталь зачищают, удаляют заусенцы, обрезают.
Механическая обработка идеально подходит для небольших объемов пластиковых деталей, требующих жестких допусков и геометрии, которые трудно формовать. Типичные области применения включают прототипирование и детали конечного использования, такие как шкивы, шестерни и втулки.
CNC-обработка имеет низкую или умеренную стоимость настройки и позволяет производить высококачественные пластиковые компоненты в кратчайшие сроки из широкого спектра материалов.
Процессы обработки имеют больше ограничений по геометрии детали, чем 3D-печать. При механической обработке стоимость детали увеличивается с увеличением сложности детали. Подрезы, проходы и элементы на нескольких поверхностях деталей увеличивают стоимость детали.
Процессы обработки требуют припусков на доступ к инструменту, а определенные геометрические формы, такие как изогнутые внутренние каналы, трудно или невозможно изготовить с помощью обычных методов вычитания.
Обработка с ЧПУ | |
---|---|
Форма | Средняя степень свободы |
Время выполнения заказа | Менее 24 часов |
Время цикла | |
Стоимость установки | $$ |
Стоимость одной детали | $$$$ |
Объем | Обработка малых и больших объемов (~1-5000 деталей) |
Большинство твердых пластиков можно обрабатывать с некоторой разницей в сложности. Для более мягких термореактивных пластиков требуются специальные инструменты для поддержки деталей во время обработки, а пластики с наполнителями могут быть абразивными и сокращать срок службы режущего инструмента.
Некоторые часто обрабатываемые пластики:
- Акрил (ПММА)
- Акрилонитрилбутадиенстирол (АБС)
- Полиамид нейлон (ПА)
- Полимолочная кислота (PLA)
- Поликарбонат (ПК)
- Полиэфирэфиркетон (PEEK)
- Полиэтилен (ПЭ)
- Полипропилен (ПП)
- Поливинилхлорид (ПВХ)
- Поликарбонат (ПК)
- Полистирол (ПС)
- Полиоксиметилен (ПОМ)
Веб-семинар
На этом веб-семинаре вы узнаете, как проектировать и печатать на 3D-принтере приспособления и приспособления для замены механически обработанных деталей, а также узнаете о пяти способах повышения эффективности вашего производственного цеха с помощью 3D-печати.
Посмотреть вебинар сейчасПри литье полимеров реактивная жидкая смола или каучук заполняет форму, которая вступает в химическую реакцию и затвердевает. Типичные полимеры для литья включают полиуретан, эпоксидную смолу, силикон и акрил.
- Подготовка пресс-формы: Форма покрыта разделительной смазкой для облегчения извлечения из формы и часто предварительно нагревается до определенной температуры материала.
- Литье: Синтетическая смола смешивается с отвердителем и заливается или впрыскивается в форму, где она заполняет полость формы.
- Отверждение: Отливка отверждается в форме до тех пор, пока не затвердеет (для некоторых полимеров нагревание формы может ускорить время отверждения).
- Извлечение из формы: Форма открывается, и отвержденная деталь удаляется.
- Обрезка: Дефекты литья, такие как заусенцы, литники и швы, обрезаются или шлифуются.
Гибкие формы, изготовленные из латексной резины или силиконовой резины, вулканизированной при комнатной температуре (RTV), недороги по сравнению с твердой оснасткой, но могут производить лишь ограниченное количество (от 25 до 100) отливок в результате химической реакции уретанов, эпоксидных смол, полиэстера. , а акрил разрушает поверхности формы.
9Силиконовые формы 0002 RTV позволяют воспроизводить даже мельчайшие детали, получая отливки высокого качества.
Полимерное литье является относительно недорогим, с небольшими первоначальными инвестициями, но термореактивные полимеры для литья обычно дороже, чем их термопластичные аналоги, а формование литых деталей является трудоемким. Каждая литая деталь требует некоторого ручного труда для последующей обработки, что делает конечную стоимость детали высокой по сравнению с автоматизированными методами производства, такими как литье под давлением.
Полимерное литье обычно используется для прототипирования, мелкосерийного производства, а также в некоторых стоматологических и ювелирных целях.
Полимерное литье | |
---|---|
Форма | Высокая степень свободы |
Менее 24 часов до нескольких дней | |
Время цикла | От минут до нескольких дней , в зависимости от времени отверждения |
Стоимость установки | $ |
Стоимость за деталь | $$ |
Объем | Применение в малых объемах (~1-1000 деталей) |
- Полиуретан
- Эпоксидная смола
- Полиэфир
- Полиэстер
- Акрил
- Силикон
Ротационное формование (также называемое ротационным формованием) представляет собой процесс, включающий нагревание полой формы, заполненной порошкообразным термопластом, и вращение вокруг двух осей для производства в основном крупных полых изделий. Процессы центробежного формования термореактивных пластмасс также доступны, однако менее распространены.
- Зарядка: Порошок пластика загружается в полость формы, а затем устанавливаются остальные части формы, закрывая полость для нагрева.
- Нагрев: Форму нагревают до тех пор, пока пластиковый порошок не расплавится и не прилипнет к стенкам формы, при этом форму вращают вдоль двух перпендикулярных осей для обеспечения однородного пластикового покрытия.
- Охлаждение: Форма медленно охлаждается, в то время как форма остается в движении, чтобы гарантировать, что оболочка детали не провиснет и не разрушится до полного затвердевания.
- Удаление детали: Деталь отделяется от формы, любые заусенцы обрезаются.
Для ротационного формования требуются менее дорогие инструменты, чем для других методов формования, поскольку в этом процессе для заполнения формы используется центробежная сила, а не давление. Формы могут быть изготовлены, обработаны на станке с ЧПУ, отлиты или сформированы из эпоксидной смолы или алюминия с меньшими затратами и намного быстрее, чем инструменты для других процессов литья, особенно для крупных деталей.
Ротационное формование позволяет создавать детали с практически одинаковой толщиной стенок. После того, как инструменты и процесс настроены, стоимость одной детали становится очень низкой по сравнению с размером детали. Также можно добавить в форму готовые детали, такие как металлическая резьба, внутренние трубы и конструкции.
Эти факторы делают ротационное формование идеальным для мелкосерийного производства или в качестве альтернативы выдувному формованию для небольших объемов. Типичные продукты ротационного формования включают резервуары, буи, большие контейнеры, игрушки, шлемы и корпуса каноэ.
Ротационное формование имеет некоторые конструктивные ограничения, а готовые изделия имеют более низкие допуски. Поскольку вся пресс-форма должна нагреваться и охлаждаться, процесс также имеет длительное время цикла и является довольно трудоемким, что ограничивает его эффективность при больших объемах производства.
Ротационное формование | |
---|---|
Форма | Средняя степень свободы, идеально подходит для больших полых деталей | Время выполнения | От нескольких дней до нескольких недель |
Время цикла | Обычно |
Стоимость установки | $$$ |
Стоимость за деталь | $$ |
Объем | Приложения среднего объема (~200-5000 деталей) |
Наиболее распространенным материалом для ротационного формования является полиэтилен (ПЭ), который используется в 80% случаев, главным образом потому, что ПЭ легко измельчается в порошок при комнатной температуре.
Обычно ротационно формованные пластмассы включают:
- Полиэтилен
- Полипропилен
- Поливинилхлорид
- Нейлон
- Поликарбонат
Вакуумное формование или термоформование — это производственный метод, при котором пластик нагревается и формуется, как правило, с использованием пресс-формы. Вакуум-формовочные машины различаются по размеру и сложности от недорогих настольных устройств до автоматизированного промышленного оборудования. Шаги ниже описывают типичный процесс промышленного вакуумного формования.
- Зажим: Пластиковый лист зажимается в раме.
- Нагрев: Лист и рама сдвинуты вплотную к нагревательным элементам, что делает пластик мягким и податливым.
- Вакуум: Рама опускается, пластик натягивается на форму, при этом включается вакуум, чтобы высосать весь воздух из пространства между пластиком и формой, формируя таким образом деталь.
- Охлаждение и разъединение: После того, как деталь сформирована на форме, ей нужно дать время остыть перед удалением. Система охлаждения, такая как вентиляторы и распыляемый туман, иногда используются для сокращения времени цикла.
- Обрезка: После освобождения детали излишки материала обрезаются либо вручную, либо на станке с ЧПУ.
Стоимость инструментов для вакуумной формовки низка по сравнению с другими методами формовки из-за малых усилий и давления. Формы изготавливаются из дерева, гипса или смолы, напечатанной на 3D-принтере, для мелкосерийного производства и нестандартных деталей. Для больших объемов производства производители используют более прочную металлическую оснастку.
Учитывая широкий спектр оборудования для термоформования и вакуумной формовки, а также возможности автоматизации на самом высоком уровне, термоформование идеально подходит для любого применения: от изготовления изделий на заказ или прототипов до массового производства. Однако этот процесс предлагает лишь ограниченную свободу форм и может использоваться только для изготовления деталей с относительно тонкими стенками и простой геометрией.
Части, формируемые под вакуумом, обычно включают упаковку продуктов, душевые поддоны, обивку дверей автомобилей, корпуса лодок и нестандартные изделия, такие как выравниватели зубов.
Вакуумная формовка | |
---|---|
Форма | Ограниченная свобода, только тонкостенные детали, без сложной геометрии | 9034 3
Время выполнения | Менее 24 часов до недель |
Время цикла | От секунд до минут, в зависимости от механизма |
Стоимость установки | $-$$$$ |
Стоимость за деталь | $-$$$ |
Объем | 903 49 Любой объем
Большинство термопластов можно использовать для термоформование, обеспечивающее гибкость в выборе материала.
Пластмассы, обычно используемые для термоформования, включают:
- Акрил (ПММА)
- Акрилонитрилбутадиенстирол (АБС)
- Полиэтилентерефталатгликоль (PETG)
- Полистирол (ПС)
- Поликарбонат (ПК)
- Полипропилен (ПП)
- Полиэтилен (ПЭ)
- Поливинилхлорид (ПВХ)
Загрузите наш технический документ, чтобы узнать, как быстро создавать сложные формы с помощью 3D-печати, и узнать о советах и рекомендациях, которым вы должны следовать при подготовке деталей формы.
Литье под давлением (IM) работает путем впрыскивания расплавленного термопластика в форму. Это наиболее широко используемый процесс для массового производства пластиковых деталей.
- Настройка пресс-формы: Если в детали есть вставки, они добавляются вручную или с помощью робота. Форма закрывается гидравлическим прессом.
- Экструзия пластика: Небольшие пластиковые гранулы расплавляются и выдавливаются через нагретую камеру с помощью шнека.
- Литье: Расплавленный пластик впрыскивается в форму.
- Охлаждение и освобождение: Деталь охлаждается в форме до тех пор, пока она не станет достаточно твердой, чтобы ее можно было вытолкнуть механически или с помощью сжатого воздуха.
- Постобработка: Литники, направляющие и любой заусенец (если применимо) удаляются из детали, часто автоматически при открытии пресс-формы.
Пресс-формы для литья под давлением очень сложны и должны быть изготовлены с жесткими допусками для производства высококачественных деталей. Из-за высокой температуры и давления эти формы изготавливаются из металлов, таких как закаленная сталь. Более мягкие алюминиевые формы дешевле, но и изнашиваются быстрее, поэтому обычно используются для более умеренных производственных циклов.
Литье под давлением можно использовать для изготовления очень сложных деталей, но некоторые геометрические формы значительно увеличат стоимость. Следование рекомендациям по проектированию для производства (DFM) поможет снизить расходы на инструменты. Создание новых пресс-форм для литья под давлением может занять месяцы, а их стоимость может исчисляться пяти- или шестизначными числами.
Несмотря на высокие первоначальные затраты и медленное наращивание производства, литье под давлением не подходит для крупносерийного производства. После того, как инструмент настроен и запущен, время цикла занимает всего несколько секунд, и миллионы высококачественных деталей могут быть изготовлены за долю стоимости всех других производственных процессов.
Литье под давлением | |
---|---|
Форма | Степень свободы от умеренной до высокой |
Время выполнения | 2-4 месяца |
Время цикла | Секунды |
Настройка стоимость | $$$$$ |
Стоимость за деталь | $ |
81 |
Для литья под давлением можно использовать практически любой тип термопласта. Аналогичный способ известного реакционного литья под давлением (RIM) используется для изготовления деталей из термореактивных пластмасс.
Пластмассы, обычно используемые в литье под давлением, включают:
- Акрил (ПММА)
- Акрилонитрилбутадиенстирол (АБС)
- Полиамид (ПА)
- Полиэтилентерефталатгликоль (PETG)
- Полистирол (ПС)
- Поликарбонат (ПК)
- Полипропилен (ПП)
- Полиэтилен (ПЭ)
- Поливинилхлорид (ПВХ)
Загрузите наш технический документ с рекомендациями по использованию 3D-печатных форм в процессе литья под давлением для снижения затрат и времени выполнения заказов, а также ознакомьтесь с реальными примерами использования приложений Braskem, Holimaker и Novus.
Экструзионное литье работает путем проталкивания пластика через матрицу. Форма штампа представляет собой поперечное сечение конечной детали.
- Экструзия пластика: Пластик нагревается и проталкивается через нагретую камеру с помощью шнека.
- Литье: Пластик продавливается через штамп, который создает окончательную форму детали.
- Охлаждение: Экструдированный пластик охлаждается.
- Нарезка или катушка: Непрерывная форма наматывается или разрезается на куски.
Экструзионное оборудование относительно дешево по сравнению с другими промышленными машинами, такими как ЧПУ или литьевое формование, поскольку оно менее сложное и не требует такого высокого уровня точности машины. Из-за простой формы штампы также менее дороги, а стоимость инструментов составляет небольшую долю от форм для литья под давлением.
Как и литье под давлением, экструзионное литье представляет собой почти непрерывный процесс, благодаря которому цена экструдированных деталей становится очень низкой.
Формы и формы, которые могут быть изготовлены с помощью экструзии, ограничиваются изделиями, которые имеют непрерывные профили, такие как тавровые, двутавровые, L-образные, U-образные сечения, а также квадратные или круглые сечения. Типичные области применения включают трубы, шланги, соломинки и молдинги оконных рам.
Экструзия | |
---|---|
Форма | Ограничено, только длинные непрерывные формы |
Время выполнения заказа | Недели |
Время цикла | Секунда с (или непрерывно) |
Стоимость установки | $$$ |
Стоимость на часть | $ |
Том | Средние и высокие применения (1000+ частей) |
Практически любой тип термопластичного экстрах0003
- Акрил (ПММА)
- Акрилонитрилбутадиенстирол (АБС)
- Полиамид (ПА)
- Полиэтилентерефталатгликоль (PETG)
- Полистирол (ПС)
- Поликарбонат (ПК)
- Полипропилен (ПП)
- Полиэтилен (ПЭ)
- Поливинилхлорид (ПВХ)
Выдувное формование — это производственная технология, используемая для создания полых пластиковых деталей путем раздувания нагретой пластиковой трубки внутри формы до тех пор, пока она не примет желаемую форму.
- Установка пресс-формы: Небольшие пластиковые гранулы расплавляются и формируются в полую трубку, называемую заготовкой или заготовкой (в зависимости от подтипа выдувного формования).
- Формовка: Заготовка зажимается в форме и надувается сжатым воздухом до тех пор, пока не примет форму внутренней части формы.
- Охлаждение и высвобождение: Деталь охлаждается в форме до тех пор, пока она не станет достаточно твердой, чтобы ее можно было извлечь.
Выдувное формование работает при гораздо более низком давлении, чем литье под давлением, что способствует более низкой стоимости оснастки. Подобно литью под давлением и экструзии, выдувное формование представляет собой непрерывный процесс, который может быть полностью автоматизирован, что приводит к высокой производительности и низкой стоимости единицы продукции.
Выдувное формование является наиболее распространенным процессом изготовления полых пластиковых изделий в больших масштабах. Типичные области применения включают изготовление бутылок, игрушек, автомобильных компонентов, промышленных деталей и упаковки.
Выдувное формование | |
---|---|
Форма | Ограниченная свобода, только полые тонкостенные формы, без сложной геометрии | 90 343
Время выполнения заказа | Недели |
Время цикла | Секунды |
Стоимость установки | $$$$ |
Стоимость за деталь | $ |
Объем | Приложения с большим объемом ( 5000+ деталей) |
Выдувное формование можно выполнять с различные термопластические материалы, наиболее распространенными примерами которых являются:
- полиэтилентерефталат (ПЭТ)
- Полипропилен (ПП)
- Поливинилхлорид (ПВХ)
- Полистирол (ПС)
- Поликарбонат (ПК)
- Акрилонитрилбутадиенстирол (АБС)
Процессы производства пластмасс постоянно развиваются, и точки перегиба, когда имеет смысл переходить от одной технологии к другой, смещаются благодаря совершенствованию оборудования, материалов и экономии за счет масштаба.