Литье в форму: изготовление, песчаные, оболочковые формы
Технология литья в форму, или матрицу, основана на физическом свойстве жидкости затекать в твердые емкости, заполняя все их уголки. После этого жидкость застывает и образует твердую отливку, повторяющую все детали поверхности матрицы.


Методом литья получают самые разнообразные изделия из металлов, для этого их предварительно нагревают, доводя до температуры плавления и перехода в жидкое состояние. Этот способ обработки металлов был освоен человечеством в IV-III тысячелетии до н.э. Температура плавления самых применяемых человеком металлов — от 213 °C у олова до 1538 °C у железа.
Кроме металлов, путем литья получают изделия из различных пластмасс. Их температура плавления намного ниже — в диапазоне 200-300 °C.
Также литьем получают изделия из смесей неметаллических веществ, химически отвердевающих при комнатной температуре — это смолы и пластмассы, гипс и цемент.
Основные виды литья в формы
Виды литья делятся по различным признакам.
По возможности повторного использования различают однократные (песчаные, оболочковые, выплавляемые модели, газифицируемые модели) и многократные формы — кокили, цементные, графитовые и асбестовые. Однократная разбивается, чтобы извлечь изделие. Многократные бывают разборные и неразборные, и обеспечивают повторное литье в форму от десятков до тысяч раз.
- Однократные формы
- Многократные формы
Традиционные методы литья, освоенные человечеством еще в древности — в песчаные формы и в кокиль.
Прогрессивные виды технологии, разработанные в прошлом веке и завоевавшие популярность сегодня:
- в оболочковые формы;
- по выплавляемым моделям;
- центробежное;
- под давлением;
- по газифицируемым моделям;
Литьё в оболочковые формы
Для литья металлов данным способом готовят состав из песка и порошкообразного связующего, чаще всего фенолформальдегидных смол.
Модель, или макет нагревают до 300 °C и обсыпают подготовленной смесью. За короткое время (около минуты) на поверхности макета запекается упрочненный слой. Излишки смеси убирают.
Иногда плакированную смесь задувают в промежуток между разогретой моделью и фигурной опокой. Следующий этап — обжиг при температуре 650 °C для окончательного набора прочности. После извлечения макета половинки матрицы соединяют вместе – и она готова к отливке. Для того чтобы матрица не деформировалась весом поступающего в нее расплава, ее окружают металлическим ящиком, который заполняют дробью. Дробь улучшает также и график остывания изделия.


Литьё в оболочковые формы
Основные преимущества метода:
- существенное снижение трудоемкости и времени подготовки формы по сравнению с литьем в землю
- контроль режима остывания изделия
- процесс поддается механизации
Данный вид заливки пригоден для изделий весом до 30 кг.
Литьё по выплавляемым моделям
Выплавляемые модели – пожалуй, самый дорогостоящий и трудоемкий вид литья металлов.
Его используют для особо ответственных видов изделий высокой точности — таких, например, как турбинные лопатки. Точный макет будущей детали выполняется из вещества с низкой температурой плавления, такого, как воск. В производстве используется смесь парафин-стеарин в равных частях. Для более крупных видов изделий в состав добавляют соли, препятствующие короблению макета. Потом путем погружения макет покрывают 5-12 слоями специальной жаростойкой суспензии. В качестве основы берут гидролизованные силикаты, жаростойкой обсыпкой являются зерна электрокорунда или кварца.


Отливки по выплавляемым моделям
Для сушки применяют шкафы, наполненные аммиачным газом. Далее форму нагревают, чтобы из нее вытек парафин. Остатки состава удаляют паром, подаваемым под высоким напором. Следующая фаза подготовки — прокаливание при температуре около 100 °C. Эту операцию проводят для избавления от остатков, способных к газификации. Заливка осуществляется в подогретые до 1000 °C матрицы. После охлаждения изделия по заданному графику в термостате, матрицу разбирают и достают деталь.
Основное преимущество этого вида заливки — высокая точность соблюдения размеров и качество поверхности.
Другие преимущества
- возможно изготовление продукции из сплавов, плохо поддающихся механической обработке
- Можно отливать детали, которые другими видами литья пришлось бы лить по частям и впоследствии соединять в единый узел
Недостатки – низкий коэффициент использования металла и чрезвычайно высокая трудоемкость.
Литье по газифицируемым моделям
Представляет собой развитие вида заливки в песчаные формы с применением ручной или машинной формовки. Суть данного вида в том, что макет делают не из дерева, а из легкоплавкого пластика, чаще всего вспененного полистирола.


Литье по газифицируемым моделям
Модель размещают в опоке, после чего проводят послойную формовку песчано-глиняной смесью с уплотнением. В верхней части формы создают литниковую систему. Расплав заливают прямо поверх модели, полистирол плавится и газифицируется, выходя через формовочные массы вместе с другими литьевыми газами.
Преимущества этого вида заливки:
- трудоемкость подготовки форм снижается многократно
- можно моделировать и отливать за один раз детали любой, даже самой сложной формы
- не нужны составные макеты и сложные составные формы.
- Доступны большие серии изделий — в этом случае макеты также отливаются.
ЛГМ-это современный вид литья, приобретающий все большую популярность среди металлургов.
Литье под давлением
Отличается от традиционного вида заливки тем, что расплав поступает в форму не под действием гравитации, а под влиянием избыточного давления, создаваемого в отливочной камере напором газа или поршнем. Тигель с расплавом, система его нагрева, формы и металлопровод помещены в герметичную камеру и представляют собой единый механизированный и автоматизированный комплекс.


Литье под давлением
По достижении требуемой температуры расплава в тигель опускается металлопровод, выполненный из тугоплавкого титанового сплава, и в камеру подается напор воздуха. Под его воздействием расплав поднимается в матрицу и заполняет ее. Автоматика поддерживает постоянное давление в камере, поскольку объем ее увеличивается по мере расходования металла. Далее вентиляционные насосы откачивают литьевые газы в систему очистки воздуха. При этом виде заливка проводится как в одноразовые песчаные формы, включая газифицируемые модели, так и в многократные: кокили, цементные, графитовые и асбестовые. По окончании заполнения формы остаток металла стекает из металлопровода обратно в тигель.
Преимущества метода
- Высокая степень автоматизации литейных операций
- Исключение ручного труда во вредных условиях
- Экологичность
- Высокий коэффициент использования металла.
Недостатки
- Сложность оборудования
- Размер отливки ограничен размером герметичной камеры.
Данный вид популярен в цветной металлургии для крупных партий небольших и средних деталей.
Центробежное литье
Используется при производстве изделий, имеющих форму вращения — втулок, шестерен и т.п. Литье проводится в металлическую матрицу, вращающуюся с большой скоростью.


Центробежное литье
Центробежная сила прижимает жидкий металл к внешней стенке, где он и кристаллизуется. Метод позволяет получить исключительно однородные отливки. Возможно создание и многослойных деталей. Слои заливаются один за другим.
Достоинства и недостатки литья в форму
Отливка в форму, как и любая технология, имеет свои плюсы и минусы.
Плюсы:
- Точное повторение геометрии макета
- Производство изделий самой замысловатой геометрии
- Возможность изготовления большого количества идентичных деталей
- Низкая себестоимость продукции
Недостатки:
- Высокая трудоемкость
- Тяжелые условия труда и вред для экологии
- Сложность автоматизации процессов, особенно подготовки сложных форм
- Неоднородность состава и плотности материала отливок.
Современные виды литья во многом снимают эти недостатки. Так, использование ЛГМ многократно снижает трудоемкость подготовки, литье под давлением повышает однородность изделий и автоматизирует процессы во вредных условиях труда, центробежное и интрузионное литье позволяет получить абсолютно однородные отливки. Металлурги постоянно разрабатывают новые разновидности известных методов литья и изобретают принципиально новые его виды.
как создать форму для отливки за неделю / Блог компании iQB Technologies / Хабр
3D-технологии, интегрированные в технологическую цепочку литейного производства, обеспечивают предприятию реальную выгоду. Как показать все преимущества 3D-сканирования и 3D-печати? Нагляднее всего – продемонстрировать процесс создания детали с нуля аддитивными методами и провести сравнение с традиционными технологиями. С этой целью мы обратились к Павлу Чадушкину, ведущему специалисту производственного направления RP-центра компании iQB Technologies.
– Итак, наша задача – создать эталонную деталь на основе цифровой модели для последующей отливки реального изделия. С чего начинается этот процесс, если мы применяем 3D-технологии?
– Прежде всего, нам необходимо исходное изделие, которое нужно отсканировать, а затем выполнить обратное проектирование (реверс-инжиниринг). Конечно, оно должно быть новое, не бывшее в употреблении, чтобы не было износа детали. Мы оцениваем, насколько сложна ее геометрия и после этого задаем только один вопрос: какой должен быть допуск по точности? Уже по внешнему виду можно понять, каким образом эта деталь производится. Чаще всего это литье (высокоточное или в землю), фрезерование или изготовление на токарном станке. У каждой из этих методик производства есть свои допуски.
После того, как мы имеем представление о технологии производства и допуске, мы выбираем оборудование, а именно – 3D-сканер с нужными нам параметрами точности, и производим оцифровку изделия. Например, ручной сканер Creafrom HandyScan 700 или стационарный Solutionix C500. Такие устройства метрологического класса уже хорошо зарекомендовали себя на производственных предприятиях. Получив 3D-модель, мы переносим ее в программное обеспечение Geomagic Design X, позволяющее быстро и легко обработать данные 3D-сканирования с целью выполнения контроля геометрии и реверс-инжиниринга. Затем к работе подключается инженер, который по результатам сканирования обрисовывает эту деталь и создает твердотельную модель.
В процессе обрисовки инженер исключает из твердотельной модели различные недостатки изделия. Здесь нужно подчеркнуть, что абсолютно любое изделие имеет производственные деформации. Они могут быть обусловлены разными факторами – например, неверно подобранным материалом, сложной формой, деформацией во время транспортировки, изношенным инструментом, с помощью которого производилось изделие.
В любом случае, какой бы объект мы ни взяли для 3D-сканирования, он будет содержать дефекты и отклонения от эталона, а наша задача – создать этот самый эталон. Если деталь круглая, то совершенно точно можно сказать, что отверстие в ней будет не круглым, а эллипсовидным. Соответственно, инженер с помощью ПО этот эллипс исключает и создает окружность правильной формы. Таким путем, обрисовывая каждый элемент геометрии, мы исправляем все недостатки. Когда деталь полностью обрисована, у нас получается твердое тело, которое можно запускать в производство.
Отливка перепускного клапана стравливания избыточного давления газа (в разрезе)
– Мы получили CAD-модель. Теперь нужно определить, каким способом производить изделие.
– Традиционный способ – подготовка оснастки для литья восковых моделей на станке с ЧПУ. В этом случае модель должна адаптироваться под станок, со своими допусками, уклонами, скруглениями – все зависит от оборудования и инструментов, с помощью которых деталь будет производиться.
Но теперь есть и второй путь – 3D-печать, которая является идеальным решением для прототипирования и изготовления малых серий.
Ключевое преимущество аддитивных технологий – возможность создавать изделия максимально сложной формы (в том числе с мельчайшими деталями), которые нельзя произвести традиционными методами. Кроме того, при запуске печати необязательно учитывать сложность геометрии. Это особенно актуально для производства изделий путем металлического и пластикового литья.
Если изделие имеет простую форму, то зачастую целесообразнее его производить на станке с ЧПУ. Если же геометрия сложная, то 3D-печать – оптимальный вариант.
Когда нам нужен не один рабочий прототип, а малая серия – от 10 до 1000 изделий, используется литье в силикон, или двухкомпонентное литье. Для этого нужно получить мастер-модель – эталон, по которому будет создаваться силиконовая форма, в которую затем заливается пластик или воск.
– Мы выяснили, что 3D-печать – незаменимое решение при производстве продукции с использованием металлического и пластикового литья. Можете привести пример создания конкретной детали?
– Возьмем корпус обыкновенного телефона из пластика. Во-первых, он делится на две половины, нижнюю и верхнюю. Чтобы произвести одну из половин, надо сделать матрицу и пуансон – это оснастка для литья пластика под давлением. Металлическая форма, состоящая из двух половин, смыкается, затем в нее под давлением подается пластик, который принимает форму внутренней геометрии изделия.
При традиционном производстве на станке с ЧПУ вытачивают внешнюю и внутреннюю форму каждой половины. Но если у нас есть 3D-принтер, мы печатаем сразу готовое изделие целиком, металлическую оснастку делать не нужно. Мало того что ее долго изготавливать, она будет баснословно дорогая для тиража в десять штук. Таким образом, выгода 3D-печати очевидна – отпадает необходимость фрезерования для получения оснастки.
Телефон – продукт массового производства, и речь идет не о десяти, а о тысячах изделий. Как раз в этом случае нужны матрица и пуансон, и постоянная штамповка большого тиража. Кроме того, если понадобится внести какое-то небольшое изменение в конструкцию, мы можем оперативно исправить CAD-модель, сразу напечатать прототип и проверить его на собираемость, посмотреть, правильно ли мы разработали геометрию.
– При создании выплавляемых и выжигаемых мастер-моделей для литья с помощью 3D-принтера используется, соответственно, воск и фотополимер (технология печати MJP, технология литья QuickCast). Как выглядит производственная цепочка с использованием этих материалов и в чем их различия?
– Использование напечатанных на 3D-принтере выплавляемых восковых и выжигаемых фотополимерных моделей имеет одну и ту же механику, немного различаются алгоритмы действия.
У нас есть напечатанная восковая модель. Мы создаем для нее корку (то есть форму, в которую заливается металл), обмазывая мелкодисперсным порошком толщиной не менее 6-8 мм. Вид материала и толщина корки зависит не только от сложности геометрии и габаритов изделия, но и от металла, который будет литься в будущую форму. Затем деталь помещается в печь. В печи воск выплавляется, а сама корка отвердевает, и у нас получается твердая форма для литья металла.
Восковая и фотополимерная модели перепускного клапана, напечатанные на 3D-принтерах
Что касается выжигаемого фотополимера, то мы так же кладем изделие в печь, но если воск вытапливается при температуре +200⁰С градусов, то фотополимер – при +950⁰С. Корка так же затвердевает, а материал, из которого была создана модель, выгорает.
Далее в получившуюся форму заливается раскаленный металл – это может быть и алюминий, и титан, и даже магний. Форма остывает, после чего корка разбивается молотком или вибромашиной, и мы получаем отливку.
Следующий этап – мехобработка. Она заключается в том, чтобы сделать поверхность детали более гладкой – обрезать литники, по которым заливался металл, зашлифовать их, снять излишнюю шероховатость изделия. На этой стадии нам также может потребоваться сверление отверстия или подгонка крепежных элементов – для этого применяются станки с ЧПУ для финальной обработки изделия до его конечного варианта (шлифовальные, пескоструйные, сверлильные и т.д.).
– От чего зависит выбор воска или фотополимера?
– Восковые машины относительно дешевы, при этом расходный материал – дорогой. С фотополимерными 3D-принтерами ситуация обратная. В сравнении с фотополимером воск достаточно хрупкий материал, это его недостаток. Но на сегодня восковая 3D-печать обеспечивает самую точную и самую гладкую поверхность. К тому же, восковое литье является традиционным для всех литейных производств в России. Соответственно, фотополимер подойдет там, где нужны модели большего размера, а прочность и детализация менее критичны. Пользователь должен сделать выбор, исходя из того, какие объемы он будет печатать, насколько часто он будет обращаться к прототипированию.
Так, на литейных предприятиях по всему миру, в России в том числе, активно используются профессиональные 3D-принтеры от 3D Systems, ведущего мирового производителя аддитивных установок. При этом ряд компаний имеют свой парк 3D-оборудования, другие заказывают услуги 3D-печати у подрядчиков.
– Мы подробно рассмотрели, как и в каких случаях выгодно использовать 3D-принтеры и 3D-сканеры. Если резюмировать: почему литейному предприятию необходимо внедрять аддитивные технологии?
– Для сокращения сроков производства при изготовлении опытных образцов и деталей малого тиража. Мы экономим и время, и деньги.
Вернемся к сравнению традиционного процесса с аддитивным. В первом случае это выглядит следующим образом:
1. Конструктор разрабатывает деталь, затем передает свою разработку инженеру.
2. Инженер адаптирует ее под методику производства вместе с технологом.
3. Дальнейшая адаптация заключается в том, что создается чертеж будущей формы матрицы и пуансона или чертеж, по которому деталь будет вытачиваться на фрезеровочном станке.
4. Затем на станке изготавливают матрицу и пуансон и отдают их на производство.
Так вот, с момента выдачи конструктором готового проекта инженеру и до получения формы, по которой будет отливаться изделие, проходит от полугода до года. И прошло, допустим, полгода, сделали десять опытных образцов, отдали их конструктору, он примерил эти металлические болванки, а они не совпадают с посадочными местами. Он понимает, почему они не совпадают, дорабатывает эту модель, и дальше цикл повторяется. Проходит еще минимум полгода до следующей примерки.
С помощью 3D-принтера конструктор фактически нажатием одной кнопки отправляет на печать свое изделие и отдает его сразу на производство в отливку. Срок сокращается с года или полугода до недели максимум. Это самое главное преимущество. Плюс, мы экономим значительные средства на изготовление формы. И, наконец, мы имеем возможность создавать изделия с геометрией любой сложности и, при необходимости, быстро оптимизировать конструкцию в программном обеспечении.
Как сделать форму для литья
Изготовление литейных форм, на фрезерном станке Roland Modela
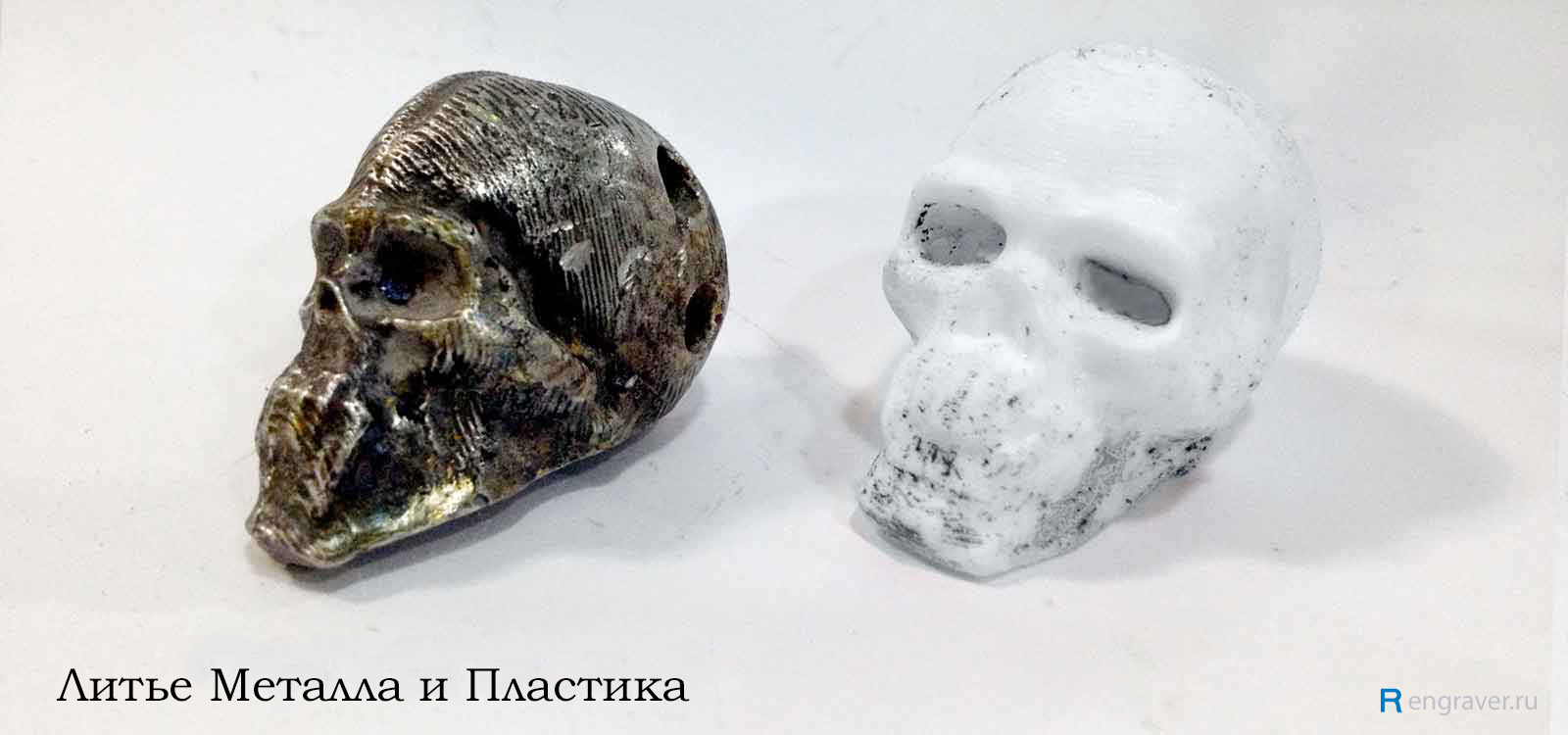
Студент ФабЛаба рассказывает, как она сделала форму для литья на фрезерном станке Roland Modela, и отлила в форму металл и пластик.
Задача: Разработать произвольную фигурку или изделие, которое мы могли бы повторить несколько раз, сделав для него форму для литья.
Я решила скачать модель фигуры с Thingiverse и по-своему персонализировать её в Rhinoceros. Мне хотелось попробовать поработать с твёрдыми материалами такими как металл или жесткий пластик, поэтому сама форма для литья должна была быть мягкой. Контрформу мы делали из воска для моделирования с помощью фрезерного станка Roland Modela, а для самой формы мы использовали термостойкий силикон.
Скачать файл модели формы можно здесь:
Rhino 3D модель Формы для литья [.3dm]
Общие рекомендации при изготовлении формы и контрформы:
1) Рассчитайте диаметр используемой фрезы. Убедитесь, что вы оставляете достаточно места между вашим изделием и стенкой контрформы.
2) Оставьте отверстие достаточного размера для заливания материала, а также дополнительное вентиляционное отверстия для выхода воздуха.
3) Стенки контрформы должны быть немного наклонены.
4) Если вы делаете форму из двух частей, не забудьте сделать шипы и пазы для точного соединения половинок.
5) Помните, что для отливки твердых изделий нужны мягкие формы.
6) Обратите внимание на соотношение смешиваемых материалов отливки.
Процесс изготовления
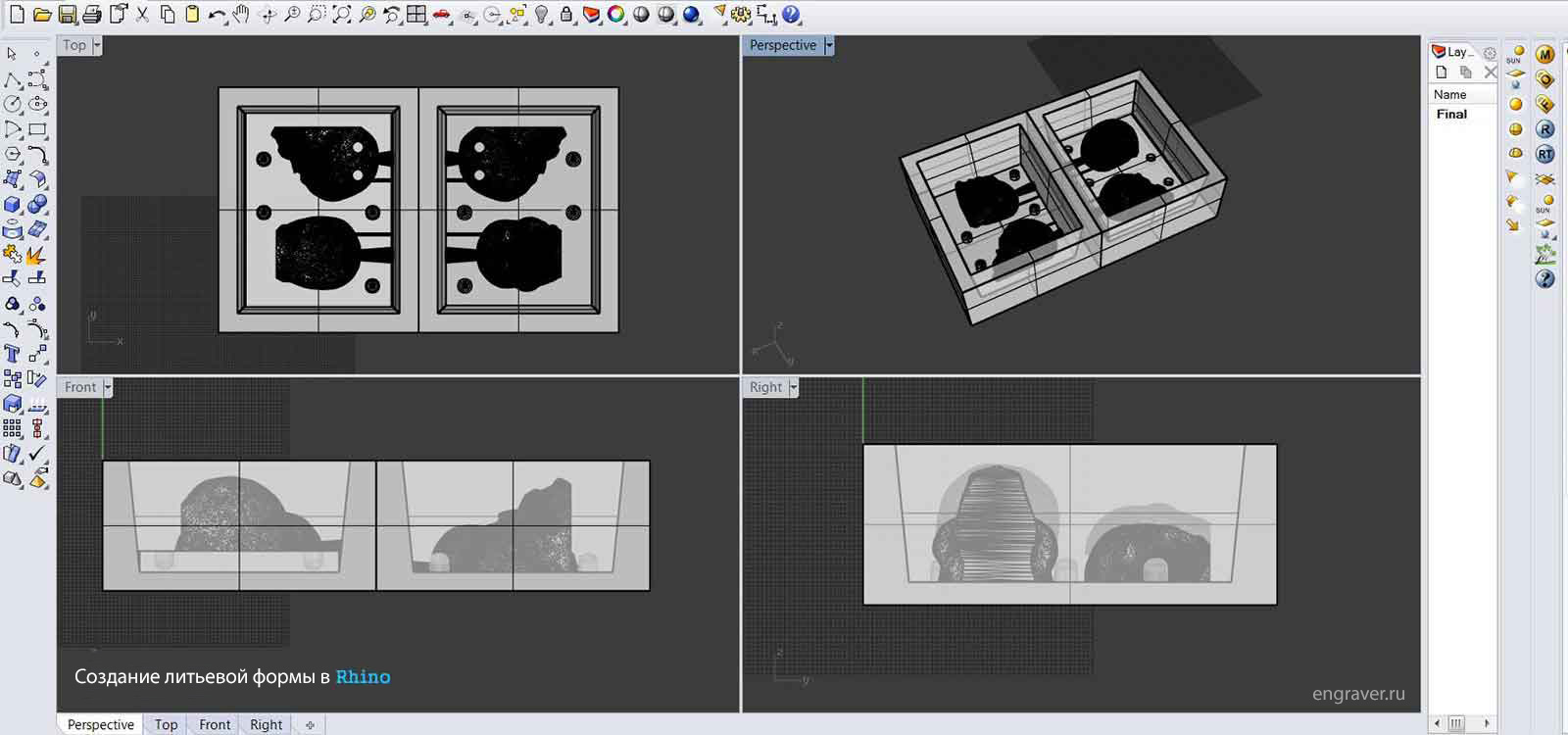
Изменить форму черепа я пробовала двумя разными способами, чтобы получить двустороннюю форму для отливки. Так как отливать я буду из металла, и изделие будет твердым, то сама форма должна быть мягкой. Я подготовила 3D-модель контрформы в Rhinoceros, которую буду вырезать из бруска воска для моделирования размером 7,0 X 14,1 X 3,5 см. Также я учла и оставила необходимые отверстия для заливки металла и вентиляционные отверстия.
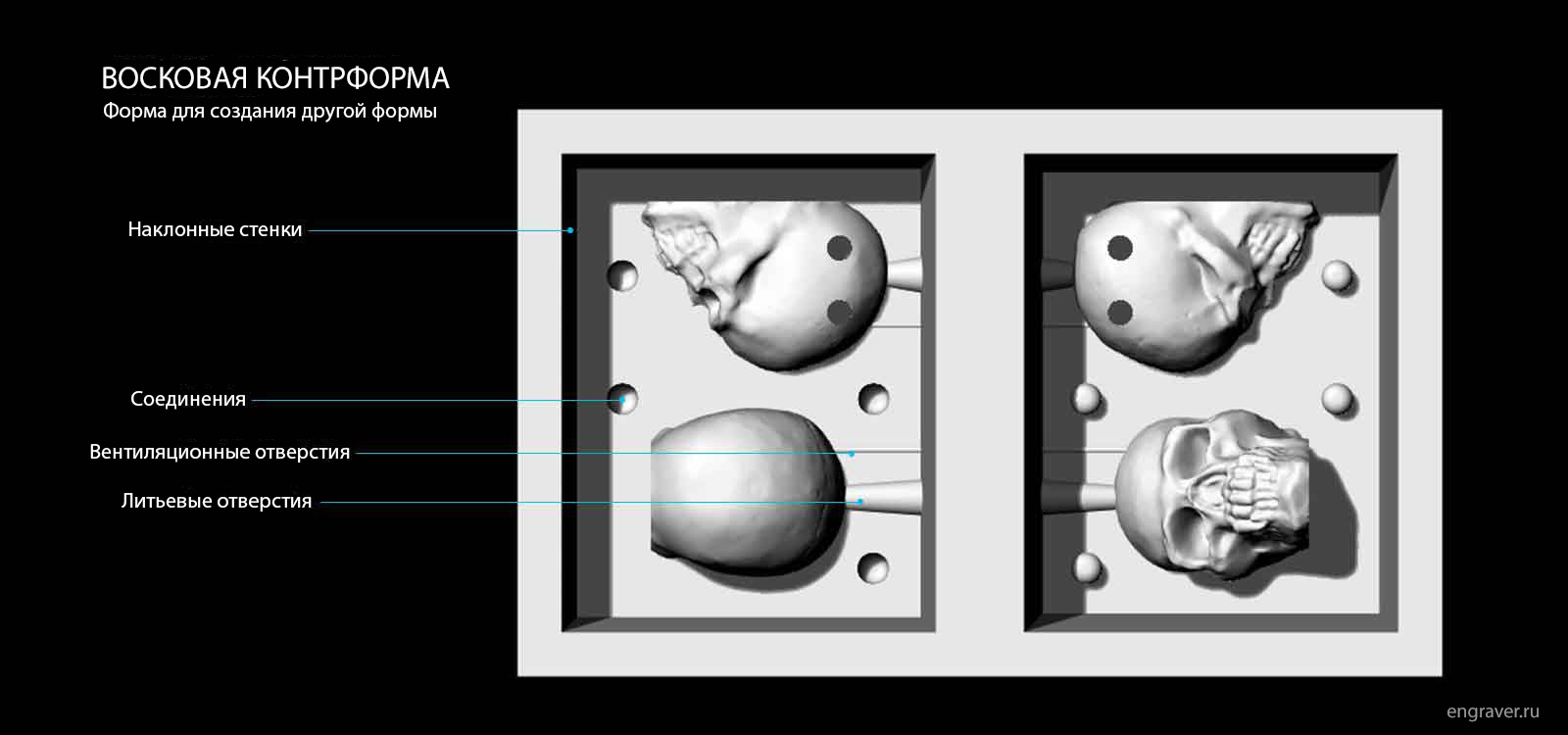
После того, как я закончила делать 3D-модель, я стала вырезать из бруска модельного воска контрформу, на фрезерном станке Roland Modela. Для черновой обработки я использовала концевую 2-зубую фрезу диаметром 3 мм, для чистовой — сферическую фрезу диаметром 1,5 мм. Я прошлась по чистовой только в одном направлении (ху), так как на мой взгляд и этого было вполне достаточно, и дополнительная обработка была ни к чему, а время — сэкономилось. На черновую и чистовую обработку в общей сложности ушло примерно 3 часа и 20 минут.
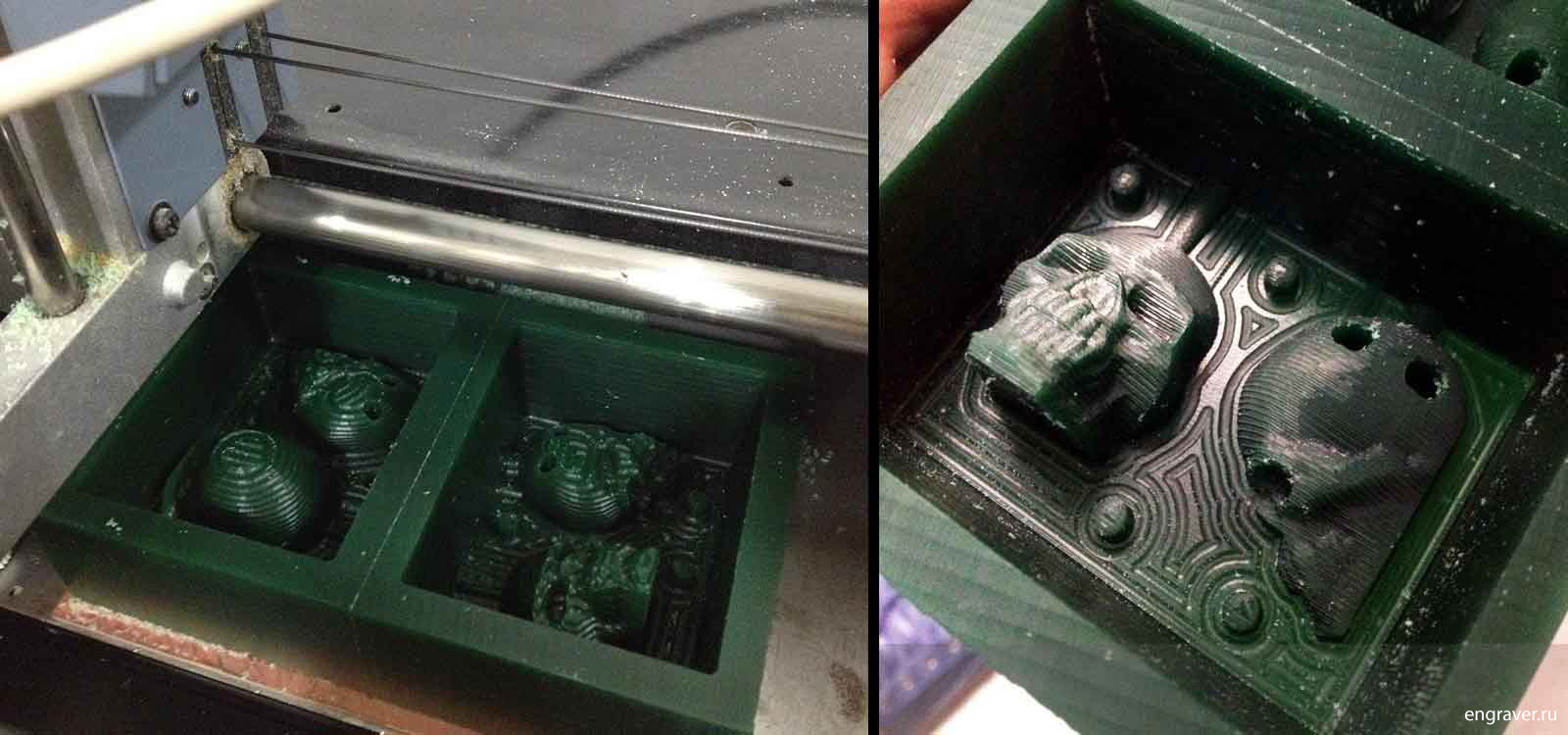
Когда контрформа была вырезана, я начала делать собственно саму форму из термостойкого силикона. Как я упоминала ранее, форма должна была быть не только мягкой, но и очень термостойкой, поэтому я использовала силикон повышенной термостойкости Mold MAX® 60.
Порядок действий изготовления нашей формы для литья:
1) Нанести некоторое количество универсальной разделительной смазки-спрея и дать ей подсохнуть в течение 3 минут.
2) Сделать смесь для силикона: компоненты A и B смешиваются в массовой пропорции 100A:3B (или согласно инструкции к тому силикону, который вы используете).
3) Вылить смесь в контрформу, убедившись, что внутрь не попали пузырьки воздуха.
4) На всякий случай тщательно простучать форму, пока все пузырьки воздуха не выйдут на поверхность.
5) Дать силикону застыть в течение суток.

К сожалению, в моём случае получилось так, что через сутки силикон был всё ещё незастывшим. Оказалось, что весы были испорчены, показывали неверный результат, и я смешала в неправильной пропорции! После очистки контрформы с помощью воды и мыла я постаралась сделать всё правильно.
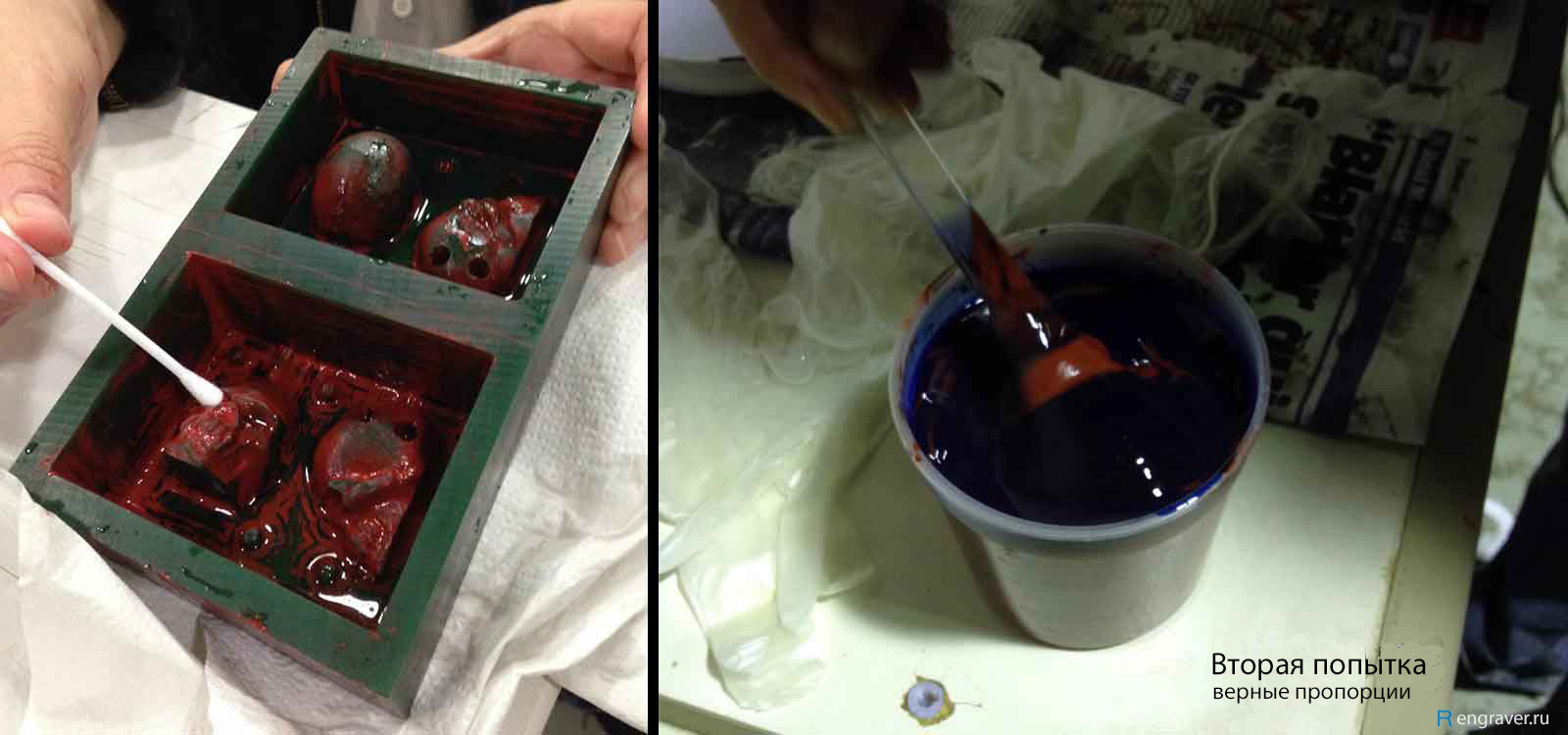
Хоть и со второго раза, но получилось же!
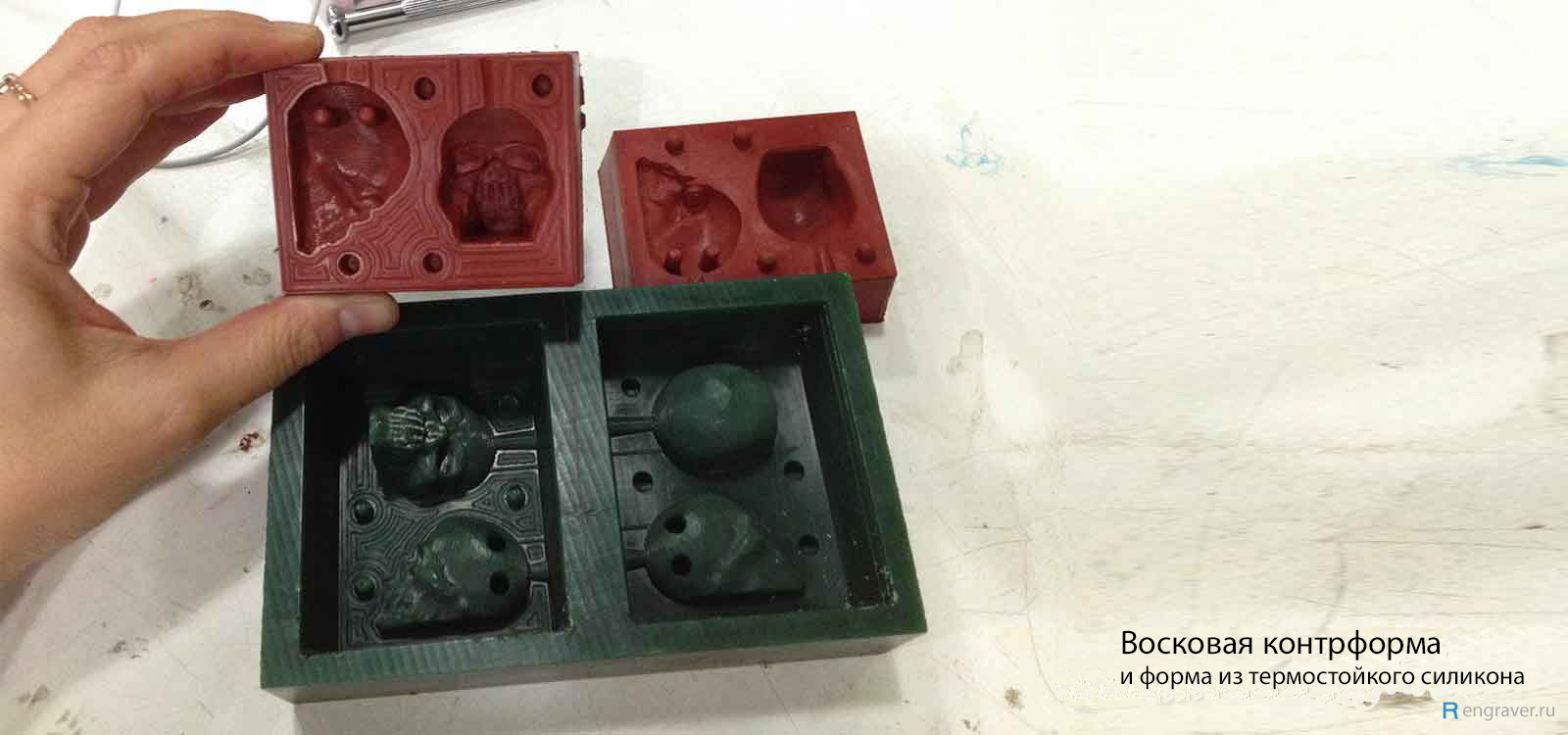
Теперь всё готово к долгожданной отливке.
Для того, чтобы отлить металлические изделия я сделала следующие шаги:
1) Добавить тальк в форму.
2) Нагреть печку или сосуд, в котором будете плавить металл, подождать пока ваши заготовки расплавятся. Соблюдайте технику безопасности и работайте в перчатках!
3) Сложить обе части формы и выровняв сжать их каким-нибудь удобным для вас способом. Части формы должны быть хорошо сжаты, чтобы не допустить протечек.
4) Аккуратно и неспешно залить расплавленный металл.
5) Сразу же окунуть форму в холодную воду для охлаждения. Оставить форму в воде до тех пор, пока она достаточно хорошо не остынет и можно будет её трогать.
6) Снять форму и достать ваше изделие.
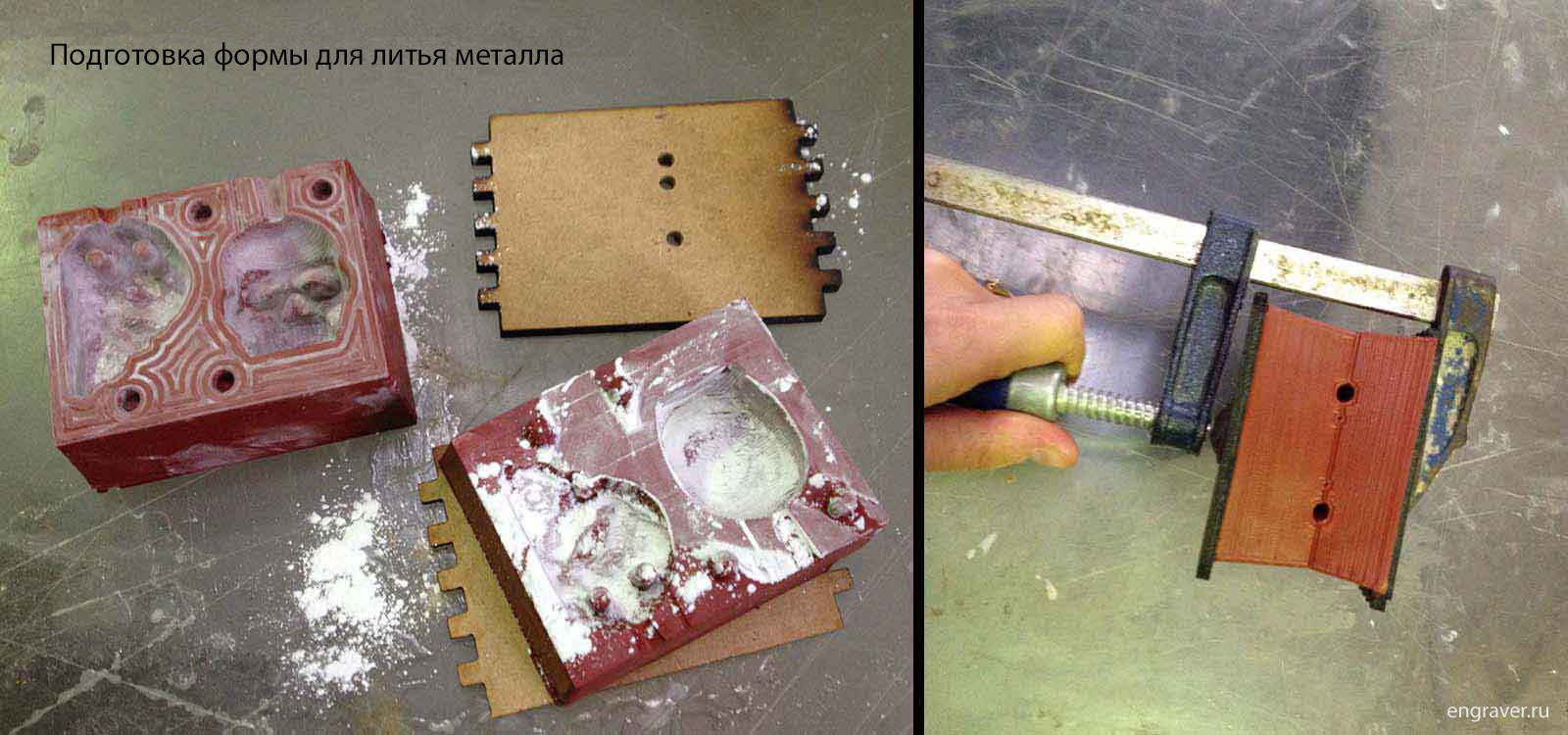
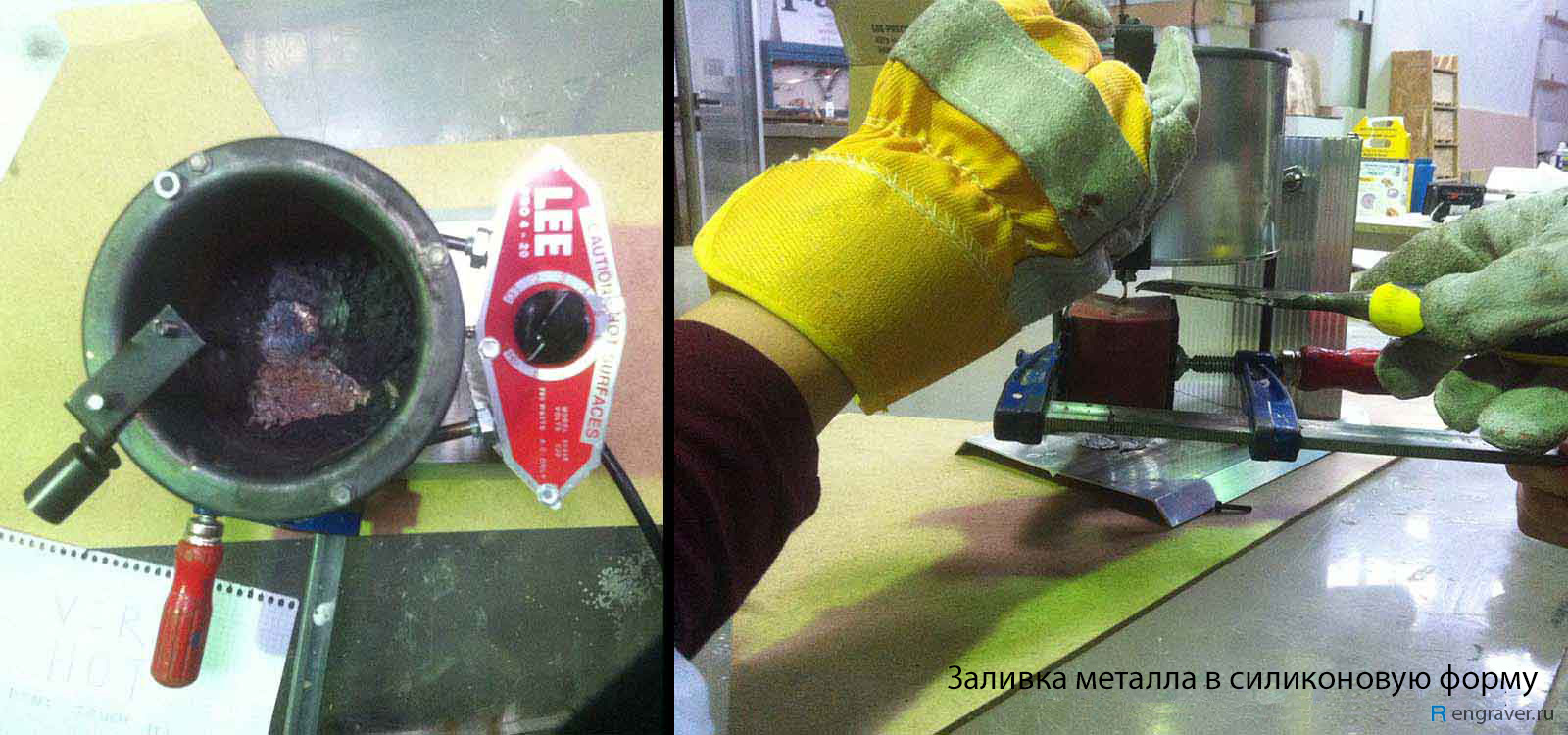
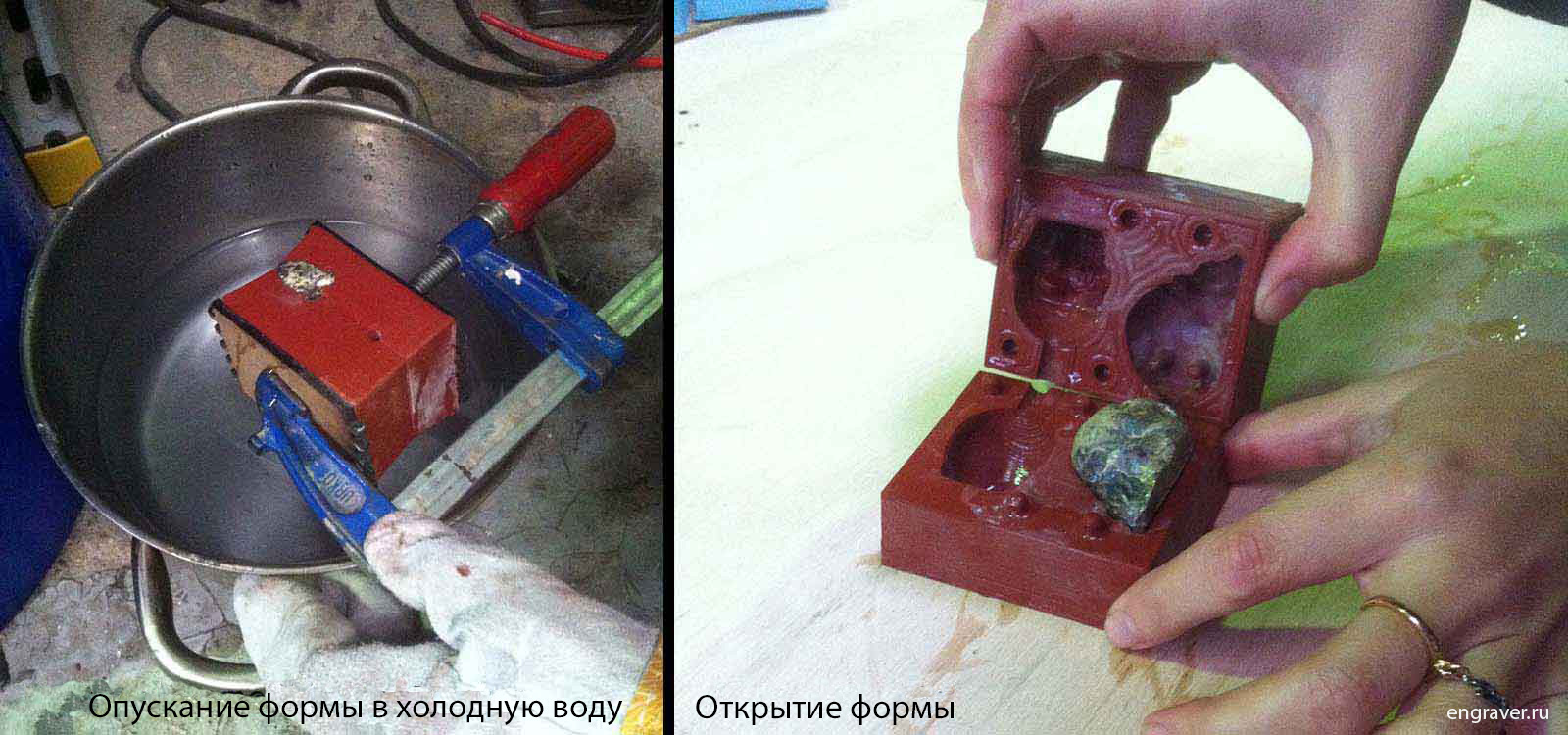
Черепа вышли очень неплохими, с хорошей детализацией. Один из них я отполировала, а второй оставила без обработки (см. рисунки).
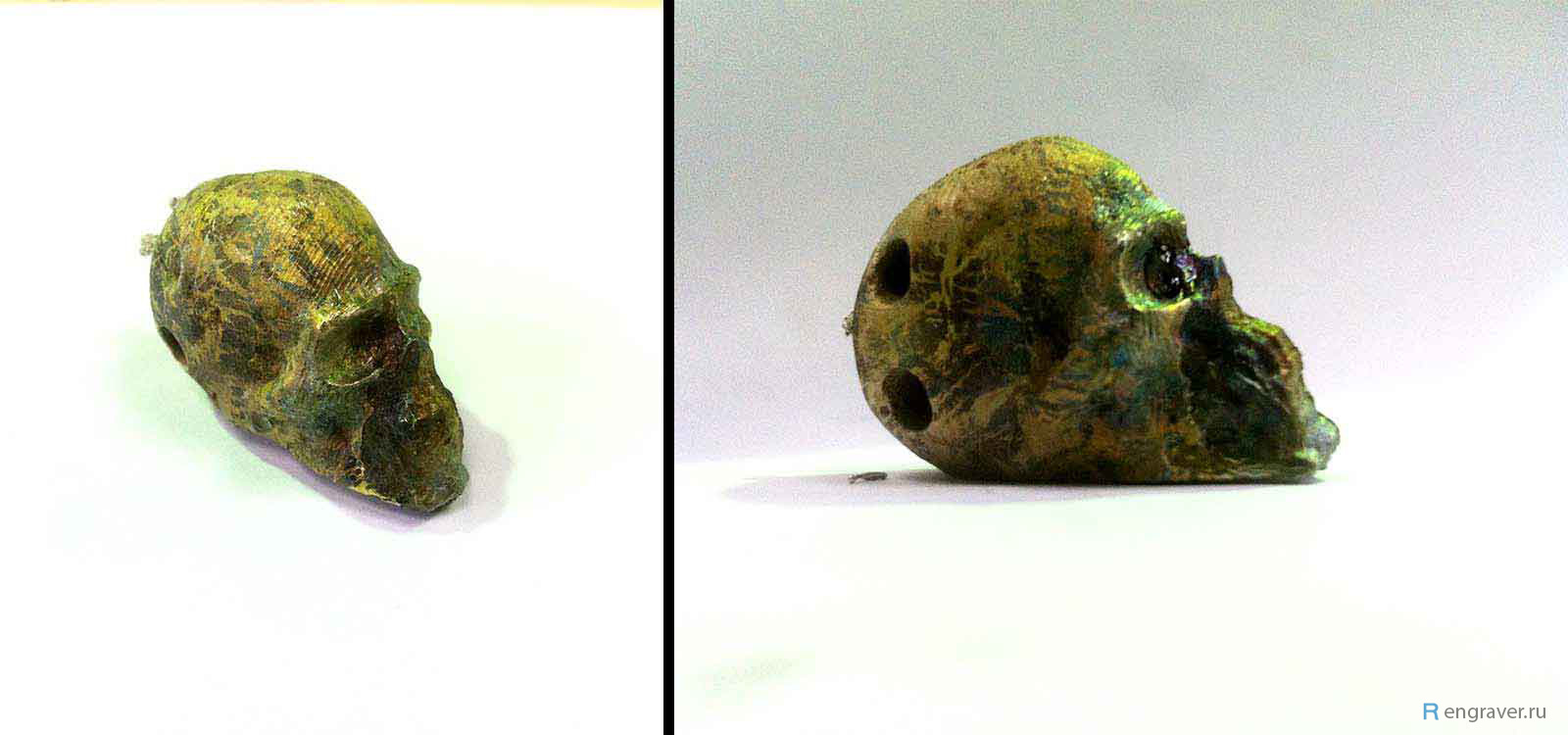
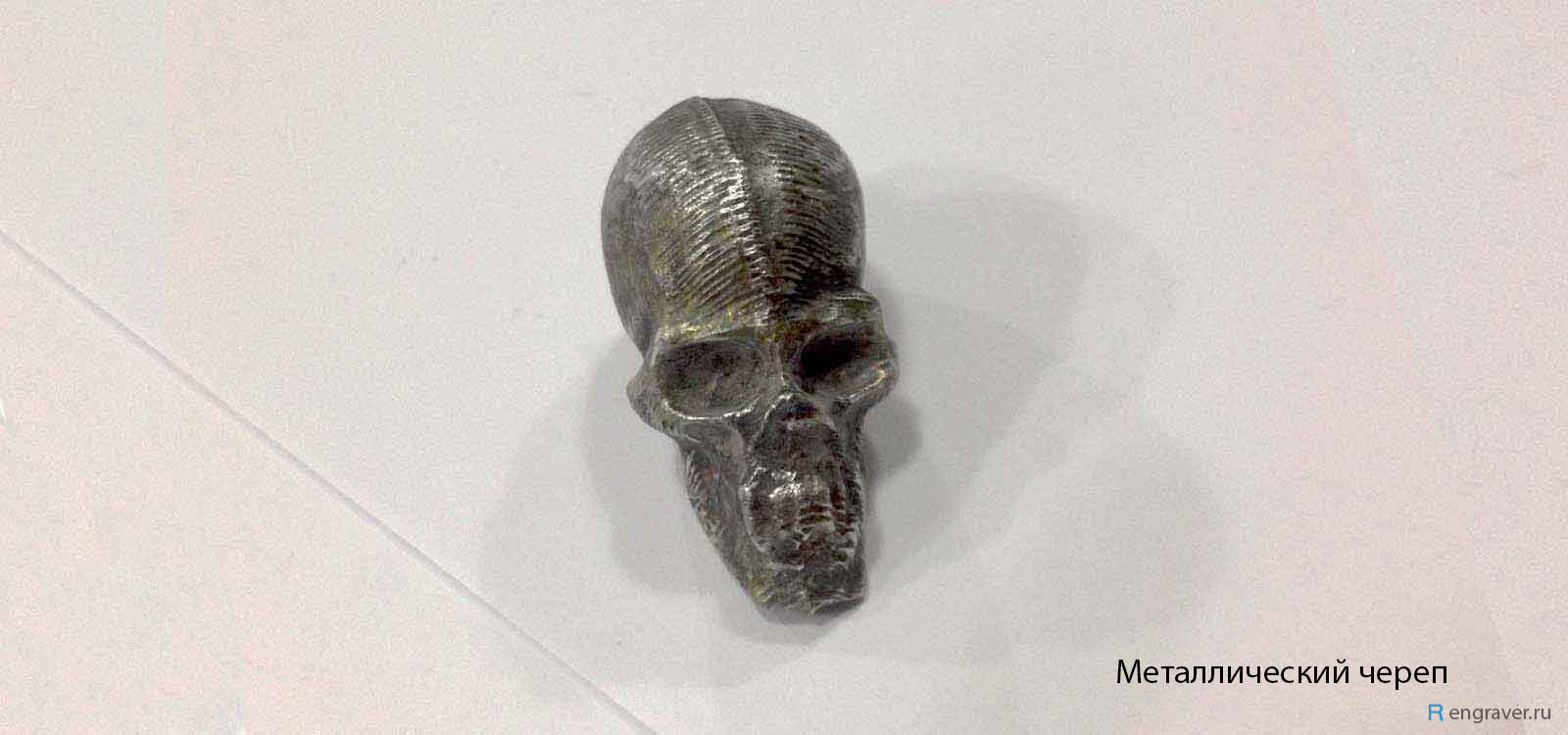
После завершения работ с металлом, я попробовала сделать то же самое из пластика.
Процесс был проще, так как пропорция смеси для материала составляет 1:1.
Также пластиком легче оперировать, он не горячий и отливать из него проще.
Результат на картинке:
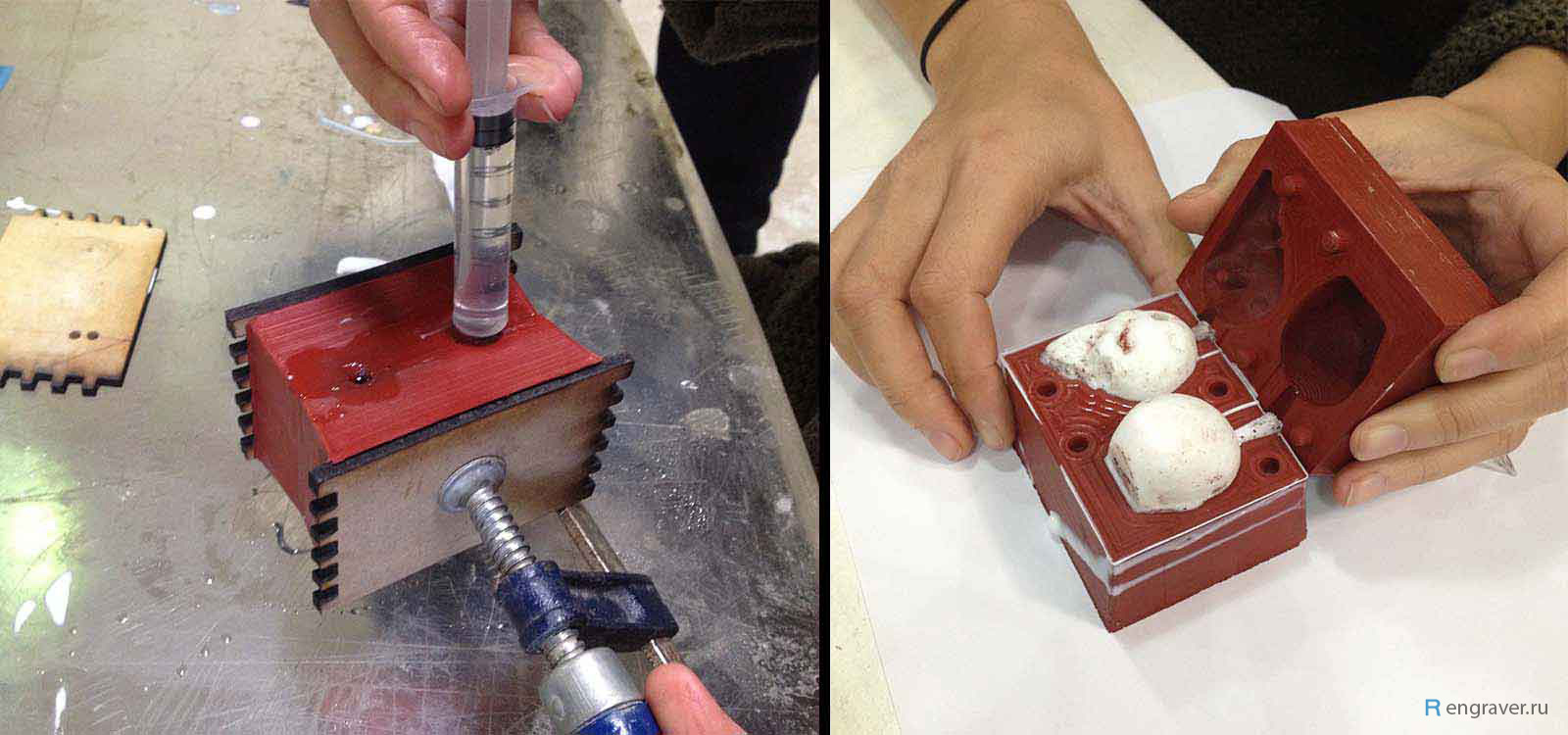
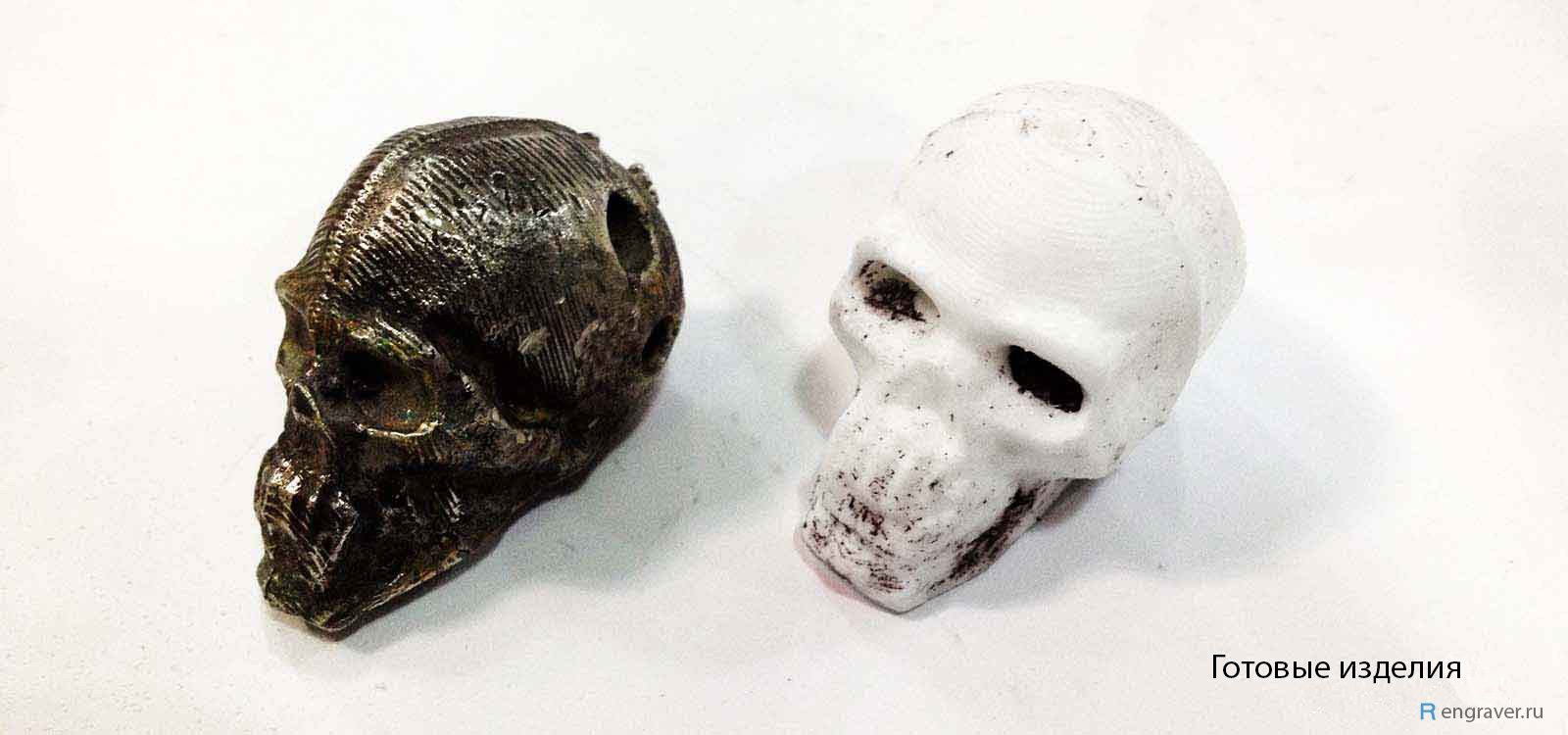
Центробежное литье металлов
Содержание.
Центробежное литье. Этот метод, заимствованный из зубоврачебной техники, уже много десятилетий используется и в ювелирном деле. Каждое ювелирное предприятие должно использовать этот метод литья. Производство оригинальных восковых моделей и сам процесс получения по ним металлических образцов при этом виде литья открывают широкие возможности для получения высокохудожественных ювелирных изделий любой сложности. Так, например, новые центробежные литейные машины отливают 50 колец за одну заливку.
Метод центробежного литья имеет следующие преимущества:
1) возможность получения отливок по моделям любой сложной формы сравнительно простым способом;
2) значительное снижение возможности образования усадочных раковин;
3) уменьшение расхода металла из-за отсутствия прибылей, потребность в которых отпадает.
Ручное центробежное литье по выплавляемой восковой модели . Рассмотрим пример отливки массивного слона высотой 30 мм (рис. 1).
Рис. 1. Элементы формы для центробежного литья:
а — опока с отверстиями; б — восковая модель; в — проволочный каркас
Изготовление модели. Сначала делают проволочный каркас восковой модели из того же материала, который используется для литья. Вокруг этого каркаса лепят из воска модель. Для моделирования можно применять красный или голубой воск, используемый в зубоврачебной технике. Воск нагревают, и с помощью подогретого металлического шпателя производят лепку модели. Готовую модель выглаживают шабером. Для выглаживания можно очень быстро пронести модель через пламя. При этом она слегка оплавляется, и выглаживание производится легко и быстро.
Для уменьшения усадки при изготовлении таких больших изделий, как данная модель, рекомендуется использовать литейные штифты из латунной или медной проволоки диаметром от 1 до 1,5 мм и длиной от 10 до 20 мм и небольшие шаровые прибыли. Штифты нагревают и вводят в восковую модель на несколько миллиметров. На расстоянии 3-4 мм от модели на штифты насаживают восковые шарики (отделяемые прибыли). Сечение литниковых каналов, образуемых штифтами, можно увеличить, покрыв штифты воском. После выплавления воска из формы литейные штифты удаляют, а полости, образованные шариками, выполняют роль прибылей при усадке металла. Кроме того, по каналам, образованным литейными штифтами, удаляются газы и тем самым уменьшается возможность образования пор.
Четыре ноги слона удлиняются восковыми штифтами, сходящимися в восковом шаре. Эти штифты и шар выполняют ту же роль, что и литейные штифты.
Формовка. Готовую модель обезжиривают погружением в спирт для того, чтобы формовочная масса плотно прилегала к модели. Из воска изготавливается и сферическая стойка, в которую вдавливаются литьевые штифты, как это показано на рис. 1, б.
Расстояние между моделью и стойкой должно быть по возможности коротким, чтобы расплаву не было необходимости проделывать столь долгий путь. Модель, кроме того, должна быть так размещена, чтобы все части ее располагались в направлении литья.
В качестве формовочной массы применяют препараты, используемые в зубоврачебной технике. Формовочную массу разводят в дистиллированной воде, тщательно размешивают и вакуумированием удаляют из нее воздух. Формовочная масса должна быть жидкотекучей, сметанообразной, без комочков. Мягкой кисточкой наносят ее на модель. При этом на ней не должно появляться пузырьков воздуха. Этот первый слой припудривается, что препятствует обезвоживанию и предотвращает образование трещин при высыхании формы. По истечении 2-3 мин наносят еще слой формовочной массы и это продолжают до тех пор, пока восковую модель не покроет слой толщиной около 5 мм. Подготовленную таким образом модель помещают в опоку и заливают формовочной массой. Поверхность опоки имеет множество отверстий, благодаря которым быстрее происходит высыхание массы. При заполнении ее следует обернуть бумагой, чтобы формовочная масса не вытекала. Расстояние менаду моделью и стенкой опоки должно быть около 10 мм; до основания формы — 15 мм.
Сушка и прокаливание. Готовую форму не следует оставлять надолго бездействующей. Когда формовочная масса схватилась, восковую полусферу и литьевые штифты удаляют. При сушке и вытапливании восковой модели форму устанавливают в нормальной печи или в печи для эмалирования при низкой температуре так, чтобы отверстие было направлено вниз и воск мог вытекать. После медленной просушки формы производят ее прокаливание. Нагрев при прокаливании должен осуществляться медленно, в противном случае форма может разрушиться. Температуру нагрева при этом повышают до тех пор, пока литниковые каналы не будут накалены до вишнево-красного цвета.
Заливка. Нагретую форму помещают на тарелке центрифуги, и производят заливку металла, который должен быть расплавлен с небольшим количеством буры. Для ювелиров, редко имеющих дело с центробежным литьем, наиболее доступной является настольная центрифуга (рис. 2). Конструкция ее настолько проста, что ее легко можно изготовить самостоятельно. При литье изделий большого размера, к которым относится и приведенный пример, на другую тарелку ставят соответствующий противовес. Сразу же после заливки формы натягивают шнур, и труба, на которой крепится коромысло с тарелкой, начинает вращаться с большой скоростью вокруг неподвижной оси. Преимущество этого способа заключается в простоте обслуживания, большой скорости вращения и безопасности. После нескольких тренировок того же успеха можно достичь и с ручной центрифугой (рис. 3), хотя в этом случае результат зачастую зависит от субъективных причин, а опасность получения дефектов литья возрастает.
Рис. 2. Простейшая настольная центрифуга
Рис. 3. Ручная центрифуга
Литье на центробежных машинах. Рассмотрим процесс получения на центробежной машине литых медалей с двусторонним рельефом (рис. 4). Для получения восковой модели потребуется изготовить резиновую пресс-форму.
Изготовление эталона модели. Так как вулканизация резины происходит при повышенной температуре, то эталон (образец) модели нельзя изготавливать из дерева, пластмассы или легкоплавких металлов. Кроме того, при вулканизации резины выделяется небольшое количество азотной кислоты, поэтому эталон не следует изготовлять из серебра и его сплавов, а также из сплавов золота 333 пробы. Для изготовления эталона модели очень хорошо подходит сплав золота 585 пробы, особенно если поверхность его покрыта родием. Поверхность эталона необходимо тщательно обработать и отполировать. Лучше затратить несколько лишних минут на обработку этого образца, чем потом терять часы при последующей чистовой обработке партии отливок. В заключение следует обратить внимание на то, что отливка из-за усадки металла получается несколько меньшей и еще дополнительно уменьшается в размерах при обязательной чистовой обработке. Поэтому эталон должен иметь несколько большие размеры, чем готовая модель.
Рис. 4. Схема процесса получения изделий центробежным литьем
Изготовление эластичной пресс-формы. Для этой цели необходима опока, подобная литейной при литье в песчаные формы, с направляющими штифтами. Литьевое отверстие необязательно. Опока с направляющими штифтами укладывается на гладкую опорную плиту основанием вниз, например стеклянную, и заполняется пластилином, в который вдавливают до половины эталон модели (рис. 4, 1, 2). Устанавливают вторую опоку и заполняют ее раствором гипса. После затвердевания гипса форму переворачивают, пластилин удаляют, а эталон остается в гипсовой форме. В гипсе делают несколько углублений, которые позднее должны стать направляющими выступами резиновой формы. Сырую резину разрезают на мелкие кусочки, которыми наполняют верхнюю половину формы (рис. 4, 3). Опоки зажимают между двумя стальными пластинами, перекрывающими стенки опок. Резину вулканизируют в течение 30 мин при температуре 150° С в газовой печи или лучше на специальном прессе с двумя подогреваемыми электрическим током плитами (рис. 4, 4, 5). Гипс разбивают, извлекают и хорошо очищают модель и резиновую полуформу. Теперь готовую резиновую полуформу изолируют тальком, и заполняют кусочками сырой резины вторую половину формы, после чего опока укладывается так, что готовая резиновая полуформа находится внизу. Производят вулканизацию резины второй полуформы и получают обе части резиновой пресс-формы (рис. 4, 6). Остается только разъединить части формы друг от друга, отделить их от опок и извлечь модель (рис. 4, 7). После этого прорезают литниковый канал.
Преимущество эластичных резиновых пресс-форм заключается в простоте их изготовления, в легком извлечении из них восковых моделей и в их долговечности.
К недостаткам следует отнести невозможность изготовления спиралевидных полостей и получения очень тонких сечений. Толщина стенки отливки не должна быть меньше 0,4 мм, так как при запрессовке воска форма должна быть зажата и поэтому стенки полуформ могут соединиться вплотную.
Другие методы изготовления эластичных пресс-форм. При изготовлении пресс-форм для простой модели достаточно поместить ее эталон между двумя резиновыми пластинами соответствующей толщины и вулканизировать их под прессом. Эталон вдавливается в размягченную резиновую массу. Недостаток этого метода заключается в том, что обе резиновые пластины <свариваются> и пресс-форму необходимо разрезать, чтобы извлечь эталон и отлить затем восковую модель
В ФРГ изготавливается специальная резиновая формовочная паста, в которую можно легко заформовать металлическую модель. Эта паста затвердевает в холодном состоянии без вулканизации.
Получение восковых моделей. Для заливки воском резиновых пресс-форм применяется восковой инжектор (рис. 4, 8). В бачке находится расплавленный воск, постоянная температура которого поддерживается с помощью электронагрева. Необходимое давление в бачке создается сжатым воздухом, последний выпрессовывает воск через штуцер в литниковый канал пресс-формы. Жидкий воск можно ввести в форму центробежным методом, используя для этого металлическую центрифугу. При этом стенки резиновой пресс-формы перед каждым заполнением воском должны изолироваться эвкалиптовым маслом или смесью, состоящей из одной части воды и одной части глицерина.
Подготовка формы и заливка. Как схематично изображено на рис. 4, 9, готовые восковые модели размещаются вокруг воскового стояка, с которым они соединяются с помощью восковых штифтов. <Восковую елку> напаивают на восковой цоколь и устанавливают на резиновом основании, поперечное сечение которого видно на этом же рисунке. Далее блок восковых моделей обрабатывают так же, как это было описано выше: обезжиривают, покрывают кисточкой формовочной массой, помещают в цилиндрическую опоку и заливают ее провакуумированной формовочной массой. После затвердевания формовочной массы опоку помещают в муфельную печь (рис. 4, 10) и в течение часа при 200° С выплавляют воск. Затем температуру повышают до 1000° С и выдерживают форму при этой температуре еще 15 мин. После этого ее вынимают из печи, помещают в центробежную машину (рис. 4, 11) и производят заливку. Готовый блок отлитых медалей с литниками, полученный после выбивки опоки, показан на рис. 4, 12.
По материалам книги ‘Теория и практика ювелирного дела’, 1975 год
Следующая статья >>Литьевая форма: классификация и особенности литья
Литьевая форма применяется в термопластавтоматах для изготовления объемных деталей различных конфигураций из пластика, металла, резины.
В пресс-форме литьевой машины может одновременно производится одна или несколько деталей. Используется в массовом или серийном производстве.
Рис. 1. Литьевая форма.
Что такое пресс-форма
Литьевые формы состоят из неподвижных матриц и подвижных пуансонов, имеющих внутри полость для формирования заготовок.
Материал внутрь формы подается с помощью литниковых систем, которые бывают холодноканальные, горячеканальные и комбинированные.
В некоторых конструкциях форм возможна установка закладных деталей.
Классификация литья
Литье пластмассы в пресс-форму применяется для создания тонкостенных изделий различной конфигурации.
Технология литья позволяет создавать армированные и пустотелые детали, многоцветные и соединяющие в себе различные полимерные материалы.
Требуемый показатель давления — от 80 до 200 Мпа. При более низком давлении могут образовываться полости или недоливы.
Превышение показателей может привести к образованию облоя.
Литье в песчаные формы
Один из самых распространенных видов литья объемных заготовок.
Применяется в автомобильной отрасли, станкостроении и других отраслях промышленности. Эта технология используются при массовом производстве, изготовлении небольших серий или единичных товаров простой или сложной формы.
При таком литье получаются изделия низкого качества. Возможно наличие пустот и различных посторонних включений.
Обычно литье в песчано-глиняные формы применяют для изготовления станин для металлообрабатывающей отрасли, корпусных элементов машин и оборудования, различных колес, колец и прочих объемных и тяжелых заготовок.
Литье в вакуумно пленочные формы
Технология применяется для отливок любого количества изделий весом от одного килограмма до десяти тонн, размерами до нескольких метров.
Формы изготавливаются в следующем порядке:
• вырезается модельный комплект из пенополистирола или других газонепроницаемых материалов;
• на модель накладывается предварительно нагретая синтетическая пленка;
• с помощью вакуумного устройства между модельным комплектом и пленкой создается вакуум, плотно притягивающий пленку к модели;
• на пленку накладывается слой меловой известняковой глины (опоки), засыпается сухим песком, трамбуется и укрывается герметично пленкой;
• из опоки при помощи вакуумного устройства удаляется воздух, модельный комплект вынимается из готовой полуформы.
Рис. 2. Литье в вакуумную форму.
Аналогично изготавливаются все детали и собираются в единую форму.
В течение всего технологического процесса составные элементы формы находятся под вакуумом.
В собранную форму заливается расплавленный металл. После охлаждения отливок вакуумное устройство отключается, вследствие чего песок удаляется из формы, отливка легко вынимается из формы.
Литье в кокиль
Кокиль — металлическая многооборотная форма из чугуна, алюминия или стали.
Литье в кокиль подходит для изготовления изделий из алюминия, цветных и черных металлов.
Технология литья в кокиль состоит из нескольких этапов:
• фиксация металлических полуформ;
• нагрев рабочей полости формы до температуры около 180°С;
• смазывание поверхности слоем защитного огнеупорного покрытия;
• заливка расплавленного сырья через литники;
• охлаждение формы;
• раскрытие кокиля и выемка отливки.
Рис. 3. Литье в кокиль.
Отливки в кокиль отличаются высоким качеством и геометрической точностью размеров.
Литье по выплавляемым моделям
Способ получения отливок заключается в изготовлении модели из легкоплавких составов в пресс формах. Затвердевшая модель вынимается из формы и покрывается несколькими слоями суспензии и обсыпки, образующими после высыхания керамическую скорлупу. Модель внутри скорлупы выплавляется, создавая оболочку формы с тонкими керамическими стенками.
В полученную форму заливается расплавленная смесь, которая после остывания образует изделие, точно повторяющее конфигурацию модели.
Детали, по выплавляемым моделям отличается высоким качеством и чистотой поверхности, не требуют дополнительной обработки.
Литье по газифицируемым моделям
Способ получения литых изделий с использованием моделей из материалов, которые превращаются в газ при контакте с расплавленным металлом. Больше всего подходит для этого вспененный полистирол.
Модели изготавливаются на модельных автоматах или путем заливки литейного полистирола мелких фракций под давлением в пресс-формы, с последующим спеканием под действием высоких температур.
Элементы моделей склеиваются или спаиваются в блоки, покрываются огнестойким покрытием путем облива или окунания и формируются на вибростоле в специальные опоки.
Расплавленный металл подается прямо на модельные блоки, выжигая и газифицируя полистирол.
Готовые отливки охлаждаются в формах, затем извлекаются и очищаются от антипригарного покрытия.
Технология литья по газифицируемым моделям позволяет выпускать изделия с гладкими точными формами.
Газы, образуемые при выжигании полистирола. удаляются при помощи вытяжных устройств.
Центробежное литье
Применяется для изготовления полых цилиндрических емкостей.
В основе технологии лежит принцип формирования отливок в поле центробежных сил.
Расплавленный металл из ковша(3) подается через заливочную воронку (2) во вращающийся цилиндр, внутренняя сторона которого (1) является формообразующей поверхностью.
Полученный пустотелый цилиндр после остывания и затвердевания металла извлекается из формы.
Рис. 4. Центробежное литье.
Литье в оболочковые формы
Технология применяется для изготовления особо точных деталей с повышенными требованиями к качеству.
Оболочковые формы изготавливаются из смоляно-песчаной смеси, термореактивных смол, кварцевого или цирконового песка на автоматических линиях.
Литье включает ряд последовательных операций:
• приготовление смеси;
• изготовление моделей в виде тонкостенных оболочек;
• сборка и подготовка форм к заливке;
• плавление металла и заливка в готовые формы;
• остывание и извлечение отливок;
• зачистка и дробеструйная обработка
Оболочковые формы применяются для изготовлени изделий из чугуна, стали, цветных металлов и алюминия.
Технология изготовления литьевых форм
Пресс формы для литья пластмасс изготавливаются на основании разработанного проекта.
1. Из стального литья вырезается заготовка по параметрам будущего изделия.
2. Форма обрабатывается на фрезерных станках, и шлифуется на шлифовальных машинах.
3. Изделия проходят термообработку в специальных печах, хромируются и полируются.
4. Готовые изделия тестируются и испытываются в лабораториях.
5. Составляются линейные карты и подписываются двусторонние акты выполненных работ.
6. Пресс-формы упаковываются и передаются заказику.
По желанию заказчика, специалисты компании «Имстек» выполнят установку и наладку оборудования, обучат технический персонал заказчика.
Определение стоимости изготовления литьевых форм
Стоимость пресс-форм определяется с учетом следующих показателей:
• исходного сырья;
• количество разъемных плоскостей;
• сложности и габаритов изделий;
• гарантированного производителем ресурса;
• количества гнезд в модуле.
Дешевле стоят машины с боковыми или прямыми литниками и холодноканальные системы.
Усадка
При изготовлении литьевых пресс-форм необходимо учитывать возможную технологическую усадку формообразующих деталей в процессе охлаждения.
Усадка может зависеть от следующих факторов:
• вида применяемых для изготовления пресс-форм материалов;
• наличия армирующих волокон;
• типа и размеров литника;
• равномерности распределения температуры;
• конструктивных особенностей форм.
Снизить усадочные явления поможет добавление в сырье армирующих волокон.
Проектирование конструкции литьевой формы
Разработка проекта литьевых форм выполняется на основании технического задания заказчика.
Выполняются необходимые расчеты, создается 3D модель будующего изделия, выполняются рабочие чертежи.
От грамотного проекта и выбранной технологии изготовления зависит качество и долговечность пресс-форм.
Деформация форм
Деформации литьевых форм может произойти при нарушениях технологии литья:
• превышение проектных параметров силы впрыска;
• сильного давления внутри формы;
• различные температуры поверхностных слоев при охлаждении заготовок;
• неправильно подобранной температуре расплава.
Отступление от проектных параметров литья могут привести к деформациям и преждевременному износу форм.
Сдвиг пуансонов
Смещения и перекосы пуансонов относительно матрицы могут произойти из-за увеличенного зазора между деталями, повреждения кромок или неравномерных нагрузок на направляющие колонны.
Сдвиг происходит из-за неправильного крепления пуансона или большого усилия при выталкивании детали из пресс форм.
Извлечение отлитых изделий
Готовые изделия извлекаются из пресс-форм с помощью сжатого воздуха, выталкивающих стержней, вкладышей или плит.
При отсутствии устройств для автоматического извлечения отливок, готовые изделия удаляются вручную.
Обслуживание литьевых форм
Для надежной и долговечной работы пресс-форм требуется регулярный осмотр и техническое обслуживание.
При смене оснастки проводите очистку направляющих штифтов и гнезд от смолы, смазки и прочих загрязнений.
Чтобы избежать коррозии, важно защищать устройство от влажности и смазывать форму антикоррозийными средствами.
Проверяйте на легкость движения подвижные элементы пресс-форм. При необходимости, выполняйте своевременно настройку.
Способы устранения дефектов, возникающих в процессе литья под давлением
В процессе литья под давлением могут проявляться различные дефекты, которые можно устранить, зная причины их образования:
1. Расслоения на поверхности изделий устраняются при повышении температуры расплава и понижении скорости впрыска.
2. Облой может появится при использовании большого объема впрыска или недостаточном смыкании пресс-формы.
3. Пустоты могут образовываться при недостаточном объеме впрыска или длительном и неравномерном охлаждении изделия.
4. Коробление изделий бывает из за низкой текучести материала, недостаточной скорости впрыска или неравномерного охлаждения изделий в форме.
5. Хрупкость и ломкость изделия возникает при малой толщине стенок изделий или низкой температуры форм при заливке.
Для профессионального обслуживания литьевых форм обратитесь в компанию «ИМСТЕК» выполняющую поставку, пусконаладку и техническое сопровождение литьевого оборудования.
Мастер-класс смотреть онлайн: Художественное литье бронзы по выплавляемым моделям
Процесс литья по выставляемым моделям.
Очень часто мои заказчики и покупатели спрашивают, «Как же все же делают фигурки из бронзы?» и постоянно приходится рассказывать процесс заново. Решил создать ..этакую шпаргалку 🙂 …мастер-классом вроде и не назовешь её. Описать решил максимально простым языком без специальной терминологии. Думаю так будет проще и понятнее не создаст дополнительных вопросов. Хочу еще сказать, что сам я не литейщик, я только создаю мастер-модели, снимаю с них формы, делаю восковки и их уже везу в литейную мастерскую. А потом готовые отливки довожу до ума. Обработка очень важная часть финального процесса.
Но во всех стадиях литья принимал не однократное участие и потому знаком со всеми стадиями процесса. Работа это не легкая и требует аккуратности и дотошности..мелочей нет. Схалтуришь на одном каком то этапе и работа всей команды будет загублена.
Литейное дело — одно из самых древних в мире ремесел, трудоемкая и сложная работа, требующая внимания и аккуратности на каждом этапе подготовки и литья. От Мастер-модели до финальной отливки в бронзе. Но результат стоит затраченных усилий. Литые изделия отличаются изысканным внешним видом. С годами на поверхности изделий из бронзы, латуни покрывается оксидной пленкой — это придаёт внешнему виду изделий антикварный вид. С годами изделия из бронзы как благородное вино растут в цене покрываясь налетом старины.
Довольно высокая цена на изделия выполненных методом художественного литья по выставляемым моделям, обусловлена большим количеством операций выполненными вручную, а так же дорогостоящими расходными материалами (ювелирный воск, формомасса, сплавы, а так же расходники для последующей обработки готовых изделий).
Коротко процесс создания бронзовой фигурки можно описать по операциям.
1. Изготовление мастер-модели для литья. Модель может быть из разных материалов: пластилин, воск, дерево, пластики, металл, гипс и т.д.
Несколько примеров моих мастер-моделей изготовленных из разных пластиков:
будущие шахматные фигурки:
фигурка сноубордист «Карвер»
Мы в своем технологическом процессе чаще создаем мастер-модели из полимерных скульптурных пластиков. Скульптор-миниатюрист создает модель вручную. Сложные модели иногда приходится делать разборными и многосоставными. На модель крепят литниковую систему продумывая как будет течь металл и как затем удалить литники без ущерба для будущей фигурки.
2. С мастер-модели снимается силиконовая (резиновая) форма из специальной резины. Изготавливается так называемая матрица, по которой затем будет получена восковая копия модели (восковка). С литниками для последующего литья.
Форму разрезают особым способом, что бы можно было получить качественную восковку.
3. После изготовление резиновой формы в неё под давлением впрыскивается горячий воск. Затем, когда воск остыл матрицу разбирают и достают восковую копию модели. Её нужно проверить на наличие дефектов., обработать снять восковый облой, если он есть, просмотреть(просветить восковки) нет ли пузырьков в восковке иначе на отливке из металла будут полости и раковины. Если нужно восковка затем проходит стадию полировки. В час в среднем с одной резиновой формы можно получить 4-5 восковок в зависимости от размера и сложности.
Восковки с литниковой системой:
4. Восковки готовы теперь предстоит спаять елку из наших восковых фигурок. Примерно под углом 45 градусов фигурки одна за другой крепятся к основному более толстому литнику. Постепенно обрастя фигурками вырастает нечто напоминающее ёлку.
5. Затем подготовленная ёлка ставится в резиновую опору и помещается в металлическую опоку. Сверху заливается формомассой (специальный гипсовый состав), Опока ставится под вакуум для удаления пузырьков из формомассы. Если этого не сделать фигурка вся будет покрыта мелкими бусинками металла. Формомасса затвердела.
6. Следующий этап вытапливаем восковые модели и затем постепенно прокаливаем получившиеся керамические формы в специальных прокалочных печах до нужной температуры. Формы должны выдерживать температуру расплавленных сплавов около 1300 градусов.
Около суток формы доводятся до нужной температуры, плавно поднимаясь до нужной температуры и затем так же плавно остывают.
7. Затем в подготовленные формы, выстоявшиеся и доведенные до требуемой температуры заливается расплавленный сплав и ставится под вакуум. Так как форма гигроскопична, металл притягивается к стенкам формы. За счет чего получается качественная поверхность отливки. Процесс подготовки форм и литья беспрерывно продолжается несколько дней. Тираж нельзя прервать и остановить всю тепловую цепочку процесса. Для этого литейщикам приходится работать в несколько смен, для контроля всего цикла литья.
8. После заливки форм их охлаждают и разрушают.
Отлитые ёлочки с фигурками разрезают специальными кусачками срезая фигурки с центрального литника.
Затем наступает очередь непосредственной обработки будущих фигурок. Фигурки размывают и очищают от остатков застывшей формомассы. Затем могут быть подвергнуты к отмачиванию в специальных растворах для удаления накала на фигурках.
9. Затем наступает очередь механической обработке. С фигурок удаляю литники, стачивая их бормашинами и полируют места крепления литников к фигурке. Далее фигурки обрабатывают мягкими латунными щетками на станках, снимая остатки окалины, полируют со специальными пастами муслиновыми кругами (тряпочные круги различной плотности с пропитками) После полировки фигурки она может проходить процесс ускоренного старения (чернения) для придания металлу антикварного вида. После обработки кислотами и специальными составами фигурки опять подвергают полировке мягкими муслиновыми кругами и растирают тканью выравнивая общий тон фигурки
Вот собственно финал нашей работы, долгожданные фигурки из металла 🙂
Кладоискатели, слева без чернения только полировка с карцеванием..справа чернение и дополнительная полировка.
Шахматная фигурка, Королева бордеров. Бронза, гальваническое покрытие меднение
«Не свисти- денег не будет!»
.
Изготовление отливок центробежным литьем
При центробежном литье сплав заливается во вращающиеся формы. Формирование отливки осуществляется под действием центробежных сил, что обеспечивает высокую плотность и механические свойства отливок.
Центробежным литьем изготовляют отливки в металлических, песчаных, оболочковых формах и формах для литья по выплавляемым моделям на центробежных машинах с горизонтальной и вертикальной осью вращения.
Металлические формы изложницы изготовляют из чугуна и стали. Толщина изложницы в 1,5…2 раза больше толщины отливки. В процессе литья изложницы снаружи охлаждают водой или воздухом.
На рабочую поверхность изложницы наносят теплозащитные покрытия для увеличения срока их службы. Перед работой изложницы нагревают до 200 0C.
Схемы процессов изготовления отливок центробежным литьем представлены на рис.6.4.
Рис.6.4. Схемы процессов изготовления отливок центробежным литьем
При получении отливок на машинах с вращением формы вокруг вертикальной оси (рис. 6.4.а) металл из ковша 4заливают во вращающуюся форму2, укрепленную на шпинделе1, который вращается от электродвигателя.
Под действием центробежных сил металл прижимается к боковой стенке изложницы. Литейная форма вращается до полного затвердевания отливки. После остановки формы отливка 3извлекается.
Отливки имеют разностенность по высоте – более толстое сечение в нижней части. Применяют для получения отливок небольшой высоты – коротких втулок, колец, фланцев.
При получении отливок типа тел вращения большой длины (трубы, втулки) на машинах с горизонтальной осью вращения (рис. 6.4.б) изложницу 2устанавливают на опорные ролики7и закрывают кожухом6. Изложница приводится в движение электродвигателем1.Расплавленный металл из ковша4 заливают через желоб3, который в процессе заливки металла перемещается, что обеспечивает получение равностенной отливки5. Для образования раструба трубы используют песчаный или оболочковый стержень8. После затвердевания металла готовую отливку извлекают специальным приспособлением.
Скорость вращения формы зависит от диаметра отливки и плотности сплава, определяется по формуле:
,
где: –
плотность сплава;
–
внутренний радиус отливки.
Центробежным литьем изготавливают отливки из чугуна, стали, сплавов титана, алюминия, магния и цинка (трубы, втулки, кольца, подшипники качения, бандажи железнодорожных и трамвайных вагонов).
Масса отливок от нескольких килограммов до 45 тонн. Толщина стенок от нескольких миллиметров до 350 мм. Центробежным литьем можно получить тонкостенные отливки из сплавов с низкой текучестью, что невозможно сделать при других способах литья.
Недостаток: наличие усадочной пористости, ликватов и неметаллических включений на внутренних поверхностях; возможность появления дефектов в виде продольных и поперечных трещин, газовых пузырей.
Преимущества – получение внутренних полостей трубных заготовок без применения стержней, экономия сплава за счет отсутствия литниковой системы, возможность получения двухслойных заготовок, что получается поочередной заливкой в форму различных сплавов (сталь – чугун, чугун – бронза).
Используют автоматические и многопозиционные карусельные машины с управлением от ЭВМ.
Учебники по изготовлению и литью бетонных форм от Smooth-On, Inc.
Фильтровать по Товар> Обработать>- AquaCon ™ (5)
- Brush-On ™ 40 (2)
- duoMatrix ™ NEO (5)
- Ease Release ™ 2831 (1)
- Ease Release ™ 200 (5)
- EpoxAcast ™ 690 (1)
- FOAM-iT! ™ 10 SLOW (1)
- FOAM-iT! ™ 5 (1)
- FOAM-iT! ™ 8 (1)
- Formlastic ™ 60 (1)
- Forton ™ VF-774 (21)
- Free Form ™ AIR (1)
- Распылитель Kwikee ™ (2)
- Mold Max ™ ХОД (1)
- Mold Max ™ XLS ™ II (1)
- Mold Star ™ 16 FAST (2)
- Mold Star ™ 30 (3)
- Plasti-Paste ™ (3)
- Plasti-Paste ™ II (3)
- PMC ™ -780 DRY (2)
- Rebound ™ 25 (10)
- ReoFlex ™ 40 (1)
- Silc Pig ™ (3)
- Smooth-Cast ™ ONYX ™ FAST (1)
- SO-Strong ™ (3)
- Воск Sonite ™ (10)
- SuperSeal ™ (8)
- ЗАДАЧА ™ 16 (2)
- THI-VEX ™ (5)
- Турбинный смеситель (1)
- Разделитель для пресс-формы Universal ™ (12)
- VytaFlex ™ 40 (6)
- VytaFlex ™ 60 (4)
- XTC-3D ™ (1)
- видеоурок (23)
- gfrc (13)
- заливочная форма (13)
- бетонные панели (12)
- форма для щетки (11)
- мебель из бетона (4)
- раковина из бетона (4)
- сеялка для бетона (3)
- Соотношение смеси 1: 1 (2)
- бетонная столешница (2)
- каменный шпон (2)
- Форма для заливки полости (1)
- скамейка бетонная (1)
- бетонный штамп (1)
- бетонный стол (1)
- стержневая форма (1)
- Заглушка формы (1)
- вакуум не требуется (1)
Как установить и обслуживать смесительную машину EZ-Mix Meter
Узнайте, как работать с дозатором EZ-Mix
›Просмотреть статью с инструкциями
видео
Как сделать бетонные столешницы для выставочного стенда
В этом видео мы покажем вам, как мы создавали новые бетонные столешницы для нестандартной перголы.
›Просмотреть статью с инструкциями
видео
Как сделать форму для заливки бетонной плитки
Изучите шаги, необходимые для изготовления производственной формы для столешницы с использованием Formlastic ™
›Просмотреть статью с инструкциями
видео
Как сделать форму из камня для бетонной раковины
Узнайте, как слепить небольшой валун с помощью кисти Rebound 25 на силиконовой резине.
›Просмотреть статью с инструкциями
видео
Как сделать стену для боулдеринга с помощью Buddy Rhodes Vertical Mix ™
Скалолазание Убергриппен недавно добавили стену для боулдеринга длиной 100 футов на своем заднем дворе
›Просмотреть статью с инструкциями
видео
Как сделать стол для аквариума Lagoon из бетона и эпоксидной смолы
Узнайте, как использовать бетон в сочетании с прозрачной эпоксидной смолой для создания аквариумного стола.
›Просмотреть статью с инструкциями
видео
Как восстановить историческую бетонную печать в Принстонском университете
Посмотрите, как Джон Паолини из компании Paolini Cast Stone восстановил историческую бетонную печать
›Просмотреть статью с инструкциями
видео
Как воспроизвести деталь дерева в бетоне
Платиновый силиконRebound 25 захватывает все детали текстуры древесины и переносит их на бетонную отливку.
›Просмотреть статью с инструкциями
видео
Как сделать стол для шаффлборда GFRC
В этом обучающем видео мы покажем вам, как мы сделали стол для шаффлборда для наших помещений.
›Просмотреть статью с инструкциями
видео
Проекты магазинов — Как сделать раковину из бетона
В этом видео мы покажем вам, как мы сделали раковину из бетона для нашего магазина, используя Forton® VF-774.
›Просмотреть статью с инструкциями
видео
GFRC Explained — Изучите основы GFRC
Мы объясняем различные компоненты, схемы смешивания и надлежащие методы, необходимые для создания высококачественного GFRC
›Просмотреть статью с инструкциями
видео
Как заливать бетон с использованием разделительного агента Aquacon®
AquaCon® — это разделительный состав для бетона на водной основе, который помогает отделить бетонные отливки от резиновых форм Smooth-On
›Просмотреть статью с инструкциями
видео
Как сделать солнцезащитную навесную стену из цифрового дизайна
Клиент Smooth-On «Taller de Prefabricados» пригласил нас заснять их процесс.
›Просмотреть статью с инструкциями
видео
Как сделать бетонный настенный светильник из модели, напечатанной на 3D-принтере
Пошаговое видео, показывающее, как 3D-печатная модель формуется, а затем заливается в бетон.
›Просмотреть статью с инструкциями
видео
Как сделать форму листа для заливки бетона
Сделайте слепок листа ревеня, используя силиконовый каучук Rebound® 25
›Просмотреть статью с инструкциями
видео
Как сделать фонтан из бетона на заказ
Узнайте, как сделать фонтан из бетона, который выглядит как песок, с помощью силиконового каучука Mold Star® 16.
›Просмотреть статью с инструкциями
видео
Как сделать нестандартные бетонные столешницы с использованием GFRC
Узнайте, как делать чрезвычайно прочные бетонные столешницы из Forton® VF-774
›Просмотреть статью с инструкциями
видео
Как построить бетонный стержень с использованием панелей GFRC — Эпизод 1
Узнайте, как изготавливать бетонные панели в стиле ар-деко, от модели до литья из пигментированного GFRC.
›Просмотреть статью с инструкциями
видео
Как построить бетонный стержень с использованием панелей GFRC — Серия 2
Узнайте, как сделать уличный бар и беседку, используя панели Art Deco GFRC.
›Просмотреть статью с инструкциями
видео
Как построить бетонный стержень с использованием панелей GFRC — Эпизод 3
Узнайте, как сделать уникальные формы для кромок для бетонных столешниц с использованием уретанового каучука TASK 16.
›Просмотреть статью с инструкциями
видео
Как сделать декоративные панели GFRC из ствола дерева джунглей
Компания «Taller de Prefabricados» пригласила нас на свои предприятия, чтобы снять фильм о процессе изготовления пресс-форм.
›Просмотреть статью с инструкциями
видео
Как создать угловую архитектурную панель из GFRC
GFRC Cladding Systems создает угловые панели для установки в здании в дизайнерском районе Майами.
›Просмотреть статью с инструкциями
видео
Как создать архитектурный карниз из GFRC
GFRC Cladding Systems показывает, как создать карниз для облицовки напылением.
›Просмотреть статью с инструкциями
видео
Как распылить GFRC для создания киоска выставочного зала
В этом видео мы показываем пошаговый процесс создания киоска для стойки продаж с пользовательской текстурированной поверхностью с использованием GFRC, улучшенного с помощью Forton® VF-774.
›Просмотреть статью с инструкциями
Как создать кресло для отдыха GFRC с использованием силиконового каучука Rebound ™ 25
Используя формовочную резину Rebound ™ 25, OBRaTUR, S.A. создала линию мебели из стеклопластика, устойчивую к ураганам.
›Просмотреть статью с инструкциями
видео
Как создать стол GFRC с использованием силиконового каучука Rebound ™ 25
При создании дизайна стола GFRC используется корень дерева Royal Poinciana, восстановленный после урагана.
›Просмотреть статью с инструкциями
видео
Как создать текстурный мат из силиконовой резины для панелей GFRC
Стена амбара внутри сарая имеет текстуру под дерево, которую можно дублировать на панели GFRC для установки душа.
›Просмотреть статью с инструкциями
видео
Как сделать текстурированные душевые панели GFRC
Несколько панелей GFRC разных размеров и форм будут изготовлены из этой формы для матов с одной текстурой.
›Просмотреть статью с инструкциями
видео
Как сделать бетонный штамп из уретанового каучука
Цель проекта: превратить заброшенный служебный вход в привлекательную бетонную дорожку с печатью.
›Просмотреть статью с инструкциями
видео
Как использовать бетонный штамп
Проект: заменить существующий служебный вход декоративным бетонным переходом.
›Просмотреть статью с инструкциями
Как сделать двухкомпонентную форму архитектурного кронштейна
После урагана Катрина, обрушившегося на Новый Орлеан, уроженец города Чеп Моррисон скопировал декоративную скобу
›Просмотреть статью с инструкциями
видео
Раскрывая тайну изготовления бетонной формы для раковины
В этом пошаговом руководстве используется резина Smooth-On VytaFlex® 40 для демонстрации изготовления формы для раковины для бетона.
›Просмотреть статью с инструкциями
Как выполнить сборные бетонные стены, созданные для восстановления Нового Орлеана
Гладкие материалы, используемые как часть видения одного человека, чтобы принести надежду жителям уставшего от шторма Нового Орлеана
›Просмотреть статью с инструкциями
видео
Как сделать бетонную раковину — от проектирования до производства
Команда талантливых мастеров объединилась, чтобы создать уникальные элементы декора из бетона с водной тематикой.Бетонные раковины, душевые из бетона по индивидуальному заказу …
›Просмотреть статью с инструкциями
видео
Как построить бетонный забор, демонстрирующий детали, невиданные ранее
Уникальный процесс изготовления пресс-форм позволяет быстро создать 11880 легких бетонных панелей …
›Просмотреть статью с инструкциями
Как сделать индивидуальную бетонную скамью
Недавняя работаBenchmark для Университета штата Пенсильвания заключалась в изготовлении специальной бетонной скамьи.Г-н Рон снова обратился к VytaFlex за резиновой формой.
›Просмотреть статью с инструкциями
видео
Как воспроизвести трехмерную скульптуру с помощью резиновой формы Brush-On ™ 40
Создание слепка трехмерной скульптуры кистью — эффективный и недорогой метод, который можно использовать для …
›Просмотреть статью с инструкциями
Как создать форму Rebound ™ 25 для литья баньянового дерева GFRC
Инженер Pretecno Хосе Хормига разработал способ привнести органику в некоторые из последних строительных проектов компании.
›Просмотреть статью с инструкциями
Как отлить бетонную облицовку из камня с использованием резины для формования VytaFlex ™
Краткая пошаговая галерея с подробным описанием стандартной процедуры заливки с использованием уретанового каучука Vytaflex® для заливки бетона.
›Просмотреть статью с инструкциями
Как сделать форму для нанесения кистью с легкой опорой
Ниже показано, как сделать форму из каменного шпона…
›Просмотреть статью с инструкциями
видео
Как сделать форму сердечника из двух частей: пример бетонной урны
В этом руководстве описаны этапы создания двухкомпонентной пресс-формы с сердечником из уретанового каучука Reoflex® 40 от Smooth-On.
›Просмотреть статью с инструкциями
Как сделать слепок для 3D-полой модели
Эта пошаговая галерея демонстрирует, как сложная форма головы пумы будет изготовлена из силиконового каучука Smooth-On Rebound 25, наносимого кистью…
›Просмотреть статью с инструкциями
Как сделать кисть на форме с помощью Mold Max ™ STROKE
Как сделать кисточку на оловянной силиконовой форме
›Просмотреть статью с инструкциями
видео
Как изготовить обшивку большого размера с резиной для формования VytaFlex ™
Департаменту транспорта Пенсильвании потребовалось 2 000 декоративных шумоподавляющих панелей, чтобы обеспечить максимальную общественную безопасность и снизить шум шоссе.
›Просмотреть статью с инструкциями
видео
Как сделать форму для сеялки по бетону
Узнайте, как сделать форму для стеклянного кашпо с помощью Mold Star ™ 16 Fast.
›Просмотреть статью с инструкциями
видео
Как использовать картриджи с влагопоглотителем на транспортных средствах
В этом видео мы показываем, как установить и использовать трубку с осушителем на бункере материала.
›Просмотреть статью с инструкциями
видео
Как использовать картриджи с влагопоглотителем на барабанных установках емкостью 55 галлонов
В этом видео мы показываем, как установить и использовать осушающую трубку на бочке с материалом объемом 55 галлонов.
›Просмотреть статью с инструкциями
.Как сделать гипсовую форму для шликерного литья
Литье в шликер, вероятно, самый популярный способ изготовления керамических стеновых панелей, особенно если они состоят из повторяющихся форм. Если вам интересно, как сделать гипсовую форму для шликерного литья, сегодняшний пост для вас. В этом отрывке из мартовского выпуска Ceramics Monthly за март 2019 года Джеки Хед проведет вас через процесс изготовления гипсовой формы от изготовления прототипа до заливки гипсовой формы.Так что взгляните и пометьте «узнайте, как сделать гипсовую форму для отливки шликера» из своего списка дел!
л.с. Чтобы узнать больше о процессе отделки и установки Джеки, а также увидеть больше изображений ее работ, смотрите выпуск Ceramics Monthly за март 2019 года!
Как сделать гипсовую форму для шликерного литья — Часть 1: прототипы
Контуры плитки увеличены на 10%, чтобы компенсировать усадку, возникающую при обжиге фарфоровой глиняной массы до конуса 6.Я распечатываю очертания прототипов форм, вырезаю их и рисую на ламинатных досках. Отдельные прототипы передней и задней половин каждой из фигур вылеплены из твердой глины с использованием глиняного тела без гребня для достижения гладкой поверхности. Влажная глина грубо набивается на доски примерно по форме и желаемой глубине, как у прототипов плитки. После высыхания в течение нескольких часов глина начинает затвердевать, затем я вырезаю прототипам более четкую форму (1). Когда прототипы достигают начальных стадий твердости кожи, я уточняю формы, используя инструменты с зазубринами и различные ребра, чтобы достичь их окончательных форм, при этом гарантируя отсутствие подрезов на прототипе (2).

Научитесь делать и использовать формы для бисквита и гипса, а также получите рецепты литейных шликеров, загрузив этот бесплатный пакет «Методы изготовления керамических форм».
При подготовке к созданию слепков передней половины каждой формы прототипы дорабатываются в последний раз. Для этого используется мягкая кисть, смоченная водой, чтобы удалить любые дефекты, а гибкое ребро используется для создания гладкой поверхности и усиления любых острых углов.

1 После того, как прототип высохнет в течение нескольких часов, вырежьте из глины более изысканные формы.

Новые технологические процессы для функционально-сортированных материалов и конструкций путем сочетания порошковой металлургии и литья
2.1. Центробежный смешанный порошковый метод
Многие попытки изготовить FGM были сделаны с помощью центробежного литья [5–7]. Как правило, чем меньше размер диспергированных частиц, тем труднее их диспергировать в расплавленной матрице. Уравнение для скорости твердой частицы в вязкой жидкости может быть записано как:
dxdt = | ρp − ρm | GgDp218ηE1где ρpis плотность частиц, ρm плотность расплавленной матрицы, g ускорение свободного падения, диаметр частицы D и η вязкость расплав [7].Поскольку скорость твердой частицы в вязкой жидкости зависит от квадрата диаметра частицы Dp, довольно сложно контролировать ступенчатое распределение дисперсных наночастиц в FGM в случае обычного центробежного литья. В качестве новой технологии обработки FGM с металлической матрицей метод центробежной порошковой смеси был предложен Watanabe et al. [12] для преодоления этих проблем. Центробежный метод смешанного порошка может дать нам FGM с мелкодисперсными частицами, используя комбинацию высокой центробежной силы и смешанного порошка.Этот новый метод представляет собой развитую технику центробежного литья путем заблаговременной заливки заданной порошковой смеси в форму [12].
Рис. 2.
Схематическое изображение, показывающее процесс центробежного метода смешанного порошка [12].
Рисунок 2 показывает экспериментальную процедуру центробежного смешанного порошкового метода. Сначала готовится заранее приготовленная порошковая смесь. Этот смешанный порошок состоит из частиц металлической матрицы и частиц дисперсии. В принципе, температура плавления частиц дисперсии должна быть выше, чем у частиц металлической матрицы, чтобы образовались FGM.Такие частицы, как керамика, металлы и сплавы, которые имеют более высокие температуры плавления по сравнению с металлической матрицей, могут быть выбраны в качестве частиц дисперсии для FGM с металлической матрицей. Смешанный порошок, включающий частицы металлической матрицы и частицы дисперсии, помещают в прядильную форму, как показано на Фигуре 2 (а). После этого слиток с металлической матрицей плавится в тигле. Эту матрицу расплавленного металла выливают в прядильную форму, как показано на Рисунке 2 (b). Вылитая матрица расплавленного металла проникает в пространство между частицами из-за приложенной центробежной силы, как показано на Рисунке 2 (c).Тепло от разлитой расплавленной матрицы плавит частицы металлической матрицы, как показано на рисунке 2 (d). Наконец, могут быть получены FGM в форме кольца или диска или структуры с частицами дисперсии, распределенными во внешней части литого образца, как показано на Рисунке 2 (e). FGM, такие как Cu / SiC [12], Al / TiO 2 [12] и Al / Al 3 Ti / Ti [15], были получены этим методом обработки в наших предыдущих исследованиях.
Рисунок 3.
Типичный внешний вид машины для вакуумного центробежного литья.
Центробежный метод смешанного порошка также может быть реализован с использованием имеющихся в продаже машин центробежного литья. На рис. 3 показан типичный внешний вид машины для вакуумного центробежного литья, поставленной Yasui & Co, Япония. Эта центробежная разливочная машина имеет нагревательный змеевик, прямую штангу, тигель, форму и балансир внутри литейной камеры [18]. За счет заблаговременной укладки предварительно разработанного смешанного порошка в форму можно получить FGM. Используя этот метод обработки, в наших предыдущих исследованиях были изготовлены Cu / алмаз [13], сплав Al / алмаз [14] и другие FGM.Подробный метод обработки и микроструктурные характеристики изготовленных FGM Cu / алмазов показаны ниже.
Рисунок 4.
Чертеж в разрезе кристаллизатора для центробежного литья.
Чертеж в разрезе кристаллизатора для центробежного литья показан на рисунке 4. Форма имеет цилиндрический образец литья шириной 40 мм и диаметром 22,8 мм. Цилиндрический стержень шириной 15 мм и диаметром 12 мм также прикреплен к форме, как показано на рисунке 4. Поскольку изготовленные FGM могут быть применены к шлифовальному кругу для механической обработки, как описано в разделе 3, требуются эти шаблон и стержень.Использовали частицы Cu дендритной формы со средним диаметром приблизительно 22 мкм и алмазные частицы 100/120 меш (149 мкм в JIS B 4130). Обе частицы были смешаны в ступке. Объемная доля алмаза по отношению к Cu была выбрана равной 25 об.%. Смешанный порошок был помещен в форму, как показано на рисунке 4. Затем расплавленная Cu была отлита в форму для прядения путем приложения центробежной силы с помощью вакуумно-центробежной литейной машины в вакууме при 1473 K и 1573 K. Форма вращалась в течение 99 с. .Расчетное приложенное число G (отношение центробежной силы к силе тяжести) в верхней части формы в направлении центробежной силы составило около 36 G.
Рис. 5.
Cu / алмазные FGM, изготовленные центробежным методом смешанного порошка. Температуры литья составляли 1473 К (а) и 1573 К (б) [13].
На рис. 5 показаны FGM Cu / алмаз, отлитые при 1473 K (рис. 5a) и 1573 K (рис. 5b) [13]. Поскольку эти образцы были изготовлены для использования в качестве шлифовального круга, эти литые образцы имеют выемки для крепления шкива.Было замечено, что консолидированная область смешанного порошка продолжала наклоняться к правой стороне отлитого образца, то есть к положению максимальной центробежной силы, как показано на рисунке 5. Поскольку плотность алмаза (3,52 Мг / м 3 ) была меньше чем у расплавленной меди (8,00 мг / м 3 ), небольшое количество алмазных частиц было распределено по поверхности со стороны литника из-за потока расплавленного металла. Эта разница в плотности между алмазом и медью должна создавать ступенчатую структуру.
Рисунок 6.
Композиционное изображение в отраженных электронах, показывающее поперечное сечение образца литого гранулированного алмаза на основе меди, полученного центробежным методом смешанного порошка [13].
Наблюдения поперечных сечений были выполнены с помощью сканирующего электронного микроскопа (SEM) для изучения характеристик дисперсии алмаза после литья при 1473 К. На рис. полый шкив [13].Частицы алмаза отличались от матрицы Cu по окрашенной в черный цвет области в образце. Следует отметить, что распределение алмазных частиц во внутренней части литого образца также смещено к верхней стороне (правой стороне), как показано на рисунке 6. Также было подтверждено, что явных следов или границ частиц Cu не наблюдалось, хотя вокруг некоторых алмазных частиц были видны пустоты. Таким образом, частицы Cu в предварительно разработанном смешанном порошке были полностью расплавлены и сплавились друг с другом за счет теплопередачи от разлитой расплавленной меди.
Рис. 7.
Количество алмазных частиц как функция расстояния от вершины литого образца Cu / алмаз [13].
Рис. 8.
Диаметр частицы как функция расстояния от вершины литого образца Cu / алмаз [13].
Были измерены количество алмазных частиц и средний диаметр алмазных частиц в каждой разделенной области вдоль направления центробежной силы. Результаты показаны на рисунках 7 и 8 соответственно. Эти данные были взяты из изображения поперечного сечения отлитого образца, как показано на рисунке 6.На Рисунке 7 количество алмазных частиц было резко уменьшено примерно на 3 мм от верха, где смешанный порошок был вставлен перед центробежным литьем. Результат показывает, что смешанный порошок был сжат и иммобилизован давлением расплавленного металла из-за центробежной силы. В то время как частицы алмаза были в достаточной мере иммобилизованы частицами меди между частицами алмаза, было успешно получено постепенное распределение частиц алмаза. В пределах плотно диспергированной области алмазных частиц между 0 и 3 мм от верха литого образца Cu / алмаз количество алмазных частиц увеличивалось по мере приближения к верху литого образца Cu / алмаз.Таким образом, Cu / алмазные FGM были успешно изготовлены центробежным порошковым методом. С другой стороны, распределение диаметров частиц от 0 до 3 мм почти однородно, как показано на рисунке 8. Средние диаметры алмазных частиц в этом диапазоне составляют 80–100 мкм. На расстоянии от верха от 3 до 5 мм распределение частиц по диаметру также однородное. Однако средний диаметр алмазных частиц в этом диапазоне составляет 30–40 мкм. Эти результаты могут свидетельствовать о том, что столкновение расплавленного металла Cu со смешанным порошком на поверхности области порошка смыло часть алмазных частиц, а поток расплавленной меди направил их на поверхность на стороне литника.Это явление не подходит для производства КО. Чтобы решить эту проблему, в следующем разделе описан модифицированный метод обработки.
2.2. Центробежный метод спеченного литья
В этом разделе показан метод центробежного спеченного литья, который является последним методом обработки FGM с металлической матрицей, разработанным нашей исследовательской группой. Центробежный метод спеченного литья представляет собой модифицированную технологию центробежного смешанного порошкового метода. В методе центробежного спекания FGM обрабатываются путем сочетания центробежного спекания и центробежного литья [16, 17].Как описано в разделе 2.1, центробежный метод смешанного порошка позволяет нам изготавливать FGM с металлической матрицей. В частности, центробежный метод смешанного порошка является эффективным способом изготовления FGM с металлической матрицей, армированных наночастицами [12]. Однако предварительно разработанные порошковые смеси имели тенденцию стекать во время центробежного литья в случае некоторых комбинаций порошков в центробежном методе смешанного порошка. В качестве попытки преодолеть эту проблему был разработан метод центробежного спекания, сочетающий центробежное спекание и центробежное литье.
Рис. 9.
Схематическое изображение, показывающее процесс центробежного спеченного литья [17].
На рис. 9 схематически показан процесс центробежного спеченного литья [17]. В методе центробежного спеченного литья заготовку с металлической матрицей в форме кольца с дисперсными частицами сначала получают центробежным спеканием. Предварительно разработанный смешанный порошок частиц дисперсии и частиц металлической матрицы помещается в прядильную форму, как показано на рисунке 9 (а).В принципе, температура плавления частиц дисперсии должна быть выше, чем у частиц с металлической матрицей, чтобы также могли формироваться FGM в этом методе. Затем смешанный порошок спекается под действием центробежной силы с помощью нагревательных спиралей для изготовления преформы, как показано на рисунке 9 (b). Затем расплавленную металлическую матрицу выливают в изготовленную преформу посредством центробежного литья для получения FGM с металлической матрицей, как показано на рисунке 9 (c). Матрица расплавленного металла проникает в пространство между частицами под действием приложенной центробежной силы, как показано на Рисунке 9 (d).В то же время частицы металлической матрицы плавятся под воздействием тепла расплавленной металлической матрицы. Наконец, можно получить кольцевые или дискообразные FGM с диспергированными частицами, распределенными во внешней части образцов, как показано на рисунке 9 (e).
В наших предыдущих исследованиях Al – Si и Cu были выбраны в качестве металлической матрицы для изготовления FGM Al – Si сплав / алмаз и Cu / алмаз соответственно [16,17]. Частицы сплава Al – Si и частицы Cu равномерно смешивались с частицами алмаза соответственно. Объемная доля алмазных частиц в смешанном порошке была выбрана равной 10 об.%. Предварительно сконструированный смешанный порошок помещали в цилиндрическую форму, имеющую ось вращения диаметром 20 мм и длиной 30 мм соответственно. Смешанные порошки спекались во вращающейся цилиндрической форме под действием центробежной силы около 280 Гс при 843 К в атмосфере аргона для частиц сплава Al – Si / алмаза [16] и 1100 Гс при 1273 К в вакууме для частиц Cu / алмаза [17]. ] соответственно. Затем было выполнено центробежное литье под действием центробежной силы около 78 G при 1373 K с разливкой расплавленного алюминия в случае заготовки из сплава Al – Si / алмаза [16].Таким же образом расплав Cu заливали в заготовку Cu / алмаз в пресс-форме под действием центробежной силы около 34 G при 1393 K [17].
Рис. 10.
Макрофотографии FGM на основе сплава Al – Si (а) и Cu (б) с диспергированными частицами алмаза, изготовленными методом центробежного спеченного литья, и изображения СЭМ, показывающие микроструктуру внешней части отливки. образцы [16, 17].
На рисунке 10 показаны макрофотографии сплавов Al – Si и FGM на основе Cu с дисперсными частицами алмаза, изготовленных методом центробежного спеченного литья.СЭМ-изображения, показывающие микроструктуру внешней части сплава Al-Si и FGM на основе Cu, также показаны на рисунке 10. Следует отметить, что частицы алмаза были распределены только на внешней части литых образцов, как показано на рисунке 10. Метод центробежного спеченного литья — эффективный способ изготовления FGM с металлической матрицей.
.Узнайте о изготовлении пресс-форм и литье для конкретного приложения
Выберите категорию ниже
Изготовление дисплеев для тематических парков, зоопарков, аквариумов и т. Д.
Методы восстановления старых или создания новых архитектурных элементов.
Уретановая и силиконовая резина Smooth-On используется для изготовления свечей
Изготавливает формы для мокрого литья, опалубки, штампы для бетона, а также декоративные конструкции и панели из стеклопласта.
Гладкие материалы для косплея.
Создавайте дисплеи для розничной торговли, театра или даже дома, а также обучающие материалы по инкапсуляции солнечных элементов.
Smooth-On предлагает самый широкий в отрасли выбор материалов с огнестойкостью.
Сделайте индивидуальную форму для конфет или льда, даже для шоколада, помадки или торта.
Проекты, которые можно выполнять дома для развлечения, учебы или ремонта дома.
Выполняйте ремонт, воссоздайте детали или создавайте собственные детали для прототипов или производственных приложений.
Использование машин или систем распыления для изготовления форм для литья бетона, архитектурной реставрации и т. Д.
Точно и безопасно снимайте и воспроизводите детали человеческого тела.
Техника создания профессиональных эффектов макияжа для кино, телевидения, театра и многого другого.
Сделайте свои собственные медицинские учебные пособия или различные нестандартные и стандартные протезы и ортопедии.
Создавайте формы, которые улавливают очень мелкие детали вплоть до «отпечатка пальца» для получения точных копий.
Создавайте битое стекло, реалистичный реквизит и другие спецэффекты.
Методы превращения вашей идеи в трехмерное физическое представление.
Создавайте или делайте точные копии оригинальных скульптур и произведений искусства.
Применение распыляемых материалов и оборудования.
Каучуки, пластмассы, пена, пигменты и т.д. для реалистичного воспроизведения дикой природы.
Использование силикона для создания многоразовых вакуумных пакетов для композитных материалов.
Формы для каучуков и литейных материалов, используемые для создания уникальных произведений искусства из натурального дерева.
.