Литье пластмасс в домашних условиях – изготовление матриц и пресс форм
В настоящее время популярными стали изделия из пластмассы. Пользоваться ими удобно и практично. Литье пластмассы в домашних условиях – это хорошая идея для открытия своего бизнеса или просто для свободного времяпрепровождения. Хорошо сделанные изделия элегантно и интересно смотрятся, а также их просто содержать в порядке.
Помимо этого, они обладают необходимой прочностью. Чтобы наладить производство такого рода на территории частного владения, необходимо усвоить пару простых правил.
Подготовка материала
В первую очередь необходимо найти пластиковый лом, для изготовления будущего изделия. Это не проблема, так как такого сырья в современном мире огромное количество сломанных вещей, бутылок и другого лома из пластика.
Лом пластиковых ящиков
Однако, необходимо учесть тот факт, что каждый вид пластмассы отличается своим температурным режимом плавления.
Именно поэтому для литья конкретного изделия необходим один вид лома. Смешение нескольких разновидностей изделий из пластмассы даже при изучении его температуры плавления, при отливе часто провоцирует появление пузырьков в продукции.
Лучшим вариантом в таком случае является купить жидкую пластмассу в магазине или заменить ее на диоксидную смолу, это позволит получить качественное изделие, которое прослужит долго. А также дополнительно понадобится ряд вспомогательных средств:
- емкость для плавки;
- силикон;
- литол.
Пары пластмассы ядовиты, они обладают высокой токсичностью. Необходимо соблюдать осторожность при изготовлении изделий в домашних условиях.
Форма
Для приготовления изделия в домашних условиях, прежде всего, необходимо соорудить модель. В первую очередь следует определиться с материалом для изготовления пресс формы. Для этого подойдут следующие материалы:
- дерево;
- пластилин;
- гипс и другие.
Затем следует пройти изготовление матриц для литья, которые и будут непосредственно использоваться для отлива. Форму необходимо обмазать литолом или любой другой смазкой.
Если выбор пал на силиконовые формы, то необходимо учесть, что это вещество работает с коэффициентом более 200%. А также необходимо обратить внимание на его вязкость, чем она меньше, тем точнее получится пресс форма.
Форма для литья силиконовая
Заливка детали
Литье пластиков своими руками напрямую зависит от того материала, который мастера выбрали для изготовления будущей конструкции.
Смолы и жидкие пластмассы хорошо подойдут для приготовления, но они обладают различной степенью вязкость у них, поэтому прослужат они разное время. Все параметры следует изучить в инструкции при покупке.
Существуют рецепты приготовления пасты в домашних условиях, они требуют от мастера щепетильности и скрупулезности во время формирования состава сырья. Для изготовления материала, следует смешать 5 частей мелких опилок с 2 частями талька. Залить массу столярным клеем (его консистенция обязана отвечать состоянию сметаны).
Все тщательно перемешивается для получения теста одной консистенции.
Есть еще один хитрый ход: следует добавить 0,5 части алюминиевых квасцов, они предотвратят появление плесени на тесте, а пластичность при этом увеличивается в несколько раз.
Процесс приготовления теста для литья своими руками трудоемкий, он требует отличных знаний по этой теме. Именно поэтому многие начинающие заливщики, отдают свое предпочтение готовым смесям.
Литье пластмассы в домашних условиях
Ход работы
Отливка происходит в несколько этапов:
- Необходимо взять пресс-форму и тщательно ее очистить. После предварительной подготовки она обязана быть полностью очищенной и высушенной. Все остатки материала после подготовительных мероприятий необходимо убрать.
- Если необходимо придать будущему изделию оттенок, необходимо добавить в состав для литья пару капель краски.
Водяные краски для этого не подходят.
- Подготовительная дегазация смеси не требуется. Все дело в том, что в домашних условиях продолжительность функционирования невелика. А чтобы удалить лишние пузырьки воздуха из небольших изделий, придется приложить силу давлением и убрать их самостоятельно.
- Аккуратно перемешайте состав для заливки и заполните пресс-форму шаблона.
- Заливается все медленно небольшой струйкой.
- Смесь заливается до полного заполнения объема, задевая небольшой участок доли канала для литья. Дело в том, что после дегазации, объем материала уменьшится и станет необходимый для литья.
- Заключительный этап – охлаждение будущей конструкции.
Пластик заливается в форму после чего ему нужно дать постепенно остыть
Для получения качественного изделия шаблон необходимо остужать постепенно.
Бизнес-идеи
Если мелкий производитель решил выйти на широкий масштаб производства, стоит задуматься об открытии собственного дела.
Попробовав свои силы на дому, следует составить бизнес-план, зарегистрироваться, как индивидуальный предприниматель и начать воплощение своей мечты в реальность.
Но покупка оборудования не обойдет предпринимателя стороной. Да и тяжело отливать формы для производства массы изделий собственноручно. Необходимо готовить первые изделия и продавать их, а на полученные средства купить определенный станок для литья пластмасс, пресс.
Как сделать процесс литья пластмассы прибыльным в своем регионе? Семь простых правил отливки позволят приготовить качественное изделие, которое будет интересно смотреться, а также радовать глаз. А со временем предприниматели смогут задаться вопросом о расширении своих навыков и обустройстве личного бизнеса.
Видео: Литье пластмассы в домашних условиях
Оборудование для литья в оболочковые формы
Содержание страницы
Что такое литье в оболочковые формы
Такое название получил в нашей стране способ, запатентованный в 1943 г. в Германии И. Кронингом (отсюда распространенное за рубежом название «кронинг-процесс»). Данный способ входит в группу методов литья в разовые разъемные формы и позволяет получать отливки с толщиной стенки 3…15 мм и массой 0,25…300 кг из чугуна, стали и цветных металлов. Этим способом получают ответственные детали машин — коленчатые и кулачковые валы, шатуны, ребристые цилиндры и т п. (Rz = 80…40 мкм, точность — 12-14-й квалитет). Процессы изготовления оболочек легко поддаются автоматизации. Оболочковые формы и стержни производят на автоматических машинах и автоматических линиях.
Тонкостенные (толщина стенки 5…20 мм) формы изготовляют из песчано-смоляной смеси: мелкозернистого кварцевого песка или другого огнеупорного зернистого материала и термореактивной синтетической смолы (3…7 %). В качестве связующего чаще всего используют фенолформальдегидные смолы (СФ-12, СФ-15 и др.) с добавкой уротропина в количестве 8… 12 % от содержания смолы. Песчано-смоляную смесь готовят перемешиванием песка и измельченной порошкообразной смолы с добавкой растворителя (холодный способ) или при температуре 100… 120 °C (горячий способ), в результате чего смола обволакивает (плакирует) зерна песка. Затем комки смеси дополнительно дробятся до получения отдельных зерен, плакированных смолой, смесь загружается в бункер. Формовка производится по металлическим моделям.
Оболочковая форма состоит из двух полуформ с горизонтальной или вертикальной плоскостью разъема. Процесс изготовления оболочек из песчано-смоляной термореактивной смеси включает в себя следующие последовательные операции (рис. 1):
- Металлическая модельная плита очищается, на нее пульверизатором наносится разделительный состав, облегчающий снятие оболочки.
- Модельная плита нагревается в электрической печи до температуры 200…220 °C.
- Плита 2 устанавливается над бункером 1 моделью вниз и закрепляется (рис. 1, я). Бункер переворачивают на 180°, и формовочная смесь 3 падает на нагретую модельную плиту (рис. 1, б). При выдержке в течение 20…30 с смола плавится и, обволакивая тонкой пленкой мелкие зерна песка, образует оболочку толщиной 8 мм.
- Бункер возвращают в исходное положение, и непрореагировавшая формовочная смесь падает на его дно (рис.
1, в).
- Снятую с бункера модельную плиту с непрочной оболочкой отправляют в электрическую печь, где нагревают до температуры 400 °C. Здесь смола в течение 90… 180 с полимеризуется и необратимо твердеет, образуя прочную оболочковую полуформу.
- Готовая оболочковая полуформа 4 снимается (рис. 1, г). с модельной плиты 6.с помощью толкателей 5.
- По такой же технологии изготавливают вторую полуформу.
- Стержни 8 формуют в нагретых стержневых ящиках 7 (рис. 1, д) центробежным способом (можно еще и свободной засыпкой, бункерным и.пескодувным способами).
- В одной из полуформ 9 (рис. 1,. е) на стержневые знаки устанавливают стержень, закрывают второй полуформой, скрепляют их скобами, струбцинами или склеивают по плоскости разъема.
- Собранную оболочковую форму 10 помещают в металлический ящик, засыпают крупным песком или чугунной дробью и заливают металлом. К моменту полной кристаллизации металла отливки смола из смеси выгорает, форма и стержни разупрочняются и легко разрушаются, освобождая отливку 11 при выбивке (рис.
1, ж).
Рис. 1. Схема процесса литья в оболочковую форму
При производстве форм и стержней применяют три вида оборудования:
- для приготовления песчано-смоляных смесей;
- для изготовления форм и стержней;
- для склеивания полуформ.
Для приготовления смесей применяют все типы смесителей. Они должны обеспечивать получение однородных смесей при отсутствии нагрева. Приготовление плакированных смесей, при котором требуется подогрев, можно производить любыми смесителями с устройствами для дальнейшего охлаждения готовой смеси.
Рис. 2. Конструкция типовой модельной плиты
1. Модельное оборудование подготовки кокильного литья
У типовой модельной плиты для литья в оболочковые формы (рис. 2) металлические модели крепятся к плите 9. Прижимная плита 12 объединяет элементы конструкции в одно целое. Плита выталкивателей 13 удерживает выталкиватели 6 и 11, которые крепятся гайками 2 и 3, а также возвратные пружины 16, упоры 14. Планки торцевые 15 и боковые 1 ограничивают полуформу по периметру и предотвращают отслаивание незатвердевшей оболочки при подъеме с бункера; они крепятся винтами 5. Модели фиксаторов — центрирующих выступов 10 и углублений 7 — запрессованы в плиту 9. В плиту встраиваются трубки охлаждения 4 и термопара 8.
Оборудование для изготовления форм и стержней бывает одно- и многопозиционным, ручным, механизированным и автоматическим с различной производительностью. Подача формовочной смеси может выполняться несколькими методами. Пескодувный метод заполнения формы и уплотнения песчано-смоляной смеси является лучшим.
Схема пескострельной головки приведена на рис. 3. Стержневой ящик 10 устанавливают на столе 1, который, поднимаясь, прижимает его к надувной плите 3. Сжатый воздух из резервуара 7 через резко открываемый дутьевой клапан 8 поступает в песко- стрельный резервуар б, отчего давление в нем мгновенно повышается и воздух, ударно действуя на порцию песчано-смоляной смеси, выталкивает ее через конусную насадку 2 в нагретый стержневой ящик, благодаря чему в нем формируется и затвердевает стержень. Поступающий через прорези 5 на боковой поверхности гильзы сжатый воздух уменьшает трение смеси о стенки резервуара 6. Избыточный воздух из ящика 10 выходит через щелевидные отверстия 9, предусматриваемые в надувной плите или в ящике. Насадки 4 подбирают в зависимости от конфигурации и стержневого ящика.
Рис. 3. Схема пескострельной головки
2. Машины для кокильного литья
Однопозиционную полуавтоматическую пескодувную машину (рис. 4) применяют для изготовления стержней в нагреваемых ящиках размером до 700 х 550 х х 350 мм с вертикальным разъемом в цехах серийного и массового производства. Части нагреваемого стержневого ящика 7 соединяются с помощью цилиндра 2. На ящик при срабатывании цилиндра 3 опускается надувная головка 4, с помощью цилиндра 5 открывается шиберная заслонка, и песчано-смоляная смесь из бункера 6, находящегося в момент надува под давлением, по трубопроводу 7 заполняет рабочую полость ящика. Система отсоса 8 удаляет излишки песчано-смоляной смеси по трубопроводу 9 через сито 10 в приемный бункер 11. По окончании отвердевания стержня в момент раскрытия стержневого ящика срабатывают толкательная система и стержень. Предварительно просеянная песчано-смоляная смесь автоматически загружается в бункер 6. Температура нагрева стержневого ящика и выдержка после заполнения смесью и отвердевания обеспечивается автоматически.
Рис. 4. Схема пескодувных машин моделей 91873, 91874, 91875
В двухпозиционной машине УКФ-2 (рис. 5) для изготовления оболочковых форм механизированы основные трудоемкие операции и контроль технологических параметров процесса (температура нагрева, выдержка модельного комплекта под смесью, отверждение оболочек, их снятие с модели). Машина имеет электрические печи 2 и 5, смонтированные на общей станине 1. Печи закрываются автоматическими заслонками 6. Посередине смонтирован поворотный бункер 8 для формовочной смеси с поворотным механизмом 9, работающим от пневмоцилиндров. С обеих сторон от бункера находятся два стола для съема готовых оболочек.
Рис. 5. Двухпозиционная машина УКФ-2 для производства оболочковых форм
Съем производится с помощью управляемых ножными пневмокранами 10 пневмогидравлических цилиндров 7. Модельная плита над бункером повачивается пневматическим подъемником 4. Машина закрыта общим вытяжным кожухом 3.
Производительность. машины — 40 полуформ в час при размерах плит 400.×.600 мм. Вместимость бункера — 80 кг.
Пневмосхема машины УКФ-2 приведена на рис. 6. Сжатый воздух поступает из магистрали через влагоотделитель 16 и масло- уловитель 17 к пневмоэлектрическому крану 25, который. подает его к.сдвоенным пневмоцилиндрам 9 и 23, поворачивающим бункер на 180° и обратно.(поворот осуществляется рейками, находящимися на штоке цилиндров, и зубчатым колесом, укрепленным на оси бункера).
Рис. 6. Пневматическая схема машины УКФ-2 для производства оболочковых форм
Краном 25 управляют с.помощью кнопок «Пуск» и «Стоп» на пульте Одновременно сжатый воздух поступает к ножным пневмокранам 21 и 26, поднимающим плиту с толкателями 6, возвращаемую в. исходное положение пружинами 7 в левой части машины, и плиту 11 с пружинами 12 в правой части. Через ресивер 24 и кнопочный кран 22 осуществляется работа пневмосъемника 8, поворачивающего модельную плиту над бункером 10. Пневмокраны двойного действия 15 и 3 питают цилиндры 14 и 4, перемещающие модельные плиты из зоны бункера в электропечи. Одноходовые краны 1 и 19 питают пневмоцилиндры 2 и 20, которые поднимают заслонки 5 и 13 электропечей. Давление воздуха в магистрали контролируется манометром 18.
Для склеивания оболочковых полуформ и стержней используются устройства, сдавливающие полуформы по контуру клеевого шва с помощью пневмоцилиндров, пружин, пневматической диафрагмы. Пресс для склеивания с помощью пружин (рис. 7) имеет станину 8 с двумя стойками 12, стол 7, подвижную траверсу 3, неподвижную траверсу 2 с пневмоцилиндром 1, откидной стол 5 и пневмокраны 10 и 9 для управления прессом. Стол и подвижная траверса имеют сменные штыри 6 и 4 с пружинами, между которыми зажата оболочковая форма при склеивании. К штырям 4 подвижной траверсы присоединены резиновые шланги для подачи к местам склейки углекислого газа. Штыри в подвижную траверсу устанавливают согласно контуру склеиваемой формы.
Рис. 7. Пресс для склеивания оболочковых полуформ
Стол 7 за рукоятку 11 выводят из-под подвижной траверсы. На пружины штырей стола кладут половину формы со стержнями, затем на поверхность склеивания наносят слой жидкого стекла и накладывают верхнюю половину формы. Стол с собранной формой подводят под подвижную траверсу, которая, опускаясь, сжимает оболочковую форму. Краном 10 включают подачу углекислого газа, продувка его продолжается 15…30 с. Поворотом крана 9 подвижную траверсу отводят в исходное положение, выдвигают стол и снимают с него склеенную форму. Производительность пресса — 80 форм в час при габаритных размерах склеиваемых форм 400 х 500 мм и давлении воздуха в сети привода 0,5…0,6 МПа.
Просмотров: 652
Статья Конструкция и виды пресс форм
Конструкция и виды пресс форм
Пресс-форма для литья пластмасс под давлением представляет из себя довольно сложное устройство, эксплуатируемое в условиях нагрузок в сотни тонн, циклических перепадов температуры на сотни градусов, испытывающее воздействие агрессивных веществ, выделяющихся из пластика. При этом, для получения качественной отливки, точность примыкания формообразующих деталей формы, должна составлять сотые доли миллиметра. Для выполнения этих довольно жестких требований, разработчиками и изготовителями пресс-форм было выработано множество типовых конструктивных решений, упрощающих и ускоряющих процесс производства.
При всем многообразии существующих видов и конструкций пресс-форм, можно выделить несколько их основных видов. Однако прежде чем перейти к их рассмотрению, договоримся о терминах.
Определения
Пресс-форма — это устройство для литья под давлением объёмных деталей из полимеров, резин и других материалов.
Пуансон – подвижная деталь пресс-формы, передающая давление на формуемый материал. Пуансон, как правило, имеет выступы, оформляющие внутреннюю поверхность изделия. Поскольку деталь в процессе охлаждения усаживается и обжимает эти выступы, съём готового изделия после раскрытия формы осуществляется чаще всего с пуансона.
Матрицей называется неподвижная часть пресс-формы, обычно имеющая впадины и оформляющая наружную поверхность детали. Подача материала в полость формы осуществляется через канал в матрице — литниковую втулку.
Формообразующая или формующая полость – полость между матрицей и пуансоном для загрузки материала, повторяющая собой форму будущей детали.
Линия разъема – поверхность смыкания пуансона и матрицы. В простых пресс-формах линия разъема представляет собой плоскость, а в сложных состоит из одной или нескольких сложных поверхностей, образуемых пуансоном, матрицей и другими подвижными элементами формы.
Двухплитные пресс-формы
Самым простым и одновременно самым распространенным типом пресс-формы является холодноканальная форма с двумя плитами.
На рисунке показана пресс-форма с центральным литниковым каналом, обеспечивающим прохождение расплавленного материала от узла впрыска до разводящего литника, проходящего по линии разъёма. Из разводящего литника расплав попадает непосредственно в формующую полость. В самом простом случае разводящий литник в пресс-форме может отсутствовать, а материал из литниковой втулки — подаваться непосредственно в полость. Изделия, полученные на таких пресс-формах легко определить по крупному круглому срезу — следу обрезки «морковки» литника, обычно расположенному в самом центре детали.
Представленная пресс-форма имеет одну плоскую линию разъёма, которая размыкается в каждом цикле литья для извлечения изделия и удаления литника. Извлечение изделия и отделение литников обеспечивается толкающей системой пресс-формы, состоящей из плиты толкателей, плиты хвостовика и множества отдельных толкателей. Толкатели бывают различной формы, но самые распространенные — цилиндрические. Круглые следы от них можно увидеть на внутренней поверхности большинства пластмассовых деталей.
Рабочие части пресс-формы — пуансон, матрица и различные вставки, называемые также «знаки», определяют конфигурацию отливаемой детали. Части формы, составляющие собой её каркас, называются несущими, или опорными плитами. Несмотря на то, что эти плиты должны выдерживать циклические нагрузки в сотни, а иногда и в тысячи тонн, они изготавливаются из более мягкого металла, по сравнению с рабочими частями формы. Это позволяет удешевить пресс-форму и упростить её изготовление.
Важным элементом конструкции формы является её теплообменник. По существу теплообменник — это множество круглых отвестий сложной конфигурации, пронизывающих плиты и рабочие части пресс-формы. Вода, пропускаемая через эти каналы, обеспечивает быстрое и равномерное охлаждение детали в формующей полости.
Трёхплитные пресс-формы
Трехплитная форма обладает двумя линиями разъёма, одна из которых служит для освобождения детали, а другая, параллельная основной — для извлечения застывшего литника. Такая конструкция позволяет усложнить разводящий литник и осуществлять впрыск не только по периметру, но и в любой точке формующей плоскости. При этом точка впрыска может иметь диаметр около одного миллиметра, а разводящий литник отделяется автоматически при раскрытии формы.
В форме, показанной на рисунке, цикл съёма начинается с открытия формы по первой линии разъёма, проходящей между плитой пуансона и матрицы. При этом разводящий литник отрывается от детали. После того, как деталь полностью освобождена, начинается раскрытие второй линии разъёма с извлечением литника.
В приведенной на рисунке пресс-форме, снятие отливки с пуансона производится плитой съёма. Такой метод применяется в случаях, когда наличие на детали следов толкателей недопустимо, или если необходимо обеспечить равномерное распределение усилия сталкивания.
Горячеканальные формы
В холодноканальных пресс-формах литник в каждом цикле должен быть остужен и в твердом виде выталкнут вместе с отливками, чтобы потом отправиться на измельчение и вторичную переработку. В горячеканальных же формах литниковая система снабжена электронагревателем, который постоянно поддерживает материал в расплавленном состоянии. Литник теперь не нужно извлекать, а значит сокращается время охлаждения формы и уменьшается объем отходов материала.
Литниковая система горячеканальных форм включает в себя два основных элемента – разводящие коллекторы и систему сопел. Коллектор системы, расположенный в плите матрицы, доставляет расплавленный материал от сопла литьевой машины к соплам. Сопла подают материал прямо в формующую полость или в холодный разводящий литник, аналогичный по конструкции с литником двухплитной формы.
Конструктивное исполнение ключевых элементов горячеканальной системы — коллектора и сопел весьма разнообразно. Поскольку эти элементы довольно часто выходят из строя, изготовители пресс-форм стараются использовать стандартные модели от специализированных производителей, а не изготавливать их самостоятельно.
Конструкция горячеканальной формы похожа на трехплитную, во второй линии разъема которой расположился коллектор горячего канала. Для управления нагревательными элементами используется специальный контроллер.
Пресс формы для пластмасс и полимеров — конструкция и виды пресс форм | ПластЭксперт
1. Введение Форма для литья пластмасс под давлением (формующая оснастка, пресс формы) – основной элемент оборудования, определяющий конструкцию и качество готового полимерного изделия.


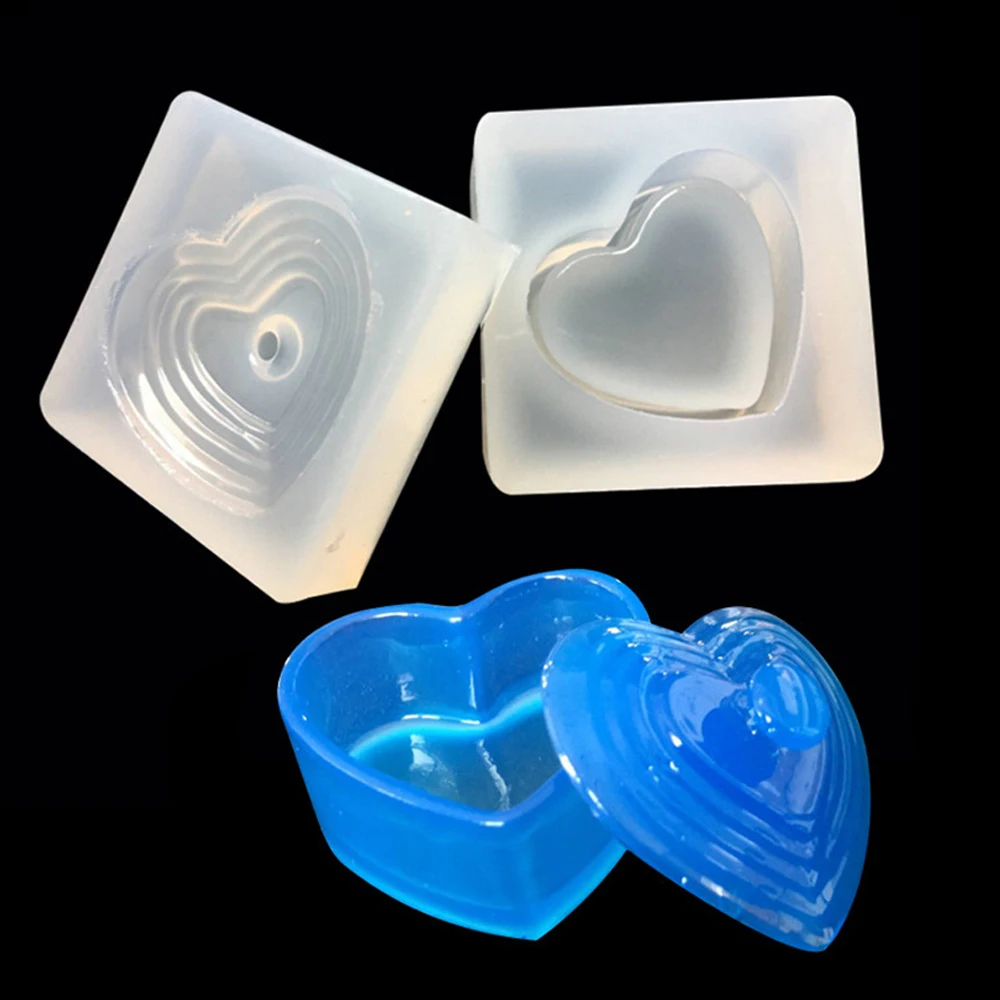
4. Основные этапы проектирования прессформы для литья пластмасс. Проектирование пресс формы обычно включает в себя четыре основных этапа.
- На первом этапе оцениваются технологические требования к форме и производится подробный анализ технологичности деталей изделия. В случае необходимости вносятся изменения в конструкцию изделия и осуществляется согласование с заказчиком. Разрабатываются трехмерные модели и чертежи изделий.
- На втором этапе производится оптимизация размещения деталей в оснастке для достижения наибольшей технико-экономической целесообразности.
- На третьем этапе производится оптимизация конструкции литниковой холодно- или горячеканальной системы и системы охлаждения прессформы. Современное программное обеспечение, используемое конструкторами, позволяют в кратчайшие сроки и с большой точностью выполнять подобного рода работы.
- Четвертый этап конструирования оснастки состоит в изготовлении комплекта документации на форму, в том числе двумерные чертежи и 3D модели, а также схемы и инструкции по работе с формой, необходимые для правильной эксплуатации литформы у заказчика.
ПластЭксперт искренно надеется, что читателям статья понравилась и они отблагодарят писателей, поделившись ею в соцсетях.
Объявления о покупке и продаже оборудования можно посмотреть на
Доске объявлений ПластЭксперт
Обсудить достоинства марок полимеров и их свойства можно на
Форуме о полимерах ПластЭксперт
Зарегистрировать свою компанию в Каталоге предприятий
Технология литья под давлением. Литьевые формы.
Паспорт литьевой формы
В паспорте отражаются данные, перечисленные ниже.
1) Оглавление и характеристики отливок литьевой формы.
Обозначение и наименование изделия, шифр и индекс литьевой формы. Фирма-изготовитель.
Материал изделия, масса детали, отливки, литников.
2) Характеристики технологических параметров процесса, марка и тип термопластавтомата, температура, давление, время, наличие каскадного впрыска и т. д.
Кроме того указывается тип применяемых смазок.
3) Регистрация проводимых доводок и ремонтов формы.
Что делали, дата поломки/ремонта, наработка деталей.
В разделе профилактического ремонта указываются плановые сроки обслуживания (подпись ответственного).
4) Учет стойкости литьевой формы. Сколько деталей наработали в месяц, год.
5) Финальная запись – причина списания литьевой формы.
Основные действия при эксплуатации литьевой формы
- Снятие консервирующей смазки с ФОД при запуске
- Визуальный осмотр ФОД на наличие задиров, забоин, наклепа замка; при наличии закладных знаков необходимо проверить наличие люфтов, других повреждений.
- Визуальный осмотр шлангов и мест соединений на наличие протечек охлаждающей жидкости
- Чистка и нанесение на направляющие элементы, колонки, втулки, толкатели, ползунов и др. движущихся элементов литьевой формы консистентной смазки
- Очистка вентиляционных каналов, выпоров
- В случае необходимости нанесение антиадгезионной смазки на ФОД
- Проверка креплений формы (подтяжка болтов на прижимах, проверка соосности)
Различия форм с внешним и внутренним обогревом
Недостатки внутреннего обогрева
- Ограничение размера горячеканальной системы (ГКС)
- Не подходит для термочувствительных полимеров
- Не подходит при частой замене цвета
- Имеет ограничения при балансировке свыше 8 гнезд
Достоинства внутреннего обогрева
- Отсутствие проблем с изоляцией
- Отсутствие различий в расширении
- Незначительные энергозатраты
- Слабое влияние температуры литьевой формы
- Стабильность работы формы
Недостатки внешнего обогрева
- Требуется увеличение установленной мощности
- Для стабильности работы литьевой формы требуются значительные ресурсы
Достоинства внешнего обогрева
- Точное поперечное сечение пути
- Малые падения давления
- Быстрый переход при смене материала и замене цвета
- Стабильное равновесие впрыска даже при многократном увеличении
Определение температуры расплава
Материал | Температура по зонам, °C | Темп-ра литьевой формы, °C | ||||
Сопло | Зона 3 | Зона 2 | Зона 1 | Зона подачи | ||
ПП | 240-300 | 240-300 | 210-250 | 150-210 | 30-50 | 20-60 |
ПС | 220-280 | 210-280 | 180-230 | 150-200 | 30-50 | 15-50 |
ПЭНП | 220-270 | 220-270 | 160-230 | 140-180 | 30-50 | 20-60 |
ПЭВП | 220-290 | 220-290 | 160-260 | 140-200 | 30-50 | 15-60 |
АБС | 220-250 | 220-250 | 180-220 | 150-180 | 40-60 | 40-70 |
ПОМ | 200-220 | 200-220 | 180-205 | 150-180 | 30-50 | 60-110 |
ПК | 280-320 | 280-320 | 260-300 | 230-270 | 70-90 | 80-110 |
ПБТ | 250-270 | 250-270 | 240-250 | 230-250 | 60-80 | 60-100 |
ПА 6 | 240-260 | 240-260 | 230-250 | 220-240 | 60-80 | 60-90 |
ПА 66 | 260-300 | 260-300 | 240-280 | 230-250 | 60-80 | 60-90 |
Время стабильности расплава
Tвр.=tцикл · Vм.о · k1 · k2Vиз
Tвр. — время пребывания материала в цилиндре, с/p>
Vм.о — максимальный объем цилиндра, см3
k1 — корректирующий коэффициент соотношения длины шнека к максимальному объему
k2 — корректирующий коэффициент плотности материала
tцикл — время цикла литья, с
Влияние давления выдержки
Слишком низкое давление выдержки вызывает следующие последствия:
- Утяжины на поверхности изделия
- Большая усадка
- Образование вакуолей
- Нестабильные размеры
- Нарушение ориентации макромолекул из-за обратного потока
- Малый вес изделия
Слишком высокое давление выдержки влечет:
- Появление облоя
- Переуплотнение изделия
- Проблемы при извлечении из формы
- Нестабильные размеры
- Повышение внутренних напряжений
- Небольшая усадка
- Ухудшение поверхности в зоне литника
- Повреждение литьевой формы
Преимущества холодноканальных литьевых форм
- Сравнительно невысокая стоимость
- Относительно простая конструкция
- Простое обслуживание в процессе эксплуатации
- Невысокая стоимость ремонтно-восстановительных работ
- Универсальность по виду перерабатываемых полимеров
Недостатки холодноканальных литьевых форм
- Образование отходов пластика
- Дополнительные операции по удалению ледников
- Особенности параметров настройки TПА
Достоинства горячеканальной системы
- Отсутствие литниковых отходов и операций, связанных с их удалением и утилизацией
- Повышенное качество изделий
- Возможность получения крупных изделий с минимальной толщиной стенки
- Возможность организации многоточечного впрыска
- Возможность тонкой балансировки впрыска
- Щадящий режим по давлению литья
- Уменьшение усадки изделия
- Экономия материала
- Возможность сокращения времени впрыска
Недостатки горячеканальной системы
- Высокая стоимость литьевой формы
- Сложности в обслуживании и эксплуатации
- Необходимость дополнительного оборудования
- Увеличение габаритов литьевой формы
- Необходимость в квалифицированном персонале
- Дополнительные расходы электроэнергии
- Ограничение переработки полимеров
- Сложность замены материала.
1701 Аксессуары для 1700 Наша цена: 3,45 $ | 1730 Аксессуары для 1729 Наша цена: 3 доллара.45 | 1738 Аксессуары для 1737 Наша цена: 3,45 $ | ||
9,5 «т. | 9,5 «т. | 11 «т. | ||
1788 Accs.для 1787 года Шотландский Санта Наша цена: 3,45 $ | 3855 Рука для херувима Наша цена: 5,00 $ | Крышка TL 1285 Turtle Наша цена: 5,00 $ | ||
7 дюймов | Форма для керамики | |||
1615 Трубка и Холли за 1614 год Наша цена: 6 $.90 | 1711 Аксессуары для 1710 Наша цена: 6,90 $ | 1736 Овощи за 1734 год Наша цена: 6,90 $ | ||
12 «т. | 11 «т. | 1 «. | ||
1747 Овцы Наша цена: 6,90 $ | 1791 г.для 1790 Fantasy Santa Наша цена: 6,90 $ | 1793 г. для 1792 Мастерская Санта Наша цена: 6,90 $ | ||
3 «л. | ||||
1795 г.за 1794 г. Наша цена: 6,90 $ | 1797 г. за 1796 г. Наша цена: 6,90 $ | 1798 База для колядников 1796 Наша цена: 6,90 $ | ||
1807 г.на 1806 г. Наша цена: 6,90 $ | 1919 г. на 1918 год Наша цена: 6,90 $ | 1975 База на 1974 год Наша цена: 6,90 $ | ||
2272 Twp Пингвины Наша цена: 6 $.90 | 2902 Держатель вотива Наша цена: 7,00 $ | TL550 Книга с рукой для Opus Наша цена: 7,00 $ | ||
2,5 «т. | 1 .5 «т. | Форма для керамики подходит к TL550 B 13 «l | ||
TL713 C Руки к Almo Gnome Наша цена: 7 долларов.00 | TL721 Руки к торговцу гномом Наша цена: 7,00 $ | TL870A Голова-лягушка Наша цена: 7,00 $ | ||
Форма для керамики | Форма для керамики подходит для TL721 B 14 «t | Форма для керамики подходит для TL870 B 19 дюймов | ||
TL944A Мужской коль — руководитель Наша цена: 7 долларов.00 | Женский коль TL945A — голова Наша цена: 7,00 $ | 1913 г. на 1912 год Наша цена: 8,05 $ | ||
Форма для керамики подходит к TL944 B 17 дюймов l | Форма для керамики подходит к TL945 B 17 дюймов l | |||
1915 г. Девушка акк.на 1914 год Наша цена: 8,05 $ | 2334 Руки за 2333 Наша цена: 8,05 $ | 2640 В соотв. для 2641 Наша цена: 8,05 $ | ||
9 «т. | ||||
Лучшее литье в формы — Выгодные предложения по литью в формы от глобальных продавцов литья в формы
Отличные новости !!! Вы находитесь в нужном месте для литья в формы. К настоящему времени вы уже знаете, что что бы вы ни искали, вы обязательно найдете это на AliExpress. У нас буквально тысячи отличных продуктов во всех товарных категориях.Ищете ли вы товары высокого класса или дешевые и недорогие оптовые закупки, мы гарантируем, что он есть на AliExpress.
Вы найдете официальные магазины торговых марок наряду с небольшими независимыми продавцами со скидками, каждый из которых предлагает быструю доставку и надежные, а также удобные и безопасные способы оплаты, независимо от того, сколько вы решите потратить.
AliExpress никогда не уступит по выбору, качеству и цене.Каждый день вы будете находить новые онлайн-предложения, скидки в магазинах и возможность сэкономить еще больше, собирая купоны. Но вам, возможно, придется действовать быстро, поскольку эта отливка в верхней форме в кратчайшие сроки станет одним из самых востребованных бестселлеров. Подумайте, как вам будут завидовать друзья, когда вы скажете им, что получили отливку на AliExpress. Благодаря самым низким ценам в Интернете, дешевым тарифам на доставку и возможности получения на месте вы можете еще больше сэкономить.
Если вы все еще не уверены в литье в формы и думаете о выборе аналогичного товара, AliExpress — отличное место для сравнения цен и продавцов.Мы поможем вам решить, стоит ли доплачивать за высококачественную версию или вы получаете столь же выгодную сделку, приобретая более дешевую вещь. А если вы просто хотите побаловать себя и потратиться на самую дорогую версию, AliExpress всегда позаботится о том, чтобы вы могли получить лучшую цену за свои деньги, даже сообщая вам, когда вам будет лучше дождаться начала рекламной акции. и ожидаемая экономия.AliExpress гордится тем, что у вас всегда есть осознанный выбор при покупке в одном из сотен магазинов и продавцов на нашей платформе.Реальные покупатели оценивают качество обслуживания, цену и качество каждого магазина и продавца. Кроме того, вы можете узнать рейтинги магазина или отдельных продавцов, а также сравнить цены, доставку и скидки на один и тот же продукт, прочитав комментарии и отзывы, оставленные пользователями. Каждая покупка имеет звездный рейтинг и часто имеет комментарии, оставленные предыдущими клиентами, описывающими их опыт транзакций, поэтому вы можете покупать с уверенностью каждый раз. Короче говоря, вам не нужно верить нам на слово — просто слушайте миллионы наших довольных клиентов.
А если вы новичок на AliExpress, мы откроем вам секрет. Непосредственно перед тем, как вы нажмете «купить сейчас» в процессе транзакции, найдите время, чтобы проверить купоны — и вы сэкономите еще больше. Вы можете найти купоны магазина, купоны AliExpress или собирать купоны каждый день, играя в игры в приложении AliExpress. Вместе с бесплатной доставкой, которую предлагают большинство продавцов на нашем сайте, вы сможете приобрести mold casting по самой выгодной цене.
Мы всегда в курсе последних технологий, новейших тенденций и самых обсуждаемых лейблов. На AliExpress отличное качество, цена и сервис всегда в стандартной комплектации. Начните самый лучший шоппинг прямо здесь.
Что такое литье в керамические формы?
Литье в керамическую форму — это производственный процесс для создания инструментов и деталей, таких как рабочие колеса.В процессе изготовления керамической формы могут использоваться такие материалы, как бронза или нержавеющая сталь. Литье в керамическую форму — это процесс, который похож на литье в гипсовую форму. Штукатурки для перманентных форм, изготовленные из пластика, дерева, гипса, резины или металла, используются как часть процесса литья в керамические формы. Керамические формы обычно расходные.
Человек с дрельюПервым этапом процесса литья в керамическую форму является заливка керамической суспензии по образцу формы.Керамическая суспензия затвердевает поверх формы. Процесс затвердевания относительно быстрый. Когда суспензия высохла, это консистенция резины. Когда он удаляется из выкройки, он становится формой для создаваемого инструмента или предмета.
Затем форму необходимо поместить в печь, установленную на низкую температуру, чтобы удалить летучие вещества из формы.Также можно использовать пламенную горелку, прокатывая пламя горелки по каждой области формы. После удаления летучих компонентов форму следует запечь в печи. Печь должна быть установлена на 1832 ° F (1000 ° C), что приведет к затвердеванию формы и превращению ее в керамическую.
На этом этапе сталь или другой элемент для создания инструментов или предметов можно вылить в форму, которая может выдерживать разливку при высоких температурах.Форму можно использовать, пока она горячая, или человек, использующий форму, может сначала подождать, пока она остынет.
Литье в керамическую форму имеет достоинства и недостатки.Одним из основных недостатков является то, что это очень дорогой процесс. Однако, с другой стороны, этот процесс может устранить необходимость во вторичных процессах, которые требуют, чтобы машины завершили или усовершенствовали процесс. Несмотря на то, что это очень дорогостоящий процесс, литье в керамическую форму предлагает несколько преимуществ, в том числе создание отливок с мелкими деталями. Этот тип литья также позволяет создавать очень гладкие поверхности. Размеры инструментов или предметов, созданных из отливки, также очень точны, когда речь идет о размере, форме и размерах.
Основные материалы, которые используются при литье в керамические формы, включают сталь, нержавеющую сталь и бронзу. Наиболее распространенные типы деталей, которые создаются в этом процессе, включают сложные режущие инструменты, рабочие колеса, прецизионные детали, сложные режущие инструменты и инструменты для изготовления пластиковых форм.
Варианты литейного материала
ComposiMold и ImPRESSive Putty работают с МНОЖЕСТВОМ литейных материалов. Мы делаем все возможное, чтобы отслеживать все инновационные материалы, надеясь дать вам советы по разнообразию литейных материалов, которые вы можете использовать.Щелкните вариант литейного материала, чтобы узнать больше. Если у вас есть литейный материал, которого вы здесь не видите, спросите нас.
Акриловые и эпоксидные смолы — отличные литейные материалы для ComposiMold и ImPRESSive Putty. Наш ComposiCast — это эпоксидная смола, разработанная специально для материалов для изготовления форм ComposiMold. Большинство текучих акриловых смол обычно представляют собой прозрачные эпоксидные смолы. Эпоксидные смолы хорошо подходят для деталей размером до 5 кубических дюймов. Для более крупных отливок объемом 5+ кубических дюймов выбирайте эпоксидные смолы с более длительным временем отверждения — 24+ часа.Поэкспериментируйте с замораживанием формы перед заливкой эпоксидной смолы, которая выделяет много тепла во время отверждения. Не рекомендуются эпоксидные смолы, для отверждения которых требуется дополнительный источник тепла. ComposiCast White, Black и Clear Casting Plastic — это эпоксидные смолы, предназначенные для использования с ComposiMold и ImPRESSive Putty.
Еще много видео об использовании смол доступно на нашем канале YouTube.
Начало страницы
Бондо и другие полиэфирные шпатлевки:
Bondo пахнет, и это нездорово.Но это относительно недорого, и вы можете найти его в большинстве хозяйственных магазинов. Обязательно используйте его в хорошо вентилируемом помещении и наденьте перчатки. Bondo отлично подходит для изготовления форм и литья как в ComposiMold, так и в ImPRESSive Putty. Куски большего размера (в зависимости от формы — около 3 кубических дюймов) будут выделять довольно много тепла и могут расплавить ComposiMold, поэтому охладите форму перед тем, как вдвигать литой материал Bondo. ImPRESSive Putty может обрабатывать большие размеры из-за более высокой температуры плавления (175 F по сравнению с135 F для ComposiMold).
Начало страницы
Сливочное масло:
Вы можете сделать форму для масла из множества разных предметов. Процесс изготовления форм прост, а с помощью ComposiMold-Flex формы легко удаляются из масла.
СОВЕТЫ для изготовления форм для масла: мы рекомендуем ComposiMold-Flex для форм для масла, потому что масло мягкое, а гибкость формы Flex позволяет сгибать форму вокруг масла. Охладите масло перед тем, как вынуть его из формы ComposiMold, чтобы оно стало более твердым.
Начало страницы
Шоколад:
Превратите практически любой предмет в шоколад, используя безопасный для контакта с пищевыми продуктами материал для изготовления форм многократного использования. Всего из одного продукта можно сделать десятки форм. Вылейте или налейте в форму несколько видов расплавленного шоколада. Слегка постучите по форме или встряхните, чтобы выпустить пузырьки воздуха в шоколаде. Для шоколадных конфет не требуется смазка для форм. Посмотрите некоторые из этих видео, чтобы увидеть процесс в действии.
Процесс изготовления шоколадной формы отлично подходит для украшения свадебных тортов и тортов на день рождения с помощью нестандартных форм из молочного шоколада и помадки. С ComposiMold вы можете легко изготавливать свои собственные формы для шоколада, вместо того, чтобы пытаться найти пластиковую форму или использовать силиконовые формы, которые можно использовать только для одного дизайна. В отличие от силиконовых форм, из которых можно сделать только одну форму, ComposiMold можно переплавить и повторно использовать для изготовления десятков уникальных форм для шоколада.Он сертифицирован как безопасный для изготовления форм, контактирующих с пищевыми продуктами.
Изготовление формы для конфет ComposiMold для шоколада:
Чтобы сделать свою первую форму, начните с простой формы: чего-нибудь с одной плоской стороной. Растопите ComposiMold в микроволновой печи и залейте им свой объект. Дайте ему застыть или поместите его в морозильную камеру на 30 минут, пока резиновая форма не затвердеет. Вытяните исходную форму и налейте шоколад. Приведенные ниже советы помогут вам добиться успеха при приготовлении шоколадных конфет для тортов, кексов или сахарных угощений.
- Сделайте шоколадные формы быстро и легко, расплавив ComposiMold в микроволновой печи. Пароварка или плавильная печь для шоколада также отлично подходят для плавления ComposiMold.
- Вам не нужно охлаждать или замораживать форму для шоколадных отливок, потому что шоколад никогда не должен быть выше 100 F.
- При изготовлении формы слегка покройте исходную форму безопасным для пищевых продуктов смазкой для форм, например растительным маслом. При отливке шоколада смазка для формы обычно не требуется.
- Вылейте растопленный шоколад в вашу уникальную форму, используя ложку, палку или кисть, чтобы заполнить форму. Постучите по дну и бокам, чтобы из шоколада вышли пузырьки воздуха. Вы также можете использовать бутылку для выжимания или небольшой кондитерский мешок, чтобы протолкнуть шоколад в небольшие отверстия и щели.
- Чтобы отливки из шоколада застыли, охладите шоколад в форме, поместив его в холодильник или морозильную камеру.
- Удалите форму с вашего шоколада, удалив плесень с восхитительного шоколадного лакомства, насколько это возможно, чтобы вы не оказывали на шоколад сильного давления.
- Наслаждайтесь уникальной шоколадной отливкой на заказ. Не забывайте: когда вы сделали все нужные шоколадные слепки с помощью одной формы, вы можете переплавить ее, чтобы сделать более 35 других форм.
Начало страницы
Глины:
Глина и сухая на воздухе глина могут быть впрессованы в ComposiMold или ImPRESSive Putty. Поскольку ComposiMold и ImPRESSive Putty поддаются биологическому разложению, их нельзя использовать с шликерным литьем. Не используйте глину в виде суспензии, иначе вода испортит форму.ComposiMold-Firm и ImPRESSive Putty отлично подходят для штамповки в глине. Возможность повторного использования позволяет при необходимости создавать уникальную форму.
Возможно, вас заинтересует информация о производстве форм из полимерной глины.
Начало страницы
Бетон и цемент:
Если вы хотите изготавливать уникальные формы для бетона, ComposiMold может вам помочь. Создавайте собственные уникальные формы для бетона и повторно используйте их для изготовления новых форм.Просто переплавив, вы можете продолжать делать новые формы: для столешниц, садовых скульптур, каменных стен, каминов, штамповки бетона и многого другого.
Преимущества ComposiMold для ваших бетонных форм:
- Позволяет изготавливать новые формы в любое время
- Превосходная детализация, легкость изготовления практически всего
- Многоразового использования! Никаких отходов!
- Форму нужно будет переделать после от 3 до 8 отливок (простые формы можно использовать дольше).Используйте смазку для пресс-формы, чтобы продлить срок службы пресс-формы.
- Бетоны с медленным отверждением требуют, чтобы смесь бетон / вода находилась в форме в течение длительного времени. Влага может разрушить плесень. Чтобы этого избежать, выбирайте бетон с быстрым схватыванием.
Изготовление формы ComposiMold для вашего бетонного творения: Следуйте основным инструкциям, чтобы изготовить форму с помощью ComposiMold. Процесс прост. Растопите ComposiMold в пароварке или микроволновой печи.
Нанесение смазки для пресс-формы (или смазки) позволит легко отделить вашу модель от ComposiMold.Применение смазки для формы перед литьем также минимизирует износ формы. Это важно, если вы используете форму для множества репродукций.
После этого сотрите смазку для формы, чтобы убедиться, что у вас не слишком много. Вы также можете использовать чистую кисть или ткань, чтобы нанести антиадгезионный состав по поверхности модели и окружающих форм. Убедитесь, что сложные детали, поднутрения и труднодоступные места покрыты как можно тщательнее.Эта птица и приветственный знак, изображенные слева, были отлиты из бетона с добавлением красного бетона.Черепаха (справа) использовала быстротвердеющий бетон Quickcrete. Ниже показано видео, как сделать статую из бетона.
Начало страницы
Формы для печенья или печенья
Печенье и кексы на заказ — в моде! Целые предприятия строятся на любви людей к этим маленьким сладким угощениям. С правильным рецептом теста для печенья, особенно с тем, которое не поднимается во время выпечки, вы можете приготовить печенье любой формы.А с ComposiMold вы не будете ограничены готовыми формами для формочки для печенья, которые доступны в вашем магазине.
1. Выберите найденный предмет нужной формы или вылепите уникальную форму из полимерной глины.
2. Залейте эту форму расплавленным ComposiMold.
3. Удалите оригинальный объект, и вы получите уникальную форму для печенья.
4. Выдавите сырое тесто для печенья в форму и осторожно выньте. Вы можете сделать это, перевернув форму и отогнув ее от теста для печенья.
5. Переложите сырые формы из теста для печенья на противень и выпекайте в соответствии с инструкциями по рецепту.
Рецепт печенья No Rise: большинство рецептов песочного печенья подходят. Вот отличный рецепт Baking a Moment от нашей подруги Элли. Это печенье хорошо держит форму.
На видео ниже вы увидите, как мы лепили логотипы Maine Startup и Create Week двух размеров. Больший размер предназначен для формы для печенья, а немного меньший — для шоколадного топпера.Это произвело большой эффект и произвело впечатление.
Начало страницы
ComposiCast
См. Дополнительную информацию на нашей странице продуктов ComposiCast. Настоящие черные, чисто белые или прозрачные смолы для изготовления форм и литья. ComposiCast разработан специально для использования в ImPRESSive Putty и ComposiMold.
• Твердость по Шору 80D
• 30-45 мин. Время работы
• Смешивает 1: 1 по весу или объему (весы не требуются).
• 3 разных версии: белый, черный и прозрачный.Белые и прозрачные краски можно окрасить с помощью наших красителей.
• Окрашивается, шлифуется, обрабатывается.
• Изготавливают до 4 кубических дюймов. Для больших размеров охладите форму, налейте смолу через определенные промежутки или добавьте наполнители.
• Специально разработан для форм ComposiMold и ImPRESSive Putty, но также отлично работает с силиконом, латексом и другими литейными материалами.
1. Сделайте слепок выбранного вами объекта. Попробуйте ComposiMold или ImPRESSive Putty, многоразовые материалы для изготовления форм.
2. Выньте объект из формы. Если вы используете ComposiMold или ImPRESSive Putty, вы можете легко сделать срез в форме, если необходимо удалить объект.
3. Распылите или протрите внутреннюю часть формы смазкой для форм, подходящей для эпоксидных смол, например, смазкой для форм ComposiMold.
4. Медленно смешайте ComposiCast Part A с Part B в равных пропорциях по объему или весу. Обязательно очистите стенки емкости для смешивания, чтобы тщательно перемешать весь материал.(Вы можете добавить наши смоляные красители или текстурные материалы в это время.)
5. Медленно вылейте смесь смолы ComposiCast в форму.
6. Дайте ComposiCast застыть в форме прибл. 10 часов или на ночь. Снимите, чтобы полюбоваться твердой пластмассовой отливкой! Затем повторите шаги 3-6 для других отливок!
Начало страницы
Твердый гипс ComposiStone
Тверже штукатурки … Гладче цемента. Перейдите на нашу страницу заказа ComposiStone для получения дополнительной информации.В этой системе используется сухая смесь и вода в соотношении 2,5 части порошка на 1 часть воды; и не менее 2 частей порошка на 1 часть воды по весу или объему. Он приобретает красивый светло-серый цвет. Текстура похожа на цемент, но выглядит намного более гладкой.
Идеально для:
Украшения для улицы / газона
Орнаменты для полок
Скульптуры
Детали для рукоделия
Другие общие приложения
Срок годности и хранение: Composi-Stone следует хранить при комнатной температуре в сухом месте.Емкости необходимо плотно закрывать для защиты от влаги и посторонних предметов.
Мелок:
Crayon — это низкоплавкий парафиновый воск с добавлением цветных пигментов. И он отлично работает с ComposiMold (Original или Flex) и ImPRESSive Putty.
Что делать со сломанными и потертыми мелками? Вы можете сделать круглые формы, используя форму для маффинов, как показано на заднем плане. Или вы можете сделать очень крутые отливки из мелков с помощью ComposiMold.
Для приготовления: снять с мелков обертку, мелки растопить. Плавили в духовке при низких температурах, но можно и на плите. Будьте осторожны, чтобы не обжечь воск.
Чтобы подготовить форму ComposiMold: выберите форму, поместите ее в безопасный ящик для форм или контейнер. Мы использовали пластиковый контейнер для посуды (такой же, как в стартовом наборе ComposiMold). Распылите смазку для форм и средство для удаления пузырей. Вылейте растопленный ComposiMold и охладите в морозильной камере.
Дайте ComposiMold остыть, чтобы он мог обрабатывать горячий воск.
Залейте воск для карандашей в холодную форму ComposiMold. Свинья впереди использовала заливки двух разных цветов.
Пусть остынет и раскрасится!
Начало страницы
Энкаустика
Encaustics — смесь смолы дамара и пчелиного воска. Отлично работает с ImPRESSive Putty. Для размеров до примерно 6 кубических дюймов вам не нужно охлаждать форму. Более 6 дюймов охладите ImPRESSive Putty, поместив ее в морозильную камеру на час.
Начало страницы
Эпоксидная шпатлевка, Апокси-шпатлевка, Milliput или другая шпатлевка для скульптурирования
Существует много различных эпоксидных шпатлевок, и мы не нашли ни одной, которая бы плохо сочеталась с ComposiMold или ImPRESSive Putty. Замазку вдавливают в формы и дают застыть. Для большинства эпоксидных шпатлевок хорошо подходит ComposiMold-Original, но если у вас очень прочная шпатлевка, используйте COmposiMold-Firm. ImPRESSive Putty отлично сочетается со шпатлевками.
Начало страницы
Помадка:
Fondant, Marzipan, Modeling Chocolate, Gum paste — все они отлично работают в ComposiMold. Мы рекомендуем ComposiMold-FC. Вдавите размягченную помадку в форму руками или скалкой и немедленно удалите. Для помады не требуется смазка для форм. При заливке съедобных угощений вы также можете использовать: рецепты теста для печенья без роста, мармеладки, пасту из жевательной резинки, лед, масло и многое другое!
Вы можете легко создать слепок в вашей форме с помадной пастой или жевательной пастой! Это можно сделать с помощью техники «пресс-формы».Это подходит для помадки, жевательной пасты, шоколада для лепки, марципана и других лакомств из пищевого сахара.
Как только ваш ComposiMold остынет до исходной эластичной консистенции, удалите исходную деталь и просто вдавите помадную пасту или жевательную пасту в форму. Вы также можете использовать технику «формы из двух частей» и вдавить шарик помады между двумя частями формы. Красящее средство можно добавить в помадку до или после нанесения слепка.
Советы:
- Будьте осторожны, чтобы не деформировать отливку из помадки при извлечении ее из формы.Вы можете «отогнуть» форму в сторону от отливки и позволить отливке «выпасть» из формы.
- Охлаждение помады или пасты для жевательной резинки сделает ее более твердой, поэтому ее не так легко деформировать, когда вы вынимаете ее из формы.
- Не оставляйте помадку в ComposiMold на ночь, так как она станет липкой.
Начало страницы
Горячий клей и порошок для тиснения:
Горячий клей и пудра для тиснения отлично подходят для нашей ImPRESSive Putty.После того, как вы сделали форму, просто налейте или выдавите горячий клей. Не заливайте горячий клей, если он выше 220 F.
Начало страницы
Желе или жевательная отливка
Ключ к отличному желе-лего — использовать ½ воды, указанной в рецепте, иначе желе будет слишком мягким и, скорее всего, сломается.
Желе… любой ароматизатор… Растительное масло в качестве смазки для формы и ComposiMold для изготовления формы.
Используйте микроволновую печь, чтобы расплавить ComposiMold.
. И холодильник, чтобы охладить форму и желе.
Используйте зубочистку, чтобы удалить пузырьки с поверхности. Лего.Вы не должны лопать пузыри, просто оторвите их от поверхности Lego.
Охладите форму в холодильнике или морозильной камере, чтобы она стала быстрее.
Перед тем, как налить желе, убедитесь, что оно остыло до комнатной температуры… поместите его в холодильник, чтобы быстрее охладить.
Обрызгайте форму растительным маслом для смазки формы. Сотрите любой доступ. Слишком большое количество смазки для формы оставит полосы на отливках.
Залейте желе в полости формы.
Начало страницы
Низкоплавкие металлы
ImPRESSive Putty хорошо работает с легкоплавкими металлами, такими как Wood’s Metal.Он может выдерживать температуры примерно до 200 F при охлаждении формы. ComposiMold не работает с металлами.
ImPRESSive Putty также подходит для отливки воска по выплавляемой восковой модели. Сделайте форму, как для любого воска, и используйте ее в процессе выплавляемого воска, чтобы сделать отливку из металла.
К началу страницы
Формовочная пластмасса
Shapelock, InstaMorph или Friendly Plastic или Polymorph пластик, который становится похож на замазку при плавлении в горячей воде и становится жестким при комнатной температуре.Изготовлен из поликапролактонового пластика. Он становится прозрачным, когда он в резиновой форме, и остывает до белого, скользкого, твердого, пластичного. В качестве материала для форм он обычно немного тверд, но в качестве литейного материала он отлично подходит для ImPRESSive Putty. Просто вдавите его в форму для ImPRESSive Putty после того, как нагреете.
Процесс:
Сделайте форму из ComposiMold-Firm или ImPRESSive Putty, расплавив в микроволновой печи и заливая деталь, которую вы дублируете. Начните с простой формы из 1 части, но вы можете сделать и более сложные формы, соединив две половинки вместе.
Форма должна быть жесткой, чтобы можно было вставить Shapelock в форму. Чтобы сделать форму более жесткой и позволить ComposiMold-Firm выдерживать температуру горячего Shapelock, поместите PowerMold на некоторое время в морозильную камеру. Замазывать ImPRESSive Putty не нужно.
Вставьте расплавленный пластик в полость формы и заполните пустоты.
Вот и все. Для изготовления отливок не требуется смазка для пресс-формы. Поскольку и ImPRESSive Putty (и ComposiMold), и Shapelock можно использовать повторно, вы можете плавить и переплавлять форму и Shapelock, чтобы создавать самые разные формы.
Начало страницы
Paper Mache
При отливке из папье-маше в ComposiMold или ImPRESSive Putty делайте это слоями и дайте внешним слоям высохнуть, прежде чем наносить другие слои. После того, как у вас будет несколько сухих слоев папье-маше, вы можете добавить еще несколько слоев, и первые слои защитят форму.
К началу страницы
Парижский гипс, ультракальный, гидрокальный, стоматологический гипс:
Отливка с гипсом Paris — это недорогая и простая процедура для основных отливок.
Для форм ComposiMold или ImPRESSive Putty Mold используйте наш гипс ComposiMold, который был разработан для отверждения в этих формах до прочной твердой отливки. Благодаря более быстрому отверждению вода в штукатурке не вступает в реакцию с ComposiMold или ImPRESSive Putty, создавая прочные и твердые гипсовые отливки. Вы также можете приобрести порошковую добавку для добавления в любую штукатурку «Париж» для получения такой же прочной и твердой отливки.
And Plaster of Paris представляет собой легко смешиваемую формулу, которая смешивается с водой и высыхает, образуя плотную, прочную, гладкую поверхность без пузырьков.«Парижский гипс» — отличный материал для основных отливок, форм и художественных проектов, потому что его просто смешивать и использовать. «Парижский гипс» схватывается за несколько минут, хотя требуется час, прежде чем его можно будет вынуть из формы. Для полного высыхания требуется 24-48 часов. Использовать Plaster of Paris легко, но есть процедуры, которые помогут вам добиться успеха при изготовлении гипсовых отливок.
Парижский гипс — это не пластик. Это твердое белое вещество, полученное путем добавления воды к порошкообразному и частично обезвоженному гипсу.Он твердый, как цемент или бетон, но белый и не такой прочный. Поэтому не используйте гипс для очень тонких отливок. Простые формы или рисунки с твердой основой будут более удачными. Если вам нужна гибкость или жесткость окончательных отливок, то переходите к пластику.
Идеальное соотношение для смеси Plaster of Paris — 3 части порошка Plaster of Paris на 1 часть воды. Отмерьте воду и налейте ее в емкость для смешивания. Некоторые рецепты предлагают 2 части штукатурки залить водой, но при этом гипсовая повязка будет намного слабее.Чем толще вы сможете налить, тем лучше. Начните с пропорции 3: 1 и, если необходимо, добавьте небольшое количество воды, чтобы облегчить налив.
- Ложкой разбейте комки гипса. Если вы смешиваете смесь руками, обязательно наденьте перчатки.
- При смешивании воды и гипса следует смешать порошок с водой. Насыпьте гипсовый порошок в воду, распределив его по поверхности воды. После того, как все вылилось, постучите по стенкам емкости для смешивания и дайте гипсовому порошку наполниться водой, чтобы уменьшить образование пузырей.Штукатурный порошок погрузится в воду. Когда вы закончите наносить штукатурку, она будет немного выше поверхности воды и не сможет легко впитаться водой.
- Осторожно перемешайте штукатурку с водой, чтобы образовалась красивая кашица, похожая на густую смесь для блинов. Аккуратное перемешивание штукатурки снизит вероятность попадания пузырьков в смесь.
- Залейте гипс в формы. Если вы хотите научиться делать свои собственные формы, посмотрите наши видеоролики по изготовлению форм и получите бесплатную электронную книгу по изготовлению форм.
Еще пара советов по отливке гипса:
- Не заливайте лишнюю штукатурку в канализацию. Это может затвердеть и повредить вашу сантехнику. Вы можете разбавить гипс, чтобы он не затвердел, или дать ему затвердеть и выбросить его. №
- Для изготовления цветной штукатурки можно добавлять красители в штукатурную смесь, пока она еще находится в жидком / пастообразном состоянии. Помните, что вы будете добавлять цвет к белому, поэтому вам понадобится больше красителя, чтобы сделать более темные цвета.Подойдут любые виды красок.
- Чтобы покрасить гипсовую отливку после ее затвердевания, сначала используйте слой гипса или грунтовки для герметизации штукатурки, а затем вы можете покрасить штукатурку как хотите.
Видео гипсовой отливки приманки для утки
Смешайте гипс и воду до консистенции зубной пасты. Традиционные штукатурки хорошо затвердевают, но оставляют легкий мягкий слой на внешней стороне гипса.Чтобы этого избежать, перед заливкой слепков нанесите на форму слой Plaster Release ComposiMold. Быстро затвердевающие кладочные цементы отлично работают и очень сильно затвердевают. Следуйте инструкциям по соотношению компонентов смеси. У нас также есть ComposiStone специально для этого применения: прочные, гладкие отливки.
У нас также есть ComposiStone Hard Plaster, который хорошо подходит для твердых и прочных гипсовых отливок. ComposiStone тверже штукатурки, но более гладкий, чем цемент. Его можно красить большинством красок.
Видео отливки гипса в формы ComposiMold
Гипсовая отливка головы куклы (или жуткий орнамент на Хэллоуин)
Начало страницы
Полиэфирная смола
Полиэфирная смола — самая дешевая из пластмассовых смол.Также вдыхание паров неприятно и вредно. Он действительно работает с ComposiMold и ImPRESSive Putty. Убедитесь, что находитесь в хорошо вентилируемом помещении, надевайте перчатки и фильтр геппа. Из-за экзотермичности полиэфира во время отверждения вы можете делать размеры до примерно 3 кубических дюймов, если смола входит в большую массу. С ImPRESSive Putty вы можете нанести до 6 кубических дюймов. Для больших кусков охладите форму, добавьте наполнители, чтобы уменьшить количество используемой смолы, или заливать с интервалами, чтобы каждый слой застыл перед нанесением следующего слоя.Не пытайтесь менять состав между отвердителем и смолой, так как это может вызвать неполное отверждение.
ComposiMold также можно использовать для вакуумной упаковки деталей из полиэфирных композитов.
Начало страницы
Полимерная глина
Полимерная глина, такая как FIMO или Sculpey, полимерно-металлическая глина (PMC), пластилиновая глина и другие , хорошо работают в ComposiMold и ImPRESSive Putty для изготовления оригинала для формования, а также для изготовления отливок.Для твердых глин мы рекомендуем ImPRESSive Putty или ComposiMold-Firm. Чтобы использовать, просто вдавите полимерную глину в формы. Не запекайте полимерную глину в формах. Это отличный способ использовать природные объекты или быстро сделать большое количество отливок.
Формовка из глины и полимерной глины с помощью ComposiMold. Высушенная на воздухе глина и другие глины для лепки являются отличными и простыми материалами для литья, чтобы придать глине нужные формы. Вы можете быстро и легко научиться делать глиняные формы с помощью ComposiMold.Используйте найденный объект для создания глиняной формы или даже вылепите свой собственный мастер-объект, а затем сделайте из него форму. Вы будете создавать дубликаты своей скульптуры в кратчайшие сроки!
Пресс-формы — это простой и эффективный способ создания трехмерных объектов очень быстро и легко. Например, пуговицы можно вдавить в форму за секунды, используя большинство типов полимерных глин или тестообразных литейных материалов. Это отличный способ сделать подвески из полимерной глины для украшений.
Для формования глины в форме ComposiMold:
Следуйте основным инструкциям на нашей странице «Как использовать ComposiMold» для изготовления формы с ComposiMold.Приведенные ниже советы помогут вам создать отличную пресс-форму для полимерной глины, FIMO, Sculpey, пластилина, PaperClay и даже мастики или жевательной пасты.
Ключ к Как сделать глиняные пресс-формы в пресс-форме ComposiMold:
Думайте о пресс-форме как о негативном пространстве, в которое вы можете вдавить литой материал, чтобы подобрать детали исходной формы.
1. Смягчите пластилин для лепки или высушите на воздухе в соответствии с инструкциями по продукту.Часто для этого нужно работать с ним в руках, пока он немного не нагреется и не станет тестообразным.
2. Нанесите смазку для форм, если вы обнаружите, что она помогает вашей глине высвобождаться из формы.
3. Вдавите глиняный материал для литья в форму. Обязательно сначала вдавите пластилин в самые низкие точки отрицательного пространства. Это гарантирует, что глиняный литейный материал подберет все детали формы.
4. Осторожно достаньте глиняную отливку из формы.Это можно сделать, перевернув форму вверх дном и дав ей выпасть. (Возможно, вам придется немного отогнуть форму от глины, чтобы высвободить ее.)
5. Если ваша пластилин деформируется, когда вы вынимаете его из формы, охладите форму и глину. Это сделает глину более твердой и твердой, что позволит вам более эффективно извлекать ее из формы с меньшими искажениями.
Начало страницы
Полиуретан или уретан:
ImPRESSive Putty работает с большинством уретановых смол.ComposiMold также работает с полиуретаном, но более подходит для нагрева более крупных форм. Выберите уретан с более длительным временем отверждения. По мере застывания они создают меньше тепла. Вы также можете поэкспериментировать с замораживанием формы перед заливкой уретановой смолы с более высокой температурой. Обязательно используйте тальк / детскую присыпку в качестве смазки для форм перед каждой отливкой.
Ключи к использованию ComposiMold с уретановыми смолами:
1. Охладите форму до и во время литья.Так что остынь свой
2. Добавьте СУХОЙ наполнитель, чтобы уменьшить количество используемой смолы. Уретаны очень чувствительны к воде, они будут пузыриться и выделять тепло при контакте с влагой. Так что убедитесь, что все высохло. Наполнитель уменьшает количество используемой смолы, поэтому у вас меньше экзотермических реакций (накопление тепла), а также снижает стоимость.
3. Используйте тальк (детская присыпка) в качестве смазки для форм, чтобы вещи оставались сухими.
4. Заливайте уретан с интервалами, чтобы при каждой заливке не возникало большого количества тепла.
Если вам не нужны конкретные свойства уретана, можно использовать смолы ComposiCast, которые являются эпоксидными смолами и предназначены для использования с ComposiMold.
Начало страницы
Силикон:
Отливки из силиконаотлично подходят для форм ComposiMold. Делайте отливки из силиконовых каучуков, отвержденных платиной или оловом. Oogoo тоже работает (Oogoo сжимается до 50%).
Начало страницы
Мыла:
Мыло из масла ши и глицерина — отличное мыло! Охладите форму перед заливкой мыла с более высокой температурой (выше 140 ° F) в ComposiMold. Мы рекомендуем ComposiMold-Flex, потому что вы можете легко извлечь мыло из формы, не повредив его. ImPRESSive Putty подходит для мыла при более высоких температурах.
Начало страницы
Воски :
Воскпредназначен для формования свечей, обработки выплавляемого воска, энкаустики или других применений.Соевый воск, парафиновый воск, пчелиный воск и плавленые мелки действительно работают. Для более высоких температур воска (выше 140 ° F) сначала охладите форму. Попробуйте наш полностью натуральный воск для свечей сои для изготовления свечей и красивых восковых отливок. Остывает до белого кремового цвета!
ImPRESSive Putty для микрокристаллических восков, используемых в процессе выплавляемого воска. Возможно, сначала нужно охладить более крупные куски. ComposiMold не может выдержать более высокую температуру микрокристаллического воска.